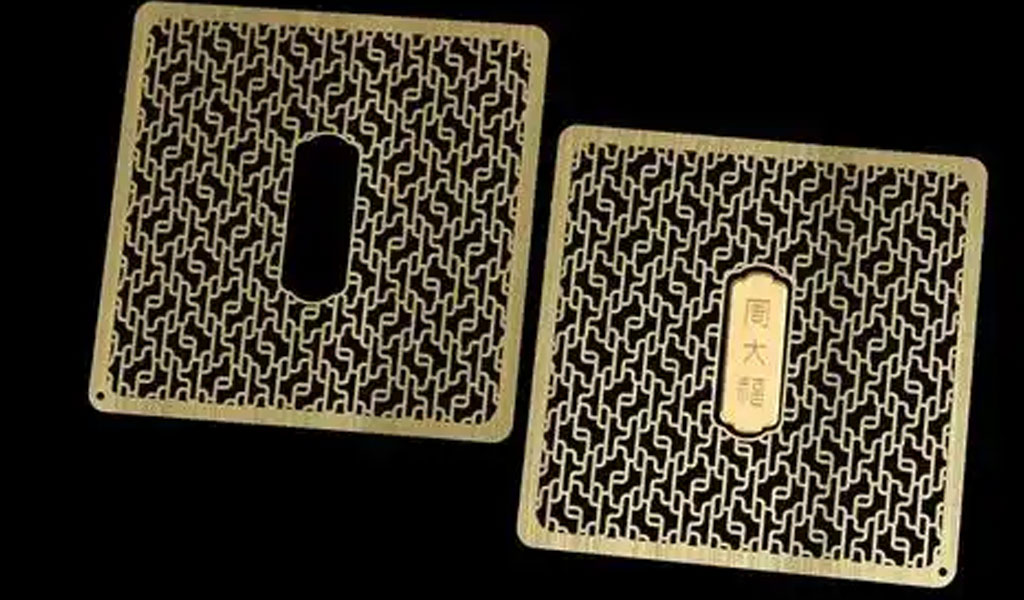
Wet etching and dry etching are two critical techniques in the field of materials processing, particularly in microfabrication and semiconductor industries.
These methods are essential for the precise and controlled removal of materials from a substrate, a process vital in creating intricate patterns and structures on materials, including metals, semiconductors, and ceramics. Understanding the differences, advantages, disadvantages, and applications of wet and dry etching is crucial for anyone involved in manufacturing, particularly those working in fields like microelectronics, optics, and nanotechnology.
Overview of Etching Processes
Etching is the process of selectively removing material from a substrate to create patterns, shapes, or structures. This is often done using a chemical or physical method, with the most common types being wet etching and dry etching. Both processes rely on a reactive agent—chemicals or gases—that interacts with the material to remove it in a controlled manner. The key difference between the two methods lies in the state of the etching medium and how it interacts with the substrate.
Wet etching involves the use of liquid chemicals to dissolve the material from the substrate. This method is known for being simpler and easier to control in many cases. It is commonly used for bulk etching or when creating relatively large features. Dry etching, on the other hand, uses gases or plasmas to etch the material, offering higher precision, control, and the ability to etch more complex or smaller features. It is commonly used in industries such as semiconductor manufacturing, where the need for fine feature sizes and high precision is paramount.
Wet Etching
Wet etching has been in use for many years and is often the first choice for applications requiring relatively simple etching processes. It uses liquid chemicals, often acids or bases, to chemically react with the material to remove it. The substrate is typically immersed in the etchant solution, which dissolves the material from the exposed areas, creating the desired pattern. The process is often relatively straightforward and cost-effective, making it an attractive option for many manufacturers.
Advantages of Wet Etching
- Simplicity and Cost-Effectiveness: Wet etching is generally simpler than dry etching, requiring fewer sophisticated tools and equipment. It can be carried out in a straightforward manner by immersing the material in a chemical bath, making it less expensive than dry etching, which often requires specialized equipment such as reactors and vacuum chambers.
- High Selectivity: Wet etching can provide a high degree of selectivity when it comes to different materials. For instance, certain acids or bases can be used to etch specific metals while leaving other materials unaffected. This property makes it ideal for applications where selective material removal is needed.
- Uniformity: The immersion process in wet etching can result in more uniform etching across the substrate’s surface. The etchant solution evenly interacts with the material, leading to consistent etching results, especially for larger areas or when the feature sizes are not as small.
- Ease of Process Control: Wet etching is easier to control because it does not require the precise regulation of plasma or other gas environments, making it more forgiving for less critical applications.
Disadvantages of Wet Etching
- Limited Precision: While wet etching can be precise for large features, it lacks the fine resolution required for smaller or more complex patterns. The diffusion of the etching solution and the isotropic nature of the etching process can lead to undercutting, which is undesirable in many applications.
- Material Removal Depth Control: Achieving precise control over the etch depth can be challenging in wet etching. The process is often less predictable than dry etching, especially when dealing with materials that have varying resistance to etching.
- Environmental and Safety Concerns: Many of the chemicals used in wet etching, such as hydrofluoric acid (HF) and sulfuric acid, can be hazardous to both human health and the environment. Proper disposal and safety measures are necessary to prevent exposure to these toxic substances.
- Less Suitable for Small Features: Wet etching is generally not ideal for creating very fine or intricate patterns. The isotropic nature of the process causes etching to occur in all directions, making it unsuitable for microelectronics applications where precise, anisotropic etching is needed.
Applications of Wet Etching
Wet etching is commonly used in applications where high throughput and cost-effectiveness are important. It is frequently used in the preparation of semiconductor wafers, particularly when larger features need to be etched. It is also employed in metalworking, glass etching, and even in the production of printed circuit boards (PCBs), where large areas of material need to be removed efficiently.
Dry Etching
Dry etching, also referred to as plasma etching or reactive-ion etching (RIE), uses gases or plasmas to etch materials from a substrate. Unlike wet etching, which relies on liquid chemicals, dry etching involves the use of reactive gases or plasmas that are activated in a vacuum or low-pressure environment. These gases react with the material to either etch it away or deposit a protective layer that prevents etching in specific regions. Dry etching offers several advantages over wet etching, especially when high precision and fine feature sizes are required.
Types of Dry Etching
- Reactive Ion Etching (RIE): RIE is one of the most commonly used dry etching techniques. It involves the generation of a plasma in a vacuum chamber. The ions in the plasma are directed toward the substrate, where they react with the material to etch it away. The process is highly controllable, allowing for anisotropic etching, meaning that the etching occurs primarily in the vertical direction, producing sharp, well-defined features.
- Deep Reactive Ion Etching (DRIE): DRIE is an advanced form of RIE that allows for even deeper etching and is commonly used in microfabrication. It uses a combination of reactive ions and passivation steps to create deep, narrow features with minimal undercutting, making it ideal for applications like MEMS (Micro-Electro-Mechanical Systems) and microfluidic devices.
- Plasma Etching: Plasma etching uses plasma in a reactive environment to etch materials, typically for cleaning or etching non-metallic substrates such as polymers or ceramics. Plasma etching can be highly effective for etching organic materials and is widely used in surface preparation processes.
- Ion Beam Etching: This method uses an ion beam directed at the substrate to physically sputter away the material. Ion beam etching is often employed for high-precision applications and when etching materials like metals and semiconductors.
Advantages of Dry Etching
- Precision and Resolution: One of the key advantages of dry etching is its ability to achieve very fine resolution and high precision. Because dry etching can be highly directional (anisotropic), it can produce sharp, well-defined features with minimal lateral etching or undercutting. This makes it ideal for the production of microelectronics and MEMS devices where fine detail is critical.
- Control Over Etch Depth: Dry etching allows for more precise control over the etch depth compared to wet etching. With techniques like RIE and DRIE, etching depths can be controlled on the nanometer scale, making these methods suitable for applications that require deep etches with high precision.
- Anisotropic Etching: Dry etching processes, such as reactive ion etching, allow for anisotropic etching, where the material is etched predominantly in one direction, usually vertically. This is important for applications where it is necessary to avoid lateral etching and achieve clean, sharp edges.
- Suitability for Small Features: Dry etching is the preferred method for etching small features or intricate designs. The precision and control offered by dry etching make it ideal for microelectronics, where feature sizes are often on the order of micrometers or smaller.
Disadvantages of Dry Etching
- Complex Equipment: Dry etching requires specialized equipment such as vacuum chambers and plasma reactors, which can be expensive to purchase and maintain. The complexity of the equipment also adds to the cost and difficulty of the process, particularly for small-scale applications.
- Slower Processing Time: While dry etching can achieve highly precise results, the process tends to be slower than wet etching. This can be a limiting factor in high-throughput manufacturing environments where speed is critical.
- Material Limitations: Dry etching can be less effective on certain materials, especially those that do not easily react with the gases used in the process. Additionally, some materials may require specialized etchants or processes, which can add to the cost and complexity.
- Risk of Plasma Damage: The plasma used in dry etching can sometimes cause damage to delicate materials, such as thin films or certain polymers. The reactive ions and radicals in the plasma may also introduce defects in the material, especially if the etching conditions are not carefully controlled.
Applications of Dry Etching
Dry etching is primarily used in industries that require high-precision etching, such as semiconductor manufacturing, MEMS fabrication, and nanotechnology. It is essential in the creation of integrated circuits, microchips, and microelectromechanical systems, where feature sizes are extremely small and precision is paramount. Dry etching is also used in the production of microfluidic devices, optical components, and even for some types of metal etching.
Comparison of Wet Etching vs Dry Etching
Both wet etching and dry etching have distinct advantages and limitations, and the choice of method largely depends on the specific requirements of the application. Wet etching is simpler, more cost-effective, and well-suited for large-area etching and bulk material removal. However, its lack of precision and isotropic nature make it less suitable for fine or intricate patterns. Dry etching, on the other hand, provides greater control, precision, and resolution, making it the preferred choice for applications requiring high-resolution patterns or the creation of small features. However, dry etching is more complex, slower, and requires more expensive equipment.
In many manufacturing environments, the two methods are used in tandem to achieve the desired results. Wet etching might be used for initial material removal or for bulk etching, while dry etching is employed for fine feature creation and high-precision tasks. Understanding the strengths and weaknesses of each method is crucial for selecting the most appropriate etching technique for a given application.
Conclusion
Wet etching and dry etching are both indispensable techniques in modern manufacturing, especially in fields like semiconductor production, microelectronics, and nanotechnology. Wet etching remains a valuable tool for cost-effective, large-scale etching applications, while dry etching continues to be the gold standard for high-precision, high-resolution processes. Both techniques have their place in the etching toolbox, and advances in materials science and etching technology will continue to refine and improve these methods, offering even more precise, efficient, and versatile etching capabilities for future applications.