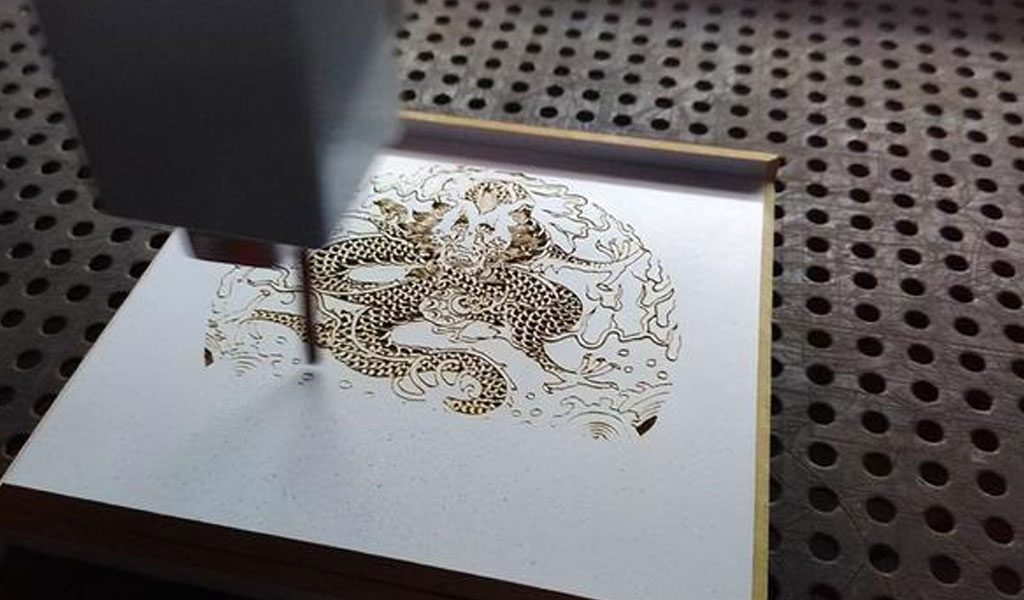
Flatbed laser etching is a sophisticated manufacturing process that employs a laser beam to create precise, permanent markings, patterns, or microstructures on a variety of materials. Utilizing a flatbed configuration, this technique allows for the processing of large, flat substrates with high accuracy and repeatability, making it a cornerstone of modern industrial, scientific, and artistic applications.
Unlike traditional mechanical or chemical etching methods, flatbed laser etching is a non-contact process, relying on the controlled application of laser energy to alter the surface properties of a material—typically through melting, ablation, or vaporization—without the need for physical tools or corrosive agents.
This article explores the principles, technologies, applications, and advancements of flatbed laser etching, providing a detailed examination of its mechanisms, equipment, and comparative advantages.
Principles of Flatbed Laser Etching
Flatbed laser etching operates on the fundamental principle of laser-material interaction, where a focused beam of coherent light delivers energy to a substrate, inducing localized physical or chemical changes. The process begins with the generation of a laser beam, typically from a gas, solid-state, or fiber laser source, which is directed through a series of optical components—mirrors, lenses, and galvanometric scanners—onto the surface of a workpiece positioned on a flatbed platform. The flatbed design distinguishes this method from other laser systems, such as rotary or cylindrical setups, by accommodating large, planar materials with minimal distortion or misalignment.
The interaction between the laser and the material depends on several parameters, including wavelength, power, pulse duration, and the material’s optical and thermal properties. For instance, when the laser beam strikes a metallic surface, it may heat and melt a thin micro-layer, causing it to expand and cool rapidly, leaving a raised mark. In contrast, on organic materials like wood or polymers, the laser may vaporize or ablate the surface, creating a shallow depression. The precision of flatbed laser etching stems from the ability to control these parameters with high fidelity, often achieving resolutions down to micrometers.
The flatbed configuration enhances this precision by providing a stable, horizontal working plane. Unlike handheld or vertical laser systems, the flatbed ensures uniform beam delivery across the entire surface, minimizing variations due to gravitational effects or substrate flexing. This setup is particularly advantageous for processing large sheets of metal, glass, or plastic, where consistency across a wide area is critical.
Physics of Laser-Material Interaction
The physics underlying flatbed laser etching involves both thermal and photochemical processes. When a laser beam interacts with a material, its energy is absorbed, converted into heat, and dissipated according to the material’s thermal conductivity and specific heat capacity. For metals, this often results in a localized melting and recrystallization process, producing a contrasting mark—typically black, white, or gray—due to changes in surface roughness or oxidation. The equation governing this heat transfer can be expressed as:
Q=m⋅c⋅ΔT
where Q Q Q is the heat energy absorbed, m m m is the mass of the affected material, c c c is the specific heat capacity, and ΔT \Delta T ΔT is the temperature change. In practice, however, the process is more complex, as the laser’s high energy density (often exceeding 10^6 W/cm² for pulsed lasers) can exceed the material’s melting or vaporization threshold within microseconds.
For non-metallic materials, such as glass or ceramics, photochemical effects may dominate, where the laser’s photon energy breaks molecular bonds directly, leading to ablation rather than melting. The threshold fluence (Fth F_th Fth), or energy per unit area required to initiate material removal, varies by material and laser wavelength, typically ranging from 0.1 J/cm² for polymers to over 10 J/cm² for ceramics.
Types of Lasers Used
Flatbed laser etching systems commonly employ three main types of lasers: CO₂, fiber, and diode lasers, each suited to specific materials and applications. CO₂ lasers, operating at a wavelength of 10.6 μm, excel at etching non-metallic materials like wood, glass, and plastics due to their high absorption in organic and dielectric substrates. Fiber lasers, with wavelengths around 1.06 μm, are preferred for metals and some ceramics, offering superior beam quality and efficiency. Diode lasers, typically in the 400–900 nm range, provide a compact, cost-effective option for lightweight etching tasks, though they lack the power of their counterparts.
The choice of laser influences the etching outcome significantly. For example, a CO₂ laser etching glass produces a frosted, white mark by creating micro-cracks, while a fiber laser on stainless steel can yield a high-contrast black mark through controlled oxidation. Pulse duration—continuous wave (CW) versus pulsed—also plays a role, with pulsed lasers (e.g., nanosecond or femtosecond) offering greater precision by minimizing heat diffusion into surrounding areas.
Equipment and System Design
Flatbed laser etching machines consist of several key components integrated into a cohesive system: the laser source, optical delivery system, motion control platform, and control software. The flatbed itself is a rigid, planar surface, often made of aluminum or steel, designed to hold materials securely via clamps, vacuum tables, or magnetic fixtures. This stability is crucial for maintaining focus and alignment over large areas, typically ranging from 300 mm × 300 mm to over 2 m × 3 m in industrial models.
Laser Source and Optics
The laser source generates the beam, which is then shaped and directed by an optical train. A typical setup includes a collimating lens to ensure a parallel beam, followed by a focusing lens to concentrate the energy into a small spot (e.g., 20–100 μm). Galvanometric scanners—mirrors mounted on high-speed motors—steer the beam across the flatbed, allowing rapid patterning without moving the substrate. The focal length of the lens determines the working distance and spot size, with shorter focal lengths yielding smaller, more precise spots but a reduced depth of field.
Motion Control and Flatbed Platform
The flatbed platform may incorporate XY motion stages for large-scale etching, though galvanometric scanning often suffices for smaller areas. High-end systems feature closed-loop feedback mechanisms, using encoders or laser interferometry to achieve positional accuracy within ±10 μm. The flatbed’s surface is typically engineered to resist laser reflection and thermal damage, ensuring longevity and safety.
Software and Control Systems
Modern flatbed laser etching systems rely on sophisticated software to translate digital designs—such as CAD files or raster images—into laser paths. Parameters like power, speed, frequency, and hatch spacing are adjustable, allowing customization for different materials and desired outcomes. For instance, etching a barcode on aluminum might use 80% power at 500 mm/s, while a decorative pattern on wood might require 30% power at 1000 mm/s to avoid charring.
Materials Compatible with Flatbed Laser Etching
Flatbed laser etching is highly versatile, accommodating a wide range of materials due to its non-contact nature and adjustable parameters. The following subsections detail common substrates and their etching characteristics.
Metals
Metals such as stainless steel, aluminum, titanium, and copper are widely etched using flatbed systems, particularly with fiber lasers. The process typically melts a thin surface layer, creating raised marks with depths of 0.001–0.01 inches (25–250 μm). Reflective metals may require pre-treatment with marking compounds to enhance absorption, though high-power fiber lasers can often overcome this limitation.
Non-Metals
Non-metallic materials, including glass, wood, plastics, and ceramics, are well-suited to CO₂ lasers. Glass etching produces a frosted effect through micro-fracturing, while wood etching vaporizes the surface, leaving a darkened mark. Plastics like acrylic and polycarbonate can be etched with high precision, though care must be taken to avoid toxic fume generation (e.g., from PVC).
Composites and Specialty Materials
Composite materials, such as carbon fiber-reinforced polymers (CFRP) or wood-plastic composites (WPC), present unique challenges due to their heterogeneous nature. Flatbed laser etching can selectively target specific layers—e.g., ablating a polymer coating to expose a metal substrate—making it valuable in electronics and aerospace. Specialty materials like sapphire or fused silica require advanced lasers (e.g., femtosecond) for minimal thermal damage.
Applications of Flatbed Laser Etching
Flatbed laser etching finds applications across diverse fields, leveraging its precision, speed, and permanence. Below are key domains where the technology excels.
Industrial Manufacturing
In manufacturing, flatbed laser etching is used for part identification, traceability, and branding. Serial numbers, barcodes, and data matrix codes etched onto metal or plastic components ensure compliance with standards like ISO 9001 or MIL-STD-130. The process’s speed—often completing marks in seconds—supports high-throughput production lines.
Electronics and Semiconductors
The electronics industry employs flatbed laser etching for microfabrication, such as patterning conductive traces on printed circuit boards (PCBs) or etching silicon wafers. The ability to process large substrates (e.g., 300 mm × 300 mm) aligns with semiconductor fabrication needs, while femtosecond lasers enable submicron features with minimal heat-affected zones (HAZ).
Art and Design
Artists and designers utilize flatbed laser etching for custom engravings on wood, glass, and metal. The flatbed’s large working area accommodates oversized pieces, such as furniture panels or architectural glass, enabling intricate patterns or photorealistic images via grayscale techniques.
Scientific Research
In research, flatbed laser etching facilitates the creation of microfluidic devices, optical gratings, and nanostructured surfaces. For instance, selective laser etching (SLE) of glass can produce channels with 1000:1 etch selectivity, advancing lab-on-chip technologies.
Advantages and Limitations
Flatbed laser etching offers numerous benefits but also faces certain constraints, as outlined below.
Advantages
- Precision and Consistency: Achieves micrometer-scale accuracy with uniform results across large areas.
- Versatility: Compatible with metals, non-metals, and composites, adjustable for various depths and contrasts.
- Speed: Marks are completed in seconds, outpacing chemical or mechanical methods.
- Non-Contact: Eliminates tool wear and reduces contamination risks.
- Environmental Impact: Produces minimal waste compared to wet etching, avoiding hazardous chemicals.
Limitations
- Material Restrictions: Highly reflective or transparent materials may require specialized lasers or pre-treatments.
- Initial Cost: High-end flatbed systems can exceed $50,000, though desktop models start at $1,000.
- Thermal Effects: Excessive heat can damage delicate substrates or induce stress cracks.
- Depth Limitation: Typically limited to shallow marks (<0.01 inches), unlike deep engraving.
Comparison with Other Etching Methods
Flatbed laser etching competes with traditional methods like chemical etching, mechanical engraving, and plasma etching. The following table compares these techniques across key metrics:
Method | Mechanism | Precision | Speed | Material Range | Cost | Environmental Impact |
---|---|---|---|---|---|---|
Flatbed Laser Etching | Laser-induced melting/ablation | High (±10 μm) | Fast (seconds) | Broad (metals, non-metals) | Moderate–High | Low (no chemicals) |
Chemical Etching | Acid/base corrosion | Moderate (±50 μm) | Slow (minutes) | Limited (mostly metals) | Low–Moderate | High (hazardous waste) |
Mechanical Engraving | Physical cutting | High (±20 μm) | Moderate (minutes) | Broad (hard materials) | Moderate | Moderate (dust, noise) |
Plasma Etching | Ionized gas bombardment | Very High (±1 μm) | Slow (hours) | Limited (semiconductors) | High | Moderate (gas emissions) |
Flatbed laser etching stands out for its balance of speed, precision, and environmental friendliness, though it may not match plasma etching’s nanoscale capabilities or chemical etching’s low cost for simple tasks.
Conclusion:Safety and Operational Considerations
Advancements in flatbed laser etching have expanded its capabilities, driven by innovations in laser technology and system design. Femtosecond lasers, with pulse durations below 10^-12 seconds, minimize thermal diffusion, enabling damage-free etching of fragile materials like fused silica. Hybrid systems combining laser etching with additive processes (e.g., laser-induced forward transfer) allow simultaneous patterning and deposition. Additionally, AI-driven control software optimizes parameters in real-time, enhancing efficiency and reducing trial-and-error.
Operating flatbed laser etching systems requires adherence to safety protocols due to the risks of high-intensity light and fume generation. Class 1 enclosures, laser-rated goggles, and ventilation systems mitigate hazards. Operators must also calibrate focal distance and power settings to prevent substrate damage or incomplete etching.
The future of flatbed laser etching lies in greater automation, integration with Industry 4.0 frameworks, and expanded material compatibility. Developments in multi-wavelength lasers could enable single-system processing of diverse substrates, while scalable flatbed designs may cater to emerging fields like flexible electronics or large-scale additive manufacturing.
Flatbed laser etching represents a pivotal advancement in surface processing, blending precision, versatility, and efficiency into a single platform. Its flatbed configuration enhances its utility for large-scale applications, from industrial marking to scientific microfabrication, while ongoing innovations promise to broaden its impact. As a non-contact, environmentally friendly alternative to traditional methods, it exemplifies the transformative potential of laser technology in modern manufacturing and beyond.