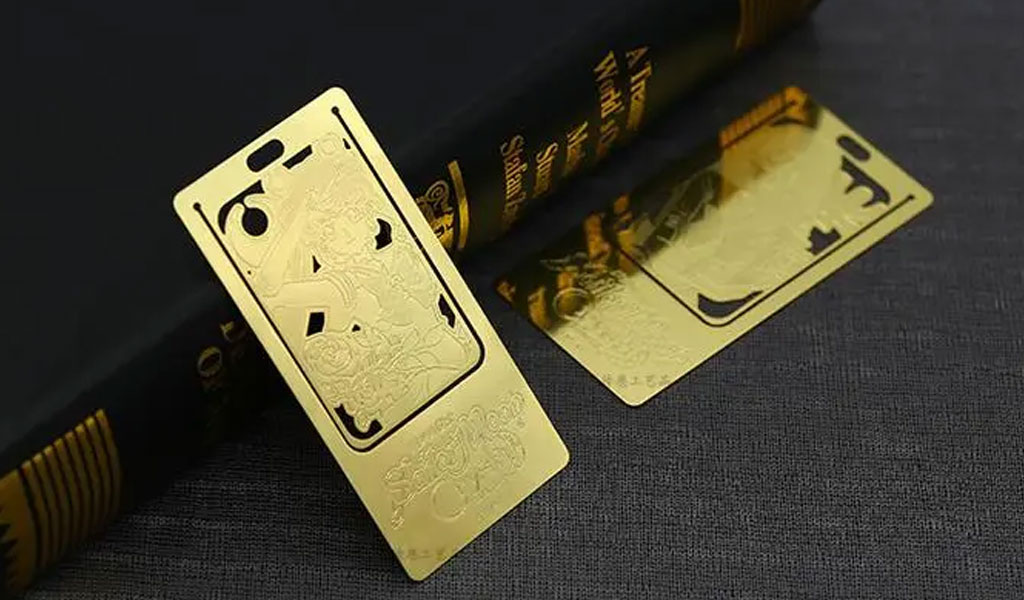
The Warhammer 40,000 (40k) universe, created by Games Workshop, is a rich and expansive science fiction setting that has captivated millions of hobbyists and gamers around the globe. One of the most fascinating aspects of this universe is the meticulous attention to detail that enthusiasts bring to their models and miniatures.
Among the myriad techniques employed to enhance the visual appeal of these models, the use of 40k etched brass stands out as a particularly intricate and rewarding method. This article delves into the world of 40k etched brass, exploring its history, application techniques, tools, and the unique flair it brings to the miniatures.
Chapter 1: The Origins and Evolution of Etched Brass in Model Making
1.1 Historical Background
Etched brass has been used in various forms of modeling for decades, long before the advent of the Warhammer 40,000 universe. The technique originated in the world of scale modeling, particularly in the creation of highly detailed military models, such as tanks, ships, and aircraft. The precision and fine details that etched brass could provide were unparalleled, making it a popular choice for modelers seeking to achieve historical accuracy and realism.
1.2 Introduction to Warhammer 40,000
The Warhammer 40,000 universe was introduced by Games Workshop in 1987. It quickly gained a massive following due to its unique blend of dystopian science fiction, grimdark aesthetic, and intricate lore. As the popularity of 40k grew, so did the demand for more detailed and visually stunning models. This demand led to the incorporation of etched brass into the hobby, allowing enthusiasts to add a new level of detail and authenticity to their miniatures.
1.3 Evolution of 40k Etched Brass
Over the years, the use of etched brass in 40k modeling has evolved significantly. Initially, hobbyists would adapt etched brass components from other modeling disciplines to suit their needs. However, as the 40k community grew, specialized etched brass kits were developed specifically for Warhammer 40,000 models. These kits include a wide range of components, from intricate insignias and iconography to detailed mechanical parts and armor enhancements, allowing for unprecedented customization and detailing possibilities.
Chapter 2: The Art and Science of Etching Brass
2.1 The Etching Process
Etching brass involves using chemicals to selectively remove parts of the metal, creating detailed patterns and designs. The process typically begins with a brass sheet coated in a photoresist material. A design is then transferred onto the sheet using ultraviolet light, which hardens the photoresist in the desired areas. The unexposed photoresist is washed away, exposing the brass underneath. Finally, the brass is submerged in an etching solution, usually ferric chloride, which dissolves the exposed areas, leaving behind the intricate design.
2.2 Tools and Materials
Creating etched brass components requires a variety of tools and materials, including:
- Brass sheets: Available in various thicknesses, typically between 0.1mm and 0.5mm.
- Photoresist film: A light-sensitive material used to transfer the design onto the brass sheet.
- Ultraviolet light source: Used to expose the photoresist film.
- Etching solution: Ferric chloride is commonly used for etching brass.
- Protective equipment: Gloves, goggles, and a well-ventilated workspace are essential for safety.
2.3 Designing for Etched Brass
Designing for etched brass requires a different approach compared to traditional model making. The designs need to account for the limitations of the etching process, such as the minimum line thickness and the potential for over-etching. Many hobbyists use graphic design software to create their patterns, allowing for precise control over the details. Additionally, understanding the mechanical properties of brass is crucial, as it can be quite fragile when etched too thinly.
Chapter 3: Techniques for Applying Etched Brass to 40k Models
3.1 Preparation and Planning
Before applying etched brass components to a 40k model, thorough preparation and planning are essential. This includes carefully studying the model and deciding where the etched brass components will be placed. It’s also important to clean the brass sheets and the model surfaces to ensure a strong bond.
3.2 Cutting and Shaping
Etched brass components are usually provided as flat sheets, so cutting and shaping them to fit the model is a critical step. Precision tools such as fine scissors, hobby knives, and small files are used to cut and shape the components. Care must be taken to avoid bending or damaging the delicate parts.
3.3 Attachment Methods
Several methods can be used to attach etched brass components to 40k models:
- Super glue: Cyanoacrylate glue provides a strong and quick bond but requires precision to avoid excess glue seeping out.
- Epoxy adhesive: Offers a very strong bond and is ideal for larger components but takes longer to set.
- Soldering: For metal models, soldering provides a robust and durable attachment but requires skill and the appropriate tools.
3.4 Blending and Finishing
Once the etched brass components are attached, blending and finishing are crucial to achieve a seamless look. This involves filling any gaps with putty or filler, sanding smooth any rough edges, and priming the model for painting. The goal is to integrate the etched brass components so that they appear as an intrinsic part of the model rather than an add-on.
Chapter 4: Enhancing 40k Models with Etched Brass
4.1 Adding Detail and Realism
One of the primary reasons hobbyists use etched brass is to add an unparalleled level of detail and realism to their 40k models. The fine lines and intricate designs that can be achieved with etched brass are impossible to replicate with plastic or resin. This includes detailed insignias, text, and mechanical parts that enhance the overall aesthetic and authenticity of the model.
4.2 Customization and Personalization
Etched brass allows hobbyists to customize and personalize their 40k models in unique ways. From adding chapter-specific insignias to creating custom armor plates and decorations, etched brass offers endless possibilities for making a model truly one-of-a-kind. This level of customization is particularly appealing in the 40k community, where individual expression and creativity are highly valued.
4.3 Structural Enhancements
In addition to aesthetic improvements, etched brass can also provide structural enhancements to 40k models. This includes reinforcing thin or delicate parts, adding functional elements such as hinges and grills, and creating more robust and durable components. These enhancements not only improve the appearance of the model but also increase its longevity and durability.
Chapter 5: Case Studies and Examples
5.1 Imperial Guard Tank Detailing
One of the most common applications of etched brass in 40k modeling is detailing Imperial Guard tanks. These large and heavily armored vehicles provide ample surface area for adding etched brass components. Common additions include detailed armor plates, insignias, and mechanical parts such as engine grills and exhaust vents. The result is a highly detailed and realistic tank that stands out on the battlefield.
5.2 Space Marine Armor Customization
Space Marines, with their iconic power armor, are another popular subject for etched brass customization. Hobbyists often use etched brass to add chapter-specific insignias, intricate armor decorations, and additional details such as rivets and bolts. This not only enhances the visual appeal of the models but also reinforces their identity within the 40k universe.
5.3 Chaos Daemons and Eldar Models
Etched brass is also used to enhance the more exotic and ornate models in the 40k universe, such as Chaos Daemons and Eldar. These models often feature intricate and organic designs that can be difficult to achieve with traditional modeling techniques. Etched brass allows hobbyists to add fine details and decorations that complement the unique aesthetics of these models, creating stunning and visually striking pieces.
Chapter 6: Advanced Techniques and Tips
6.1 Advanced Cutting and Shaping
For more complex and intricate etched brass components, advanced cutting and shaping techniques are required. This includes using fine saw blades, rotary tools, and custom jigs to achieve precise cuts and shapes. Additionally, techniques such as annealing (heating the brass to make it more malleable) can be used to create curved or bent components.
6.2 Painting and Weathering
Painting and weathering etched brass components require a different approach compared to plastic or resin parts. Priming is essential to ensure proper paint adhesion, and specialized metal primers are recommended. Weathering techniques such as dry brushing, washes, and chipping can be used to add realism and depth to the etched brass components, blending them seamlessly with the rest of the model.
6.3 Creating Custom Etched Brass Components
For hobbyists looking to take their skills to the next level, creating custom etched brass components is a rewarding challenge. This involves designing the components from scratch, creating the photoresist masks, and etching the brass sheets. While it requires a significant investment in time and equipment, the ability to create entirely custom components opens up a world of possibilities for truly unique and personalized 40k models.
Chapter 7: The Community and Future of 40k Etched Brass
7.1 The 40k Etched Brass Community
The use of etched brass in 40k modeling has fostered a vibrant and supportive community of hobbyists. Online forums, social media groups, and dedicated websites provide a platform for sharing tips, techniques, and inspiration. This sense of community not only helps hobbyists improve their skills but also fosters a collaborative and creative environment where new ideas and innovations can flourish.
7.2 Trends and Innovations
As the 40k etched brass community continues to grow, new trends and innovations are emerging. This includes the use of advanced technologies such as laser cutting and 3D printing to create even more intricate and detailed components. Additionally, collaborations between hobbyists and professional model makers are leading to the development of new products and techniques that push the boundaries of what is possible with etched brass.
7.3 The Future of 40k Etched Brass
The future of 40k etched brass is bright, with endless possibilities for innovation and creativity. As new technologies and techniques continue to emerge, the potential for even more detailed and realistic models is exciting. Additionally, the growing community of hobbyists ensures that the art of etched brass in 40k modeling will continue to evolve and thrive for years to come.
Conclusion
The world of 40k etched brass is a fascinating and intricate one, offering hobbyists the opportunity to enhance their models with unparalleled detail and realism. From its historical origins to the advanced techniques used today, etched brass has become an integral part of the Warhammer 40,000 modeling experience. Whether you’re a seasoned veteran or a newcomer to the hobby, the use of etched brass opens up a world of possibilities for creating truly stunning and unique models. As the community continues to grow and innovate, the future of 40k etched brass looks incredibly promising, promising even more exciting developments and creative opportunities in the years to come.