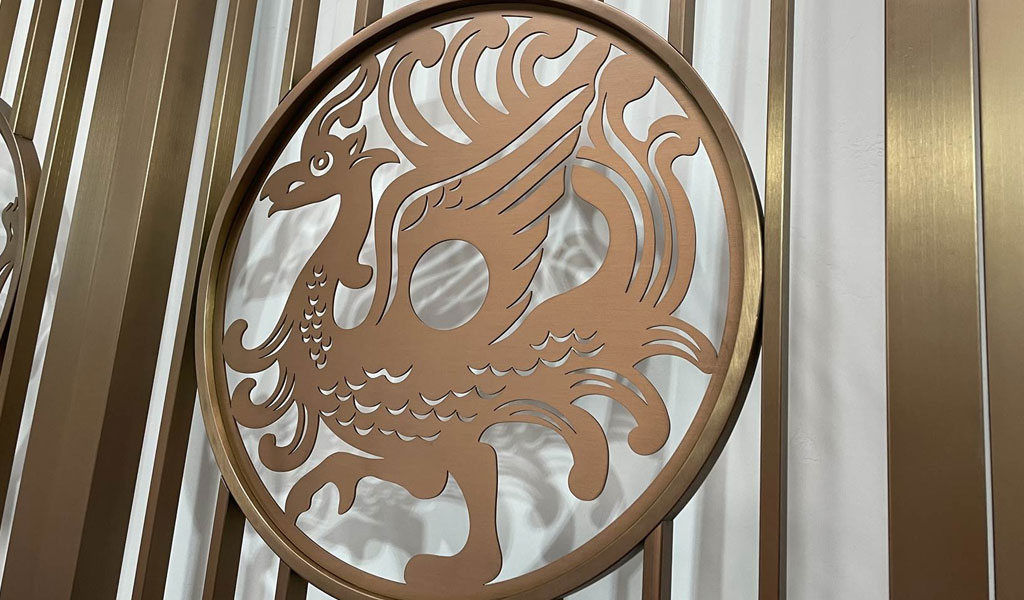
Chemical engraving, also known as chemical etching, is a technique used to create precise, detailed patterns or designs on the surface of materials, particularly metals such as stainless steel. This process relies on the use of acid-based solutions to selectively remove material, resulting in a pattern that is etched into the metal’s surface. Unlike traditional engraving methods, such as mechanical engraving, chemical engraving offers several advantages, including the ability to work with delicate materials, produce highly intricate designs, and minimize tool wear. The process is particularly valued in industries requiring high precision, including aerospace, medical devices, automotive, and electronics.
The origins of chemical engraving date back to the early 19th century, with its roots in the development of etching techniques used in art and printmaking.
History of Chemical Engraving
The industrial adaptation of chemical etching, however, began in the mid-20th century as advances in chemistry and materials science enabled more controlled and consistent processes. As industrial applications for stainless steel and other metals grew, chemical engraving became an indispensable tool for manufacturers. It allowed for the production of high-quality, reproducible designs without the need for extensive tooling, making it particularly useful for high-volume production.
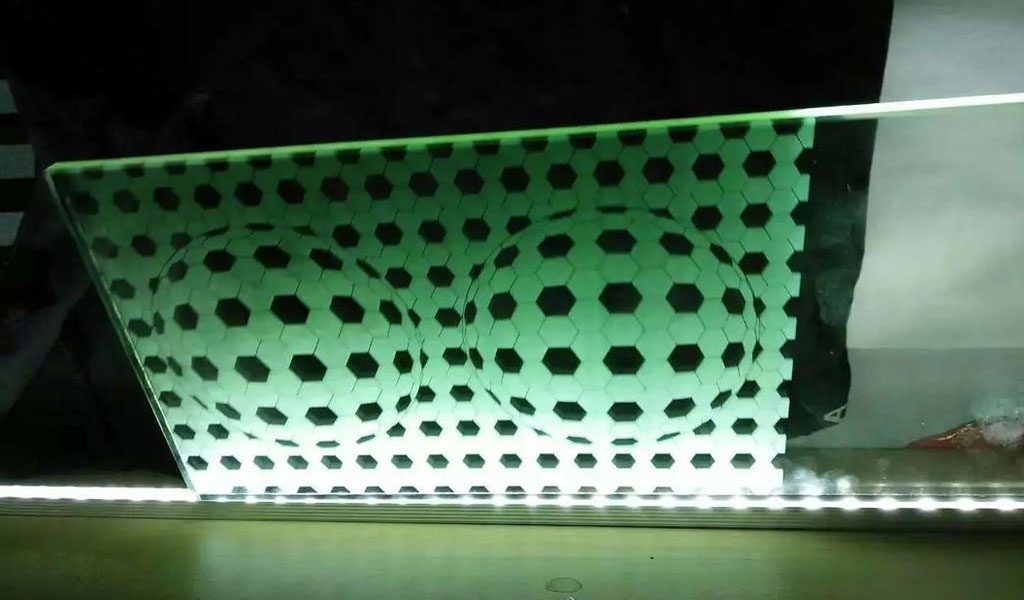
Principles of Chemical Engraving
Chemical engraving operates on the principle of selective corrosion. The process involves applying a resist (or mask) to the surface of the material, followed by exposure to a chemical etching solution, typically an acidic mixture that reacts with the metal. The resist protects areas of the surface from the etchant, allowing only the exposed areas to be corroded.
The resist can be applied in various ways, including:
- Photographic Resist: In this method, a photographic film or light-sensitive material is applied to the surface. The design is transferred to the film, which is then exposed to UV light. The unexposed areas are removed, leaving behind a resist layer that shields the metal from the etchant.
- Laser Resist: For more complex or high-precision designs, a laser can be used to directly apply a resist layer onto the surface of the stainless steel. The laser creates microstructures on the material that prevent etching in certain areas.
- Adhesive Resist: A simple approach where a resist material, such as a vinyl film or a wax-based coating, is manually applied. The design is cut into the resist with a precision cutter or by hand, leaving areas exposed for chemical engraving.
Once the resist is in place, the metal is submerged in an etching bath containing an appropriate acidic solution, often based on hydrochloric acid, nitric acid, or ferric chloride. The acid reacts with the exposed metal, creating a pit or groove in the material. The duration and concentration of the etchant, along with the temperature, can be adjusted to control the depth and texture of the engraving.
Advantages of Chemical Engraving
Chemical engraving offers several significant advantages compared to traditional mechanical engraving methods, particularly for applications involving stainless steel:
- Precision and Detail: Chemical etching allows for the creation of extremely fine, detailed designs with high accuracy. This is particularly beneficial for applications that require microscopic features, such as those found in electronics and medical devices.
- No Tool Wear: Unlike mechanical engraving, which relies on rotating tools that can wear down over time, chemical engraving does not cause tool degradation. This eliminates the need for frequent tool replacements and ensures consistency in high-volume production runs.
- Non-Contact Process: Since chemical engraving does not involve direct contact between tools and the material, there is less risk of surface damage, such as warping or distortion. This makes it ideal for delicate or thin materials.
- Cost-Effective for High Volumes: Once the resist is applied, chemical engraving can be used to produce a large number of identical parts quickly and at a lower cost than traditional mechanical engraving. The process is particularly suited for mass production runs.
- Flexibility: Chemical engraving can be applied to a wide range of metals, including stainless steel, which is known for its corrosion resistance, durability, and strength. This versatility makes chemical engraving an ideal choice for industries that require high-quality and reliable marking, such as aerospace, medical, automotive, and defense.
Types of Stainless Steel Used in Chemical Engraving
Stainless steel is a popular material for chemical engraving due to its durability, corrosion resistance, and aesthetic appeal. Different grades of stainless steel exhibit varying characteristics that make them suitable for specific applications:
- 304 Stainless Steel: One of the most commonly used grades of stainless steel, 304 is known for its excellent corrosion resistance and good formability. It is commonly used in the food, pharmaceutical, and medical industries. Its ability to be chemically etched with fine details makes it a popular choice for decorative and functional applications.
- 316 Stainless Steel: This grade offers higher resistance to corrosion, particularly in chloride environments, making it ideal for applications in marine and chemical processing industries. Its ability to withstand harsh environments makes it a preferred choice for parts requiring chemical engraving that must endure extreme conditions.
- 430 Stainless Steel: A lower-cost, less corrosion-resistant option, 430 stainless steel is often used in decorative applications and household appliances. While it is not as suitable for harsh environments as 304 or 316, it is still an excellent choice for chemical engraving applications that do not require the highest levels of corrosion resistance.
- 440C Stainless Steel: Known for its high hardness and excellent wear resistance, 440C stainless steel is often used in applications that require sharpness or durability, such as in medical devices, tooling, and knives. Its resistance to corrosion, while not as high as that of 316, still makes it suitable for chemical engraving in certain contexts.
- Duplex Stainless Steel: Duplex grades, such as 2205, combine the properties of both austenitic and ferritic stainless steels. These materials offer superior strength and resistance to stress corrosion cracking. Duplex stainless steels are often used in high-strength, high-pressure applications, where chemical engraving can be used to create intricate markings without compromising material integrity.
The Chemical Engraving Process
Chemical engraving of stainless steel involves several stages, each critical to achieving the desired outcome. These stages typically include:
1. Surface Preparation
The surface of the stainless steel must be thoroughly cleaned before applying the resist. Any oils, grease, dirt, or oxidation must be removed to ensure that the resist adheres properly and that the etching process is uniform. Common cleaning methods include:
- Abrasive Blasting: A process where small abrasive particles are blasted onto the metal surface to remove contaminants and create a uniform texture.
- Ultrasonic Cleaning: High-frequency sound waves are used to agitate a cleaning solution, effectively removing dirt and contaminants from the surface.
- Chemical Cleaning: An acid-based cleaning solution is applied to remove oils, oxides, or other contaminants from the metal’s surface.
2. Resist Application
Once the surface is clean and free of contaminants, the resist material is applied. As mentioned earlier, different methods can be used to apply the resist, including photographic, laser, or adhesive-based systems. The resist forms a protective layer that shields certain areas of the stainless steel from the etching solution.
3. Exposure and Development
In the case of photographic resist, the material is exposed to UV light through a photomask or film. The areas that are exposed to light harden, while the unexposed areas remain soft. The unexposed resist is then removed in a development process, leaving the desired pattern on the surface of the metal. In laser-based systems, the laser directly burns or etches the resist, making the design areas vulnerable to the etching process.
4. Etching
With the resist in place, the stainless steel is submerged in an etching solution. The composition of the etchant varies depending on the type of metal being etched. For stainless steel, common etchants include ferric chloride, nitric acid, or a mixture of hydrochloric acid and hydrogen peroxide. The solution reacts with the exposed metal, dissolving it and leaving behind the desired pattern or design. The depth of the etching can be controlled by adjusting the exposure time and concentration of the etchant.
5. Resist Removal and Finishing
After the etching process is complete, the resist material is removed, revealing the etched pattern on the stainless steel surface. The surface is then washed to remove any remaining etching solution or resist residues. Additional finishing steps, such as polishing or passivation, may be required to enhance the appearance or further protect the metal from corrosion.
Applications of Chemical Engraving on Stainless Steel
Chemical engraving of stainless steel is widely used across numerous industries due to its ability to produce precise, intricate designs with minimal material distortion. Some of the most common applications include:
- Aerospace and Defense: Chemical engraving is used to mark or etch serial numbers, barcodes, logos, and other identifying information on parts and components used in aerospace and defense applications. The precision and durability of chemical engraving ensure that these markings remain legible throughout the life of the component, even in harsh conditions.
- Medical Devices: Stainless steel is commonly used in medical devices due to its biocompatibility and corrosion resistance. Chemical engraving allows for the precise marking of parts such as surgical instruments, implants, and diagnostic tools, often with intricate markings for identification or branding.
- Electronics: In the electronics industry, chemical engraving is used to create detailed markings on components like circuit boards, connectors, and heatsinks. The high precision of chemical etching is essential