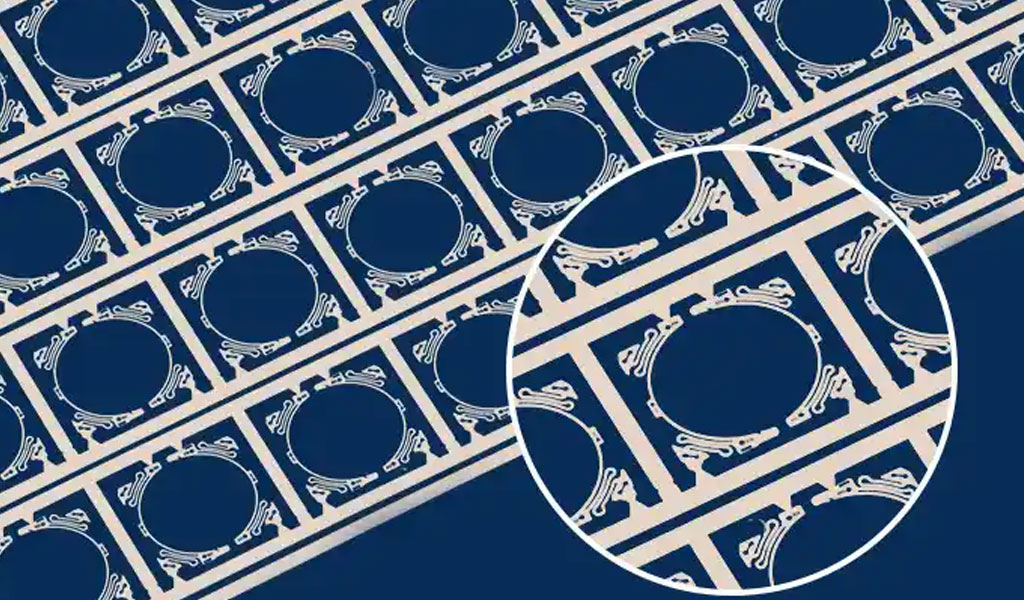
Etching product numbers on products and parts is a widely utilized industrial practice aimed at ensuring traceability, authenticity, and efficient management of manufactured goods.
This process involves the permanent marking of alphanumeric codes, serial numbers, or other identification symbols onto the surface of components using various techniques. These markings serve as critical tools in industries such as manufacturing, aerospace, automotive, electronics, and medical device production, where precision and accountability are paramount.
The practice dates back to early industrial efforts to track goods but has evolved significantly with advancements in technology, offering a range of methods suited to different materials and applications.
The importance of etching product numbers lies in its ability to provide a unique identifier for each item, enabling manufacturers, distributors, and end-users to monitor the lifecycle of a product from production to disposal. This article explores the history, methods, applications, advantages, and challenges of etching product numbers, delving into the scientific principles behind each technique and comparing their efficacy across diverse scenarios. By examining the intricacies of this process, we aim to provide a comprehensive resource for understanding its role in modern industry.
Historical Background of Product Number Etching
The concept of marking products for identification purposes can be traced back to ancient civilizations, where artisans engraved symbols or initials onto tools, pottery, and weapons to signify ownership or origin. In medieval Europe, guilds adopted similar practices to authenticate goods and prevent counterfeiting. However, the systematic etching of product numbers as we know it today emerged during the Industrial Revolution in the 18th and 19th centuries. With the advent of mass production, manufacturers needed a reliable way to distinguish between identical items produced in large quantities.
Early methods of marking involved manual engraving or stamping, which were labor-intensive and prone to human error. The introduction of chemical etching in the 19th century marked a significant advancement, allowing for more precise and consistent markings on metal surfaces. By the 20th century, the development of electrical and mechanical etching tools further refined the process, paving the way for automation. The rise of laser technology in the late 20th century revolutionized the field, offering unparalleled accuracy and versatility across a wide range of materials, including metals, plastics, and ceramics.
Today, etching product numbers is a cornerstone of industrial standardization, governed by international protocols such as ISO 9001 and MIL-STD-130, which dictate requirements for identification marking in quality management and defense sectors, respectively. This historical evolution reflects the growing complexity of global supply chains and the increasing demand for precision in manufacturing.
Scientific Principles of Etching Techniques
Etching product numbers relies on the controlled removal or alteration of a material’s surface to create legible, permanent markings. The underlying science varies depending on the technique employed, but all methods aim to achieve durability, readability, and compatibility with the substrate. Below, we explore the primary etching techniques and their scientific foundations.
Chemical Etching
Chemical etching, also known as wet etching, involves the use of corrosive substances to selectively remove material from a surface. The process begins with the application of a resist—a protective layer, often made of wax, vinyl, or photoresist—that covers the areas not intended for etching. An acid or alkaline solution, such as ferric chloride for metals or hydrofluoric acid for glass, is then applied, dissolving the exposed material to form the desired pattern.
The chemical reaction is governed by principles of oxidation and reduction. For example, when etching steel with ferric chloride (FeCl₃), the iron (Fe) in the steel oxidizes to form iron chloride (FeCl₂), while the ferric ions are reduced. The reaction can be represented as:
Fe+2FeCl3→3FeCl2
This method is highly effective for metals like stainless steel, copper, and aluminum but requires careful control of etchant concentration, temperature, and exposure time to avoid over-etching or under-etching.
Electrochemical Etching
Electrochemical etching, or electrolytic etching, enhances chemical etching by incorporating an electric current. A stencil or mask defines the marking area, and the workpiece acts as the anode in an electrolytic cell, while a cathode completes the circuit. An electrolyte solution facilitates ion transfer, accelerating material removal at the anode through anodic dissolution.
The process leverages Faraday’s laws of electrolysis, where the amount of material removed is proportional to the electric charge passed through the system. For a metal like aluminum, the reaction might involve the formation of aluminum ions:
Al→Al3++3e−
Electrochemical etching offers greater precision than chemical etching and is widely used for marking conductive materials, such as titanium and steel, in aerospace and medical applications.
Laser Etching
Laser etching employs a focused beam of light to vaporize or alter the surface of a material. The process operates on the principle of photothermal or photochemical ablation, depending on the laser type and material. For instance, a CO₂ laser (wavelength 10.6 μm) heats the surface to evaporate material, while a fiber laser (wavelength ~1 μm) can induce localized melting or color changes in metals.
The energy delivered by the laser is calculated as:
E=h⋅f
where E E E is energy, h h h is Planck’s constant, and f f f is the frequency of the laser light. Laser etching is highly versatile, applicable to metals, plastics, ceramics, and even organic materials, with minimal thermal damage to surrounding areas due to its precision.
Mechanical Etching
Mechanical etching, or engraving, involves physically removing material using tools like diamond-tipped styluses, rotary cutters, or abrasive blasting. The process relies on mechanical force and friction to displace material, governed by principles of contact mechanics and tribology. For example, the depth of an engraving depends on the hardness of the tool and substrate, as well as the applied pressure.
This method is durable and cost-effective for softer materials like plastics or wood but less precise than laser or chemical techniques, making it suitable for larger, less intricate markings.
Applications of Etching Product Numbers
The etching of product numbers finds applications across a multitude of industries, each with specific requirements for marking durability, size, and legibility. Below are some key sectors where this practice is indispensable.
Manufacturing and Quality Control
In manufacturing, etched product numbers enable tracking of components through assembly lines, ensuring that defective parts can be traced back to their source. For example, in the automotive industry, engine blocks and transmission gears bear serial numbers that link them to production batches, facilitating recalls or warranty claims.
Aerospace and Defense
Aerospace components, such as turbine blades and fuselage panels, require markings that withstand extreme temperatures and pressures. Laser and electrochemical etching are preferred here, meeting standards like MIL-STD-130, which mandates permanent identification for military equipment.
Electronics
In electronics, tiny components like circuit boards and microchips are etched with codes to denote model numbers or batch information. Laser etching is often used due to its ability to produce microscopic markings without compromising functionality.
Medical Devices
Medical implants, such as pacemakers and prosthetics, must carry etched identifiers for patient safety and regulatory compliance. Biocompatible etching methods, such as laser marking, ensure that markings do not degrade in the body.
Consumer Goods
From jewelry to firearms, consumer products often feature etched numbers for branding, authentication, or legal purposes. Mechanical etching remains common in these applications for its simplicity and cost-effectiveness.
Advantages of Etching Product Numbers
Etching offers several benefits that make it a preferred method for product identification:
- Permanence: Unlike labels or ink, etched markings resist wear, corrosion, and environmental exposure.
- Precision: Modern techniques like laser etching allow for intricate, legible designs on small surfaces.
- Versatility: Etching can be applied to diverse materials, from metals to polymers.
- Traceability: Unique identifiers enhance supply chain management and regulatory compliance.
- Tamper Resistance: Etched marks are difficult to alter, reducing the risk of counterfeiting.
Challenges and Limitations
Despite its advantages, etching product numbers presents challenges that must be addressed:
- Cost: Advanced methods like laser etching require significant investment in equipment.
- Material Compatibility: Not all techniques suit every substrate; for example, chemical etching may damage delicate plastics.
- Skill Requirement: Precision etching demands trained operators and careful process control.
- Environmental Impact: Chemical etching generates hazardous waste, necessitating proper disposal measures.
- Legibility Over Time: Wear or corrosion can obscure markings on heavily used items.
Comparative Analysis of Etching Techniques
To provide a clearer understanding of the strengths and weaknesses of each etching method, the following table compares key parameters:
Technique | Material Compatibility | Precision | Speed | Cost | Durability | Environmental Impact |
---|---|---|---|---|---|---|
Chemical Etching | Metals, Glass | Moderate | Slow | Low | High | High (chemical waste) |
Electrochemical | Conductive Metals | High | Moderate | Moderate | High | Moderate |
Laser Etching | Metals, Plastics, Ceramics | Very High | Fast | High | Very High | Low |
Mechanical Etching | Metals, Plastics, Wood | Low | Moderate | Low | Moderate | Low |
Detailed Comparison Notes
- Chemical Etching: Ideal for batch processing of metal parts but limited by slow throughput and waste management needs.
- Electrochemical Etching: Balances cost and precision, making it suitable for industrial applications requiring conductive substrates.
- Laser Etching: Offers unmatched flexibility and speed, though initial setup costs can be prohibitive for small-scale operations.
- Mechanical Etching: Best for low-budget projects but lacks the finesse needed for intricate designs or small components.
Technological Advancements in Etching
Recent innovations have expanded the capabilities of etching product numbers. For instance, the integration of computer numerical control (CNC) systems with laser and mechanical etching allows for automated, repeatable patterns. Additionally, the development of ultraviolet (UV) lasers has enabled marking on heat-sensitive materials without thermal distortion. In chemical etching, eco-friendly etchants, such as citric acid-based solutions, are reducing environmental footprints.
The rise of Industry 4.0 has also introduced smart etching systems, where Internet of Things (IoT) devices monitor etching parameters in real-time, optimizing quality and reducing errors. These advancements signal a future where etching becomes even more efficient and sustainable.
Regulatory and Standardization Frameworks
Etching product numbers is subject to strict regulations, particularly in safety-critical industries. The International Organization for Standardization (ISO) provides guidelines under ISO 9001 for quality management, requiring traceable identification of products. In the United States, the Department of Defense enforces MIL-STD-130, specifying marking methods and durability criteria for military assets. Similarly, the Food and Drug Administration (FDA) mandates unique device identifiers (UDIs) for medical equipment, often achieved through etching.
These standards ensure consistency and reliability but also impose constraints on manufacturers, who must balance compliance with cost and production timelines.
Case Studies of Etching in Industry
Aerospace: Boeing 737 Components
Boeing employs laser etching to mark serial numbers on 737 landing gear components. The process ensures traceability during maintenance, with markings enduring harsh conditions like vibration and temperature extremes.
Automotive: Ford Engine Blocks
Ford uses electrochemical etching to engrave batch numbers on engine blocks, allowing rapid identification of faulty units during recalls. The method’s moderate cost and high durability suit high-volume production.
Electronics: Intel Microchips
Intel relies on laser etching to inscribe microscopic codes on microprocessors, enabling precise tracking through supply chains and aiding in counterfeit prevention.
Conclusion
The future of etching lies in sustainability and automation. Researchers are exploring biodegradable etchants and energy-efficient lasers to minimize environmental impact. Meanwhile, artificial intelligence (AI) is being integrated into etching systems to predict optimal parameters based on material properties, reducing trial-and-error. Additionally, the adoption of blockchain technology may link etched numbers to digital ledgers, enhancing traceability and security.
Etching product numbers on products and parts is a vital practice that underpins modern industry, blending historical craftsmanship with cutting-edge technology. From chemical reactions to laser precision, the science of etching offers a spectrum of methods tailored to diverse needs. While challenges like cost and environmental concerns persist, ongoing innovations promise to refine the process further. As industries evolve, etching will remain a cornerstone of identification, ensuring that every product carries its unique story etched into its surface.