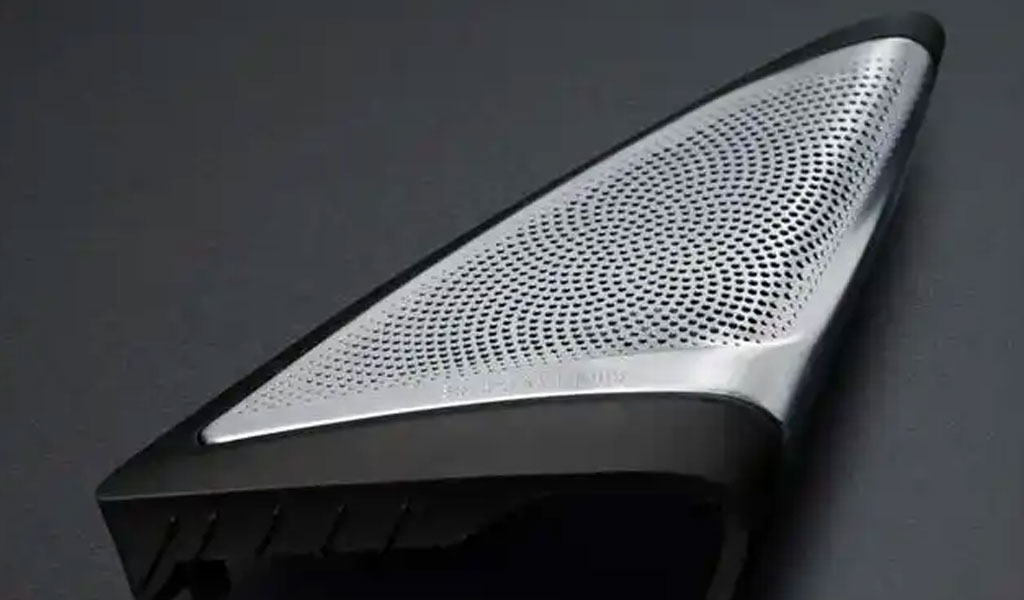
Speaker grilles are critical components in audio systems, serving both functional and aesthetic purposes. They protect delicate speaker drivers from physical damage while allowing sound waves to pass through with minimal interference. The manufacturing process for speaker grilles significantly influences their performance, durability, and visual appeal. Two prominent methods for producing metal speaker grilles are metal etching (often referred to as chemical etching or photochemical machining) and CNC (Computer Numerical Control) machining. This article provides an in-depth comparison of these two techniques, exploring their principles, applications, advantages, disadvantages, and impact on speaker grille design and performance. Detailed tables are included to facilitate a scientific and quantitative analysis.
Overview of Metal Etching Speaker Grill
Metal etching, also known as chemical etching or photochemical machining (PCM), is a subtractive manufacturing process that uses chemical etchants to selectively remove material from a metal sheet, creating precise patterns or perforations. The process begins with the application of a photoresist—a light-sensitive chemical layer—onto a metal substrate, typically stainless steel, aluminum, or copper. A photographic mask, or “phototool,” bearing the desired grille pattern is placed over the photoresist-coated metal and exposed to ultraviolet (UV) light. This exposure hardens the photoresist in areas corresponding to the mask’s transparent regions, while unexposed areas remain soluble. The soluble photoresist is then washed away, exposing the underlying metal to an etchant, such as ferric chloride, which dissolves the unprotected metal. The result is a perforated metal sheet with intricate designs, such as the hole patterns typical of speaker grilles.
The history of chemical etching dates back to the 19th century, when it was used for decorative purposes in jewelry and printmaking. Its adaptation to industrial applications, particularly in the mid-20th century, coincided with advancements in photolithography and the growing demand for precision components in electronics and aerospace. Today, metal etching is widely employed in industries requiring high-precision, thin-metal parts, including automotive, consumer electronics, and audio equipment manufacturing.
Overview of CNC Machining Speaker Grill
CNC machining is a subtractive manufacturing process that utilizes computer-controlled tools to remove material from a solid workpiece, shaping it into the desired form. For speaker grilles, CNC machining typically involves milling, where a rotating cutting tool (e.g., an end mill) removes metal from a flat sheet or block, creating perforations or contours. The process is guided by a digital design file, often in G-code format, which dictates the tool’s movements across three or more axes (X, Y, Z, and sometimes rotational axes). Common materials for CNC-machined speaker grilles include aluminum, steel, and brass, chosen for their durability and machinability.
CNC machining emerged in the 1940s and 1950s with the advent of numerical control (NC) systems, which evolved into computer numerical control with the integration of computers in the 1960s. Its versatility and precision have made it a cornerstone of modern manufacturing, applicable to everything from aerospace components to custom speaker grilles. In the context of audio equipment, CNC machining is favored for its ability to produce robust, high-quality parts with tight tolerances.
Process Comparison
Metal Etching Process Details
The metal etching process for speaker grilles involves several steps:
- Design and Phototool Creation: A digital design of the grille pattern is created using CAD (Computer-Aided Design) software. This design is transferred onto a high-resolution photographic film or glass plate, forming the phototool.
- Material Preparation: A thin metal sheet (typically 0.1–1.5 mm thick) is cleaned and coated with a photoresist layer on both sides.
- Exposure: The phototool is aligned with the coated metal and exposed to UV light, hardening the photoresist in the pattern areas.
- Development: The unexposed photoresist is removed with a chemical developer, exposing the metal beneath.
- Etching: The metal sheet is immersed in or sprayed with an etchant, which removes the unprotected metal, leaving the desired perforations.
- Cleaning and Finishing: The remaining photoresist is stripped away, and the grille may undergo secondary processes like polishing, painting, or plating.
Etching is typically isotropic, meaning the etchant removes material equally in all directions, which can result in slightly rounded hole edges. The process is highly scalable, with modern facilities employing automated lines capable of producing thousands of grilles per batch.
CNC Machining Process Details
The CNC machining process for speaker grilles follows a different workflow:
- Design and Programming: A CAD model of the grille is converted into a CNC program (G-code) using CAM (Computer-Aided Manufacturing) software.
- Material Setup: A metal sheet or block is secured to the CNC machine’s worktable, often with clamps or a vacuum system.
- Machining: The CNC machine’s spindle, equipped with a cutting tool (e.g., a drill bit or milling cutter), removes material according to the programmed path. For grilles, this typically involves drilling holes or milling slots.
- Finishing: The machined grille may be deburred, polished, or coated to enhance its appearance and durability.
CNC machining is anisotropic, with material removal dictated by the tool’s geometry and motion, resulting in sharp, well-defined edges. The process is inherently sequential, with each feature machined individually, making it less suited to high-volume production compared to etching.
Material Considerations
Both metal etching and CNC machining can process a range of metals, but their suitability varies:
- Metal Etching: Works best with thin sheets (0.1–2 mm) of metals like stainless steel, aluminum, copper, and brass. Thicker materials are impractical due to increased etching time and etchant consumption.
- CNC Machining: Can handle thicker materials (up to several centimeters) and a broader range of metals, including titanium and harder alloys, though softer metals like aluminum are preferred for speaker grilles due to ease of machining.
The choice of material affects the grille’s weight, durability, and acoustic properties. For example, aluminum offers a lightweight, corrosion-resistant option, while stainless steel provides greater strength and longevity.
Precision and Design Flexibility
Metal Etching
Metal etching excels in producing intricate, complex patterns with high precision. The process can achieve feature sizes as small as 0.1 mm, with tolerances typically around ±0.025 mm, depending on material thickness and etchant control. This makes it ideal for speaker grilles requiring fine meshes or decorative elements, such as logos or geometric patterns. The isotropic nature of etching limits its ability to create perfectly vertical sidewalls, but this is rarely a concern for grilles, where hole shape has minimal acoustic impact.
The design flexibility of etching is virtually limitless within the constraints of two-dimensional patterns. Engineers can specify hole sizes, shapes (e.g., circular, hexagonal, slotted), and spacing to optimize sound transmission and aesthetics. Additionally, etching can produce variable-depth features by controlling exposure and etchant application, though this is less common in grille manufacturing.
CNC Machining
CNC machining offers excellent precision, with tolerances as tight as ±0.01 mm achievable on high-end machines. However, its design flexibility is constrained by the cutting tool’s geometry and the sequential nature of the process. For speaker grilles, CNC machining typically produces simple hole patterns (e.g., circular or rectangular) due to the time and cost of milling complex shapes. Minimum feature sizes are larger than in etching—typically 0.5 mm or more—limited by the smallest practical tool diameter.
CNC machining can create three-dimensional features, such as beveled edges or raised contours, which are beyond the scope of standard etching. This capability is advantageous for custom or high-end grilles where structural or aesthetic enhancements are desired. However, intricate patterns with hundreds or thousands of holes become time-intensive, reducing CNC’s efficiency for such designs.
Acoustic Performance
The primary function of a speaker grille is to protect the driver while minimizing acoustic interference. Both manufacturing methods influence sound quality through hole size, open area percentage, and material properties.
- Metal Etching: Etched grilles often achieve open areas of 50–70%, with hole sizes ranging from 0.1 mm to several millimeters. Research suggests that for optimal acoustic transparency, grilles should have at least 60% open area, with hole diameters exceeding the metal thickness. Etching easily meets these criteria, producing grilles that allow sound waves to pass with minimal diffraction or attenuation. The rounded edges of etched holes may slightly reduce comb-filtering effects compared to sharp-edged alternatives.
- CNC Machining: CNC-machined grilles can also achieve high open areas, though the practical limit depends on machining time and tool wear. Hole edges are sharp and well-defined, which can introduce minor diffraction at higher frequencies, though this is typically inaudible in real-world conditions. The ability to use thicker materials may add rigidity, reducing resonance but potentially increasing reflection.
Testing by audio engineers, such as those at MISCO, indicates that metal grilles—whether etched or machined—should balance openness with structural integrity to avoid rattling or distortion. Both methods can achieve this, though etching’s finer patterns may offer a slight edge in high-frequency transparency.
Production Scalability and Cost
Metal Etching
Metal etching is highly scalable, making it cost-effective for medium to large production runs. Once the phototool is created (a one-time cost of $100–$500), the process can produce thousands of grilles with minimal additional tooling expense. Material costs are low due to the use of thin sheets, and labor is reduced by automation. For example, a facility with five 39-meter etching lines, as operated by companies like TMN, can process hundreds of square meters of metal daily. The cost per grille decreases significantly with volume, often falling below $1 for simple designs in batches of 10,000 or more.
However, etching’s upfront costs (phototool creation, setup) make it less economical for small runs or prototypes, where expenses may range from $500 to $1,000 for a few units.
CNC Machining
CNC machining is better suited to low-volume production or custom orders. Setup costs are minimal—primarily programming time and material fixturing—ranging from $50 to $200 per job. However, the process is time-intensive, with each grille requiring individual machining. For a grille with 1,000 holes, machining time could exceed an hour per unit, driving costs to $20–$50 or more, depending on labor rates and machine overhead. Economies of scale are limited, as production speed does not increase significantly with volume.
Durability and Maintenance
Etched grilles, being thinner, are more susceptible to denting or bending under impact, though their material choice (e.g., stainless steel) can mitigate corrosion. CNC-machined grilles, often thicker and more robust, offer superior resistance to physical damage, making them ideal for heavy-duty applications like PA systems or automotive speakers. Both methods allow for protective coatings (e.g., anodizing, powder coating), enhancing longevity.
Environmental Impact
Metal etching generates chemical waste, such as spent ferric chloride, requiring careful disposal or recycling. Modern facilities have reduced waste significantly—Precision Micro, for instance, cut waste from 1,881 tonnes in 2020 to 581 tonnes in 2021 through process optimization. CNC machining produces metal chips, which are recyclable, but consumes more energy per unit due to prolonged machine operation.
Comparative Tables
Table 1: Technical Specifications
Parameter | Metal Etching | CNC Machining |
---|---|---|
Material Thickness | 0.1–2 mm | 0.5–50 mm |
Minimum Feature Size | 0.1 mm | 0.5 mm |
Tolerance | ±0.025 mm | ±0.01 mm |
Hole Edge Profile | Rounded (isotropic) | Sharp (anisotropic) |
Max Open Area | 70% | 60–70% (practical limit) |
Production Speed (per unit) | Seconds (batch process) | Minutes to hours (sequential) |
Table 2: Cost Analysis
Production Volume | Metal Etching Cost (per unit) | CNC Machining Cost (per unit) |
---|---|---|
1–10 units | $50–$100 | $20–$50 |
100 units | $5–$10 | $15–$40 |
1,000 units | $1–$5 | $10–$30 |
10,000+ units | <$1 | $10–$20 |
Table 3: Acoustic and Durability Factors
Factor | Metal Etching | CNC Machining |
---|---|---|
Acoustic Transparency | High (fine, uniform holes) | High (sharp-edged holes) |
Diffraction Potential | Low (rounded edges) | Moderate (sharp edges) |
Structural Rigidity | Moderate (thin material) | High (thicker material) |
Impact Resistance | Low to moderate | High |
Corrosion Resistance | Material-dependent | Material-dependent |
Conclusion
Metal etching is prevalent in mass-produced consumer electronics and automotive speaker grilles, where companies like Precision Micro supply etched components to brands like Mercedes and Rolls-Royce. Its ability to handle intricate designs and large volumes aligns with the needs of these markets. CNC machining, conversely, is favored for custom or high-end audio systems, such as home theater speakers or boutique PA systems, where durability and unique geometries are prioritized. Hobbyists and small manufacturers also use CNC for one-off designs, as seen in Reddit communities like r/hometheater.
The choice between metal etching and CNC machining for speaker grilles depends on specific project requirements. Metal etching offers unmatched efficiency and design complexity for high-volume production, making it the preferred method for consumer and automotive applications. CNC machining, with its versatility and durability, excels in low-volume, custom, or heavy-duty scenarios. Both methods produce acoustically viable grilles, though their impact on sound quality is subtle and often overshadowed by speaker design itself. As manufacturing technologies evolve, hybrid approaches—combining etching’s scalability with CNC’s structural capabilities—may emerge, further blurring the lines between these techniques.
Metal Etching
- Advantages: High precision, intricate designs, cost-effective for large runs, minimal tool wear, rapid batch production.
- Disadvantages: Limited to thin materials, chemical waste, higher setup costs for small runs, isotropic etching limits vertical features.
CNC Machining
- Advantages: High precision, robust parts, versatile material thickness, no chemical waste, suitable for prototypes.
- Disadvantages: Time-intensive, higher cost per unit in volume, limited to simpler patterns, tool wear.
For engineers and designers, understanding the trade-offs in precision, cost, scalability, and performance is key to selecting the optimal process. The tables and analysis provided here offer a scientific foundation for such decisions, ensuring speaker grilles meet both functional and aesthetic demands in the ever-evolving audio industry.