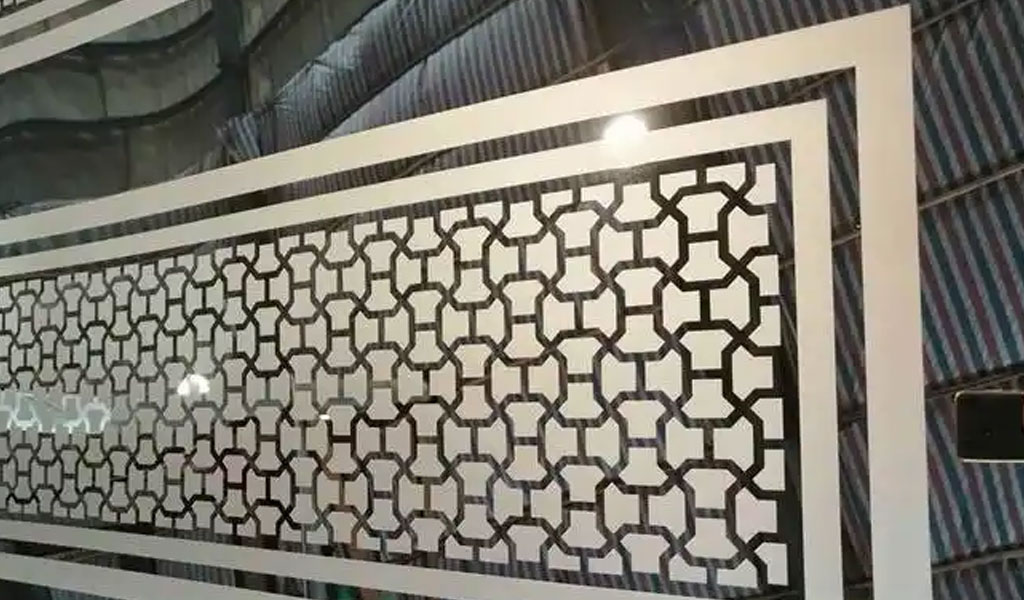
Stainless steel pattern etching is a sophisticated manufacturing process used to create intricate designs and patterns on stainless steel surfaces.
This technology is widely employed in various industries, including electronics, automotive, aerospace, and medical devices, due to its precision, durability, and aesthetic appeal.
The process involves the selective removal of material from the stainless steel surface using chemical or physical means, resulting in highly detailed and accurate patterns.
Introduction to Stainless Steel
Stainless steel is an alloy of iron with a minimum of 10.5% chromium. The chromium forms a passive layer of chromium oxide on the surface, which prevents further corrosion and provides the material with its characteristic resistance to staining and rusting. There are several types of stainless steel, each with unique properties and applications. The most common types include:
- Austenitic Stainless Steel: Contains high levels of chromium and nickel, making it highly resistant to corrosion. It is non-magnetic and has excellent formability.
- Ferritic Stainless Steel: Contains chromium but little or no nickel. It is magnetic and has good resistance to corrosion and stress corrosion cracking.
- Martensitic Stainless Steel: Contains chromium and carbon, making it hardenable through heat treatment. It is magnetic and has moderate corrosion resistance.
- Duplex Stainless Steel: A combination of austenitic and ferritic structures, offering a balance of strength, toughness, and corrosion resistance.
- Precipitation Hardening Stainless Steel: Can be hardened by a heat treatment process that precipitates hard particles within the microstructure.
Pattern Etching Techniques
Pattern etching on stainless steel can be achieved through various techniques, each with its own advantages and limitations. The primary methods include chemical etching, laser etching, and photochemical machining.
Chemical Etching
Chemical etching, also known as photo etching or photochemical etching, is a subtractive manufacturing process that uses chemical solutions to remove material from the stainless steel surface. The process involves several steps:
- Cleaning: The stainless steel surface is thoroughly cleaned to remove any contaminants that could interfere with the etching process.
- Masking: A photoresist material is applied to the surface. This material is sensitive to ultraviolet (UV) light and will harden when exposed.
- Exposure: The photoresist is exposed to UV light through a photomask, which contains the desired pattern. The exposed areas harden, while the unexposed areas remain soft.
- Developing: The unexposed photoresist is removed, leaving the hardened areas as a protective mask.
- Etching: The stainless steel is immersed in an etching solution, typically a mixture of ferric chloride and hydrochloric acid, which selectively removes the unprotected areas.
- Stripping: The remaining photoresist is removed, revealing the etched pattern.
- Finishing: The etched surface may undergo additional finishing processes, such as polishing or plating, to enhance its appearance and durability.
Laser Etching
Laser etching uses high-energy laser beams to vaporize material from the stainless steel surface. This method is highly precise and can create intricate patterns with fine details. The process involves the following steps:
- Design: The desired pattern is created using computer-aided design (CAD) software.
- Programming: The CAD file is converted into a format that can be understood by the laser etching machine.
- Etching: The laser beam is focused on the stainless steel surface, vaporizing the material in the areas defined by the pattern.
- Finishing: The etched surface may undergo additional finishing processes to enhance its appearance and durability.
Photochemical Machining
Photochemical machining (PCM) is a combination of chemical etching and photolithography. It is particularly suitable for creating complex patterns with high precision. The process involves the following steps:
- Cleaning: The stainless steel surface is cleaned to remove any contaminants.
- Laminating: A photoresist material is laminated onto the surface.
- Exposure: The photoresist is exposed to UV light through a photomask containing the desired pattern.
- Developing: The unexposed photoresist is removed, leaving the hardened areas as a protective mask.
- Etching: The stainless steel is immersed in an etching solution, which selectively removes the unprotected areas.
- Stripping: The remaining photoresist is removed, revealing the etched pattern.
- Finishing: The etched surface may undergo additional finishing processes to enhance its appearance and durability.
Comparison of Etching Techniques
The following table compares the different etching techniques based on various parameters:
Parameter | Chemical Etching | Laser Etching | Photochemical Machining |
---|---|---|---|
Precision | High | Very High | Very High |
Complexity | Moderate | High | High |
Cost | Moderate | High | High |
Speed | Moderate | Fast | Moderate |
Material Removal | Chemical Solution | Laser Beam | Chemical Solution |
Surface Finish | Good | Excellent | Excellent |
Applications | Electronics, Medical Devices | Aerospace, Automotive, Electronics | Electronics, Medical Devices |
Applications of Stainless Steel Pattern Etching
Stainless steel pattern etching is used in a wide range of applications due to its precision, durability, and aesthetic appeal. Some of the key applications include:
- Electronics: Etched stainless steel is used in the manufacture of printed circuit boards (PCBs), connectors, and other electronic components. The precision and conductivity of stainless steel make it ideal for these applications.
- Automotive: Etched stainless steel is used in the production of fuel injectors, sensors, and other automotive components. The corrosion resistance and durability of stainless steel make it suitable for harsh automotive environments.
- Aerospace: Etched stainless steel is used in the manufacture of aircraft components, such as turbine blades, sensors, and control systems. The high strength-to-weight ratio and corrosion resistance of stainless steel make it ideal for aerospace applications.
- Medical Devices: Etched stainless steel is used in the production of surgical instruments, implants, and other medical devices. The biocompatibility and corrosion resistance of stainless steel make it suitable for medical applications.
- Industrial: Etched stainless steel is used in the manufacture of filters, screens, and other industrial components. The durability and corrosion resistance of stainless steel make it ideal for industrial applications.
Advantages and Limitations
Advantages
- Precision: Stainless steel pattern etching allows for the creation of highly detailed and accurate patterns with fine tolerances.
- Durability: Stainless steel is highly resistant to corrosion, wear, and tear, making it suitable for long-term use in various applications.
- Aesthetic Appeal: Etched stainless steel has a polished and professional appearance, making it suitable for decorative and functional applications.
- Versatility: Stainless steel pattern etching can be used in a wide range of industries and applications, from electronics to medical devices.
Limitations
- Cost: The equipment and materials required for stainless steel pattern etching can be expensive, making it a costly process.
- Complexity: The process involves multiple steps and requires specialized knowledge and skills, making it complex and time-consuming.
- Environmental Impact: The chemical solutions used in etching can be hazardous and require proper disposal to minimize environmental impact.
Future Trends
The field of stainless steel pattern etching is continually evolving, driven by advancements in technology and increasing demand for precision and durability in various industries. Some of the future trends in this field include:
- Advanced Materials: The development of new stainless steel alloys with enhanced properties, such as improved corrosion resistance and strength, will expand the applications of pattern etching.
- Automation: The integration of automation and robotics in the etching process will increase efficiency, reduce costs, and improve consistency.
- Sustainability: The development of eco-friendly etching solutions and recycling processes will minimize the environmental impact of stainless steel pattern etching.
- Nanotechnology: The application of nanotechnology in pattern etching will enable the creation of even more precise and intricate patterns, opening up new possibilities in various industries.
Conclusion
Stainless steel pattern etching is a critical technology in modern manufacturing, offering precision, durability, and aesthetic appeal. The various etching techniques, including chemical etching, laser etching, and photochemical machining, each have their own advantages and limitations. The wide range of applications, from electronics to medical devices, highlights the versatility and importance of this technology. As advancements continue, the future of stainless steel pattern etching promises even greater possibilities and innovations.