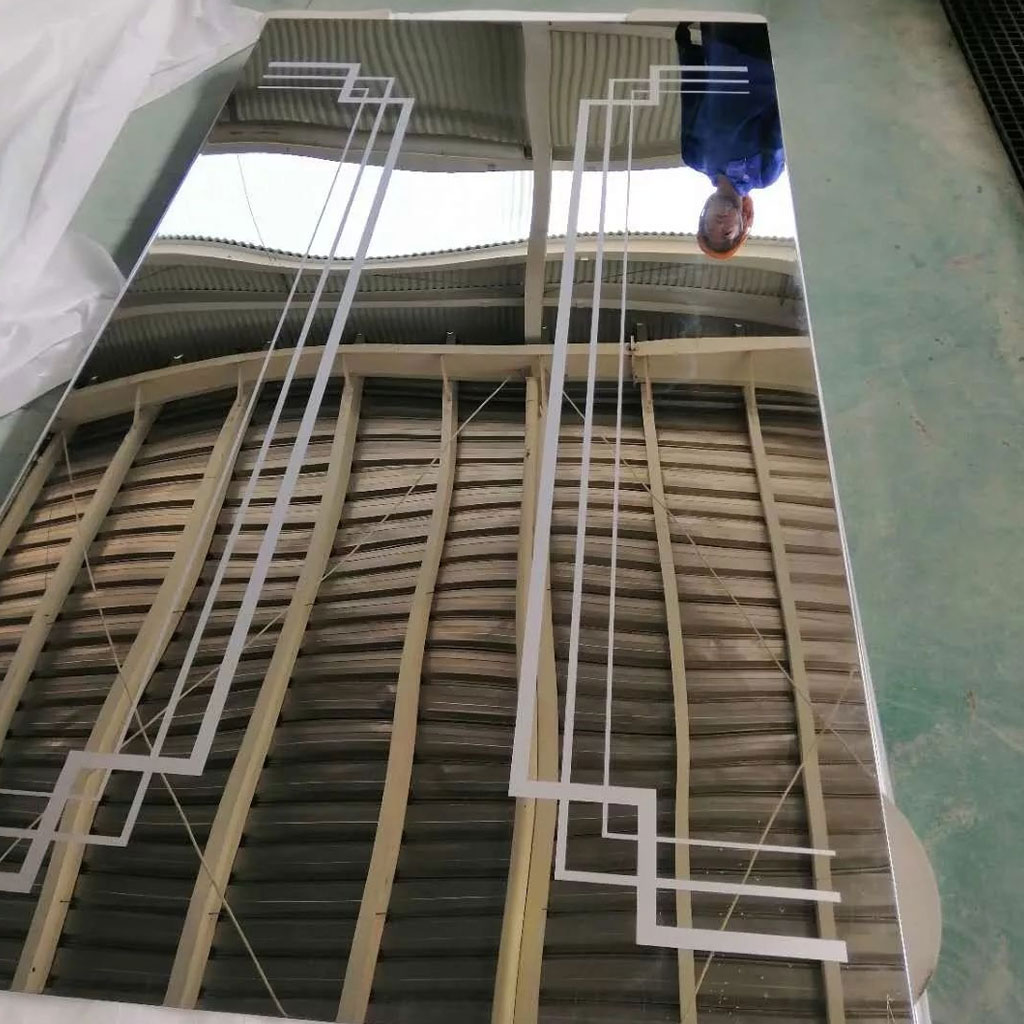
Stainless steel etched plates are a common material for elevator decoration, such as in hall doors, car doors, car walls, nameplate surfaces, etc. We often see them, but most people don’t know how they are processed. This article briefly introduces some Relevant knowledge, I hope it will give you a deeper understanding of this process.Usually referred to as etching, also known as photochemical etching (photochemical etching), it refers to removing the protective film of the area to be etched through exposure plate making and development, and contacting chemical solutions during etching to achieve the effect of dissolving corrosion and forming concave and convex or hollow molding effects.
The etched stainless steel plates used in elevators usually use screen printing, and can be customized with personalized patterns, text and LOGOs. They are often used on elevator hall doors and car walls, and are commonly used materials in elevator decoration. Usually 304 stainless steel is used as the base material, which can be used for etching mirror, hairline, and textured plates, supplemented by sandblasting, concave gold spraying, color plating, etc., as well as the combination of the above effects and processes to achieve rich and colorful expressions. .
Etched Stainless Steel Process Flow
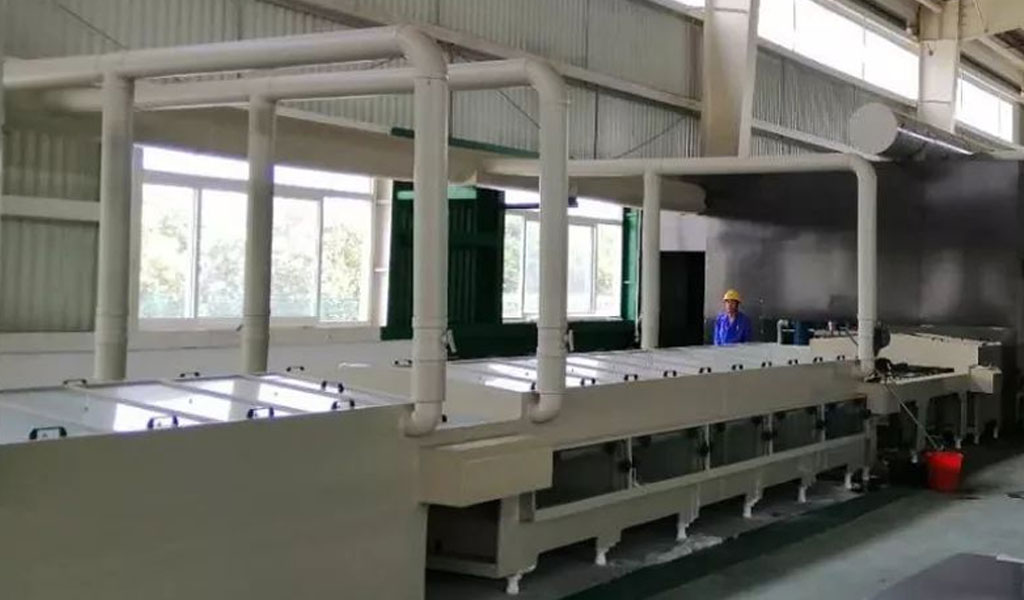
1.Exposure Method
The project prepares the material size according to the drawing – material preparation – material cleaning – drying → film or coating → drying → exposure → development → drying – etching → stripping → OK
2.Screen Printing Method
Cut the material → Clean the plate (stainless steel and other metal materials) → Screen printing → Etch → Remove the film → OK
The biggest advantage of stainless steel etched plates is that they are resistant to corrosion, pitting, rust or wear, so the structural components can permanently maintain design integrity.
From the splendid Jin Mao Tower in Shanghai and the majestic Petronas Twin Towers in Kuala Lumpur to the Disney Concert Hall in Los Angeles and the Waterloo Railway Station in London, which are all stainless steel shells; from the 150,000-square-meter roof and the 452-meter-high tower to the exquisite Decorative parts and small structural parts, the contribution of colored stainless steel etched plates to sustainable architecture fully proves this. It is the most sustainable building material and exudes a unique charm that ordinary materials do not have around the world. .
First, the design life of the most sustainable building should be at least 50 years. In most sustainable building designs, major building components such as structural frames, roofs, walls, and other large surfaces are required to outlast the structure, avoiding the use of coatings and treatments that generate emissions and increase the building’s environmental footprint. method. If the right stainless steel is selected and properly maintained, colored stainless steel may never need to be replaced during the life of the building, even if the building is hundreds of years old. At the same time, there is no need to coat stainless steel surfaces to prevent corrosion.
Secondly, the best materials may be naturally regenerated, or they must be recycled while maintaining the same quality.
Stainless steel etched plates have the highest material composition that can be utilized in many construction aspects. If it can be fully recycled when it reaches a certain service life, it can be recycled to produce stainless steel etched plates of the same quality.
Pay Attention To The Problem
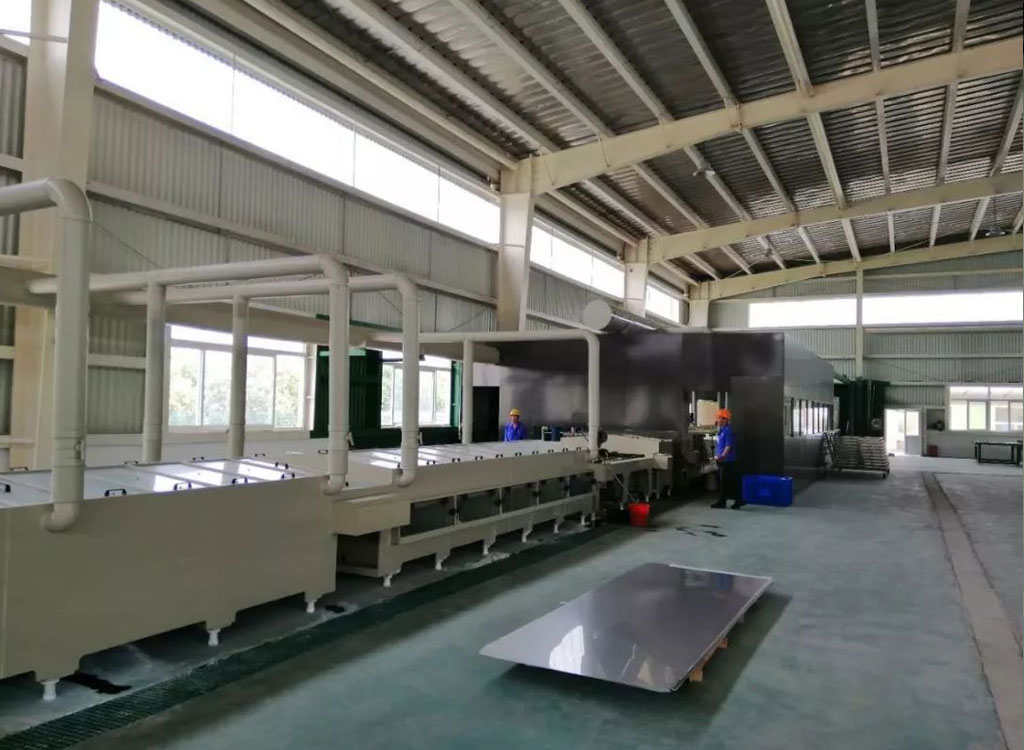
Reduce side etching and protruding edges and increase etching coefficient
Lateral erosion produces a bulging edge. Generally, the longer the printed board is in the etching solution (or using an old-fashioned left-right etching machine), the more serious the side etching will be. Undercutting seriously affects the accuracy of printed conductors, and severe undercut will make it impossible to produce fine conductors. When the side etching and protruding edges are reduced, the etching coefficient increases. A high etching coefficient indicates the ability to maintain thin wires, making the etched wires close to the original size. Whether the electroplating etching resist is tin-lead alloy, tin, tin-nickel alloy or nickel, excessive protrusion will cause a short circuit in the wire. Because the protruding edge breaks off easily, an electrical bridge is formed between the two points of the wire.
Improve etch rate consistency from board to board
In continuous board etching, the more consistent the etching rate is, the more uniformly etched boards can be obtained. To meet this requirement, it is necessary to ensure that the etching solution is always in the best etching state during the entire etching process. This requires choosing an etching liquid that is easy to regenerate and compensate, and the etching rate is easy to control. Select processes and equipment that can provide constant operating conditions and automatic control of various solution parameters. This is achieved by controlling the amount of dissolved copper, pH value, solution concentration, temperature, uniformity of solution flow (spray system or nozzle and nozzle swing), etc.
Improve the uniformity of etching rate across the entire board surface
The uniformity of etching on the upper and lower sides of the board and various parts of the board is determined by the uniformity of the etchant flow rate on the surface of the board.
During the etching process, the etching rates on the upper and lower plates are often inconsistent. Generally speaking, the etching rate of the lower plate surface is higher than that of the upper plate surface. Because there is accumulation of solution on the upper plate surface, the etching reaction is weakened. The phenomenon of uneven etching on the upper and lower plate surfaces can be solved by adjusting the spray pressure of the upper and lower nozzles. A common problem with etching printed circuit boards is that it is difficult to etch the entire board surface cleanly at the same time. The edges of the board etch faster than the center of the board. Using a sprinkler system and oscillating the nozzles is an effective measure. Further improvement can be achieved by making the spray pressure different at the center of the board and the edge of the board, and by intermittent etching at the front and rear ends of the board to achieve etching uniformity across the entire board
Improved ability to safely handle and etch thin copper foil and thin laminates
When etching thin laminates such as the inner layers of multilayer boards, the board can easily wrap around the rollers and transfer wheels, resulting in scrap. Therefore, equipment for etching inner laminates must be able to process thin laminates smoothly and reliably. Many equipment manufacturers add gears or rollers to their etching machines to prevent this from happening. A better approach is to use additional oscillating Teflon-coated wire as a support for thin laminate transfer. For etching of thin copper foil (such as 1/2 or 1/4 ounce), it must be guaranteed not to be scratched or scratched. Thin copper foil cannot withstand the mechanical disadvantages of etching 1 ounce copper foil, and sometimes severe vibrations may scratch the copper foil
Pollution reduction issues
Copper contamination of water is a common problem in printed circuit production, and the use of ammonia-alkali etching liquid makes this problem even more serious. Because copper is complexed with ammonia, it is not easily removed by ion exchange or alkali precipitation. Therefore, the second spray operation method is used to rinse the board with copper-free additive liquid, which greatly reduces the amount of copper discharge. Then, an air knife is used to remove excess solution from the board before water rinsing, thereby reducing the water rinse burden on the copper and etching salts.
When To Choose Etching Processing?
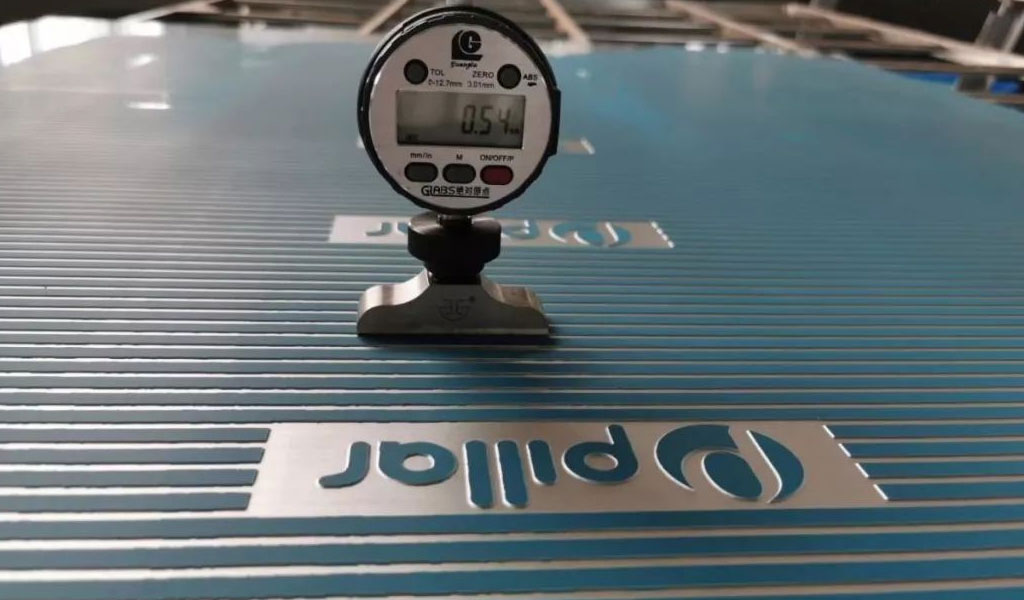
The metal parts to be processed have complex shapes, such as very thin stainless steel mesh, which is a typical example. By using etching technology, molding difficulty and processing costs can be reduced.
- If your product is very thin (thickness between 0.03mm–1mm), using other processes may cause product deformation. However, etching can ensure that the product does not deform. Typically, the thinner the product, the higher the precision.
- The etching process will not change the hardness, strength, formability and other physical properties of the metal material.
- Some metal materials are easy to break during the stamping process, and are prone to curling burrs, which affects the assembly of the product. However, etching can ensure that these materials are intact.
- Magnetic soft materials can maintain their original physical properties after etching.
- Products processed by etching are burr-free.
Cleaning and surface treatment of substrates (for smaller stainless steel etched flat workpieces, the coating process can be completed directly by silk screen printing. However, for stainless steel etched products with large areas where silk screen printing cannot be performed, the coating and development can only be done directly on the surface of the work piece. .)—->Coating—->Hot air pre-baking—->Exposure—->Development—->Fill light curing—->Drying—->Etching removal Ink—->Post-production—->Inspection—->Package and ship.