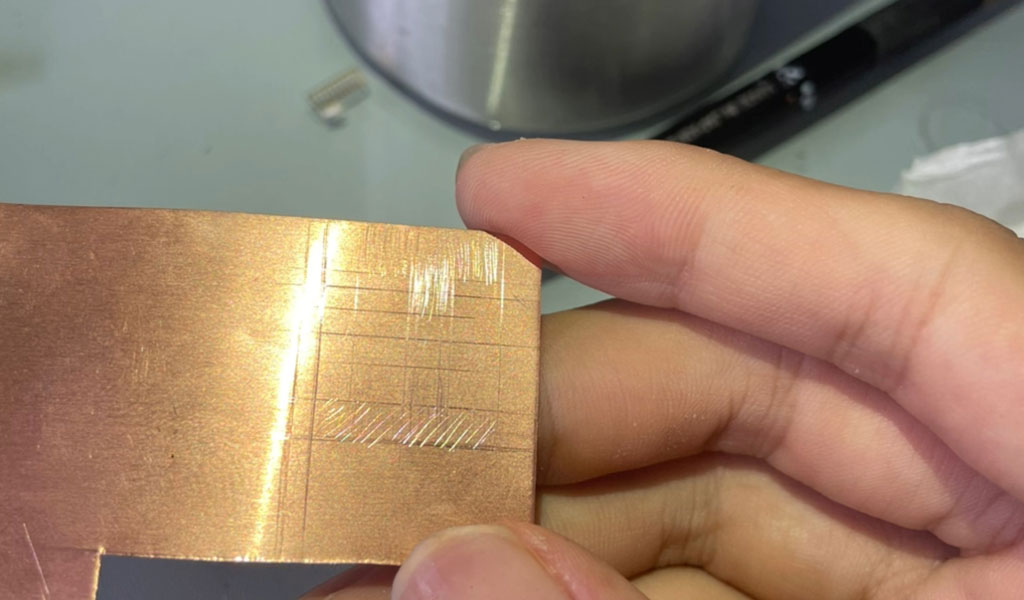
Metal etching is a widely utilized technique across various industries, from manufacturing and aerospace to art and jewelry, where precise patterns, designs, or functional features are created on metal surfaces.
The question of whether metal etching is permanent is central to understanding its applications, limitations, and long-term implications. This article provides an in-depth exploration of metal etching, its permanence, the underlying science, and its practical considerations, drawing on a multidisciplinary perspective to address the topic comprehensively.
Metal etching is a subtractive manufacturing process that involves selectively removing material from a metal surface to create patterns, designs, or functional features. The process typically employs chemical, electrochemical, or mechanical methods to achieve the desired effect. Etching has been used for centuries, evolving from artisanal techniques in medieval armories to modern industrial applications in microelectronics and aerospace engineering.
The permanence of metal etching refers to the durability and longevity of the etched features under various environmental conditions, mechanical stresses, and chemical exposures. Unlike surface coatings or temporary markings, etching physically alters the metal’s structure, suggesting a high degree of permanence. However, the extent to which these alterations withstand time, wear, and external factors depends on multiple variables, including the etching method, metal type, and application context.
This article examines the permanence of metal etching by exploring its scientific principles, methodologies, material interactions, environmental impacts, and practical applications. Detailed comparisons are provided through tables to elucidate key differences across techniques and materials.
Scientific Principles of Metal Etching
Chemical Etching
Chemical etching, also known as wet etching, involves the use of corrosive chemicals to dissolve specific areas of a metal surface. A resist or mask is applied to protect designated areas, while the exposed metal reacts with the etchant, resulting in material removal. Common etchants include acids (e.g., hydrochloric acid, nitric acid) and bases, selected based on the metal’s chemical properties.
The chemical reaction during etching can be represented as a redox process. For example, in etching copper with ferric chloride (FeCl₃), the reaction is:
[ \text{Cu} + 2\text{FeCl}_3 \rightarrow \text{CuCl}_2 + 2\text{FeCl}_2 ]
This reaction permanently removes copper atoms from the surface, creating recessed features. The depth and precision of the etch depend on factors such as etchant concentration, temperature, and exposure time.
Electrochemical Etching
Electrochemical etching, or electropolishing, uses an electric current to drive material removal. The metal workpiece acts as the anode in an electrolyte solution, and the application of voltage causes metal ions to dissolve into the electrolyte. This method is highly controllable and is often used for precision applications, such as in medical device manufacturing.
The permanence of electrochemical etching stems from the physical removal of metal, similar to chemical etching. However, the process can also smooth the surface, reducing microscopic irregularities that might affect durability.
Laser Etching
Laser etching employs focused laser beams to vaporize or ablate metal, creating precise patterns. The laser’s energy heats the metal to its vaporization point, removing material in a controlled manner. Laser etching is non-contact, minimizing mechanical stress on the workpiece.
The permanence of laser-etched features depends on the depth of material removal and the metal’s resistance to environmental factors. For instance, shallow laser etchings may be less durable under abrasive conditions compared to deeper chemical etches.
Mechanical Etching
Mechanical etching, such as engraving or abrasive blasting, physically removes material using tools or high-pressure abrasives. While effective for creating deep, durable patterns, mechanical etching is less precise than chemical or laser methods and may introduce surface stresses that affect long-term stability.
Table 1: Comparison of Metal Etching Methods
Method | Mechanism | Precision | Depth Control | Permanence | Common Applications |
---|---|---|---|---|---|
Chemical Etching | Corrosive chemical reaction | High | Moderate | High | Circuit boards, decorative art |
Electrochemical Etching | Electric current-driven dissolution | Very High | High | High | Medical devices, aerospace components |
Laser Etching | Laser ablation/vaporization | Very High | High | Moderate-High | Serial numbers, microelectronics |
Mechanical Etching | Physical material removal | Low-Moderate | Low-Moderate | High | Engraving, industrial part marking |
Factors Influencing the Permanence of Metal Etching
The permanence of etched features is determined by a combination of material properties, etching techniques, and environmental conditions. Below, we explore these factors in detail.
Metal Properties
The type of metal significantly affects the durability of etched features. Metals with high corrosion resistance, such as stainless steel or titanium, are more likely to retain etched patterns over time compared to reactive metals like aluminum or copper.
Hardness and Mechanical Strength
Harder metals, such as tungsten or hardened steel, resist wear and abrasion, preserving etched features under mechanical stress. The Mohs scale or Vickers hardness test can quantify a metal’s resistance to scratching or deformation.
Corrosion Resistance
Corrosion can degrade etched features, particularly in reactive environments. For example, etched aluminum may corrode in saline conditions, reducing the visibility or integrity of the pattern. Corrosion-resistant alloys, such as those containing chromium or nickel, are preferred for applications requiring long-term durability.
Table 2: Metal Properties and Etching Permanence
Metal | Hardness (Vickers, HV) | Corrosion Resistance | Common Etching Method | Permanence Rating |
---|---|---|---|---|
Stainless Steel | 200–600 | High | Chemical, Laser | Very High |
Titanium | 830–3420 | Very High | Electrochemical, Laser | Very High |
Aluminum | 15–120 | Moderate | Chemical, Laser | Moderate |
Copper | 35–130 | Low | Chemical | Low-Moderate |
Tungsten | 3000–4000 | High | Laser, Mechanical | Very High |
Etching Depth
The depth of the etch is a critical factor in determining permanence. Deeper etches are more resistant to wear, abrasion, and surface treatments like polishing. For example, a laser etch with a depth of 0.01 mm may be worn away by sanding, whereas a chemical etch of 0.5 mm is more likely to endure.
Environmental Exposure
Etched metals are often exposed to harsh conditions, such as moisture, temperature fluctuations, or chemical agents. These factors can degrade the etched features over time.
Moisture and Corrosion
In humid or saline environments, etched features on non-corrosion-resistant metals may degrade due to rust or oxidation. Protective coatings, such as passivation layers or polymer seals, can enhance permanence.
Temperature Extremes
High temperatures can cause thermal expansion or phase changes in metals, potentially distorting etched patterns. Conversely, low temperatures may embrittle certain metals, increasing susceptibility to cracking.
Abrasion and Wear
Mechanical wear from friction or contact can erode shallow etches. Applications like industrial tooling, where etched surfaces are subject to constant abrasion, require deep etches or wear-resistant metals.
Post-Etching Treatments
Post-etching treatments, such as passivation, anodizing, or coating, can enhance the permanence of etched features. For instance, anodizing aluminum creates a protective oxide layer that improves corrosion resistance, preserving the etch in harsh environments.
Applications of Metal Etching and Permanence Considerations
Metal etching is employed in diverse fields, each with unique requirements for permanence. Below, we discuss key applications and their implications for etched feature durability.
Industrial Manufacturing
In manufacturing, etching is used to create precision components, such as gears, molds, and circuit boards. The permanence of these etches is critical, as components are often subjected to mechanical stress, heat, and chemical exposure.
For example, etched stainless steel molds used in injection molding must withstand repeated cycles of high pressure and temperature. Deep chemical or electrochemical etches are preferred to ensure longevity.
Aerospace and Defense
Aerospace components, such as turbine blades or structural panels, require etched markings for identification or functional purposes. These etches must remain legible and intact under extreme conditions, including high temperatures, vibration, and exposure to jet fuel.
Titanium and nickel-based alloys are commonly used in aerospace due to their corrosion resistance and mechanical strength. Laser or electrochemical etching is often employed to achieve precise, durable patterns.
Electronics and Microfabrication
In electronics, etching is critical for producing microchips, printed circuit boards (PCBs), and sensors. Chemical etching is widely used to create intricate conductive pathways on copper-clad substrates. The permanence of these etches is essential for ensuring reliable electrical performance over the device’s lifespan.
Art and Jewelry
In artistic applications, metal etching is used to create decorative patterns, engravings, or textures. The permanence of these etches is less critical than in industrial applications, as aesthetic features are often protected by coatings or displayed in controlled environments. However, outdoor sculptures or jewelry exposed to wear may require durable etches to maintain their appearance.
Table 3: Applications and Permanence Requirements
Application | Common Metals | Etching Method | Permanence Requirement | Environmental Challenges |
---|---|---|---|---|
Industrial Manufacturing | Stainless Steel, Tool Steel | Chemical, Electrochemical | Very High | Abrasion, Heat, Chemical Exposure |
Aerospace | Titanium, Nickel Alloys | Laser, Electrochemical | Very High | Temperature, Vibration, Corrosion |
Electronics | Copper, Silicon | Chemical | High | Moisture, Thermal Cycling |
Art and Jewelry | Silver, Brass, Copper | Chemical, Mechanical | Moderate | Wear, Oxidation |
Mechanisms of Etch Degradation
Despite the inherent permanence of metal etching, certain mechanisms can degrade etched features over time. Understanding these mechanisms is essential for designing durable etched components.
Corrosion-Induced Degradation
Corrosion is a primary cause of etch degradation, particularly in reactive metals. For example, etched iron surfaces exposed to moisture may develop rust, obscuring the etched pattern. Corrosion can be mitigated through material selection, protective coatings, or environmental controls.
Mechanical Wear
Abrasion or friction can erode etched features, especially shallow etches. In applications like tooling or machinery, where surfaces are subject to constant contact, deep etches or wear-resistant metals are necessary to maintain permanence.
Thermal Degradation
High temperatures can cause phase changes, recrystallization, or thermal expansion in metals, potentially distorting etched patterns. For instance, etched aluminum components in high-temperature environments may experience surface recrystallization, reducing etch clarity.
Chemical Exposure
Exposure to aggressive chemicals, such as acids or solvents, can further etch or dissolve the metal, altering the original pattern. In chemical processing plants, etched components must be made from chemically resistant alloys or protected with coatings.
Strategies to Enhance Etch Permanence
To maximize the permanence of etched features, several strategies can be employed, ranging from material selection to post-processing techniques.
Material Selection
Choosing metals with high corrosion resistance, hardness, and thermal stability is critical for ensuring etch durability. For example, titanium is an excellent choice for applications requiring resistance to both corrosion and mechanical wear.
Etching Technique Optimization
Selecting the appropriate etching method based on the application can enhance permanence. For instance, deep chemical etching is ideal for industrial components, while laser etching is better suited for precise, shallow markings.
Protective Coatings
Applying protective coatings, such as epoxy, polyurethane, or ceramic layers, can shield etched surfaces from environmental degradation. Anodizing is particularly effective for aluminum, creating a durable oxide layer that enhances corrosion resistance.
Environmental Controls
Controlling the operating environment can extend etch longevity. For example, storing etched components in low-humidity conditions or using corrosion inhibitors can prevent degradation.
Table 4: Strategies for Enhancing Etch Permanence
Strategy | Description | Applicable Metals | Effectiveness | Cost |
---|---|---|---|---|
Material Selection | Use corrosion-resistant, hard metals | Titanium, Stainless Steel | Very High | High |
Etching Technique | Optimize method for depth and precision | All | High | Moderate |
Protective Coatings | Apply polymer, ceramic, or oxide layers | Aluminum, Steel | High | Moderate-High |
Environmental Controls | Control humidity, temperature, exposure | All | Moderate | Low-Moderate |
Case Studies in Metal Etching Permanence
Case Study 1: Etched Stainless Steel in Marine Environments
Stainless steel panels etched with identification markings were deployed on a marine vessel exposed to saltwater and humidity. Chemical etching was used to create 0.3 mm deep patterns. After five years, the etches remained legible, with minimal corrosion due to the steel’s high chromium content. This case highlights the importance of material selection in corrosive environments.
Case Study 2: Laser-Etched Aluminum in Aerospace
Aluminum components in an aircraft were laser-etched with serial numbers. After 10 years of service, including exposure to thermal cycling and vibration, the shallow etches (0.05 mm) showed signs of wear, with some numbers becoming faint. This case underscores the need for deeper etches in high-wear applications.
Case Study 3: Electrochemical Etching in Medical Devices
Titanium medical implants were electrochemically etched with microscale patterns to promote bone integration. The etches remained intact after 15 years in the human body, demonstrating the durability of electrochemical etching on corrosion-resistant metals.
Future Directions in Metal Etching
Advancements in etching technologies are poised to enhance the permanence and versatility of etched features. Emerging trends include:
Nanotechnology in Etching
Nanoscale etching techniques, such as focused ion beam (FIB) etching, enable the creation of ultra-precise patterns with applications in quantum computing and nanomedicine. The permanence of these etches is under investigation, as nanoscale features are more susceptible to environmental perturbations.
Hybrid Etching Methods
Combining chemical, laser, and electrochemical methods can achieve synergistic effects, such as enhanced precision and durability. For example, a hybrid process might use laser etching to create initial patterns, followed by chemical etching to deepen the features.
Sustainable Etching Practices
The environmental impact of etching, particularly chemical etching, has prompted research into green etchants and recycling systems. Biodegradable etchants and closed-loop electrolyte systems could reduce the ecological footprint while maintaining etch permanence.
Conclusion
The permanence of metal etching is a complex interplay of material properties, etching techniques, environmental conditions, and post-processing strategies. Chemical, electrochemical, laser, and mechanical etching each offer unique advantages, with permanence determined by factors such as etch depth, metal hardness, and corrosion resistance. Applications in manufacturing, aerospace, electronics, and art highlight the diverse requirements for etched feature durability.
Through careful material selection, optimized etching methods, and protective measures, the permanence of etched features can be maximized, ensuring their functionality and aesthetic value over extended periods. As etching technologies evolve, innovations in nanotechnology, hybrid methods, and sustainable practices promise to further enhance the durability and applicability of metal etching.
This comprehensive analysis underscores that, while metal etching is inherently permanent due to its subtractive nature, its long-term durability depends on a nuanced understanding of scientific principles and practical considerations. By addressing these factors, industries and artisans alike can leverage etching to create lasting, high-quality features on metal surfaces.