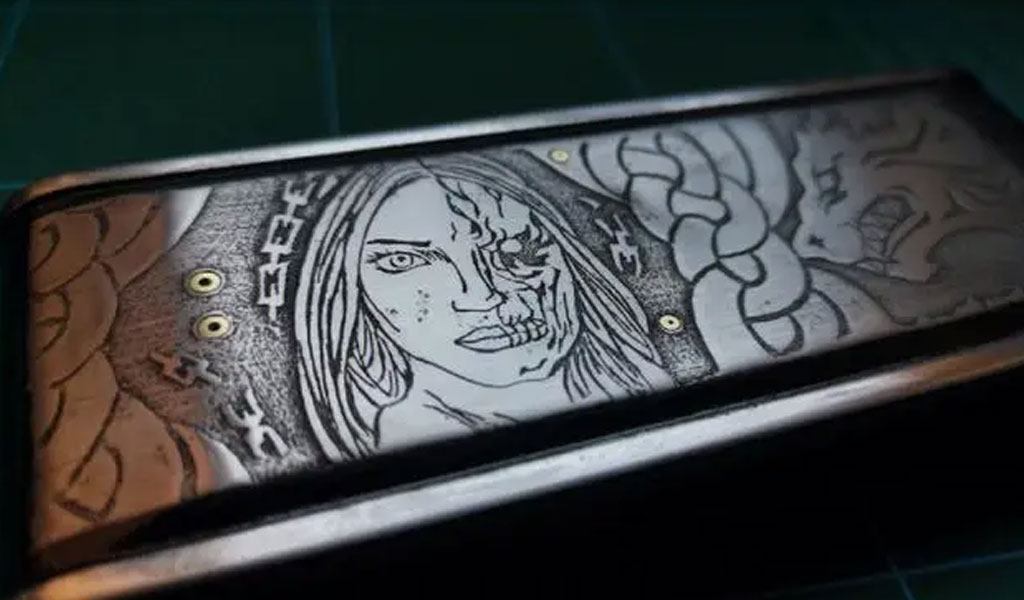
In the world of manufacturing and precision engineering, the choice of cutting methods can significantly impact the quality, efficiency, and intricacy of the final product. Chemical etching and conventional cutting techniques stand as two distinct methodologies, each with its own set of advantages and limitations. This article aims to delve into the intricacies of both processes, highlighting their mechanisms, applications, benefits, and drawbacks to aid in making informed decisions within various industries.Understanding Chemical Etching: Chemical etching, also known as chemical milling or photochemical machining, is a subtractive manufacturing process that employs chemical reactions to selectively remove material from a substrate.
It involves the use of acids or alkaline solutions to dissolve specific areas of the workpiece, creating intricate patterns, designs, or precise shapes with exceptional accuracy and minimal material waste.
The Process of Chemical Etching: The process begins with the preparation of a mask or protective layer on the material’s surface, typically made of photoresist or a similar substance. This mask is patterned using photolithography or other methods, exposing only the areas that need to be etched. The material is then exposed to a chemical solution, which selectively dissolves the unprotected areas, leaving behind the desired shape or pattern.
Advantages of Chemical Etching:
- High Precision: Chemical etching offers unparalleled precision, allowing for intricate designs and fine details that might be unattainable through conventional cutting methods.
- Burr-Free Finish: The process produces smooth edges without burrs or mechanical stresses, maintaining the integrity of the material.
- Complex Geometries: It excels in producing complex and multi-level geometries with high repeatability.
- Material Versatility: Chemical etching can be applied to a wide range of materials, including metals, alloys, and polymers.
Limitations of Chemical Etching:
- Material Thickness: Chemical etching is more suitable for thin materials, and thicker materials may pose challenges or require specialized techniques.
- Initial Setup: The initial setup for chemical etching involves designing masks and preparing chemical solutions, which can be time-consuming and may require expertise.
- Environmental Considerations: The disposal of chemical waste must be handled with care and adherence to environmental regulations due to the use of corrosive chemicals.
Conventional Cutting Methods: Conventional cutting techniques encompass a variety of processes such as milling, turning, drilling, sawing, and grinding. These methods involve the use of mechanical tools to remove material from a workpiece to achieve the desired shape, size, or finish.
Processes and Mechanisms:
- Milling: Involves rotary cutters to remove material from the workpiece.
- Turning: Rotates the workpiece while a cutting tool removes material.
- Drilling: Creates holes through the application of a rotating tool.
- Sawing: Uses a blade or abrasive wire to cut through the material.
- Grinding: Abrasive grains remove material by abrasion, resulting in a fine finish.
Advantages of Conventional Cutting:
- Versatility: Conventional cutting methods are versatile and can be applied to a wide range of materials, including metals, plastics, ceramics, and composites.
- Suitable for Various Thicknesses: Unlike chemical etching, conventional cutting methods are suitable for both thin and thick materials.
- Faster Prototyping: For simple designs or prototypes, conventional cutting can often be quicker to set up and execute.
- Flexibility: Operators have greater control over the process and can make adjustments in real-time.
Limitations of Conventional Cutting:
- Tolerance and Precision: Achieving high levels of precision and intricate designs can be challenging compared to chemical etching.
- Material Waste and Tool Wear: Conventional cutting methods generate more waste material and can cause tool wear, affecting cost-effectiveness.
- Surface Integrity: Some methods might introduce burrs, surface imperfections, or residual stresses in the material.
Conclusion: Both chemical etching and conventional cutting methods have their distinct advantages and limitations. The choice between these techniques ultimately depends on the specific requirements of the project, material properties, desired precision, and economic considerations. Chemical etching excels in intricate designs and high precision but may not be suitable for thicker materials or rapid prototyping. On the other hand, conventional cutting methods offer versatility and quicker setup but may lack the precision and fine detailing achievable through chemical etching. Understanding the nuances of each method enables manufacturers and engineers to make informed decisions, optimizing the manufacturing process for superior results.
As technology advances, innovations in both chemical etching and conventional cutting methods continue to refine these processes, offering improved capabilities and efficiencies across various industries.