In the realm of industrial manufacturing, precision is paramount. To meet the stringent demands of modern industries, innovative techniques such as chemical etching have emerged as indispensable processes, particularly when it comes to aluminum. This versatile metal, renowned for its lightweight and corrosion-resistant properties, has found a myriad of applications in aerospace, electronics, and medical industries. In this article, we delve into the intricate world of chemical etching aluminum, exploring its applications, advantages, and the advanced methodologies employed to achieve unparalleled precision.
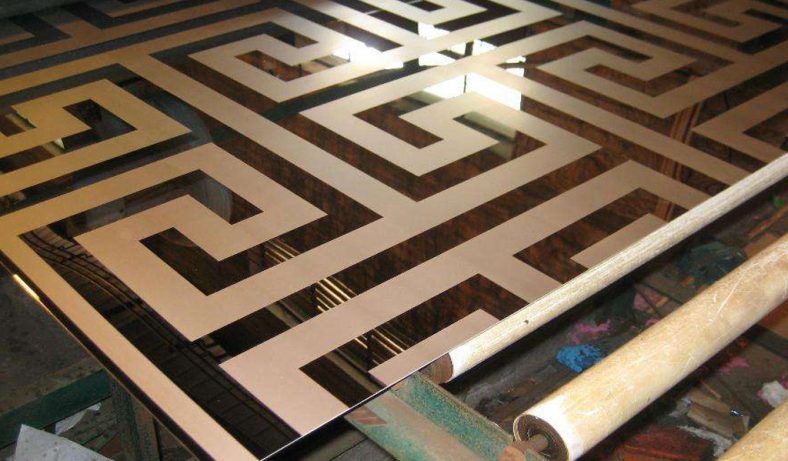
The Significance of Aluminum in Industrial Applications
Aluminum, with its remarkable balance of strength and weight, has become the material of choice in numerous industrial sectors. From aircraft components to electronic enclosures, aluminum’s versatility has paved the way for technological advancements and enhanced product performance.
However, achieving precision in the fabrication of aluminum components requires a method that goes beyond conventional machining processes. This is where chemical etching steps in as a game-changer.
Chemical Etching
Chemical etching, also known as chemical milling or acid etching, is a subtractive manufacturing process that selectively removes material from a metal surface to create intricate patterns, shapes, or features. In the context of aluminum, this technique offers unparalleled precision and allows for the production of complex geometries with tight tolerances.
Applications of Chemical Etching in Aluminum
Aerospace Components: Chemical etching aluminum is extensively utilized in the aerospace industry to manufacture lightweight components with intricate designs. This includes critical parts such as fuel nozzles, brackets, and heat exchangers.
Electronics and Microfabrication: The electronics industry benefits from the precision of chemical etching for aluminum circuit boards, heat sinks, and microelectromechanical systems (MEMS). This process enables the creation of finely detailed features on a microscopic scale.
Medical Devices: In the medical sector, where precision is non-negotiable, chemical etching aluminum is employed to manufacture components for devices such as implantable devices, surgical instruments, and diagnostic equipment.
Advantages of Chemical Etching Aluminum
Precision and Accuracy: Chemical etching ensures high precision and accuracy, allowing for the creation of intricate designs and features with tight tolerances that may be challenging or impossible to achieve through other manufacturing methods.
Cost-Effectiveness: Compared to traditional machining methods, chemical etching offers cost-effective solutions for producing complex aluminum components. The process minimizes material wastage, making it an environmentally friendly and economically viable choice.
Versatility: Chemical etching is a versatile process that accommodates a wide range of aluminum alloys and thicknesses. This adaptability allows manufacturers to address diverse industrial requirements without compromising on precision.
Advanced Methodologies in Chemical Etching
To achieve exacting precision, advanced methodologies have been developed in chemical etching for aluminum. These may include the use of specialized etchants, masking techniques, and advanced equipment to control the etching process with unparalleled accuracy.
Conclusion
In the pursuit of precision for exacting industrial applications, chemical etching aluminum emerges as a technological marvel. Its ability to marry the inherent benefits of aluminum with unmatched precision makes it an indispensable tool for industries where excellence is not just a goal but a requirement. As technology continues to evolve, chemical etching will likely play an even more pivotal role in shaping the future of precision manufacturing, further pushing the boundaries of what is achievable in the world of aluminum fabrication.