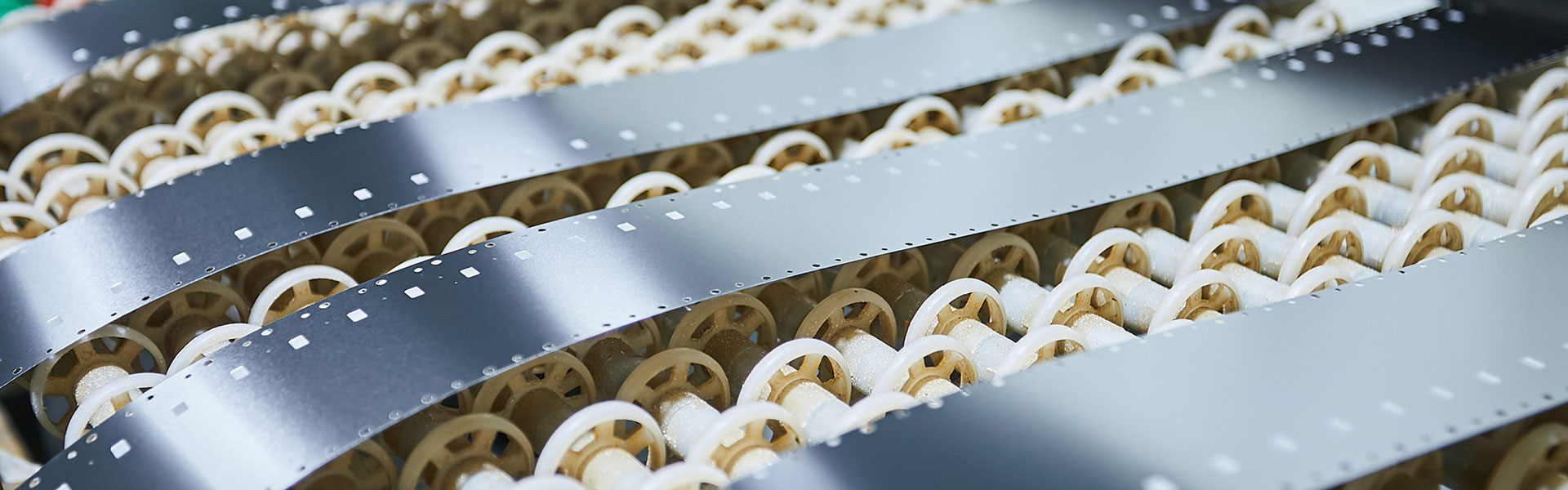
Precision Etching Service And Solutions for Today’s Innovative Part Designs
Photochemical etching refers to removing the protective film from the area to be etched after plate exposure and development. During etching, the metal is exposed to a chemical solution. Two positive patterns are used to dissolve and corrode through chemical flooding and grinding from both sides, forming concave and convex or hollows. molding effect. Chemical etching is very targeted and refers specifically to controlled corrosion. It is a controllable processing method of metal through chemical methods.BE-CU ETCH is a full-service provider of high-quality metal etching parts. We offer an array of value-added and metal finishing options to bring you closer to the production finish line.
High precision up to +/-0.0075mm
Low tolerance up to +/-0.01mm
3 layers of testing to strictly control quality
From raw materials to finished products
Homepage » Metal Etching »
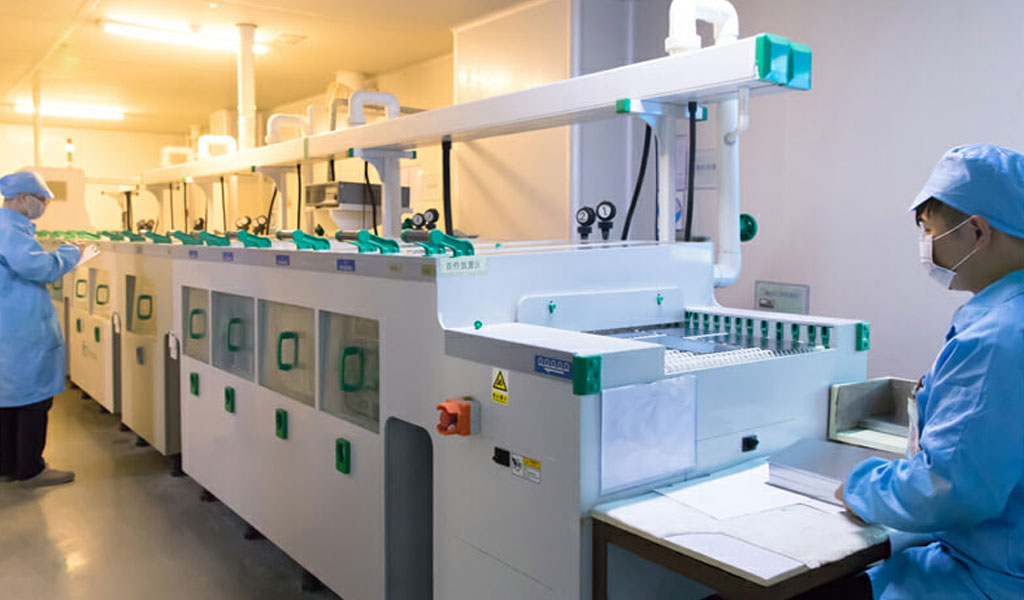
MEET BE-CU ETCH
Conventional Sheet Etching
Traditional hardware etching is a process of using sheet metal materials of certain specifications to process raw materials through a series of processes such as “cleaning – coating – exposure – development – etching – inspection – packaging”; the entire process is done manually Assisted completion.
Sheet Metal Etching is a flexible etching processing method, suitable for small batch or mass production processing of products of various sizes and thicknesses.
MEET BE-CU ETCH
Roll-to-roll Continuous Etching
Roll-to-roll continuous etching is also called RTR continuous etching, which means that the entire process from raw materials to finished products is a roll-to-roll tape production method. The process flow is “RTR cleaning – RTR photosensitive film – RTR exposure – RTR development – RTR etching – inspection – packaging”, which is very different from sheet etching. The entire production process is highly automated.
Roll-to-roll continuous etching is mainly targeted at products with high precision and high post-process automation requirements, and is usually targeted at products with material thicknesses below 0.3mm.
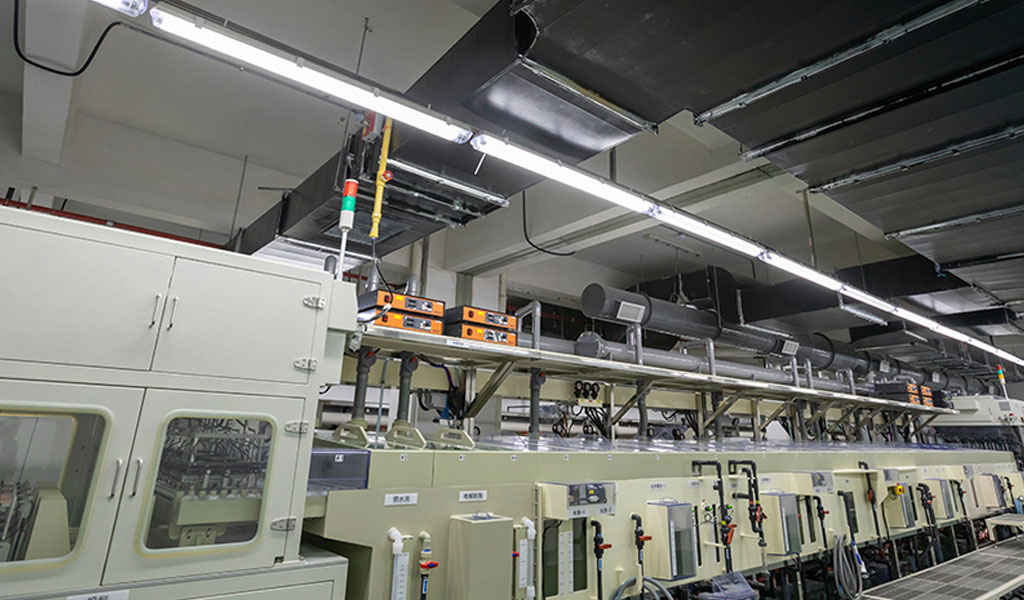
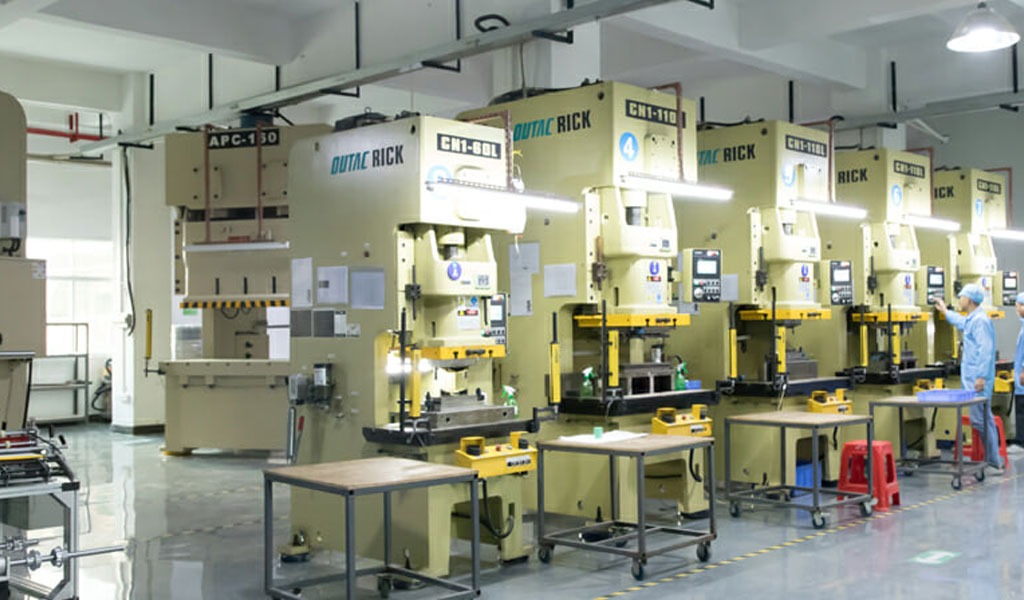
MEET BE-CU ETCH
Precision Stamping
We are equipped with 80 sets of 6ton-1000ton pressure stamping equipment, which can process materials with a thickness of 0.005 inches to 5 inches, and can manufacture stamping parts with a maximum width of 24 inches.
The largest hydraulic stroke provides cost-effective manufacturing solutions for customized stamping parts of any size.
The internal precision stamping die processing workshop can handle high-precision and complex stamping die design and manufacturing, including: progressive die stamping dies, compound dies, deep drawing dies, precision single stamping dies and rapid stamping tools.
MEET BE-CU ETCH
Die Cutting
We serve our customers with a complete selection of die cutting equipment, capable of meeting every die cutting need. We use our range of presses from a 25-ton punch clicker to a 110-ton flatbed press to die cut a variety of standard or customer-provided materials. Our largest die cutting machinery is equipped with either a 41.3” x 78.7” flat bed diecutter or a 28” x 38” platen press die cutter. For high volume products, we have high speed die cutting capabilities with our Clam Shell equipment as well as SCHOEN Automatic Die Cutter to produce tens of thousands parts that meet your needs.
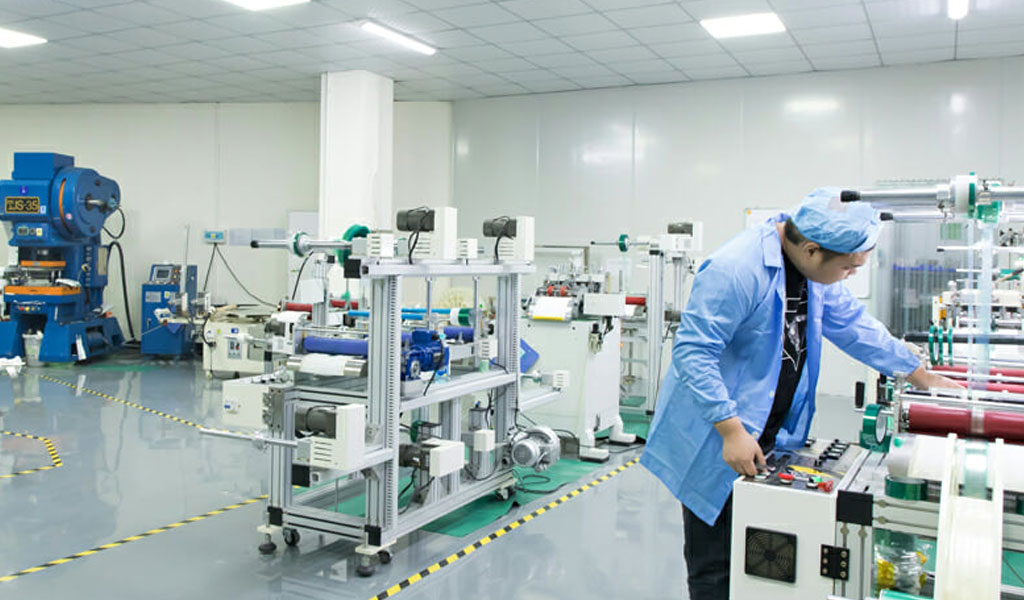
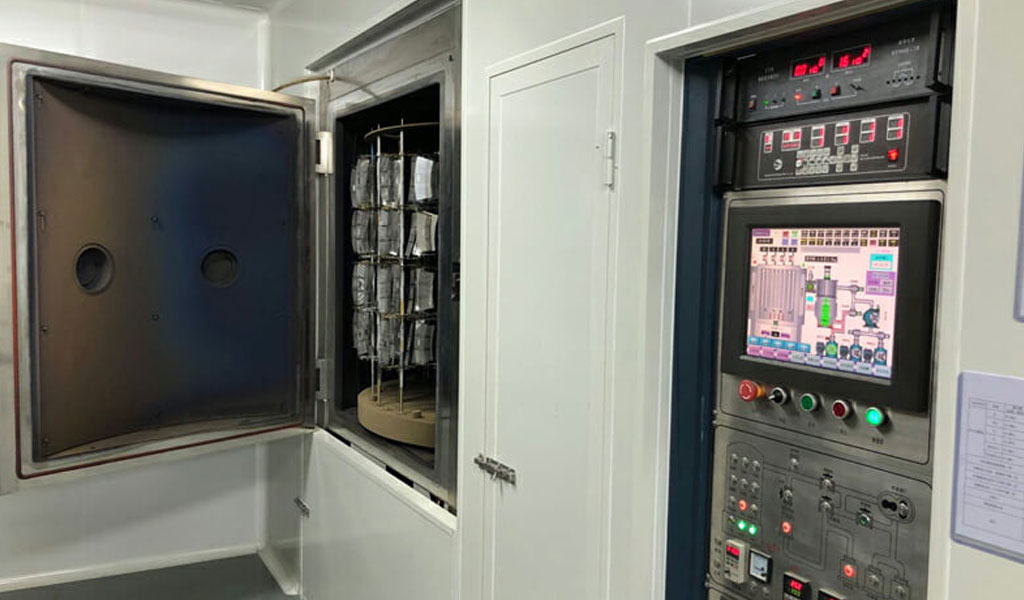
MEET BE-CU ETCH
PVD Coatings
The BE-CU ETCH PVD process is used for the deposition of coatings made of nitrides, carbides and carbonitrides of Ti, Cr, Zr and alloys like AlCr, AlTi, TiSi on a large range of tools and components. Applications include cutting and forming tools, mechanical components, medical devices and products that benefit from the hard and decorative features of the coatings. The typical process temperature for PVD coatings is between 250 and 450 °C. In some cases, BE-CU ETCH PVD coatings can be deposited at temperatures below 70 °C or up to 600 °C, depending on substrate materials and expected behavior in the application.
MEET BE-CU ETCH
Electroplating Process
Electroplating is basically the process of plating a metal onto the other by hydrolysismostly to prevent corrosion of metal or for decorative purposes. The process uses anelectric current to reduce dissolved metal cations to develop a lean coherent metalcoating on the electrode. Electroplating is often applied in the electrical oxidation ofanions on a solid substrate like the formation of silver chloride on silver wire to formsilver chloride electrodes.BE-CU ETCH offers the broadest array of plating finishes and process capabilities in the industry. We specialize in gold plating, silver plating, palladium-nickel plating, tin plating and nickel plating finishes, and utilize state-of-the-art barrel plating, rack plating, and continuous reel-to-reel plating and coil plating processes.
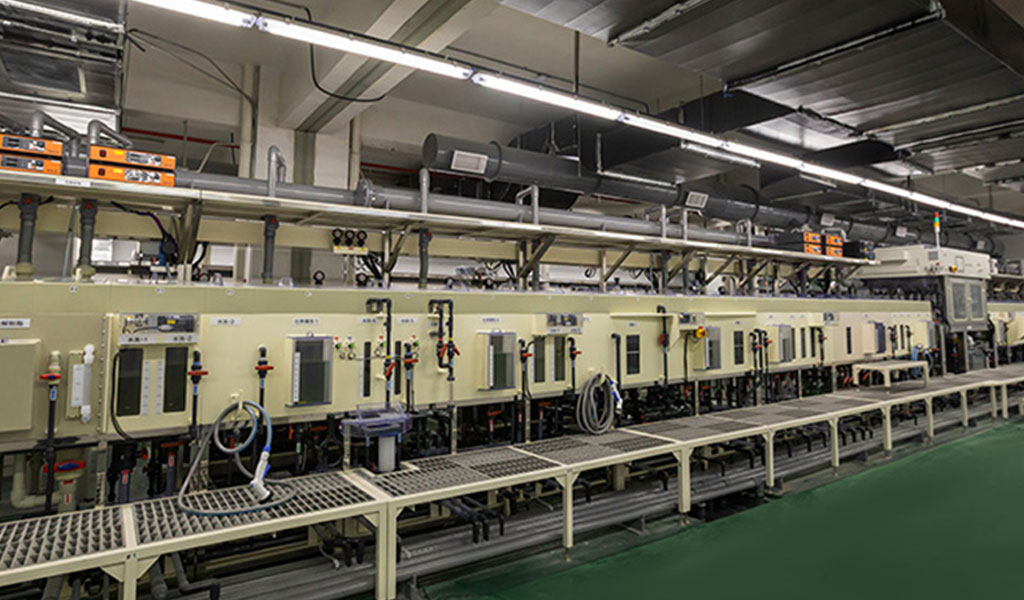
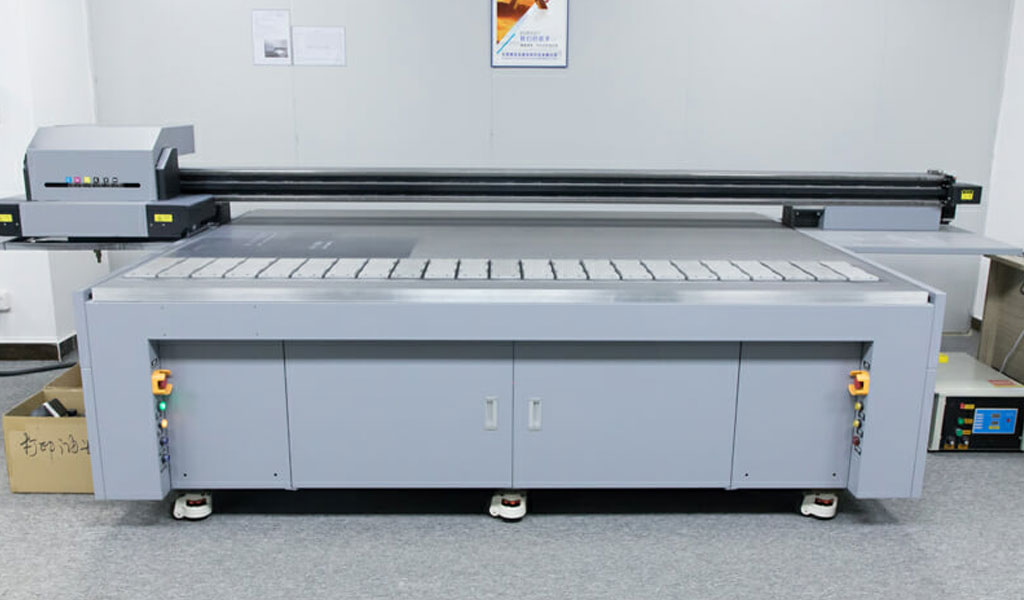
MEET BE-CU ETCH
2D Printing
Different from traditional spraying or electrophoresis processes, the insulation printing process accurately prints ink onto the product through the printer’s print head.
The advantages of insulation printing are obvious: the color is adjustable and controlled by CMYK color; the film thickness can be controlled; areas can be selectively printed; can be printed on uneven surfaces; almost any graphics can be printed; the coating has good adhesion and is resistant to harsh environments .
MEET BE-CU ETCH
Silk Screen Printing
Screen printing refers to using a silk screen as a plate base and using a photosensitive plate making method to create a screen printing plate with graphics and text. Printing is carried out using the basic principle that the mesh of the graphic part of the screen printing plate can pass through the ink, but the mesh of the non-graphic part cannot pass the ink.
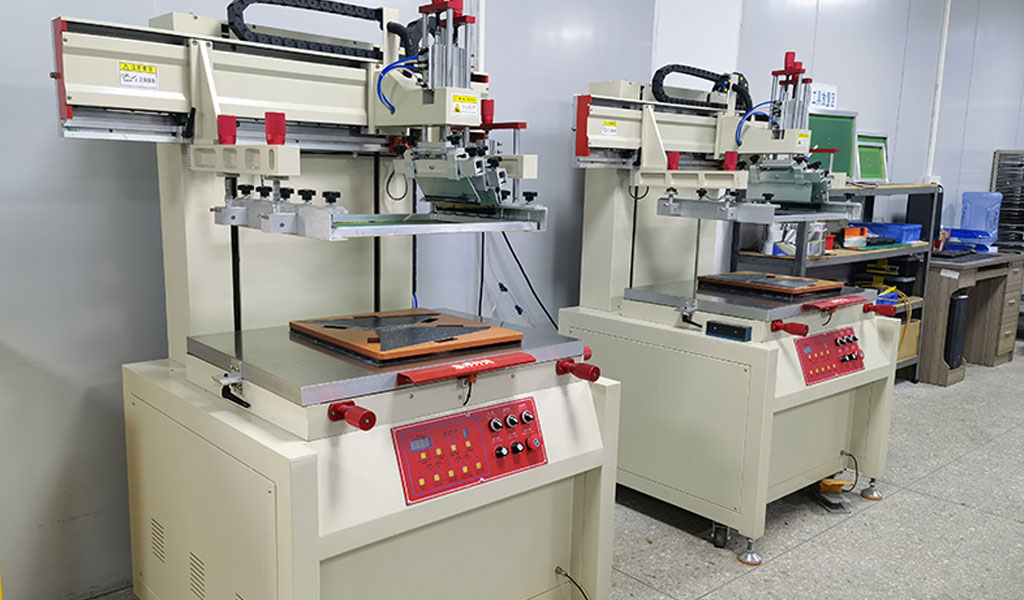
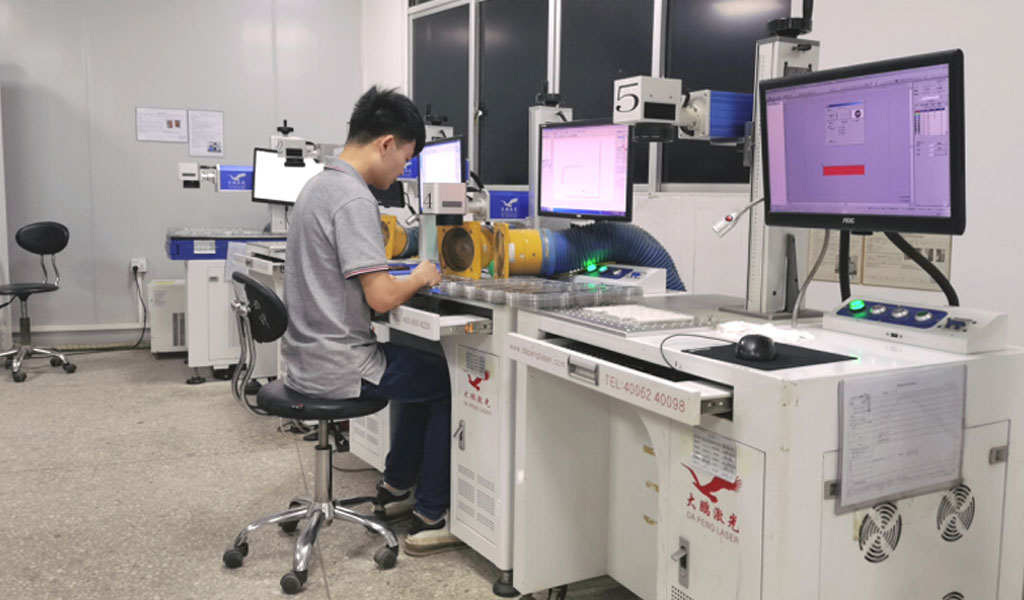
MEET BE-CU ETCH
Laser Engraving Process
The laser engraving process uses laser beams to carve marks on the surface of materials or inside transparent materials. Laser beams can produce two types of metabiotic effects and terrestrial effects on substances. When the substance instantly absorbs the laser light, a physical or chemical reaction occurs, which can trace or display patterns or words, thereby forming marks.
MEET BE-CU ETCH
Laser Cutting Process
BE-CU inc is a China Best laser cutting enterprise that specializes in delivering top-notch and affordable services. Our services revolve around rapid prototyping, mass production, and small quantity machining to cater to all our clients. We offer a range of services that include CNC milling, CNC turning, and precision grinding, and we can operate on different materials such as aluminum, copper, stainless steel, plastics, tool steel, brass, and more. Our reputation for quick delivery and high precision makes us the preferred choice for many clients.Capable of handling sheets and plates with 16 gauge to 1.25 in. thickness, 20 to 90 ft. length and 7 to 12 ft. width. Other capabilities include fabrication, press brake forming, bending, contract manufacturing, punching and welding.
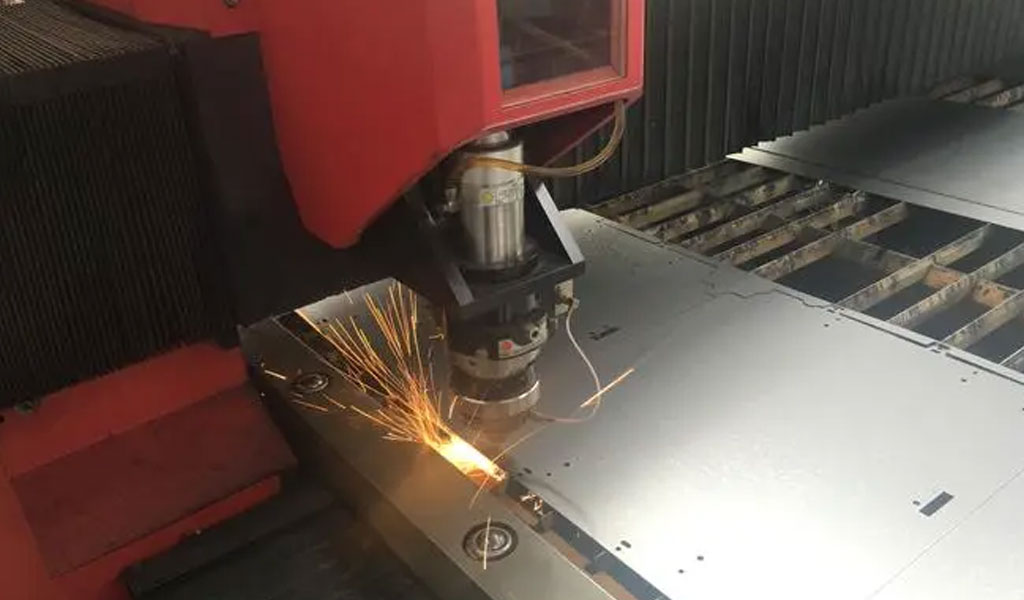
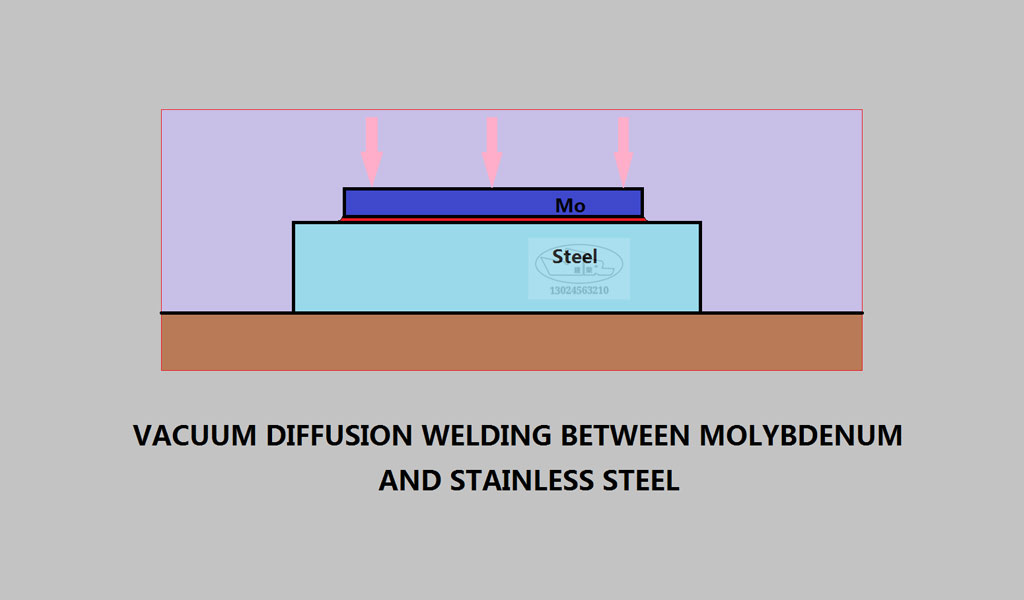
MEET BE-CU ETCH
Vacuum Diffusion Bonding
Vacuum Diffusion Bonding (VDB) is a solid-state joining process where two or more materials are bonded together at elevated temperatures in a vacuum environment. The process involves the diffusion of atoms between the surfaces of the materials to form a metallurgical bond without the use of fillers or adhesives. It is distinct from other bonding methods like welding, soldering, or brazing in that it does not involve the melting of the materials being joined. Instead, the materials remain in their solid state during the bonding process.