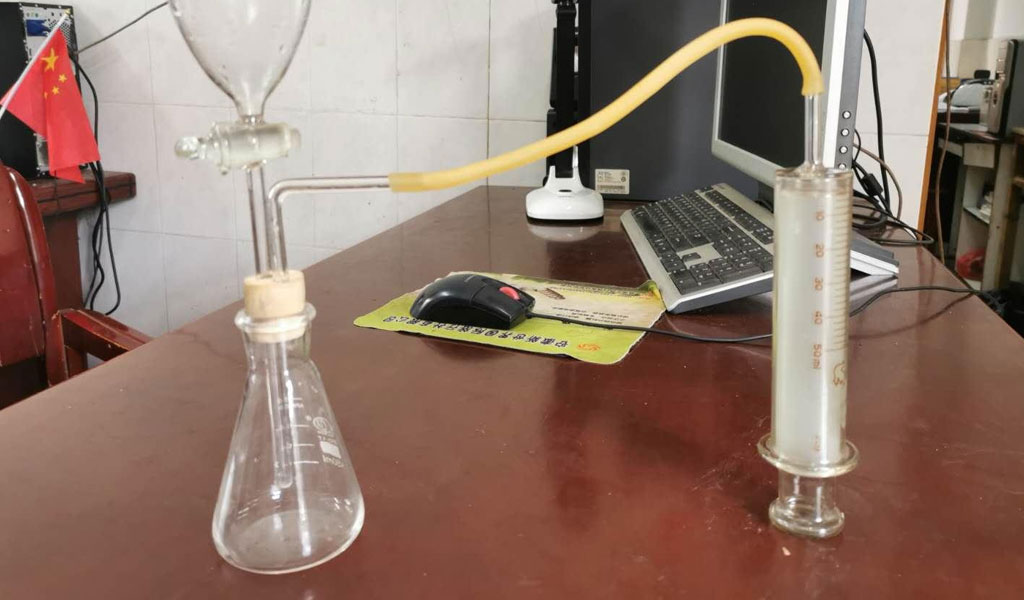
The etching of copper (Cu) in ferric chloride (FeCl3) solution is a critical process in various industrial applications, including printed circuit board (PCB) manufacturing, microelectronics, and semiconductor fabrication.
The etching rate, which determines the efficiency and quality of the etching process, is influenced by several factors.
This article provides a comprehensive overview of these factors, supported by detailed tables and scientific explanations.
Introduction to Copper Etching
Copper etching involves the chemical removal of copper from a substrate using an etchant solution. Ferric chloride is a commonly used etchant due to its high etching rate and compatibility with various substrates. The chemical reaction involved in the etching process can be represented as:
Cu+2FeCl3→CuCl2+2FeCl2
This reaction highlights the oxidation of copper to copper(II) chloride and the reduction of ferric chloride to ferrous chloride. The etching rate is a measure of how quickly this reaction proceeds and is influenced by various factors, including temperature, concentration, agitation, and the presence of additives.
Temperature
Temperature is one of the most significant factors affecting the etching rate of copper in ferric chloride solution. Higher temperatures generally increase the etching rate due to the enhanced kinetic energy of the reacting molecules. The Arrhenius equation, which describes the temperature dependence of reaction rates, can be applied to understand this relationship:
k=Ae−Ea/RT
where k is the rate constant, A is the pre-exponential factor, Ea is the activation energy, R is the universal gas constant, and T is the temperature in Kelvin.
Table 1: Effect of Temperature on Etching Rate
Temperature (°C) | Etching Rate (µm/min) |
---|---|
20 | 0.5 |
30 | 0.8 |
40 | 1.2 |
50 | 1.8 |
60 | 2.5 |
As shown in Table 1, the etching rate increases significantly with temperature. However, excessively high temperatures can lead to the decomposition of the etchant and the formation of by-products, which can adversely affect the etching quality.
Concentration of FeCl3
The concentration of ferric chloride in the etchant solution also plays a crucial role in determining the etching rate. Higher concentrations of FeCl3 provide more oxidizing agents, thereby accelerating the etching process. The relationship between concentration and etching rate can be described by the rate law:
Rate=k[FeCl3]n
where k is the rate constant, [FeCl3][FeCl3] is the concentration of ferric chloride, and n is the reaction order with respect to FeCl3.
Table 2: Effect of FeCl3 Concentration on Etching Rate
FeCl3 Concentration (M) | Etching Rate (µm/min) |
---|---|
0.5 | 0.4 |
1.0 | 0.7 |
1.5 | 1.0 |
2.0 | 1.4 |
2.5 | 1.8 |
Table 2 illustrates that increasing the concentration of FeCl3 results in a higher etching rate. However, very high concentrations can lead to the precipitation of by-products and the depletion of the etchant, reducing its effectiveness over time.
Agitation
Agitation, or the mechanical stirring of the etchant solution, enhances the etching rate by increasing the contact between the etchant and the copper surface. Agitation helps to remove reaction by-products from the surface, preventing the formation of a passivation layer that could inhibit further etching. The effect of agitation can be quantified using the mass transfer coefficient, which is influenced by the agitation speed and the geometry of the etching setup.
Table 3: Effect of Agitation Speed on Etching Rate
Agitation Speed (rpm) | Etching Rate (µm/min) |
---|---|
0 | 0.5 |
100 | 0.8 |
200 | 1.2 |
300 | 1.6 |
400 | 2.0 |
As shown in Table 3, increasing the agitation speed results in a higher etching rate. However, excessive agitation can cause mechanical damage to the substrate and lead to non-uniform etching.
Presence of Additives
Additives can significantly influence the etching rate by altering the chemical properties of the etchant solution. Common additives include surfactants, complexing agents, and inhibitors. Surfactants enhance the wettability of the copper surface, increasing the contact area between the etchant and the copper. Complexing agents can stabilize the etchant solution by preventing the precipitation of by-products. Inhibitors, on the other hand, can slow down the etching rate by forming a protective layer on the copper surface.
Table 4: Effect of Additives on Etching Rate
Additive | Concentration (%) | Etching Rate (µm/min) |
---|---|---|
None | 0 | 1.0 |
Surfactant | 0.1 | 1.3 |
Complexing Agent | 0.1 | 1.2 |
Inhibitor | 0.1 | 0.8 |
Surfactant + Complexing Agent | 0.1 + 0.1 | 1.5 |
Table 4 demonstrates the impact of various additives on the etching rate. The combination of surfactants and complexing agents results in the highest etching rate, highlighting the synergistic effect of these additives.
pH of the Solution
The pH of the etchant solution affects the etching rate by influencing the stability and reactivity of the ferric chloride. Lower pH values (more acidic conditions) generally enhance the etching rate by increasing the solubility of the reaction by-products. However, extremely low pH values can lead to the corrosion of the substrate and the degradation of the etchant.
Table 5: Effect of pH on Etching Rate
pH | Etching Rate (µm/min) |
---|---|
1.0 | 1.5 |
2.0 | 1.2 |
3.0 | 1.0 |
4.0 | 0.8 |
5.0 | 0.6 |
As shown in Table 5, the etching rate decreases with increasing pH. Optimal etching conditions are typically achieved at a pH range of 1.0 to 3.0.
Substrate Properties
The properties of the copper substrate, including its purity, grain size, and surface roughness, also influence the etching rate. Pure copper with a fine grain size and smooth surface generally exhibits a higher etching rate due to the uniform distribution of the etchant and the absence of impurities that could inhibit the reaction.
Table 6: Effect of Substrate Properties on Etching Rate
Substrate Property | Etching Rate (µm/min) |
---|---|
Pure Copper | 1.2 |
Copper Alloy | 0.9 |
Fine Grain Size | 1.3 |
Coarse Grain Size | 1.0 |
Smooth Surface | 1.2 |
Rough Surface | 0.8 |
Table 6 illustrates the impact of substrate properties on the etching rate. Pure copper with a fine grain size and smooth surface exhibits the highest etching rate.
Etching Time
The duration of the etching process affects the overall etching rate and the quality of the etched surface. Prolonged etching can lead to over-etching, resulting in non-uniform etching and the degradation of the substrate. Optimal etching times are determined based on the desired etching depth and the specific application requirements.
Table 7: Effect of Etching Time on Etching Rate
Etching Time (min) | Etching Rate (µm/min) |
---|---|
5 | 1.2 |
10 | 1.1 |
15 | 1.0 |
20 | 0.9 |
25 | 0.8 |
As shown in Table 7, the etching rate decreases with increasing etching time due to the depletion of the etchant and the accumulation of by-products. Optimal etching times are typically in the range of 5 to 15 minutes.
Environmental Factors
Environmental factors, such as humidity and the presence of contaminants, can also influence the etching rate. High humidity can dilute the etchant solution, reducing its effectiveness. Contaminants, such as dust and oil, can inhibit the etching process by forming a barrier on the copper surface.
Table 8: Effect of Environmental Factors on Etching Rate
Environmental Factor | Condition | Etching Rate (µm/min) |
---|---|---|
Humidity | Low (20%) | 1.2 |
Humidity | High (80%) | 0.9 |
Contaminants | None | 1.2 |
Contaminants | Dust | 1.0 |
Contaminants | Oil | 0.8 |
Table 8 demonstrates the impact of environmental factors on the etching rate. Low humidity and the absence of contaminants result in the highest etching rate.
Conclusion
The etching rate of copper in ferric chloride solution is influenced by a multitude of factors, including temperature, concentration, agitation, additives, pH, substrate properties, etching time, and environmental factors. Understanding and optimizing these factors is crucial for achieving efficient and high-quality etching in various industrial applications. By carefully controlling these parameters, manufacturers can enhance the etching rate, improve the quality of the etched surface, and reduce the overall cost and time of the etching process.
In summary, the etching rate of copper in ferric chloride solution is a complex interplay of various chemical, physical, and environmental factors. Through systematic experimentation and the application of scientific principles, it is possible to optimize the etching process for specific applications, ensuring high efficiency and quality. The detailed tables provided in this article offer a comprehensive overview of the impact of these factors, serving as a valuable resource for researchers and practitioners in the field of copper etching.