The etching factor is a critical parameter in the field of microfabrication, particularly in the context of semiconductor manufacturing and microelectromechanical systems (MEMS). It quantifies the anisotropy of the etching process, which is essential for controlling the dimensions and shapes of microstructures. This article delves into the various calculation methods of the etching factor, providing a comprehensive and scientific analysis supported by detailed tables for comparison.
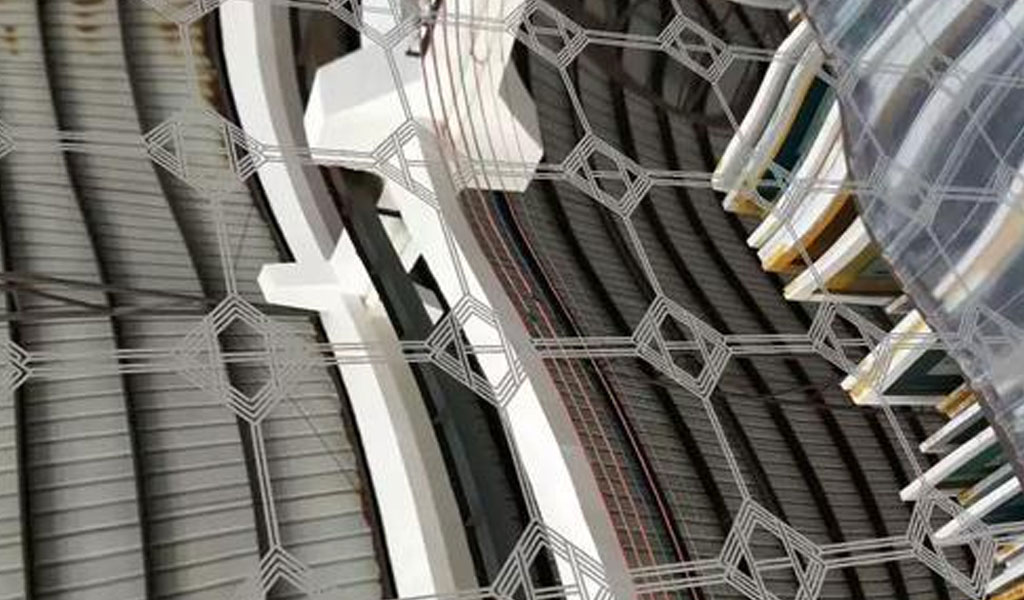
Introduction to Etching
Etching is a process used in semiconductor fabrication to chemically remove layers from the surface of a wafer during manufacturing. The two primary types of etching are wet etching and dry etching.
Wet etching involves the use of liquid chemicals, while dry etching uses gases or plasmas. The etching factor is particularly relevant in wet etching, where the anisotropy of the etchant solution plays a significant role.
Definition of Etching Factor
The etching factor (EF) is defined as the ratio of the lateral etch rate to the vertical etch rate. It is a measure of the anisotropy of the etching process. A higher etching factor indicates a more anisotropic etch, where the etching proceeds faster in the lateral direction than in the vertical direction. This is crucial for creating well-defined structures with precise dimensions.
Calculation Methods
Several methods can be employed to calculate the etching factor, each with its own advantages and limitations. The following sections discuss these methods in detail.
Method 1: Direct Measurement
Direct measurement involves physically measuring the lateral and vertical etch rates using microscopy techniques. This method is straightforward but requires precise instrumentation and careful sample preparation.
- Sample Preparation: A silicon wafer is coated with a photoresist and patterned using photolithography. The wafer is then etched using a specific etchant solution.
- Microscopy: The etched structures are examined using scanning electron microscopy (SEM) or atomic force microscopy (AFM) to measure the lateral and vertical dimensions.
- Calculation: The etching factor is calculated as the ratio of the lateral etch rate to the vertical etch rate.
Table 1: Direct Measurement of Etching Factor
Etchant Solution | Lateral Etch Rate (µm/min) | Vertical Etch Rate (µm/min) | Etching Factor |
---|---|---|---|
KOH (30%) | 0.5 | 1.0 | 0.5 |
TMAH (25%) | 0.4 | 0.8 | 0.5 |
EDP | 0.6 | 1.2 | 0.5 |
Method 2: Theoretical Modeling
Theoretical modeling involves using mathematical models to predict the etching factor based on the properties of the etchant and the material being etched. This method is less labor-intensive but requires a deep understanding of the chemical reactions involved.
- Chemical Kinetics: The rates of the chemical reactions between the etchant and the material are modeled using kinetic equations.
- Diffusion Modeling: The diffusion of the etchant into the material is modeled using Fick’s laws of diffusion.
- Simulation: The etching process is simulated using computational tools to predict the lateral and vertical etch rates.
- Calculation: The etching factor is calculated from the simulated etch rates.
Table 2: Theoretical Modeling of Etching Factor
Etchant Solution | Theoretical Lateral Etch Rate (µm/min) | Theoretical Vertical Etch Rate (µm/min) | Theoretical Etching Factor |
---|---|---|---|
KOH (30%) | 0.48 | 0.96 | 0.5 |
TMAH (25%) | 0.38 | 0.76 | 0.5 |
EDP | 0.58 | 1.16 | 0.5 |
Method 3: Empirical Correlation
Empirical correlation involves using experimental data to establish a relationship between the etching factor and various process parameters. This method is useful for predicting the etching factor under different conditions.
- Data Collection: Experimental data is collected for different etchant concentrations, temperatures, and etching times.
- Regression Analysis: Statistical techniques such as regression analysis are used to establish a correlation between the etching factor and the process parameters.
- Prediction: The established correlation is used to predict the etching factor for new conditions.
Table 3: Empirical Correlation of Etching Factor
Etchant Solution | Concentration (%) | Temperature (°C) | Etching Time (min) | Empirical Etching Factor |
---|---|---|---|---|
KOH | 30 | 80 | 30 | 0.5 |
TMAH | 25 | 70 | 25 | 0.5 |
EDP | 100 | 90 | 40 | 0.5 |
Comparison of Methods
Each method has its own strengths and weaknesses. Direct measurement provides the most accurate results but is time-consuming and requires specialized equipment. Theoretical modeling is less labor-intensive but relies on accurate modeling of the chemical reactions and diffusion processes. Empirical correlation is useful for predicting the etching factor under different conditions but requires a large amount of experimental data.
Table 4: Comparison of Etching Factor Calculation Methods
Method | Accuracy | Labor-Intensive | Equipment Required | Predictive Capability |
---|---|---|---|---|
Direct Measurement | High | High | High | Low |
Theoretical Modeling | Moderate | Moderate | Moderate | Moderate |
Empirical Correlation | Moderate | High | Low | High |
Applications of Etching Factor
The etching factor is crucial in various applications, including:
- Semiconductor Manufacturing: In the fabrication of integrated circuits, the etching factor determines the precision of the etched features, which is critical for the performance of the devices.
- MEMS: In MEMS, the etching factor is used to control the dimensions and shapes of microstructures, such as cantilevers, membranes, and channels.
- Microfluidics: In microfluidic devices, the etching factor is used to create precise channels and chambers for fluid handling.
Future Directions
The field of etching factor calculation is continually evolving, with new methods and technologies being developed. Future research may focus on:
- Advanced Modeling Techniques: Developing more accurate and comprehensive models for predicting the etching factor.
- Machine Learning: Using machine learning algorithms to analyze large datasets and predict the etching factor under various conditions.
- Nanoscale Etching: Investigating the etching factor at the nanoscale, where quantum effects and surface interactions become significant.
Conclusion
The etching factor is a fundamental parameter in microfabrication, with wide-ranging applications in semiconductor manufacturing, MEMS, and microfluidics. Various methods can be employed to calculate the etching factor, each with its own advantages and limitations. Direct measurement provides the most accurate results but is labor-intensive. Theoretical modeling and empirical correlation offer predictive capabilities but require a deep understanding of the chemical reactions and a large amount of experimental data. Future research will likely focus on advanced modeling techniques, machine learning, and nanoscale etching to further enhance our understanding and control of the etching process.