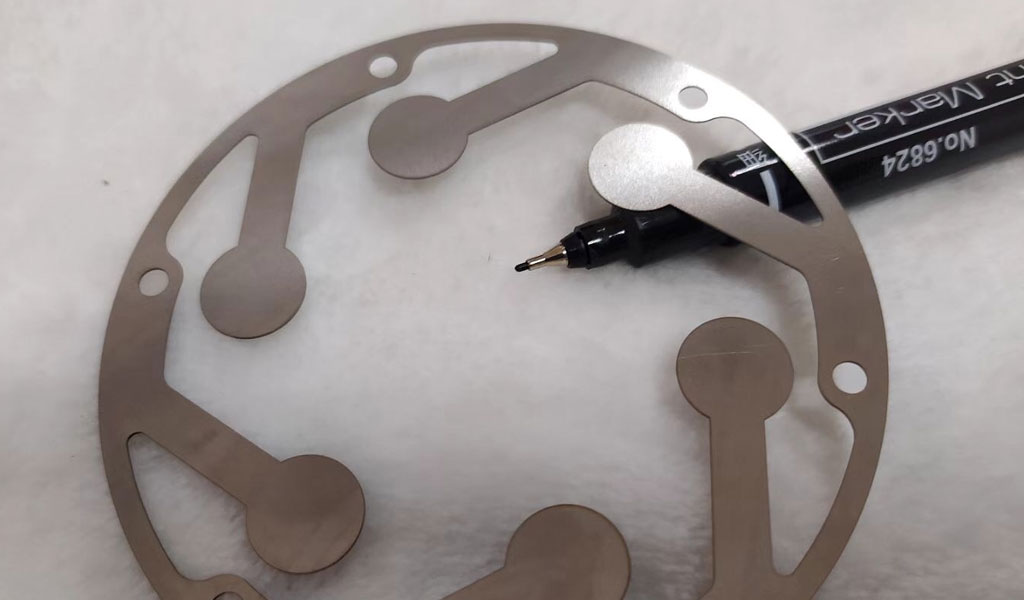
Chemical etching, a subtractive manufacturing process, involves the removal of material from a substrate using chemical solutions. This technique has found widespread applications in the production of precision parts, microelectronics, and various industrial processes.
The calculation of etching time is a critical aspect of this method, determining the precision and quality of the final product.
In this article, we delve into the intricate process of calculating etching time, examining the scientific principles, practical considerations, and advanced techniques that ensure accuracy and efficiency.
Fundamental Principles of Etching Time Calculation
Chemical etching, also known as chemical milling or photochemical machining, relies on the reaction between a chemical etchant and the substrate material. Commonly used etchants include acids and bases, each selected based on the material to be etched. The process can be divided into several stages:
- Preparation of the Substrate: The substrate, often a metal or silicon wafer, is cleaned to remove contaminants that might interfere with the etching process.
- Application of Resist: A resist, such as photoresist or wax, is applied to protect areas that should not be etched. The resist is patterned using photolithography or other methods to define the etching areas.
- Etching: The substrate is immersed in the etchant solution. The exposed areas react with the etchant, leading to material removal.
- Resist Removal and Cleaning: After etching, the resist is stripped away, and the substrate is cleaned to remove any residual chemicals.
The etching time is influenced by several factors, including the etchant type, concentration, temperature, agitation, and the nature of the substrate. The calculation primarily revolves around the etch rate, which is the rate at which material is removed from the substrate. The etch rate is typically expressed in micrometers per minute (µm/min) and can be determined experimentally or from established data for specific etchant-substrate combinations.
Formula for Etching Time
Calculating the etching time in a chemical etching process is essential to achieving the desired precision and quality in the final product. The basic formula to determine the etching time is derived from the relationship between the etch rate and the depth of material to be removed.
However, this formula can be adapted to account for various influencing factors, such as temperature, concentration, and agitation.
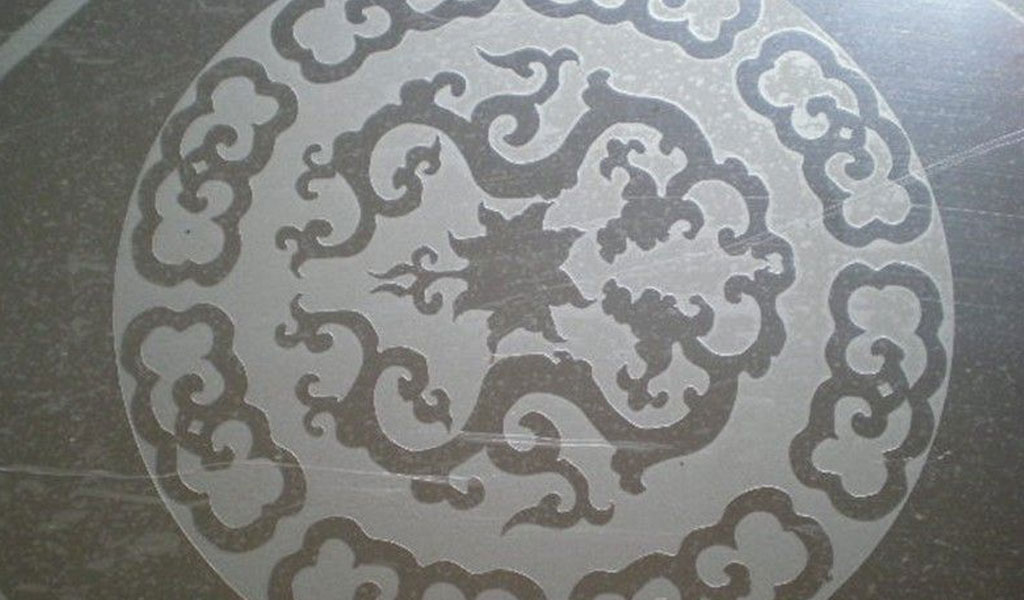
Basic Formula
The fundamental formula for calculating etching time is:
t=d/r
Where:
- t is the etching time (minutes)
- d is the desired depth of etching (micrometers or other units of length)
- r is the etch rate (micrometers per minute or other units of length per time)
This simple formula assumes a constant etch rate throughout the process. However, in real-world scenarios, the etch rate may vary due to changes in etchant concentration, temperature, and other factors. Therefore, a more comprehensive approach is often necessary.
Comprehensive Formula
To account for varying conditions, the etching time calculation can incorporate factors such as etchant concentration (C), temperature (T), and agitation (A). The etch rate (r) can be expressed as a function of these variables:
r=f(C,T,A)
A common way to represent the temperature dependence of the etch rate is through the Arrhenius equation, which describes how reaction rates increase with temperature:
r=r0⋅e-Ea/RT
Where:
- r0 is the pre-exponential factor (etch rate at reference conditions)
- Ea is the activation energy of the etching reaction (Joules per mole)
- R is the universal gas constant (8.314 J/(mol\cdotpK)
- T is the temperature in Kelvin (K)
For practical purposes, the etch rate can also be empirically determined through experimentation, leading to an experimentally-derived etch rate constant (kkk) that incorporates the effects of concentration, temperature, and agitation:
For practical purposes, the etch rate can also be empirically determined through experimentation, leading to an experimentally-derived etch rate constant (kkk) that incorporates the effects of concentration, temperature, and agitation:
r=k⋅Cm⋅Tn⋅Ap
Where:
- k is an experimentally determined etch rate constant
- C is the concentration of the etchant
- T is the temperature
- A is the level of agitation
- m, n, and p are empirical constants determined through experimentation
Example Calculation
Consider a scenario where you need to etch a depth of 10 micrometers (d=10 μm) using an etchant with a known etch rate of 2 micrometers per minute (r=2 μm/min):
Using the basic formula:
t=10 μm/(2 μm/min)=5 min
In a more complex scenario, suppose the etch rate is influenced by temperature and is given by the Arrhenius equation. If the pre-exponential factor (ro) is 3 micrometers per minute, the activation energy (Ea) is 50 kJ/mol, and the process operates at 298 K:
First, convert the activation energy to Joules per mole:
Ea=50 kJ/mol=50,000 J/mol
Then, calculate the etch rate:
r=3 μm/min⋅e−50,000/8.314⋅298
r≈3 μm/min⋅e−20.12
r≈3 μm/min⋅2.06×10−9
r≈6.18×10−9 μm/min
This indicates a significantly slower etch rate due to the high activation energy at this temperature, resulting in a much longer etching time.
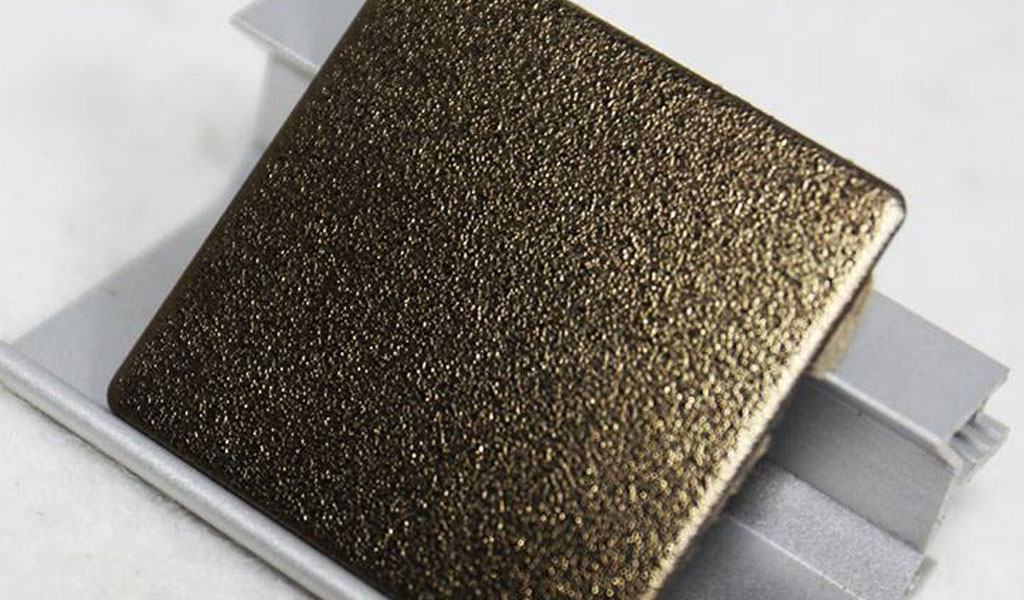
Factors Influencing Etching Time
In chemical etching, achieving precise control over the etching time is critical to producing high-quality and accurate components. Several factors influence the etching time, each affecting the rate at which material is removed from the substrate.
Understanding these factors allows for better optimization and control of the etching process.
1. Etchant Concentration
The concentration of the etchant in the solution is a primary factor influencing the etch rate. Higher concentrations typically result in faster etch rates, reducing the overall etching time. However, an excessively high concentration can lead to uneven etching, increased undercutting, and surface roughness.
- Optimal Concentration: Finding the optimal concentration is crucial. Too low, and the etching process will be inefficient and slow. Too high, and it can cause defects in the material.
- Control: Regular monitoring and adjusting the concentration of the etchant solution can maintain a consistent etch rate.
2. Temperature
Temperature plays a significant role in the metal etching process. Higher temperatures generally increase the etch rate due to the acceleration of chemical reactions. The relationship between temperature and etch rate is often described by the Arrhenius equation.
- Uniform Temperature: Maintaining a uniform temperature throughout the etching process is essential for consistent etching. Temperature gradients can lead to non-uniform etching.
- Temperature Limits: Each etchant and substrate combination has an optimal temperature range. Exceeding this range can lead to undesirable side effects, such as excessive undercutting or damage to the substrate.
3. Agitation
Agitation, or stirring, of the etchant solution ensures uniform distribution of the etchant around the substrate. It helps in preventing the buildup of reaction by-products that can slow down the etch rate.
- Consistent Agitation: Consistent and controlled agitation helps achieve uniform etching across the entire substrate surface.
- Methods: Agitation can be achieved through mechanical stirring, ultrasonic agitation, or flow systems that continuously circulate the etchant.
4. Material Properties
The chemical composition and properties of the substrate material significantly influence the etch rate. Different materials react at different rates to the same etchant.
- Material Selection: Choosing the right etchant for the specific material is crucial for achieving the desired etch rate and quality.
- Material Hardness: Harder materials may etch more slowly than softer materials.
- Crystal Structure: The crystallographic orientation of the material can also affect the etch rate, especially in anisotropic etching processes.
5. Masking and Patterning
The quality and type of resist used to mask the substrate impact the etching process. An effective resist should withstand the etchant and precisely define the areas to be etched.
- Resist Material: The choice of resist material affects its resistance to the etchant and the precision of the etching.
- Pattern Accuracy: High-resolution patterning techniques, such as photolithography, are essential for achieving precise and accurate etching.
6. Etchant Depletion
As etching progresses, the concentration of the active etchant components decreases, leading to a reduction in the etch rate over time.
- Replenishment: Regular replenishment or continuous flow of fresh etchant can maintain a steady etch rate.
- Monitoring: Real-time monitoring of etchant concentration can help in making timely adjustments to maintain consistency.
7. Etch Depth and Time
The depth of etching desired directly influences the etching time. The deeper the etch, the longer the etching time required.
- Proportionality: The etching time is proportional to the desired etch depth for a given etch rate.
- Control: Precise control over etch depth requires accurate timing and monitoring of the etching process.
8. Etching Area and Geometry
The surface area and geometry of the substrate being etched can affect the etching time. Larger surface areas or complex geometries may require longer etching times to achieve uniformity.
- Surface Area: Larger areas may need more etchant and longer processing times.
- Complex Geometries: Intricate designs or high-aspect-ratio features can pose challenges, requiring careful control of etching parameters to achieve uniform results.
9. By-products and Contaminants
Reaction by-products and contaminants in the etchant solution can interfere with the etching process, reducing the etch rate and affecting the quality of the etch.
- Removal: Regular removal of by-products and contaminants is essential to maintain an effective etch rate.
- Purity: Using high-purity etchants and maintaining clean conditions can prevent contamination-related issues.
Practical Implications
Understanding and controlling these factors is crucial for optimizing the chemical etching process. Here are some practical implications:
- Process Optimization: By fine-tuning etchant concentration, temperature, and agitation, manufacturers can achieve optimal etching conditions for specific materials and applications.
- Quality Control: Ensuring consistent etching conditions leads to higher quality and more precise components.
- Efficiency: Proper management of etchant concentration, temperature, and agitation can reduce etching times and improve production efficiency.
Advanced Techniques for Factor Control
Advanced techniques and technologies are employed to control and optimize these factors:
- Automated Systems: Automation in chemical etching systems allows for precise control of temperature, agitation, and etchant replenishment.
- Real-time Monitoring: Technologies like optical monitoring and interferometry provide real-time feedback on etch depth and rate, enabling dynamic adjustments.
- Simulation and Modeling: Computational tools simulate the etching process, providing insights into the effects of various parameters and helping optimize the process.
Experimental Determination of Etch Rate
While theoretical calculations provide a baseline, practical experimentation is often necessary to determine the exact etch rate for a specific process. This involves conducting test etches and measuring the material removal over a fixed period.
Steps for Experimental Determination
Sample Preparation: Prepare a sample substrate with the same material and dimensions as the actual workpiece.
Etching: Immerse the sample in the etchant solution for a predetermined time.
Measurement: After etching, measure the depth of material removed using techniques such as profilometry, microscopy, or weight loss measurement.
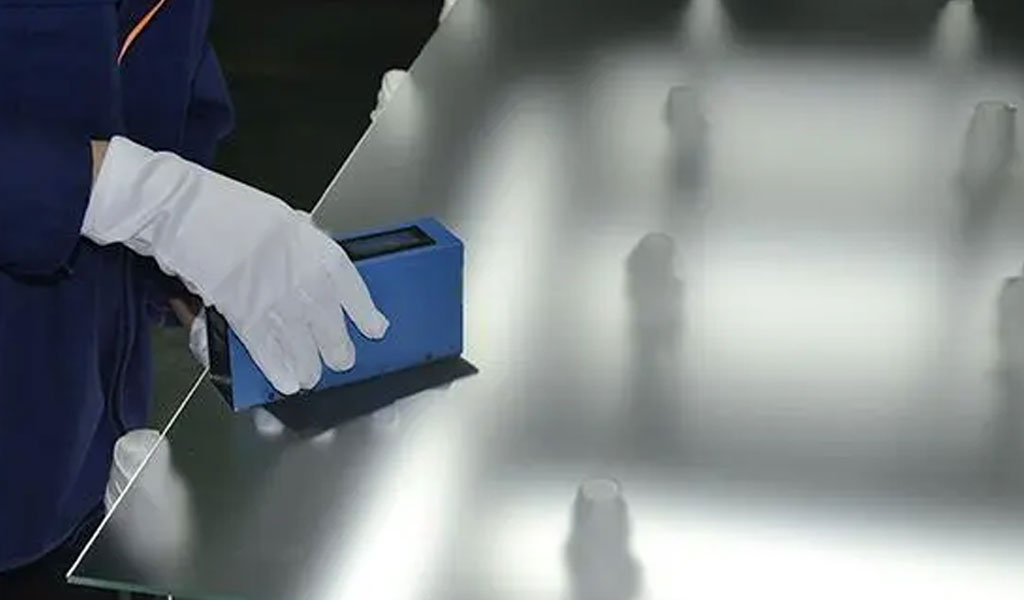
Calculation: Calculate the etch rate using the formula:
r=d/r
Where:
- d is the depth of material removed (micrometers)
- t is the etching time (minutes)
Repeat and Average: Repeat the experiment multiple times and average the results to obtain a reliable etch rate.
Advanced Techniques for Etching Time Calculation
For high-precision applications, more advanced methods and tools are employed to ensure accurate etching time calculations. These include:
- Computer Simulations: Software tools can simulate the etching process, taking into account various parameters such as etchant concentration, temperature, and material properties. These simulations provide a detailed understanding of how different factors influence the etch rate and help optimize the process.
- Real-Time Monitoring: Techniques like optical monitoring and interferometry allow real-time observation of the etching process. These methods provide immediate feedback on etch depth and rate, enabling dynamic adjustments to the process parameters.
- Etch Rate Models: Mathematical models, such as the Arrhenius equation for temperature dependence and diffusion-based models, provide a more comprehensive understanding of the etch rate. These models incorporate factors like activation energy, diffusion coefficients, and reaction kinetics.
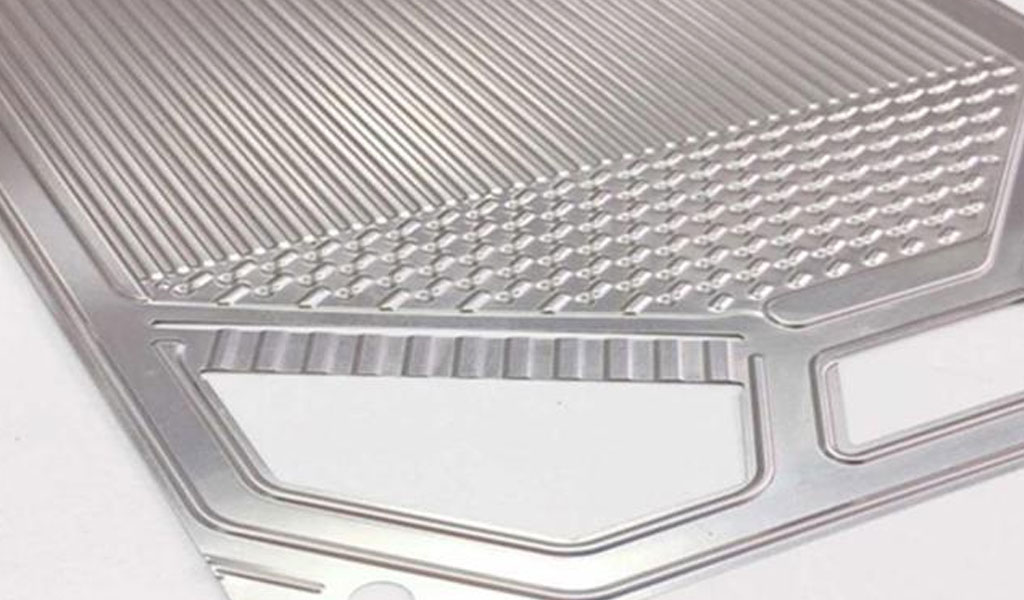
Conclusion
Calculating etching time in chemical etching processes is a multifaceted task that requires a deep understanding of chemical reactions, material properties, and process parameters. By combining theoretical principles with practical experimentation and advanced technologies, precise control over the etching process can be achieved. As industries continue to demand higher precision and efficiency, the importance of accurate etching time calculation will only grow, driving further innovations in this essential manufacturing technique.