Electromagnetic interference (EMI) and radio-frequency interference (RFI) are ubiquitous in our connected world. The ever-expanding landscape of electronics and wireless communication has made shielding against these disruptive forces a fundamental consideration. Shielding materials, particularly metals, play a critical role in protecting sensitive electronics from EMI and RFI. In this comprehensive guide, we will delve into the science and technology behind metal selection for EMI and RFI shielding.
Understanding EMI and RFI
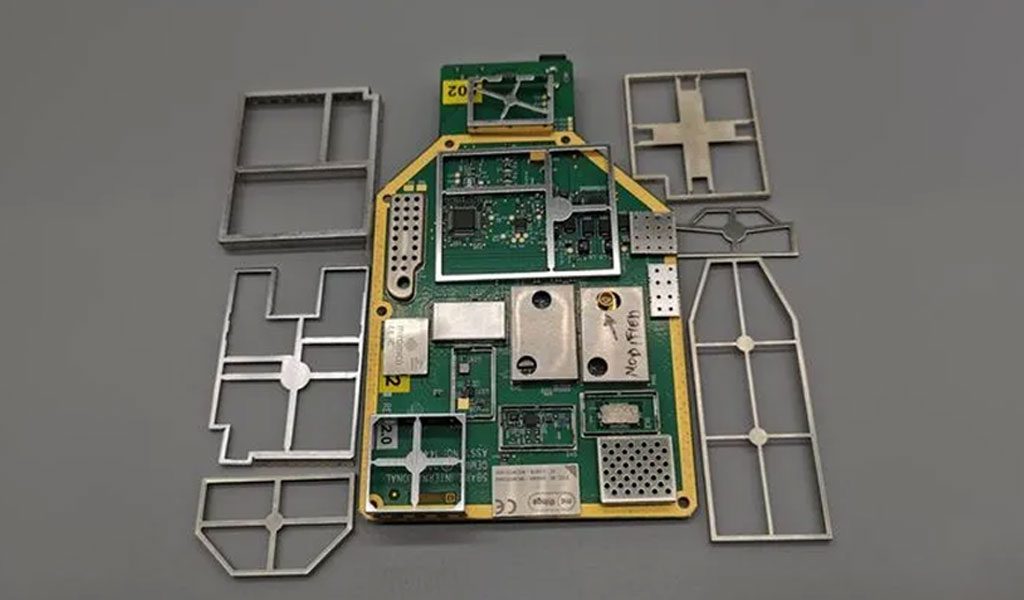
What is EMI?
Electromagnetic Interference (EMI) refers to the interference or disturbance caused by electromagnetic radiation from one electronic or electrical device that affects the operation of another nearby device. In essence, EMI occurs when unwanted electromagnetic emissions generated by one device negatively impact the functioning of another. These emissions can manifest as electrical noise, voltage spikes, or electromagnetic radiation in various frequency ranges.
EMI can result in a wide range of problems, from signal degradation to complete equipment failure. This phenomenon is particularly significant in industries heavily reliant on electronic and wireless technology, such as telecommunications, aerospace, and healthcare.
What is RFI?
Radio-Frequency Interference (RFI) is a subset of EMI that specifically occurs in the radio frequency (RF) spectrum. RFI is a form of electromagnetic interference caused by unwanted emissions or signals in the RF range. This interference can disrupt the operation of radio receivers, wireless communication systems, and other RF-sensitive devices.
RFI sources can include radio transmitters, wireless communication equipment, power lines, electronic devices, and various industrial machinery. RFI can lead to a loss of signal quality, data corruption, and other operational issues in RF-dependent systems.
Sources of EMI and RFI
To effectively address and mitigate EMI and RFI, it is crucial to identify their sources. These sources can be categorized into natural and man-made, and they include:
Natural Sources of EMI and RFI
- Solar Radiation: Solar flares and other solar activities can emit electromagnetic radiation that interferes with radio communications and other electronic systems on Earth.
- Lightning: Lightning strikes generate powerful electromagnetic pulses that can disrupt nearby electronic equipment.
- Cosmic Radiation: High-energy particles from space, such as cosmic rays, can induce electromagnetic interference in sensitive electronic devices, especially at high altitudes or in outer space.
Man-Made Sources of EMI and RFI
- Electronic Devices: Everyday electronic devices, including computers, smartphones, and household appliances, can emit EMI. This is especially relevant in densely populated urban areas with a high concentration of electronic devices.
- Power Lines and Transformers: Electrical power distribution systems can emit EMI, particularly in situations where there are power fluctuations, surges, or other electrical disturbances.
- Industrial Machinery: Heavy machinery used in manufacturing and industrial processes can generate electromagnetic interference. This is a significant concern in industrial settings with sensitive control systems.
- Wireless Communication Systems: Cellular towers, Wi-Fi routers, and other wireless communication infrastructure can emit RFI, which can impact the performance of nearby electronic devices and communication networks.
Impact of EMI and RFI
EMI and RFI can have a wide range of detrimental effects on electronic systems, communication networks, and equipment, including but not limited to:
- Data Corruption: EMI and RFI can lead to errors in digital data transmission, causing incorrect data to be received, which can be critical in fields like data transmission and storage.
- Signal Degradation: Weakened signals due to interference can result in poor reception, reduced signal quality, and slower data transfer rates, affecting the functionality of communication systems and wireless networks.
- Equipment Malfunction: EMI and RFI can disrupt the normal operation of electronic devices, causing malfunctions, glitches, or complete failure. This is particularly concerning in critical applications like medical devices and aerospace technology.
- Security Risks: In some cases, EMI and RFI can pose security risks. For instance, unauthorized parties might intercept and decode sensitive data transmitted via radio waves, leading to data breaches and privacy concerns.
- Compliance Issues: Many industries are subject to regulations and standards governing EMI and RFI emissions. Failure to meet these requirements can result in legal and financial consequences for manufacturers and operators of electronic and communication systems.
EMI and RFI are challenges that impact a broad spectrum of industries and technologies. To effectively address these issues, it is essential to understand the sources, principles, and materials used for shielding against electromagnetic interference. This article will explore these aspects in detail, providing a comprehensive guide to metal selection for EMI and RFI shielding.
Principles of Shielding
Shielding is a crucial technique employed to protect electronic devices and systems from electromagnetic interference (EMI) and radio-frequency interference (RFI). The primary function of shielding is to create a barrier that isolates sensitive components from unwanted electromagnetic fields. This is achieved through a combination of reflection, absorption, and redirection of electromagnetic waves.
The fundamental principles of how shielding works
The fundamental principles of how shielding works can be summarized as follows:
- Reflection:When an electromagnetic wave encounters a conductive shield, it induces electric currents within the shield material due to the wave’s electric field. These induced currents generate an opposing electromagnetic field that reflects the incoming wave. By reflecting the EMI or RFI, the shield effectively prevents it from penetrating and interfering with the enclosed electronic components.
- Absorption:In some cases, shielding materials are designed to absorb and dissipate electromagnetic energy as heat. Absorptive shielding materials contain substances like ferrites or conductive polymers that can convert the incoming electromagnetic energy into thermal energy. Absorptive shielding is particularly useful for broadband or low-frequency interference.
- Redirection:Shielding can also redirect electromagnetic waves away from sensitive areas. This redirection is achieved through the design of the shield, which can include the use of shielding enclosures, waveguides, or other structures that guide the unwanted electromagnetic radiation away from the critical components.
The choice between reflective and absorptive shielding depends on the specific application and the frequency range of the interference. Conductive shielding, which reflects EMI and RFI, is often more effective at higher frequencies. In contrast, absorptive shielding can be beneficial for broadband or low-frequency interference that is challenging to reflect effectively.
Conductive vs. Absorptive Shielding
Conductive Shielding:
Conductive shielding relies on materials with excellent electrical conductivity to reflect and redirect electromagnetic interference. Common conductive shielding materials include metals like copper, aluminum, and steel. The effectiveness of conductive shielding is influenced by several key factors:
- Electrical Conductivity: The ability of the shielding material to conduct electrical current is crucial. Higher electrical conductivity allows for more efficient reflection of electromagnetic waves.
- Magnetic Permeability: Magnetic permeability, which is a measure of a material’s ability to become magnetized in the presence of an external magnetic field, also plays a role in conductive shielding. Some materials, like mu-metal, exhibit high magnetic permeability and are effective at shielding against magnetic fields.
- Skin Effect: At high frequencies, the skin effect causes electromagnetic currents to flow mainly on the surface of a conductor. Therefore, for effective conductive shielding at high frequencies, the surface quality and thickness of the shielding material become important considerations.
- Thickness: The thickness of the shielding material is another critical factor in conductive shielding. A thicker shield can provide more effective protection against EMI and RFI.
- Compatibility: Compatibility with the specific application, environment, and other components in the system is crucial. For example, in some applications, corrosion resistance may be a key consideration, leading to the choice of materials like stainless steel.
Absorptive Shielding:
Absorptive shielding materials are designed to dissipate electromagnetic energy as heat, thus reducing the intensity of interference. These materials typically contain substances that have high electrical resistance or properties that convert electromagnetic energy into thermal energy. Some key points regarding absorptive shielding include:
- Absorptive Substances: Absorptive shielding may utilize substances like ferrites (magnetic materials with high electrical resistance) or conductive polymers to absorb and dissipate electromagnetic energy.
- Broadband Protection: Absorptive shielding is particularly useful for broadband or low-frequency interference because it can effectively absorb a wide range of frequencies.
- Selective Absorption: It can be engineered to selectively absorb specific frequencies or ranges of frequencies, making it adaptable to specific interference sources.
- Temperature Considerations: The heat generated during absorption must be managed to prevent overheating of the shielded components, which requires careful design and cooling mechanisms.
The choice between conductive and absorptive shielding is driven by the specific requirements of the application, the frequency range of the interference, and the desired level of protection. Many applications may use a combination of both conductive and absorptive techniques to achieve optimal shielding effectiveness.
Properties of Shielding Materials
Effective EMI and RFI shielding relies on selecting materials with specific properties that enable them to reflect, absorb, or dissipate electromagnetic interference. These properties play a crucial role in the shielding performance. Let’s explore the key properties in detail:
Conductivity
Conductivity refers to a material’s ability to conduct electrical current. For EMI and RFI shielding, electrical conductivity is a fundamental property because it determines the material’s effectiveness in conducting and reflecting electromagnetic fields. Conductive materials can efficiently dissipate incoming electromagnetic energy, preventing it from penetrating the shielded area.
Key points related to conductivity in shielding materials include:
- Metals: Metals, particularly copper, aluminum, and steel, are commonly used for conductive shielding due to their high electrical conductivity. Copper is one of the most popular choices for EMI and RFI shielding because of its exceptional conductivity.
- Skin Effect: At high frequencies, the skin effect becomes prominent. This effect causes electromagnetic currents to flow mainly on the surface of a conductor. Therefore, for effective conductive shielding at high frequencies, the surface quality and thickness of the shielding material are important considerations.
- Impurities: The presence of impurities in a metal can affect its conductivity. Highly pure metals are preferred for shielding applications because they provide better shielding performance.
- Frequency Dependence: Conductivity is often frequency-dependent. Some materials may exhibit different conductivity characteristics at various frequencies. As such, the choice of shielding material should align with the specific frequency range of the interference.
Magnetic Permeability
Magnetic permeability is a measure of a material’s ability to become magnetized in the presence of an external magnetic field. For EMI and RFI shielding, magnetic permeability is significant when dealing with magnetic fields.
Key considerations regarding magnetic permeability in shielding materials include:
- High Permeability Materials: Some materials, like mu-metal, exhibit high magnetic permeability, making them effective at shielding against magnetic fields. This is especially important in applications where both electric and magnetic field shielding is required.
- Selective Shielding: Shielding materials with different levels of magnetic permeability can be used for selective shielding, allowing control over the types of interference being blocked.
- Material Composition: The composition of shielding materials can influence their magnetic permeability. Materials containing iron or other magnetic elements can exhibit significant permeability.
Skin Effect
The skin effect is a phenomenon that occurs at high frequencies. It causes electromagnetic currents to flow primarily on the surface of a conductor, rather than evenly through its entire cross-section. This effect is relevant to EMI and RFI shielding because it impacts the efficiency of the shield at higher frequencies.
Key points related to the skin effect include:
- Frequency Dependence: The skin effect becomes more pronounced at higher frequencies, making it essential to consider when selecting shielding materials for applications involving high-frequency interference.
- Surface Quality: The surface quality of the shielding material is critical. Imperfections or surface irregularities can hinder the effectiveness of the shield, especially in high-frequency applications.
- Conductor Thickness: The thickness of the conductor can affect the skin effect. Thicker conductors may reduce its impact, but the overall thickness of the shield also plays a role in shielding effectiveness.
Thickness
The thickness of a shielding material is a significant factor in determining its shielding effectiveness. A thicker shield provides a more robust barrier against electromagnetic interference.
Key points related to thickness in shielding materials include:
- Frequency Considerations: Shield thickness is often frequency-dependent. Higher frequencies may require thinner shields, while lower frequencies may benefit from thicker shields.
- Weight and Space Constraints: In certain applications, weight and space limitations may restrict the use of very thick shielding materials. In such cases, other properties, such as the material’s conductivity and magnetic permeability, become more critical.
- Shielding Enclosures: For applications where space constraints are not a concern, shielding enclosures with substantial thickness can be used to provide comprehensive protection.
Compatibility
The compatibility of shielding materials is a crucial consideration. It involves assessing whether the chosen material aligns with the specific application, environment, and other components in the system.
Key aspects of compatibility include:
- Corrosion Resistance: In environments where corrosion is a concern, selecting a shielding material with good corrosion resistance, such as stainless steel, is essential.
- Environmental Conditions: Consider the temperature range, humidity, and other environmental factors the shielding material will be exposed to. Some materials may degrade or lose effectiveness under extreme conditions.
- Integration with Other Components: Ensure that the chosen shielding material can be effectively integrated into the system and is compatible with other components, connectors, and interfaces.
- Regulatory Compliance: Some industries have strict regulations regarding the materials used for EMI and RFI shielding. Ensure that the selected material meets the necessary regulatory requirements.
Understanding the properties of shielding materials, such as conductivity, magnetic permeability, the skin effect, thickness, and compatibility, is essential for selecting the right material to effectively protect against electromagnetic interference in various applications. The choice of shielding material should align with the specific requirements and challenges of the application at hand.
Metal Selection for EMI and RFI Shielding
Selecting the appropriate metal for EMI and RFI shielding is a critical decision that influences the effectiveness of the shielding solution. Various factors, including the properties of the metal, its compatibility with the application, and cost considerations, must be taken into account. In this section, we will explore the key aspects of metal selection for EMI and RFI shielding.
Common Shielding Metals
Several metals are commonly used for EMI and RFI shielding due to their specific properties and conductivity. The most prevalent choices include:
Copper:
Copper is one of the most widely used metals for EMI and RFI shielding. It offers exceptional electrical conductivity, making it effective in reflecting and containing electromagnetic interference. Copper is often chosen for applications involving radio frequency (RF) interference.
Aluminum:
Aluminum is another popular choice for shielding due to its good electrical conductivity and lightweight properties. It is often used in applications where weight is a critical consideration, such as in aerospace and automotive industries.
Steel:
Steel is valued for its durability and magnetic properties. It is effective in shielding against both electric and magnetic fields, making it a suitable choice for applications where both types of interference need to be addressed. Stainless steel, in particular, is known for its corrosion resistance.
Nickel-Silver:
Nickel-silver, an alloy of copper, nickel, and zinc, is chosen for its combination of electrical conductivity and corrosion resistance. It is often used in precision instruments and electronics.
Mu-Metal:
Mu-metal is a nickel-iron alloy known for its high magnetic permeability, making it effective at shielding against magnetic fields. It is often used in applications where magnetic interference is a primary concern, such as in sensitive scientific instruments.
Factors Affecting Metal Selection
The choice of shielding metal depends on several factors, including:
Frequency Range:
The frequency of the interference is a critical factor in metal selection. Some metals may perform better at certain frequencies, so the choice should align with the specific frequency range of the EMI or RFI.
Material Properties:
Consider the electrical conductivity, magnetic properties, and permeability of the metal. These properties determine the material’s effectiveness in shielding against electromagnetic interference.
Weight:
In applications where weight is a concern, such as aerospace or automotive industries, lighter metals like aluminum are preferred.
Corrosion Resistance:
In environments where corrosion is a potential issue, corrosion-resistant metals like stainless steel may be necessary.
Magnetic Shielding:
For applications requiring protection against magnetic fields, metals with high magnetic permeability, like mu-metal, are suitable.
Galvanic Compatibility
Galvanic compatibility is an important consideration when selecting shielding metals, especially in applications where different metals come into contact. Galvanic compatibility refers to the likelihood of two dissimilar metals causing galvanic corrosion when they are in direct contact with each other and exposed to an electrolyte, such as moisture.
For instance, when copper and aluminum come into contact, galvanic corrosion can occur, leading to the deterioration of the shielding materials. To mitigate galvanic compatibility issues, techniques such as using galvanic isolators or gaskets made of compatible materials can be employed. Careful design and insulation can also prevent direct contact between incompatible metals.
Plating and Coating Options
In many cases, it’s possible to enhance the properties of shielding materials through plating and coating. This can be particularly useful for materials that may not have all the desired characteristics for a specific application. Plating and coating options can include:
- Tin Plating: Tin plating can improve the corrosion resistance of metals like steel. It’s often used in electronic enclosures to protect against moisture and humidity.
- Nickel Plating: Nickel plating can enhance the durability of metals like copper, providing a protective layer against wear and tear.
- Silver Coating: Silver is an excellent conductor of electricity and is sometimes applied as a thin coating to improve the conductivity of other metals.
- Paints and Conductive Coatings: Conductive paints and coatings can be applied to surfaces to add conductive properties to non-conductive materials.
- Anodizing: Anodizing aluminum creates a protective oxide layer that enhances its corrosion resistance.
The choice of plating or coating depends on the specific requirements of the application and the properties needed for effective shielding.
Cost Considerations
Cost is a significant factor in metal selection for EMI and RFI shielding. The cost of the material itself, as well as the cost of any additional processes such as plating and coating, must be factored into the decision. Some key cost considerations include:
- Material Cost: Some metals are more expensive than others, and the volume of material required for the shielding solution can impact costs.
- Processing Costs: Plating, coating, or other surface treatments can add to the overall cost of the shielding solution.
- Installation Costs: The ease of working with the chosen metal, as well as any additional installation requirements, can influence costs.
- Maintenance Costs: Consider the long-term costs associated with the material, including maintenance and replacement, if necessary.
In some cases, the choice of shielding material may be a trade-off between performance and cost, with a balance struck to meet the requirements of the specific application.
Selecting the right metal for EMI and RFI shielding is a complex decision that depends on a variety of factors, including the properties of the metal, compatibility, frequency range, and cost considerations. Careful consideration of these factors is essential to design effective and efficient shielding solutions for a wide range of applications.
Specific Applications of Metal Shielding
Metal shielding plays a critical role in various industries and applications where electromagnetic interference (EMI) and radio-frequency interference (RFI) must be mitigated to ensure the reliable operation of electronic and electrical systems. In this section, we will explore specific applications of metal shielding in different industries.
Aerospace and Defense
The aerospace and defense industry relies heavily on electronic systems, sensors, and communication devices. In this sector, metal shielding is crucial for several applications:
- Aircraft Avionics: Aircraft avionics systems are vulnerable to EMI and RFI due to the complex array of electronic components. Metal shielding is used to protect sensitive systems from interference, ensuring the safety and reliability of aircraft.
- Military Electronics: Military equipment, including radar systems, communication devices, and control systems, must operate effectively in hostile environments. Metal shielding is employed to safeguard critical electronic components from interference, including intentional jamming.
- Satellite Communication: Satellites operating in space are exposed to a range of electromagnetic radiation. Metal shielding is used to protect onboard electronics, ensuring the success of communication and navigation systems.
- Missile Guidance Systems: EMI and RFI can disrupt missile guidance systems, leading to catastrophic consequences. Metal shielding is applied to ensure accurate and reliable guidance, even in adverse electromagnetic environments.
Telecommunications
The telecommunications industry is a key user of metal shielding to ensure uninterrupted communication services:
- Cellular Base Stations: Mobile base stations, often located in urban and densely populated areas, are prone to interference from various sources. Metal shielding enclosures protect the equipment from EMI and RFI, maintaining signal quality and network reliability.
- Fiber Optic Networks: Fiber optic systems are sensitive to electromagnetic interference. Metal shielding is used to protect optical transceivers and data centers from external EMI and RFI sources.
- Telecommunication Towers: Telecommunication towers and antennas are exposed to a variety of interference, including radio signals and electrical noise. Metal enclosures and shielding materials protect the electronic components from outside interference.
Medical Devices
In the healthcare industry, metal shielding is critical to ensure the accurate and safe operation of medical devices:
- MRI Machines: Magnetic Resonance Imaging (MRI) machines generate powerful magnetic fields and radio waves. Metal shielding is used to contain these fields and prevent interference with nearby electronic equipment and medical devices.
- Implantable Medical Devices: Implantable medical devices, such as pacemakers and neurostimulators, require shielding to protect their sensitive electronics from external EMI and RFI sources.
- Diagnostic Equipment: Medical diagnostic equipment like CT scanners and X-ray machines can be sensitive to electromagnetic interference. Metal shielding ensures precise and artifact-free imaging.
Consumer Electronics
In the consumer electronics sector, metal shielding is applied to various devices to maintain performance and user experience:
- Smartphones and Tablets: These devices incorporate multiple wireless communication technologies and sensitive components. Metal shielding prevents external interference that could disrupt signals and reduce performance.
- Laptops and Computers: PCs and laptops contain various electronic components and interfaces. Metal shielding is used to safeguard internal components from EMI and RFI, which can affect device performance and data integrity.
- Home Entertainment Systems: Home theater systems and gaming consoles often contain sensitive audio and video components. Metal shielding protects against external interference to deliver high-quality audio and video experiences.
Automotive Industry
The automotive industry relies on metal shielding to ensure the proper functioning of vehicle electronics and safety systems:
- Vehicle Control Systems: Modern vehicles incorporate numerous electronic control units (ECUs) for engine management, safety systems, and infotainment. Metal shielding protects these ECUs from EMI and RFI, ensuring safe and reliable operation.
- Wireless Communication: As vehicles become more connected, they are equipped with various wireless communication systems. Metal shielding safeguards these systems from external interference, maintaining communication reliability.
- Electric and Hybrid Vehicles: Electric and hybrid vehicles rely on sensitive electronic components for power management and control. Metal shielding ensures the integrity of these components in electric and hybrid drivetrains.
Metal shielding is a critical technology in a wide range of applications and industries where the reliability and performance of electronic systems are essential. By protecting sensitive electronics from EMI and RFI, metal shielding ensures that these systems function effectively in various environments and under diverse conditions.
Testing and Evaluation of Shielding Effectiveness
Shielding effectiveness (SE) is a crucial metric used to evaluate the performance of shielding materials and structures in their ability to mitigate electromagnetic interference (EMI) and radio-frequency interference (RFI). In this section, we will delve into the concept of SE, how it is measured, and the relevant standards and regulations.
Shielding Effectiveness (SE)
Shielding Effectiveness (SE) is a measure of the reduction in the strength of an electromagnetic field that occurs when it passes through a shielding material or structure. It quantifies how effectively the shielding material or enclosure prevents electromagnetic radiation from penetrating and interfering with the enclosed electronic components. SE is typically expressed in decibels (dB) and is a ratio of the incident field strength (before shielding) to the transmitted field strength (after shielding).
A higher SE value indicates better shielding performance. It represents the ability of the shielding material to reflect, absorb, or dissipate electromagnetic energy. The calculation of SE can be expressed as:
SE=20log10(EtransmittedEincident)
Where:
- SE is the shielding effectiveness in decibels (dB).
- incidentEincident is the incident electromagnetic field strength before shielding.
- transmittedEtransmitted is the transmitted electromagnetic field strength after shielding.
Measuring SE
Measuring SE is a critical step in assessing the shielding performance of materials and enclosures. Various methods and techniques are employed to determine SE:
- Plane Wave Method: This method involves exposing the shielding material or enclosure to a plane wave of known frequency and measuring the field strength before and after the material. The ratio of these field strengths is used to calculate SE.
- Cavity Method: In this method, the material to be tested is placed in a cavity or shielded room. The electromagnetic field is introduced into the cavity, and the field strengths inside and outside the cavity are measured. The difference in field strength indicates the SE.
- Two-Enclosure Method: This technique involves two enclosures separated by the material under test. One enclosure is the source of the electromagnetic field, while the other is the receiver. By comparing the field strengths inside the source enclosure and outside the receiver enclosure, SE can be calculated.
- Free-Space Method: In this method, the material under test is placed in a free-space environment where the electromagnetic field is directed at it. The field strength before and after the material is measured, and SE is calculated.
- Insertion Loss Method: This method involves measuring the electromagnetic field inside and outside a waveguide or transmission line with and without the shielding material. The difference in field strength is used to calculate SE.
The choice of measurement method depends on the specific application and the nature of the shielding material. The accuracy of the measurement method is critical in determining the true SE of the material.
Standards and Regulations
To ensure consistency and reliability in shielding effectiveness testing, there are various standards and regulations that guide the evaluation of SE. These standards are specific to different industries and applications. Some notable standards include:
- MIL-STD-285 (Military Standard): This standard provides guidelines for the measurement of shielding effectiveness for military applications. It details the procedures and methods for evaluating SE in military environments.
- IEC 61000-4-21 (International Electrotechnical Commission): This standard outlines the testing of SE for electromagnetic compatibility (EMC) in the industrial and commercial sectors. It covers the frequency range from 30 MHz to 1 GHz.
- IEEE 299 (Institute of Electrical and Electronics Engineers): This standard provides guidelines for measuring the shielding effectiveness of materials and enclosures in the frequency range of 14 kHz to 10 GHz.
- ASTM D4935 (American Society for Testing and Materials): This standard focuses on the measurement of SE for planar materials at microwave frequencies.
- ISO 11452-9 (International Organization for Standardization): This standard specifies methods for measuring SE for vehicles and their components in automotive EMC testing.
Adherence to these standards is essential for ensuring accurate and consistent testing and evaluation of SE. Compliance with these standards is often a requirement for specific industries and applications, especially in sectors where reliable EMI/RFI shielding is critical for safety and performance.
In Conclusion
Understanding electromagnetic interference (EMI) and radio-frequency interference (RFI) and how to effectively shield against them is of paramount importance in a world increasingly dependent on electronic and wireless technologies. This comprehensive article has provided insights into the fundamental concepts, principles, and materials used in EMI and RFI shielding.
We began by exploring the definitions and sources of EMI and RFI, emphasizing the impact of these interferences on various industries. We delved into the principles of shielding, understanding how it works through reflection, absorption, and redirection of electromagnetic waves, and differentiating between conductive and absorptive shielding techniques.
The article further elucidated the critical properties of shielding materials, including conductivity, magnetic permeability, the skin effect, thickness, and compatibility. These properties play a pivotal role in selecting the right materials for effective shielding.
We then examined the factors influencing metal selection for EMI and RFI shielding, such as the frequency range, material properties, weight, corrosion resistance, and magnetic shielding. We discussed galvanic compatibility and the role of plating and coating in enhancing shielding materials. Cost considerations were also addressed, highlighting the economic aspects of material selection.
Specific applications of metal shielding in industries like aerospace and defense, telecommunications, medical devices, consumer electronics, and the automotive sector were explored. In each of these sectors, metal shielding ensures the reliable operation of electronic systems, safety, and overall performance.
Testing and evaluating shielding effectiveness (SE) were discussed, with an emphasis on the importance of SE measurement methods, including plane wave, cavity, two-enclosure, free-space, and insertion loss methods. We also delved into the relevant standards and regulations guiding the evaluation of SE in various industries, ensuring consistent and reliable testing practices.
The article concluded by highlighting advanced techniques and materials in the field of EMI and RFI shielding, such as conductive polymers, metamaterials, and nanomaterials. These innovative approaches offer the potential for more versatile and effective solutions, but they require further research and development to fully harness their capabilities.
In today’s technology-driven world, the importance of EMI and RFI shielding cannot be overstated. As electronic systems continue to advance and the spectrum of electromagnetic interference widens, the ongoing development of materials, techniques, and standards is crucial to ensure the reliability and performance of critical electronic equipment and systems.