Metal-assisted chemical etching (MACE) has emerged as a pivotal technique in the field of nanofabrication and microfabrication, enabling the creation of high-aspect-ratio nanostructures with precise control over their dimensions and morphology. This advanced etching process leverages the catalytic properties of metal nanoparticles to direct and enhance the chemical etching of semiconductor materials, most notably silicon. MACE has found significant applications in various domains, including photonics, electronics, sensing, and energy harvesting.
This article aims to provide an exhaustive analysis of metal-assisted chemical etching, detailing its principles, mechanisms, methodologies, applications, and recent advancements. The discussion is framed within a scientific context, suitable for both newcomers and experts in the field.
The Fundamentals of Metal-Assisted Chemical Etching
Metal-assisted chemical etching is a wet chemical process that involves the use of noble metal catalysts, typically in the form of nanoparticles or thin films, to facilitate the etching of semiconductor materials. The process is highly effective in creating nanostructures with precise control over their size, shape, and distribution.
Basic Principles
The basic principle of MACE relies on the localized catalytic action of metal particles. When a semiconductor substrate, such as silicon, is exposed to a solution containing an etchant (such as hydrofluoric acid) and an oxidizing agent (such as hydrogen peroxide), the metal nanoparticles act as catalysts, enhancing the local etching rate. The overall reaction can be summarized as follows:
Si+6HF+2H2O2→H2SiF6+4H2O
In the presence of metal nanoparticles, the local oxidation of silicon occurs more efficiently, leading to the preferential dissolution of silicon beneath the metal particles. This results in the formation of well-defined nanostructures.
Mechanisms of MACE
The MACE process involves several key mechanisms, including:
- Oxidation-Reduction Reactions: The metal nanoparticles facilitate the reduction of the oxidizing agent (H₂O₂), which, in turn, oxidizes the silicon surface.
- Localized Etching: The oxidized silicon is dissolved by the hydrofluoric acid, resulting in the etching of silicon beneath the metal particles.
- Anisotropic Etching: The directionality of the etching process can be controlled by the orientation of the metal particles and the crystallographic planes of the silicon substrate.
These mechanisms work synergistically to produce nanostructures with high precision and control.
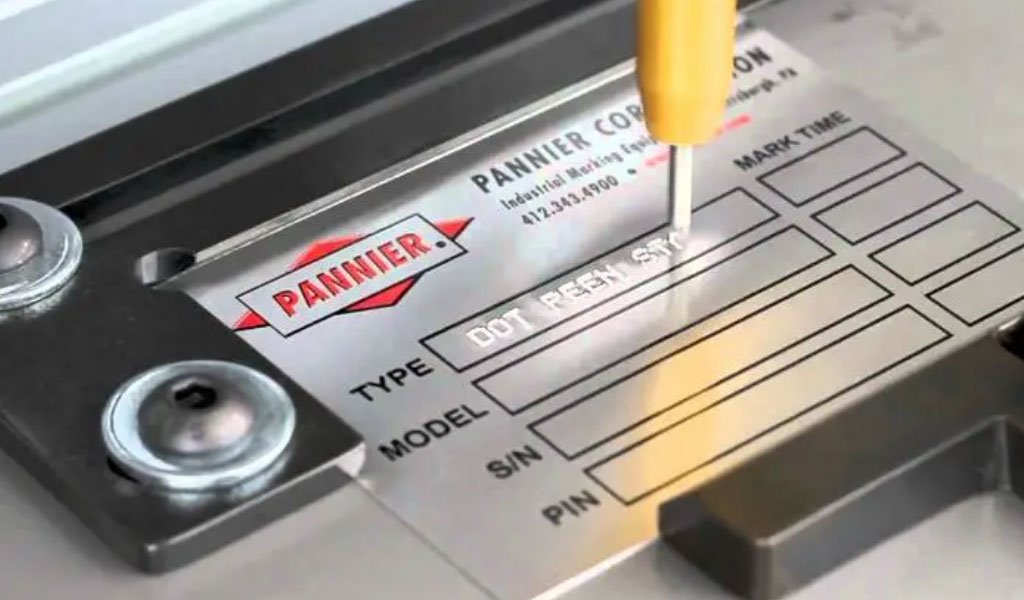
Historical Context and Development
The concept of metal-assisted chemical etching can be traced back to the early 2000s, when researchers first observed the catalytic effects of metal nanoparticles in silicon etching. Since then, the technique has undergone significant development, driven by advances in nanotechnology and materials science.
Pioneering studies demonstrated the ability to create vertically aligned silicon nanowires using silver nanoparticles as catalysts.
These initial experiments laid the foundation for the widespread adoption of MACE in various applications, leading to a deeper understanding of the underlying mechanisms and optimization of the process parameters.
Methodologies and Process Parameters
The MACE process involves several critical steps, each requiring meticulous control to achieve the desired etching outcomes. The following sections outline the key methodologies and process parameters involved in metal-assisted chemical etching.
Preparation of Metal Catalysts
The first step in MACE is the preparation and deposition of metal catalysts on the semiconductor substrate. Commonly used metals include silver, gold, and platinum, chosen for their excellent catalytic properties and stability. The metal catalysts can be deposited using various techniques, such as:
- Electroless Deposition: A chemical process that deposits metal nanoparticles onto the substrate without the use of an external electric current.
- Sputtering: A physical vapor deposition method that creates a thin metal film on the substrate surface.
- Thermal Evaporation: A process that involves heating a metal source to produce a vapor that condenses onto the substrate.
The choice of deposition technique affects the size, distribution, and morphology of the metal catalysts, which in turn influences the etching process.
Etching Solution Composition
The composition of the etching solution is a crucial parameter in MACE. A typical etching solution consists of hydrofluoric acid (HF) and hydrogen peroxide (H₂O₂) in varying concentrations. The ratio of HF to H₂O₂ determines the etching rate, with higher concentrations of HF leading to faster etching.
The concentration of the etching solution must be carefully controlled to balance the etching rate and the quality of the nanostructures. Additionally, additives such as surfactants can be used to modify the surface tension and enhance the uniformity of the etching process.
Process Parameters
Several process parameters influence the outcome of MACE, including:
- Etching Time: The duration of the etching process determines the depth and morphology of the etched nanostructures.
- Temperature: The etching temperature affects the reaction kinetics and the etching rate. Higher temperatures generally increase the etching rate but may also lead to undesirable side reactions.
- Agitation: Gentle agitation of the etching solution ensures uniform etching and prevents the formation of gas bubbles on the substrate surface.
Optimizing these parameters is essential for achieving high-quality nanostructures with the desired properties.
Applications of Metal-Assisted Chemical Etching
The versatility and precision of MACE have led to its adoption in a wide range of applications. The following sections highlight some of the most significant applications of this technique.
Photonics and Optoelectronics
MACE is widely used in the fabrication of nanostructures for photonics and optoelectronics. Silicon nanowires and nanopores created using MACE exhibit unique optical properties, making them ideal for applications such as:
- Solar Cells: Silicon nanowires enhance light absorption and reduce reflection, improving the efficiency of solar cells.
- Light-Emitting Diodes (LEDs): Nanostructured silicon can be used to create LEDs with improved light emission characteristics.
- Photodetectors: High-aspect-ratio silicon nanowires enhance the sensitivity and response speed of photodetectors.
Sensing Applications
The high surface area and tunable properties of nanostructures created by MACE make them ideal for sensing applications. These include:
- Biosensors: Silicon nanowires functionalized with biomolecules can detect specific biological targets with high sensitivity and selectivity.
- Chemical Sensors: Nanostructured silicon can be used to detect various chemical species, including gases and organic compounds, through changes in electrical conductivity or optical properties.
Energy Harvesting
MACE-fabricated nanostructures are also used in energy harvesting applications, such as:
- Thermoelectric Devices: Nanostructured silicon exhibits enhanced thermoelectric properties, enabling efficient conversion of heat to electricity.
- Supercapacitors: High-aspect-ratio silicon nanowires provide a large surface area for charge storage, improving the performance of supercapacitors.
Microelectromechanical Systems (MEMS)
MACE is employed in the fabrication of MEMS devices, which require precise control over the dimensions and morphology of micro- and nanostructures. Applications include:
- Accelerometers and Gyroscopes: Nanostructured silicon improves the sensitivity and performance of MEMS-based motion sensors.
- Micromirrors and Microlenses: High-aspect-ratio silicon structures enhance the functionality of optical MEMS devices.
Recent Advancements in Metal-Assisted Chemical Etching
Advancements in materials science, nanotechnology, and process engineering have led to significant improvements in MACE. The following sections discuss some of the recent developments and innovations in this field.
Enhanced Catalysts
Research efforts have focused on developing novel metal catalysts that improve the efficiency and precision of MACE. For example, bimetallic catalysts, which combine two different metals, have shown enhanced catalytic activity and stability compared to single-metal catalysts. Additionally, the use of alloy nanoparticles allows for fine-tuning of the etching properties.
Nanoparticle Shape and Size Control
Controlling the shape and size of metal nanoparticles is crucial for achieving uniform and well-defined nanostructures. Advances in nanoparticle synthesis techniques have enabled the production of nanoparticles with precise control over their dimensions and morphology. Shape-controlled nanoparticles, such as nanocubes and nanorods, offer unique etching characteristics that can be exploited to create complex nanostructures.
Patterned Deposition Techniques
Patterned deposition techniques, such as nanosphere lithography and block copolymer lithography, have been developed to create well-ordered arrays of metal nanoparticles on semiconductor substrates. These techniques enable the fabrication of highly uniform and reproducible nanostructures, essential for applications in photonics, electronics, and sensing.
Environmental Considerations
Environmental concerns have driven the development of more sustainable MACE processes. Researchers are exploring green etching solutions that reduce or eliminate the use of hazardous chemicals. For example, the use of eco-friendly oxidizing agents and etchants derived from natural sources is being investigated as alternatives to conventional HF and H₂O₂ solutions.
Conclusion
Metal-assisted chemical etching is a versatile and powerful technique that has revolutionized the field of nanofabrication. Its ability to create high-aspect-ratio nanostructures with precise control over their dimensions and morphology has opened up new possibilities in photonics, electronics, sensing, and energy harvesting. As research in this field continues to advance, we can expect further innovations that will enhance the efficiency, precision, and sustainability of MACE processes.
This comprehensive overview provides a solid foundation for understanding the principles, methodologies, applications, and recent advancements in metal-assisted chemical etching. Whether you are a novice seeking to learn the basics or an experienced professional looking to stay abreast of the latest developments, the information presented here will serve as a valuable resource in the rapidly evolving field of nanofabrication.