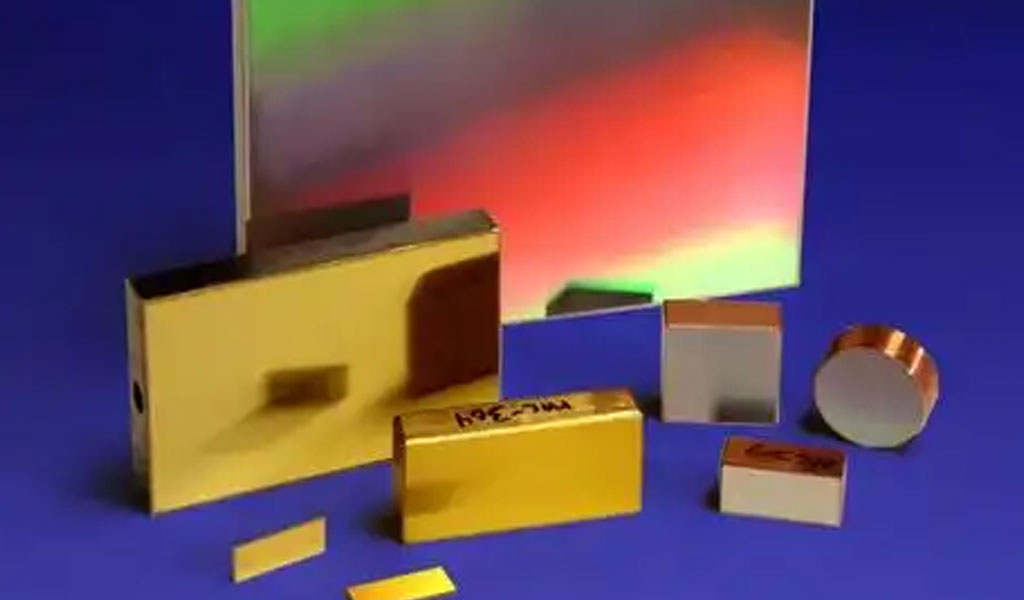
Diffraction gratings are optical components with a periodic structure that splits and diffracts light into several beams traveling in different directions.
The angles of these beams depend on the spacing of the grating and the wavelength of the light, so that the grating acts as a dispersive element.
Diffraction gratings are commonly used in monochromators and spectrometers to analyze the wavelengths present in a beam of light.
There are several methods for designing and fabricating diffraction gratings, each with its own advantages and limitations. Two prominent methods are the one-point method and the two-point method, particularly for etched diffraction gratings. This article delves into the intricacies of these methods, providing a comprehensive comparison and detailed analysis.
One-Point Method for Etched Diffraction Grating Design
The one-point method is a straightforward approach to designing diffraction gratings. It involves creating a periodic structure by etching a single point on the substrate and then replicating this pattern across the surface. This method is relatively simple and cost-effective, making it suitable for mass production.
Fabrication Process
The fabrication process for the one-point method typically involves the following steps:
- Substrate Preparation: The substrate material, often glass or silicon, is cleaned and prepared for etching.
- Mask Application: A photoresist mask is applied to the substrate. The mask is patterned with the desired grating structure using photolithography.
- Etching: The substrate is etched using a chemical or plasma etching process. The etching depth and profile are carefully controlled to achieve the desired diffraction properties.
- Mask Removal: The photoresist mask is removed, leaving the etched grating structure on the substrate.
- Post-Processing: The grating may undergo additional post-processing steps, such as coating with a reflective material, to enhance its performance.
Advantages
- Simplicity: The one-point method is straightforward and requires fewer steps compared to more complex methods.
- Cost-Effectiveness: The simplicity of the process translates to lower production costs, making it suitable for large-scale manufacturing.
- Uniformity: The replication process ensures that the grating structure is uniform across the substrate, which is crucial for consistent performance.
Limitations
- Limited Flexibility: The one-point method offers less flexibility in terms of grating design. The periodic structure is fixed, and any deviations can be challenging to implement.
- Resolution: The resolution of the grating is limited by the etching process. Fine features may be difficult to achieve, affecting the diffraction efficiency.
Two-Point Method for Etched Diffraction Grating Design
The two-point method is a more advanced approach to designing diffraction gratings. It involves creating a periodic structure by etching two points on the substrate and then interpolating the pattern between these points. This method offers greater flexibility and precision, making it suitable for high-performance applications.
Fabrication Process
The fabrication process for the two-point method involves the following steps:
- Substrate Preparation: Similar to the one-point method, the substrate is cleaned and prepared for etching.
- Dual Mask Application: Two photoresist masks are applied to the substrate. Each mask is patterned with a different part of the grating structure using photolithography.
- Dual Etching: The substrate is etched in two separate steps, each corresponding to one of the masks. The etching depth and profile are carefully controlled to achieve the desired diffraction properties.
- Mask Removal: Both photoresist masks are removed, leaving the etched grating structure on the substrate.
- Post-Processing: The grating may undergo additional post-processing steps, such as coating with a reflective material, to enhance its performance.
Advantages
- Flexibility: The two-point method offers greater flexibility in terms of grating design. The ability to interpolate between two points allows for more complex and customized structures.
- Precision: The dual etching process provides higher precision, enabling the creation of fine features and improving diffraction efficiency.
- Versatility: This method can be adapted to various substrate materials and grating designs, making it suitable for a wide range of applications.
Limitations
- Complexity: The two-point method is more complex and requires additional steps compared to the one-point method.
- Cost: The increased complexity translates to higher production costs, which may not be suitable for large-scale manufacturing.
- Alignment: The dual etching process requires precise alignment of the two masks, which can be challenging and time-consuming.
Comparison of One-Point and Two-Point Methods
To provide a clear comparison between the one-point and two-point methods, the following table summarizes their key features, advantages, and limitations:
Feature | One-Point Method | Two-Point Method |
---|---|---|
Fabrication Process | Single mask and etching step | Dual masks and etching steps |
Complexity | Low | High |
Cost | Low | High |
Flexibility | Limited | High |
Precision | Moderate | High |
Uniformity | High | Moderate |
Alignment Requirements | Low | High |
Post-Processing | Simple | Complex |
Suitability | Mass production | High-performance applications |
Applications of Etched Diffraction Gratings
Etched diffraction gratings are used in a variety of applications, including:
- Spectroscopy: Diffraction gratings are essential components in spectrometers, where they separate light into its constituent wavelengths for analysis.
- Telecommunications: Gratings are used in optical communication systems to multiplex and demultiplex light signals.
- Astronomy: Diffraction gratings are employed in telescopes and other astronomical instruments to analyze the spectral composition of celestial objects.
- Metrology: Gratings are used in precision measurement instruments to calibrate wavelengths and angles.
- Laser Systems: Diffraction gratings are used in laser systems to control the wavelength and direction of laser beams.
Conclusion
The one-point and two-point methods for etched diffraction grating design offer distinct advantages and limitations. The one-point method is simple, cost-effective, and suitable for mass production, while the two-point method provides greater flexibility, precision, and versatility, making it ideal for high-performance applications. The choice between these methods depends on the specific requirements of the application and the available resources.
As technology advances, the design and fabrication of diffraction gratings continue to evolve, offering new possibilities for optical systems and applications. Future research may focus on improving the precision and flexibility of these methods, as well as exploring new materials and fabrication techniques to enhance the performance of diffraction gratings.