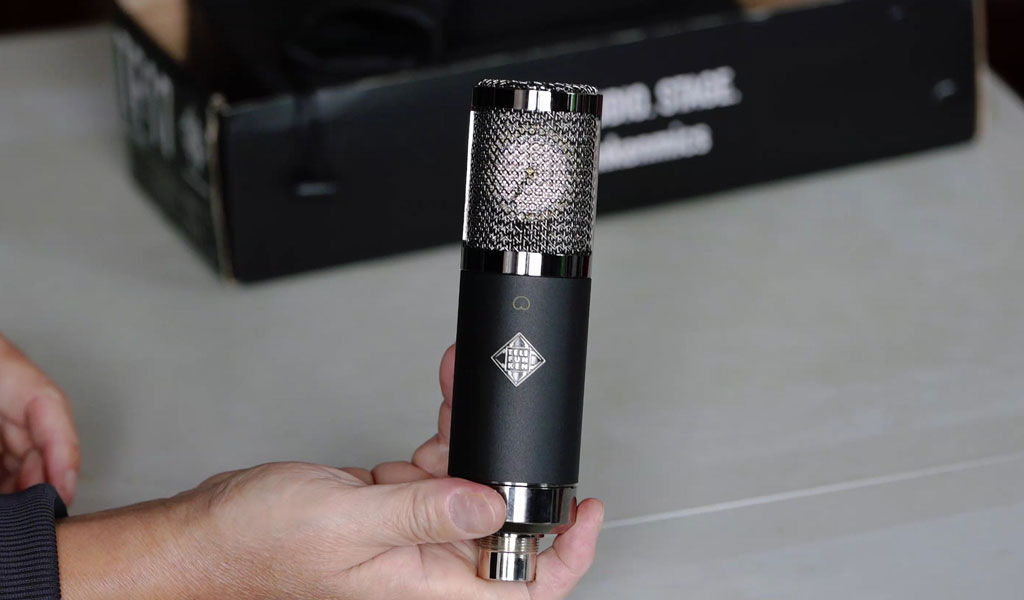
Metal etching is a critical process in the fabrication of microphone diaphragms, which are essential components in converting acoustic energy into electrical signals. This technique involves the selective removal of material from a metal substrate to create precise, thin, and often intricate structures that serve as the vibrating membrane in microphones. The diaphragm’s properties—such as thickness, uniformity, and mechanical compliance—directly influence a microphone’s sensitivity, frequency response, and overall performance. Metal etching, as applied to microphone diaphragms, encompasses a range of methods, including chemical etching, electrochemical etching, and plasma-based techniques, each offering distinct advantages and challenges.
This article explores the principles, processes, applications, and advancements in metal etching for microphone diaphragms, with an emphasis on its role in modern audio technology, particularly in microelectromechanical systems (MEMS) microphones.
Historical Context of Microphone Diaphragms
The development of microphone technology dates back to the 19th century, with early devices relying on rudimentary diaphragms to capture sound. Alexander Graham Bell’s liquid transmitter, patented in 1876, used a diaphragm attached to a conductive rod in an acidic solution to modulate electrical resistance in response to sound waves. This marked an early milestone in diaphragm-based transducers. Subsequent innovations, such as the carbon microphone and the dynamic microphone, introduced metal diaphragms made from materials like aluminum or steel, necessitating techniques to shape and thin these metals accurately.
By the mid-20th century, the advent of condenser microphones highlighted the need for extremely thin and lightweight diaphragms to achieve high sensitivity. Traditional mechanical methods, such as stamping or milling, were limited in precision and often introduced stresses or distortions into the metal. This spurred the adoption of etching techniques, borrowed from metallurgy and later semiconductor manufacturing, to produce diaphragms with the required finesse. The transition to MEMS microphones in the late 20th century further accelerated the use of metal etching, as these devices demanded micron-scale precision and compatibility with silicon-based fabrication processes.
Principles of Metal Etching
Metal etching is a subtractive manufacturing process that removes material from a metal surface through chemical, electrochemical, or physical means. The process typically involves masking areas of the metal to protect them from the etchant, while exposed regions are selectively dissolved or eroded. For microphone diaphragms, etching must achieve a balance between material removal and preservation of mechanical integrity, as the diaphragm must remain thin yet robust enough to withstand acoustic pressure without excessive deformation.
Chemical Etching
Chemical etching, also known as wet etching, uses liquid etchants—often acids or bases—to dissolve metal. For microphone diaphragms, common etchants include hydrochloric acid (HCl), nitric acid (HNO₃), or ferric chloride (FeCl₃), depending on the metal substrate (e.g., aluminum, copper, or stainless steel). The process begins with the application of a photoresist mask, patterned via photolithography, to define the diaphragm’s shape. The metal is then immersed in the etchant, which reacts with the exposed surface, removing material isotropically (equally in all directions).
This isotropy can be a limitation, as it may lead to undercutting beneath the mask, affecting dimensional accuracy. However, chemical etching is cost-effective, scalable, and suitable for producing diaphragms with thicknesses ranging from 10 to 50 micrometers. Its simplicity made it a staple in early microphone manufacturing, though modern applications often require more anisotropic (directional) methods.
Electrochemical Etching
Electrochemical etching enhances control over material removal by applying an electric current in an electrolyte solution. The metal workpiece acts as the anode, while a cathode completes the circuit. As current flows, metal ions are oxidized and dissolve into the electrolyte, allowing precise thinning of the diaphragm. This method is particularly effective for metals like titanium or nickel, which are resistant to purely chemical etchants.
For microphone diaphragms, electrochemical etching offers advantages in uniformity and surface finish, critical for consistent acoustic performance. By adjusting voltage, current density, and electrolyte composition (e.g., sulfuric acid or sodium chloride solutions), manufacturers can tailor the etch rate and minimize defects such as pitting or roughness.
Plasma Etching
Plasma etching, a dry etching technique, uses ionized gases (plasmas) to remove material through physical bombardment or chemical reaction. Common gases include fluorine-based compounds (e.g., SF₆ or CF₄) for silicon substrates or chlorine-based gases (e.g., Cl₂ or BCl₃) for metals like aluminum. In a plasma reactor, radio frequency (RF) energy ionizes the gas, creating reactive species that etch the exposed metal surface.
This method excels in anisotropy, enabling vertical sidewalls and precise feature definition—key for MEMS microphone diaphragms, which often integrate metal layers with silicon structures. Reactive ion etching (RIE), a variant of plasma etching, combines chemical and physical mechanisms, offering high selectivity (the ratio of metal etch rate to mask etch rate) and resolution down to nanometer scales.
Materials for Microphone Diaphragms
The choice of metal for a microphone diaphragm influences both the etching process and the device’s acoustic properties. Common materials include:
- Aluminum: Lightweight and corrosion-resistant, aluminum is widely used in dynamic and condenser microphones. It etches readily with chlorine-based plasmas or acidic solutions, achieving thicknesses as low as 5 micrometers.
- Stainless Steel: Valued for its durability and stiffness, stainless steel suits applications requiring robust diaphragms. Ferric chloride or electrochemical etching is typically employed, though the process is slower due to the alloy’s resistance.
- Nickel: Often used in MEMS microphones, nickel offers excellent mechanical properties and compatibility with electroforming and etching. It responds well to both wet and dry etching methods.
- Titanium: With high strength-to-weight ratio and biocompatibility, titanium is emerging in specialized microphones (e.g., medical implants). Electrochemical etching is preferred due to its chemical inertness.
Each material presents unique etching challenges, such as etch rate variability or mask adhesion, necessitating tailored process parameters.
Fabrication Process of Etched Metal Diaphragms
The fabrication of a metal diaphragm via etching involves several steps, adapted to the microphone type (e.g., condenser, dynamic, or MEMS). Below is a generalized process, with variations noted:
- Substrate Preparation: A metal foil or deposited film (e.g., aluminum on a silicon wafer) is cleaned to remove contaminants, ensuring uniform etching. For MEMS, the metal is often sputtered onto a sacrificial layer.
- Masking: A photoresist is applied and patterned using photolithography. The mask defines the diaphragm’s geometry, including its diameter (typically 0.5–2 mm for MEMS) and any perforations for acoustic tuning.
- Etching: The exposed metal is etched using the chosen method—chemical, electrochemical, or plasma. Process parameters (e.g., etchant concentration, plasma power) are optimized to achieve the target thickness (e.g., 1–20 micrometers).
- Mask Removal: The photoresist is stripped using solvents or plasma ashing, revealing the etched diaphragm.
- Post-Processing: The diaphragm may undergo annealing to relieve residual stresses or coating (e.g., gold for conductivity) to enhance performance.
For MEMS microphones, additional steps like sacrificial layer removal (via wet or dry etching) release the diaphragm, suspending it over an air gap.
Applications in Microphone Technology
Etched metal diaphragms are integral to various microphone designs, each leveraging the precision of etching differently:
Condenser Microphones
In condenser microphones, the diaphragm forms one plate of a capacitor, with a fixed backplate as the other. Sound waves vibrate the diaphragm, altering the capacitance and generating an electrical signal. Etching ensures the diaphragm is thin (e.g., 2–10 micrometers) and uniform, maximizing sensitivity (up to 50 mV/Pa) and frequency response (20 Hz–20 kHz).
Dynamic Microphones
Dynamic microphones use a diaphragm attached to a coil in a magnetic field. Etching thins the metal (e.g., aluminum or copper) to reduce mass, improving transient response while maintaining durability for high sound pressure levels (e.g., 140 dB SPL).
MEMS Microphones
MEMS microphones, prevalent in smartphones and wearables, integrate etched metal diaphragms with silicon backplates. Plasma etching enables submicron precision, yielding diaphragms as thin as 1 micrometer with high signal-to-noise ratios (SNR > 60 dB). The compact size (e.g., 1 mm²) and batch fabrication compatibility make them cost-effective.
Advancements in Metal Etching Techniques
Recent innovations have enhanced metal etching for microphone diaphragms, addressing limitations in precision, scalability, and material compatibility:
Deep Reactive Ion Etching (DRIE)
DRIE, an advanced plasma etching technique, alternates etching and passivation cycles (the Bosch process) to achieve high-aspect-ratio features. While primarily used for silicon, adaptations for metals like aluminum and nickel have improved diaphragm uniformity and reduced sidewall roughness, critical for MEMS applications.
Metal-Assisted Chemical Etching (MACE)
MACE employs a metal catalyst (e.g., gold or silver nanoparticles) to enhance etching selectivity on semiconductor-metal hybrids. For diaphragms with metal-silicon interfaces, MACE offers nanoscale control, enabling novel designs like corrugated or perforated diaphragms for enhanced compliance.
Laser-Assisted Etching
Combining laser ablation with chemical etching, this hybrid method allows rapid prototyping of diaphragms. It’s particularly useful for titanium or stainless steel, where traditional etching is slow, though it may introduce thermal stress.
Comparative Analysis of Etching Methods
To illustrate the trade-offs in metal etching techniques, the following tables compare their key parameters for microphone diaphragm fabrication:
Technique | Etch Rate (μm/min) | Anisotropy | Selectivity | Cost | Typical Materials | Advantages | Disadvantages |
---|---|---|---|---|---|---|---|
Chemical Etching | 1–10 | Low (Isotropic) | Moderate (5:1) | Low | Al, Cu, Stainless Steel | Simple, scalable | Undercutting, poor precision |
Electrochemical Etching | 0.5–5 | Moderate | High (10:1) | Moderate | Ni, Ti, Al | Uniformity, good surface finish | Slower, requires conductive setup |
Plasma Etching (RIE) | 0.1–1 | High | High (20:1) | High | Al, Ni, Si-metal hybrids | Precision, anisotropy | Expensive equipment, slower rates |
DRIE | 1–5 | Very High | Very High (50:1) | Very High | Al, Ni, Si | Deep features, high resolution | Complex, costly |
MACE | 0.1–2 | High | High (30:1) | Moderate | Metal-Si composites | Nanoscale control, versatility | Limited to specific materials |
Material | Etching Method | Thickness (μm) | Sensitivity (mV/Pa) | Frequency Range (Hz) | SNR (dB) | Applications |
---|---|---|---|---|---|---|
Aluminum | Chemical Etching | 10–50 | 20–30 | 50–15,000 | 50–55 | Dynamic, Condenser |
Stainless Steel | Electrochemical | 20–100 | 10–20 | 20–10,000 | 45–50 | Rugged Dynamic |
Nickel | Plasma Etching | 1–10 | 40–50 | 20–20,000 | 60–65 | MEMS, Condenser |
Titanium | Laser-Assisted | 5–20 | 30–40 | 100–18,000 | 55–60 | Specialty (e.g., Medical) |
Challenges and Limitations
Despite its advantages, metal etching for microphone diaphragms faces several challenges:
- Residual Stress: Etching can introduce stresses that warp the diaphragm, affecting resonance frequency and sensitivity. Annealing or corrugated designs mitigate this but add complexity.
- Uniformity: Variations in etch rate across a wafer (e.g., ±10%) can lead to inconsistent diaphragm thickness, degrading performance in batch-processed MEMS devices.
- Material Compatibility: Some metals (e.g., titanium) resist etching, requiring specialized processes that increase cost and time.
- Environmental Impact: Chemical etching generates toxic waste, necessitating careful disposal, while plasma etching requires energy-intensive equipment.
Future Directions
The future of metal etching for microphone diaphragms lies in integrating emerging technologies:
- Nanostructured Diaphragms: Techniques like MACE could enable nanoporous or textured diaphragms, enhancing sensitivity and bandwidth.
- Sustainable Processes: Green etchants (e.g., citric acid-based solutions) and low-power plasma systems aim to reduce environmental impact.
- Hybrid Fabrication: Combining etching with additive manufacturing (e.g., 3D printing metal precursors) could streamline production and enable complex geometries.
As demand grows for compact, high-performance microphones in IoT devices, wearables, and medical diagnostics, metal etching will remain a cornerstone of diaphragm innovation.