Thin-film transistor liquid crystal displays (TFT-LCDs) have become ubiquitous in modern electronic devices, ranging from smartphones and tablets to televisions and computer monitors. The demand for thinner, lighter, and more efficient displays has driven significant advancements in manufacturing technologies. One such technology is chemical etching thinning, which has emerged as a critical process in the production of TFT-LCD panels. This article delves into the intricacies of chemical etching thinning, its impact on product reliability, and a comprehensive analysis of the associated research and development efforts.
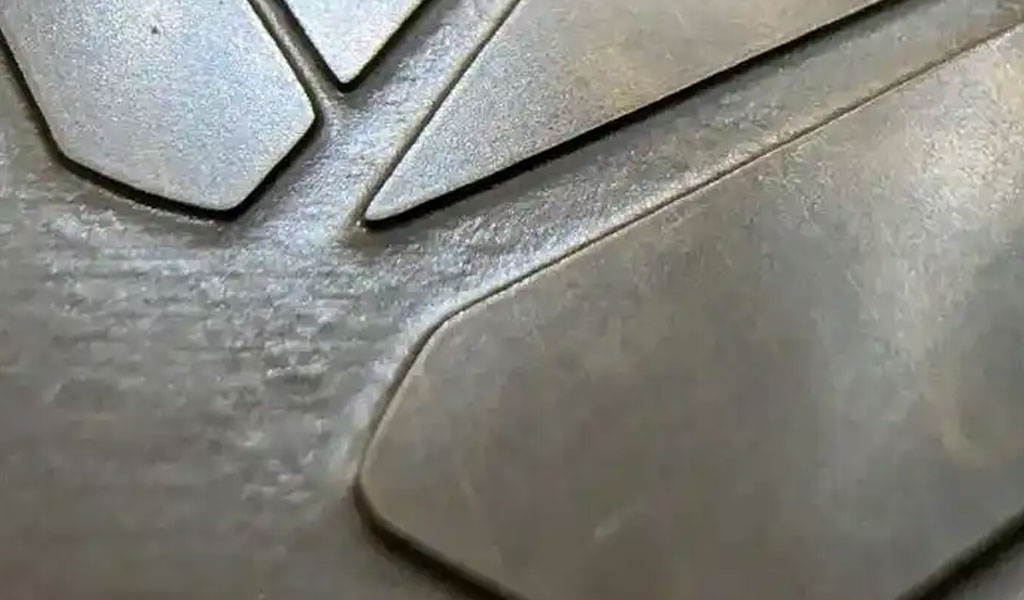
Chemical Etching Thinning: An Overview
Chemical etching thinning is a process that involves the selective removal of material from a substrate using chemical agents. In the context of TFT-LCD panels, this process is employed to reduce the thickness of the glass substrate, thereby enhancing the overall flexibility and lightness of the display. The primary objective is to achieve a uniform and controlled reduction in thickness without compromising the structural integrity and optical properties of the panel.The chemical etching process typically involves the following steps:
- Surface Preparation: The glass substrate is cleaned to remove any contaminants that could interfere with the etching process. This step is crucial for ensuring uniform etching and preventing defects.
- Masking: A protective mask is applied to the areas of the substrate that are not to be etched. This mask is usually made of a material that is resistant to the etching chemicals.
- Etching: The substrate is immersed in an etching solution, which selectively removes material from the unmasked areas. The composition and concentration of the etching solution, as well as the duration of the etching process, are carefully controlled to achieve the desired thickness reduction.
- Rinsing and Drying: After etching, the substrate is rinsed to remove any residual chemicals and then dried to prepare it for further processing.
Chemical Agents and Etching Mechanisms
The choice of chemical agents is critical to the success of the etching process. Common etching agents include hydrofluoric acid (HF), buffered oxide etch (BOE), and various proprietary solutions developed by manufacturers. Each of these agents has its unique properties and etching mechanisms, which are summarized in Table 1.
Chemical Agent | Composition | Etching Mechanism | Advantages | Disadvantages |
---|---|---|---|---|
Hydrofluoric Acid (HF) | HF in water | Dissolves silicon dioxide (SiO2) | High etch rate, uniform etching | Highly corrosive, hazardous to handle |
Buffered Oxide Etch (BOE) | HF and ammonium fluoride (NH4F) | Dissolves SiO2, buffered to control etch rate | Controlled etch rate, safer than HF | Slower etch rate compared to HF |
Proprietary Solutions | Varies by manufacturer | Varies by manufacturer | Optimized for specific applications | Often expensive, proprietary formulations |
Factors Affecting Etching Performance
Several factors influence the performance of the chemical etching process, including temperature, concentration of the etching solution, and the duration of the etching process. These factors are interdependent and must be carefully controlled to achieve the desired results.
- Temperature: Higher temperatures generally increase the etch rate but can also lead to non-uniform etching and increased risk of defects. Optimal temperature control is essential for consistent results.
- Concentration: The concentration of the etching solution affects the etch rate and uniformity. Higher concentrations can accelerate the etching process but may also increase the risk of over-etching and surface damage.
- Duration: The duration of the etching process determines the final thickness of the substrate. Prolonged etching can result in excessive material removal and structural weakness.
Product Reliability Analysis
The reliability of TFT-LCD panels is a critical concern for manufacturers and consumers alike. Chemical etching thinning, while beneficial for reducing thickness and weight, can introduce potential reliability issues if not properly controlled. Key reliability factors include mechanical strength, optical performance, and environmental durability.
- Mechanical Strength: Thinning the glass substrate can reduce its mechanical strength, making it more susceptible to fractures and cracks. Advanced etching techniques and post-etching treatments, such as annealing, can help mitigate these risks.
- Optical Performance: The optical properties of the TFT-LCD panel, including transmittance, reflectance, and color uniformity, must be preserved during the etching process. Any deviations can result in poor display quality and reduced user satisfaction.
- Environmental Durability: TFT-LCD panels must withstand various environmental conditions, including temperature changes, humidity, and mechanical stress. Chemical etching can affect the panel’s resistance to these conditions, necessitating rigorous testing and optimization.
Research and Development Efforts
Significant research and development efforts have been dedicated to improving the chemical etching thinning process and enhancing the reliability of TFT-LCD panels. Key areas of focus include:
- Advanced Etching Techniques: Researchers are exploring new etching techniques, such as plasma etching and reactive ion etching, which offer greater control and precision compared to traditional chemical etching.
- Material Innovations: The development of new glass substrate materials with improved mechanical and optical properties is an active area of research. These materials can withstand the etching process better and provide enhanced reliability.
- Process Optimization: Optimizing the etching process parameters, such as temperature, concentration, and duration, is crucial for achieving consistent and reliable results. Advanced modeling and simulation tools are being employed to predict and optimize etching outcomes.
- Quality Control: Implementing robust quality control measures, including in-line inspection and real-time monitoring, can help detect and correct defects early in the production process, ensuring higher reliability.
Comparative Analysis of Etching Techniques
Table 2 provides a comparative analysis of various etching techniques, highlighting their advantages, disadvantages, and applications.
Etching Technique | Advantages | Disadvantages | Applications |
---|---|---|---|
Chemical Etching | High etch rate, uniform etching | Highly corrosive, hazardous to handle | General thinning of glass substrates |
Plasma Etching | High precision, low damage | Complex equipment, higher cost | Precision thinning, selective etching |
Reactive Ion Etching | High control, low damage | Complex equipment, higher cost | Precision thinning, selective etching |
Laser Etching | High precision, non-contact | High cost, limited throughput | Precision thinning, selective etching |
Case Studies and Industry Applications
Several case studies and industry applications illustrate the practical implementation of chemical etching thinning in TFT-LCD panel production. For instance, a leading display manufacturer employed chemical etching to reduce the thickness of their glass substrates by 50%, resulting in a 30% reduction in panel weight and improved flexibility. Another example involves the use of plasma etching to achieve precise thinning of high-resolution displays, enhancing their optical performance and reliability.
Future Directions
The future of chemical etching thinning in TFT-LCD panel production holds promise for further advancements. Key areas of focus include:
- Sustainable Etching Solutions: Developing environmentally friendly etching solutions that minimize waste and reduce the environmental impact of the manufacturing process.
- Integrated Processes: Integrating chemical etching with other manufacturing processes, such as lamination and coating, to streamline production and enhance overall efficiency.
- Advanced Monitoring and Control: Implementing advanced monitoring and control systems, including machine learning and artificial intelligence, to optimize the etching process and ensure consistent quality.
- New Materials and Technologies: Exploring new materials and technologies, such as flexible substrates and roll-to-roll processing, to meet the evolving demands of the display industry.
Conclusion
Chemical etching thinning is a vital process in the production of TFT-LCD panels, offering significant benefits in terms of reduced thickness, weight, and enhanced flexibility. However, achieving these benefits while maintaining product reliability requires careful control and optimization of the etching process. Ongoing research and development efforts are focused on advancing etching techniques, improving material properties, and enhancing process control to meet the growing demands of the display industry. As technology continues to evolve, chemical etching thinning will play a crucial role in shaping the future of TFT-LCD panels and other display technologies.