Homepage » Metal Etching »
Batteries Etching – Metal Etching for Batteries and Supercapacitors Industry
Metal etching, a process primarily used in the manufacturing of precision metal parts, has evolved into an indispensable technique in industries ranging from electronics to automotive. In the realm of energy storage, particularly in the batteries and supercapacitors industry, metal etching plays a critical role in the production of high-performance components that ensure enhanced efficiency, durability, and overall performance. In the context of energy storage devices like batteries and supercapacitors, metal etching is used to manufacture components such as electrodes, current collectors, and other intricate parts that require high precision.
Our Batteries Etching Service
If you need Batteries parts etched we are one of the most capable and affordable sources specializing in manufacturing custom etched parts on advanced photo etching machines with cnc precision. Through our Photo Chemical Etching process, the smallest and most complex designs are made possible such as electrical spring contacts, contact membranes, busbars, antennae and micro antennae, spring fingered contacts, heating elements and battery terminal as well as many other bespoke components to your own designs.
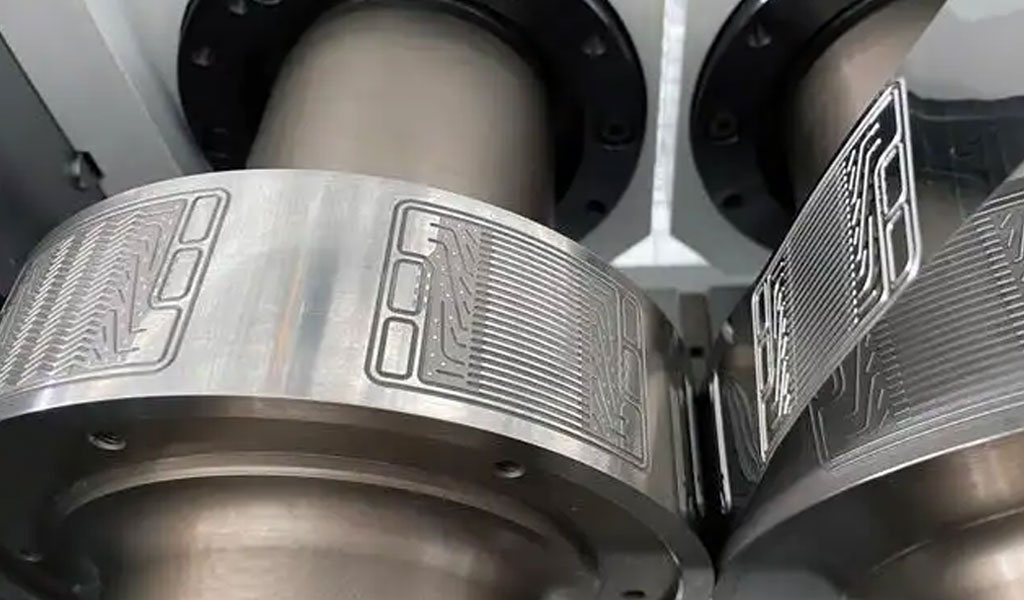
We can machine to print and accept the most common file formats including: .dwg .dxf .iges .step .sat as well as .pdf files. If you don’t see your file format here let us know. Please send us files to: [email protected] We can accept both small and large run jobs of custom Batteries etching parts.
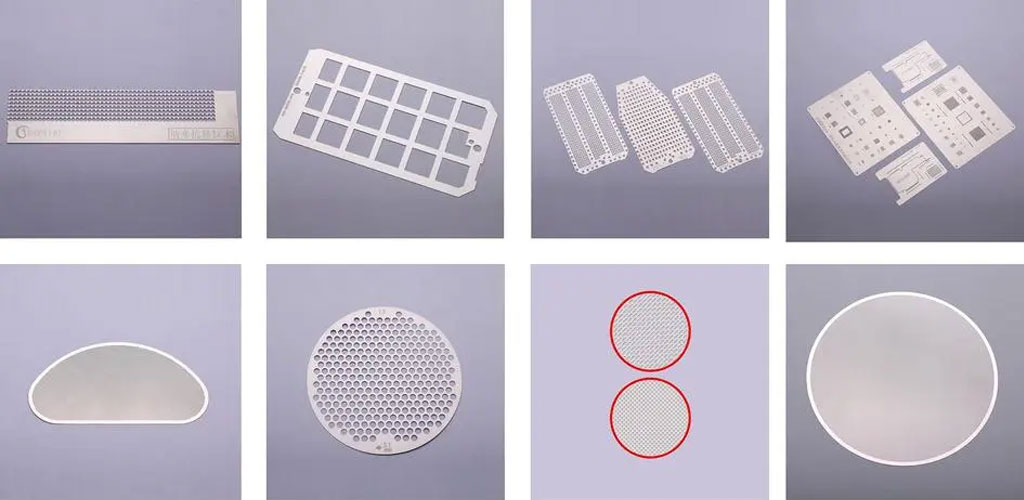
Our Etching Capabilities
- Etching of many grades of metal and more
- Combining Stamping, Laser Cutting,CNC machining and photochemical etching on sheets up to 2mm thick
- Etching of up to 0.025″ thick sheets as large as 22×12 inches
- Tolerances of ±.0005″ in many applications
How To Etch Batteries Parts
Automated-Coating Automatic-Baking-Line Automatic-Shearing Coating-For-Etching-Parts Deinking Etching Exposure Inspection-For-Etching
Materials Used in Metal Etching for Energy Storage Devices
The materials chosen for etching in the energy storage industry must possess specific properties to meet the demanding requirements of battery and supercapacitor performance. Some of the most commonly used metals in etching processes for these applications include:
1. Copper
Copper is widely used in the manufacture of current collectors for lithium-ion batteries due to its excellent electrical conductivity, thermal conductivity, and corrosion resistance. Etching copper allows for the creation of highly precise patterns that improve the efficiency of current transfer within the battery. Additionally, copper’s malleability and ductility make it easy to process during the etching process.
2. Aluminum
Aluminum is another common material used for current collectors, particularly in the cathodes of lithium-ion batteries. Aluminum is lightweight, has good electrical conductivity, and is resistant to corrosion, making it ideal for use in energy storage applications. Etching aluminum allows for the creation of fine patterns that enhance the conductivity and mechanical strength of the current collector while reducing weight.
3. Stainless Steel
Stainless steel, known for its durability and resistance to corrosion, is often used in components of supercapacitors and batteries that require structural integrity. Stainless steel’s resistance to oxidation is particularly important in energy storage devices, where exposure to high temperatures and chemical environments is common. Etching stainless steel helps to create intricate microstructures that improve the performance and longevity of the components.
4. Titanium
Titanium and its alloys are sometimes used in the construction of energy storage devices due to their strength, light weight, and excellent corrosion resistance. Titanium’s resistance to chemical attack, particularly in high-temperature or high-voltage environments, makes it a suitable choice for certain applications. Titanium etching can be used to create fine structures that improve the performance of titanium-based components.
5. Nickel
Nickel and nickel-based alloys are often used in the manufacture of electrodes and current collectors for supercapacitors and batteries, particularly in nickel-metal hydride (NiMH) and nickel-cobalt-manganese (NCM) batteries. Nickel’s excellent corrosion resistance and ability to withstand high currents make it an ideal material for energy storage applications. Etching nickel-based alloys allows for the creation of intricate patterns and structures that optimize performance.
Components That Are Produced By Etching Batteries Parts
The popularity of Batteries makes it a desirable metal for use in fabrication because it is easy to manufacture and has favorable properties for many industrial products.With the photo etching process, the metal is etched evenly without any structural deformations from the hard tooling used in stamping and punching.Since there isn’t a heat point of contact like laser cutting, the parts’ metal properties remain unchanged and free from thermal deformations.Get inspired by our custom etching part projects and contact us to Get Instant Quote for rapid prototype or Batteries etching parts start from 1pcs.
-
Precision Etched Titanium Alloy Odor Eliminator Perforated Plates
-
High-End Etched TC4 Titanium Alloy Filters
-
Precision Etching Titanium Alloy Hanging Fixture for Anodizing
-
Metal Chemical Etching Reciprocating Razor Blades
-
Titanium Alloy Etched Coffee Filter
-
Etching Bipolar Plates for Hydrogen Fuel Production
-
0.3MM Laser Etched Titanium Mesh
-
Precision Etching Printer Single Drum Scraper
Metal Etching Certification,Equipment List and Quality
We are committed to enlisting the full support of all employees to continuously improve our processes and enhance quality, thereby fulfilling our customer's needs with defect free products and services, on time and every time
- ISO 9001:2015 certified
- Compliance in DFARS materials sourcing requirements
- Strict compliance with PPAP and Process FMEA
- Fully compliant with the exacting requirements of our customers
- ITAR registered
- NIST cybersecurity standard compliant
- Proprietary Patented quality systems
- Skilled in KanBan and other customer driven quality and inventory management systems
Metal Etching Material
BE-CU is experienced in precision etching various metals, allowing customers the freedom to specify components in hundreds of different materials.
The Surface Treatment Of Metal Etching Parts
Do you want your etching parts to be more corrosion-resistant or get a specific look? Metal finishing service is a essential choice to achieve your design perfectly. BE-CU – metal-etch.com is an accomplished finished parts manufacturer, our workers and craftsman are capable to provide precision metal etching services and a wide range of finishing services including aluminum anodizing, painting, passivation, electroplating, powder coating, polishing, black oxide, conversion coating, abrasive blasting, etc. We offers several common surface finishes to help improve functionality and aesthetics.
- Anodizing (Anodized)
- Passivation
- Plating (Electroplating)
- Painting
- Black Oxide (Hot Blackening)
- Polishing
- Powder Coating
- Heat Treatment
- Satin Finish
- Abrasive blasting (Sandblasting)
- Conversion coating
- Tungsten carbide coating
After browsing a list of metal finishing services, select a process based on essential considerations, like production time, cost-effectiveness, part tolerance, durability and applications. High-tolerance metal etching parts are not recommended to apply secondary metal surface finish, because the treatment may change the sizes of the finished part through removing or adding a small amount of materials.
Other requirements or custom designs, welcome to contact us for a free quote fast!