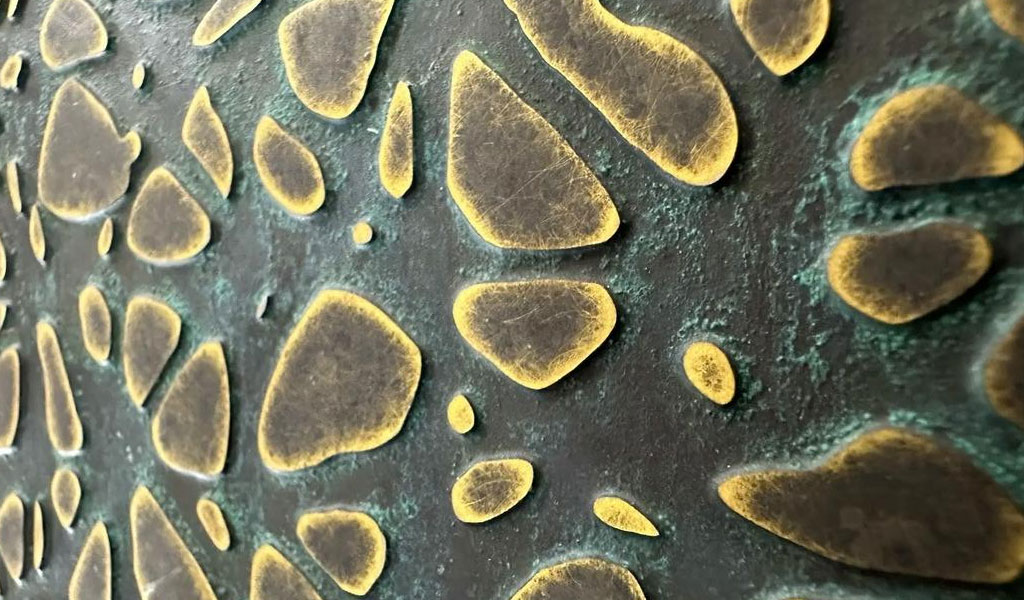
Etching is a critical process in the manufacturing of printed circuit boards (PCBs), semiconductors, and other electronic components. Among the various etching solutions, acid copper chloride (CuCl2) stands out due to its high etching rate and selectivity. However, the conventional use of CuCl2 etching solutions faces challenges related to waste management and environmental impact. Electrochemical regeneration has emerged as a promising solution to address these issues, offering a sustainable and efficient method for recycling the etching solution. This article provides an in-depth review of electrochemically regenerated acid copper chloride etching solutions, covering their principles, advantages, challenges, and recent advancements.
Principles of Electrochemical Regeneration
Electrochemical regeneration involves the use of electrical current to convert spent etching solution back into its active form. The process typically occurs in an electrochemical cell, where the spent solution is subjected to an electric field. The key reactions involved in the regeneration of CuCl2 etching solution are:
Cathodic Reaction:
Cu2++2e−→Cu
At the cathode, copper ions (Cu2+) are reduced to metallic copper (Cu), which can be recovered and reused.
Anodic Reaction:
2Cl−→Cl2+2e−
At the anode, chloride ions (Cl-) are oxidized to chlorine gas (Cl2), which can be captured and reused in the etching process.
The overall reaction can be summarized as:CuCl2→Cu+Cl2CuCl2→Cu+Cl2
Advantages of Electrochemical Regeneration
Electrochemical regeneration offers several advantages over traditional methods of waste management:
Environmental Benefits:
Reduced Waste: By regenerating the etching solution, the amount of hazardous waste generated is significantly reduced.
Lower Emissions: The process minimizes the release of harmful chemicals into the environment, contributing to a cleaner production process.
Economic Benefits:
Cost Savings: The recovery and reuse of copper and chlorine reduce the need for fresh raw materials, leading to cost savings.
Efficiency: The process is highly efficient, allowing for continuous operation and minimal downtime.
Operational Benefits:
Consistency: Electrochemical regeneration ensures a consistent composition of the etching solution, maintaining high etching rates and selectivity.
Automation: The process can be automated, reducing the need for manual intervention and improving overall productivity.
Challenges and Limitations
Despite its advantages, electrochemical regeneration of CuCl2 etching solutions faces several challenges:
Energy Consumption:
The process requires a significant amount of electrical energy, which can be a limiting factor in terms of cost and environmental impact.
Equipment Maintenance:
Electrochemical cells and associated equipment require regular maintenance to ensure optimal performance and longevity.
Chemical Management:
Handling and storing chlorine gas can be hazardous, requiring specialized equipment and safety protocols.
Scalability:
Scaling up the process for large-scale industrial applications can be complex and costly.
Recent Advancements
Recent research and technological advancements have focused on addressing the challenges associated with electrochemical regeneration. Some notable developments include:
Improved Electrode Materials:
The development of advanced electrode materials, such as titanium-based anodes and graphite-based cathodes, has enhanced the efficiency and durability of electrochemical cells.
Optimized Process Parameters:
Studies have optimized process parameters, including current density, temperature, and electrolyte concentration, to improve the regeneration efficiency and reduce energy consumption.
Integrated Systems:
Integrated systems that combine electrochemical regeneration with other waste management techniques, such as ion exchange and membrane filtration, have been developed to enhance overall performance.
Automation and Control:
Advanced automation and control systems have been implemented to monitor and optimize the regeneration process in real-time, ensuring consistent performance and minimizing downtime.
Comparative Analysis
To provide a comprehensive understanding of the electrochemical regeneration process, a comparative analysis with traditional waste management methods is presented in the table below:
Parameter | Electrochemical Regeneration | Traditional Waste Management |
---|---|---|
Waste Reduction | High | Low |
Energy Consumption | Moderate to High | Low to Moderate |
Cost | Moderate | High |
Environmental Impact | Low | High |
Efficiency | High | Moderate |
Maintenance | Moderate | High |
Scalability | Moderate | Low |
Automation | High | Low |
Case Studies
Several case studies have demonstrated the practical application and benefits of electrochemical regeneration in industrial settings. For instance, a leading PCB manufacturer implemented an electrochemical regeneration system, resulting in a 50% reduction in waste generation and a 30% decrease in operational costs. Another study in the semiconductor industry showed that the regeneration process improved etching consistency and reduced the need for frequent solution replacements.
Future Directions
The future of electrochemical regeneration lies in continued research and development to overcome existing challenges and further enhance the process. Key areas of focus include:
- Material Innovation:Developing new electrode materials with higher efficiency and durability.
- Process Optimization:Optimizing process parameters to reduce energy consumption and improve regeneration efficiency.
- Integrated Solutions:Integrating electrochemical regeneration with other waste management techniques to create comprehensive and sustainable solutions.
- Automation and AI:Implementing advanced automation and artificial intelligence (AI) to monitor and control the regeneration process, ensuring optimal performance and minimizing human intervention.
Conclusion
Electrochemical regeneration of acid copper chloride etching solutions offers a sustainable and efficient method for recycling spent etching solutions. By addressing the challenges associated with waste management and environmental impact, this process contributes to a cleaner and more efficient production of electronic components. Continued research and development are essential to overcome existing limitations and further enhance the benefits of electrochemical regeneration. As the demand for electronic devices continues to grow, the adoption of such sustainable practices will be crucial for the future of the industry.