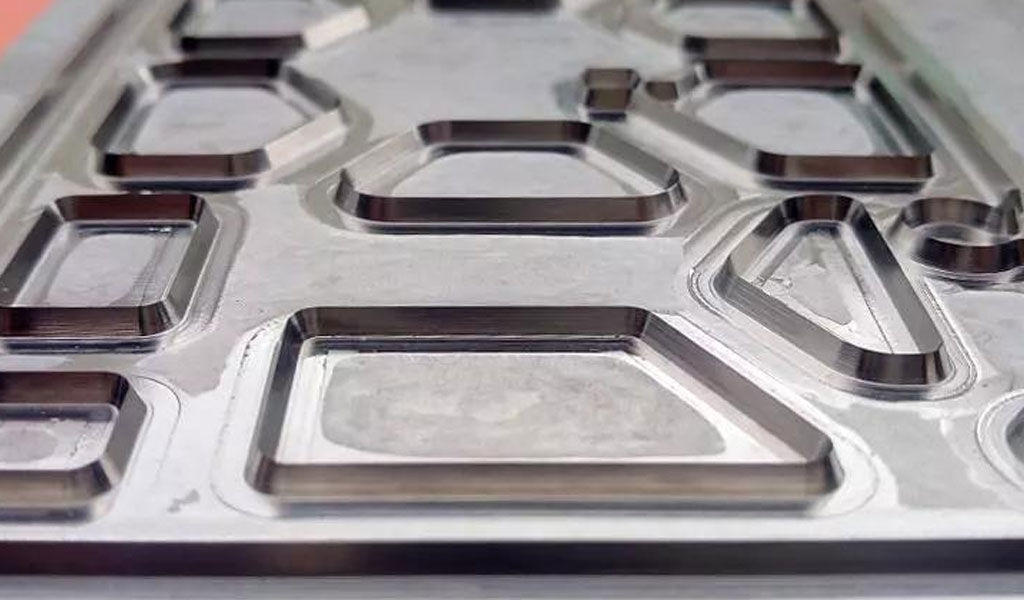
In Dongguan in August, under the scorching high temperature, a refreshing shower can relieve a lot of summer irritability. The night before, Famer Li had just returned to Dongguan from visiting a client. Since the beginning of this year, his work has become even busier.
In addition to receiving PEM electrolyzer customers at home and abroad, at other times he is like a migratory bird, flying to several major domestic hydrogen energy demonstration cities for customer return visits and product research. To prepare for the next mass production delivery of titanium electrode plates.
In a traditional OEM manufacturing industry such as etching, Famer Li and his Dongguan Be-Cu Technology Co., Ltd. have stepped into the spotlight of the green hydrogen industry and customized titanium plates for PEM electrolyzer companies.
I was ignorant of the hydrogen energy industry when I started “practicing” with customers in 2018. Now, the mass-produced titanium plates have been widely praised by customers. In the past five years, Famer Li and Be-Cu led by him have witnessed the process of the hydrogen energy industry from silence to rise. The “old craft” of etching has begun to shine in the new industry of green hydrogen.
Why Choose Etching Process For Titanium Plate Manufacturing?
Metal etching, also known as photochemical metal etching, refers to removing the protective film from the area to be metal etched through exposure plate making and development. During metal etching, it is exposed to chemical solutions to achieve the effect of dissolving corrosion and forming concave and convex or hollow shapes. Effect.
As an extremely ancient manufacturing technology, its origins can be traced back to the 14th century from recorded data. The development of modern metal etching benefited from the continuous advancement of photosensitive anti-corrosion technology including photosensitive materials and photosensitive light sources after the 20th century, and caused Iterations of photosensitive devices. After continuous improvement and development of process equipment, the metal etching process can be widely used in the manufacturing of precision metal products for electronic wafer parts in the aviation, machinery, and chemical industries. Especially in the semiconductor manufacturing process, metal etching is an indispensable technology.
Applying metal etching process to titanium bipolar plate manufacturing is also an accidental attempt for Be-Cu TECH.
https://metal-etch.com/
“We had no idea what the hydrogen energy industry was doing at the beginning and how big the application market would be in the future.” Famer Li, general manager of Be-Cu TECH, said that when participating in an industry exhibition exchange in 2018, he was told by a fuel cell company Senior executives asked whether etching technology could be used to create metal bipolar plates with special flow channels. This was when they really entered the field of hydrogen energy.
However, when Famer Li actually entered the metal bipolar plate manufacturing industry, he discovered that everything was not as simple as imagined. In the following years, the manufacturing of metal bipolar plates for fuel cells has gradually transitioned from the initial CNC machining process and etching process to the molding process. In particular, the addition of the molding process has enabled large-scale and efficient manufacturing of metal bipolar plates. became possible and widely accepted by the industry.
Hard work pays off. When most of the fuel cell customers he had previously contacted began to turn to molding, Famer Li had already done supporting development work for them for many years, especially the solution composition ratio for metal plate flow channel molding, forming his own A set of experience and accumulation, which also laid a solid foundation for its transformation into specialized titanium bipolar plate etching.
Compared with graphite, titanium has excellent corrosion resistance, low initial resistivity, good mechanical strength and light weight. It is currently the best plate material for PEMWE. The surface of titanium is usually plated with precious metals or platinum group metals. To meet durability and performance requirements in high pressure and oxidizing environments.
The excellent performance also makes titanium bipolar plates encounter difficulties in the manufacturing process. Usually, both sides of titanium bipolar plates contain extremely complex features. These features are sometimes beyond the capabilities of stamping and machining, but are easily achieved using an etching process that can also produce different features on both sides of the plate, saving significant manufacturing costs.
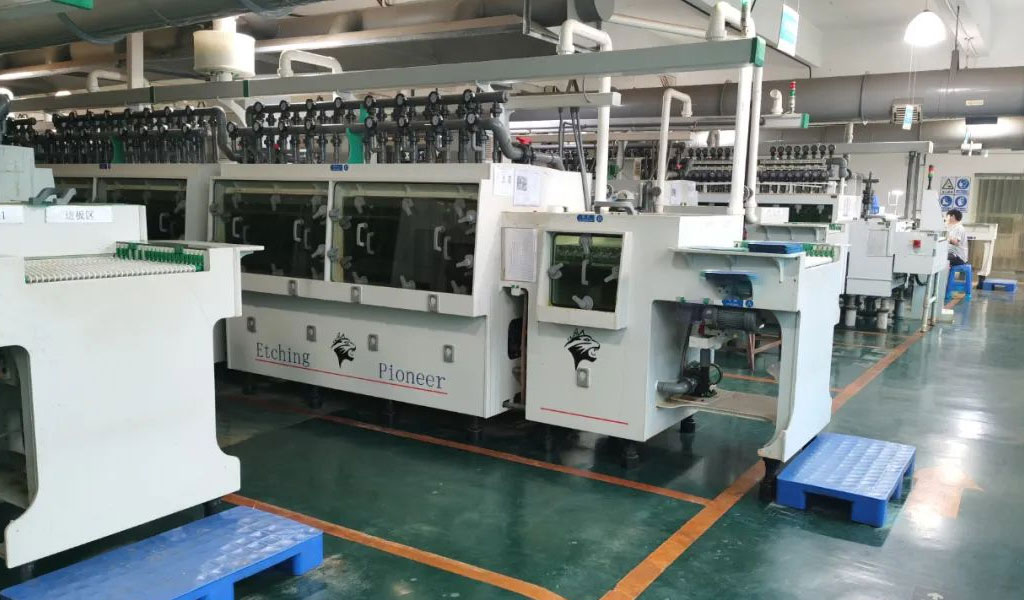
In the preparation process of PEM electrolytic cells, the manufacturing of electrode plates is particularly important. At present, the manufacturing of PEM electrolytic cell electrode plates mainly includes three different process routes: stamping, etching and machining. The etching process has a significant impact on the production cycle, cost and material. Each has its unique advantages in terms of adaptability.
There is a big difference between etching and stamping in terms of working principle. Stamping actually compresses metal to create channels, while etching removes material to create channels. The characteristics of this etching process retain the characteristics of the material to the greatest extent. The parts are free of burrs, stress-free, clean contours, no heat-affected zones, and the shading is consistent with the original material.
On the other hand, in the early stages of the development of the hydrogen energy industry, the industry has not yet formed standardized products. The titanium bipolar plate products of different PEM electrolyzer companies are very different from size to flow channel design. If the stamping process is used, the product of a single model will be different. The mold opening cost is unacceptable.
In this context, flexible production can be achieved with high flexibility, which can not only meet the needs of mass production, but also achieve rapid delivery of small batch products. PEM titanium plate etching has become a very cost-effective choice.
Be-Cu’s Unique Titanium Plate Etching Technology
With the rise of the green hydrogen concept and the explosion of orders for water electrolysis hydrogen production equipment, PEM electrolysis hydrogen production has gradually entered the commercial demonstration application stage. In the first half of 2023, Be-Cu TECH has received more orders for titanium plate etching for PEM electrolyzers than all of last year. To this end, Be-Cu TECH has also formulated a production line expansion plan.
“With the improvement of product qualification rate and consistency, upstream customers’ demand for Be-Cu TECH titanium plate etching is also growing rapidly.” Famer Li said that customers have high recognition of the company’s etching process, and Be-Cu TECH The expansion of the production line has been completed in half a year. With the commissioning of two new production lines, the company’s titanium plate etching capacity has now reached 30,000 pieces/month. In the future, the company will flexibly skip frames according to changes in market demand.
Be-Cu TECH can bring new tricks to the traditional etching process in the hydrogen energy industry by relying on excellent technology and continuous research and practice. Through repeated improvements in yield, Be-Cu TECH began to use PEM titanium bipolar plates. Leading the etching industry.
At this stage, Be-Cu TECH has 20 years of rich experience in high-end metal etching production and independent research and development capabilities. It has passed ISO9001 quality system, IATF16949, and national high-tech enterprise certification. In the field of metal etching, Be-Cu TECH has applied for a number of products. technology patents.
In order to improve the consistency and reliability of the product, in the first half of this year, Be-Cu TECH established its own hydrogen energy testing laboratory and purchased related testing equipment such as major appearance testing, model comparison, and data analysis. Be-Cu TECH also Become the first metal etching company in the industry to establish a hydrogen energy product laboratory.
“The company started with contact metal bipolar plate etching. Over the past five years, through multiple iterations of technology and processes, it has been able to stably meet customer needs.” Famer Li said that the current yield rate of Be-Cu TECH in titanium plate etching has been Reaching more than 99%, far exceeding the industry yield level of about 70% during the same period.
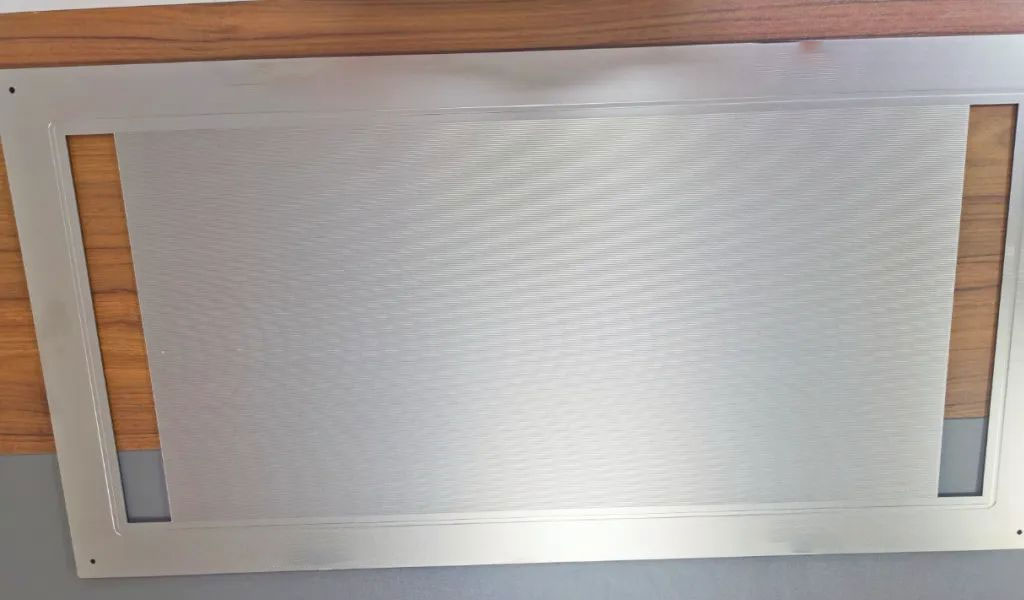
Up to now, the etching solution configuration in the PEM titanium plate has been upgraded to the third generation, making the edge of the flow channel body smoother. With the continuous improvement of technology, Be-Cu TECH has the production etching manufacturing capability of different depths on the same surface of the plate design. , currently capable of eight steps of mass production.
“During the product development process, the company has been working closely with upstream customers, starting from customer needs, formulating specific process technologies and directional output plates, so as to deliver products that satisfy customers.”Famer Li said that Be-Cu TECH focuses on metals The only track for etching bipolar plates and PEM titanium plates enables the entire process to be completed in the factory, and continues to provide customers with one-stop comprehensive solutions.