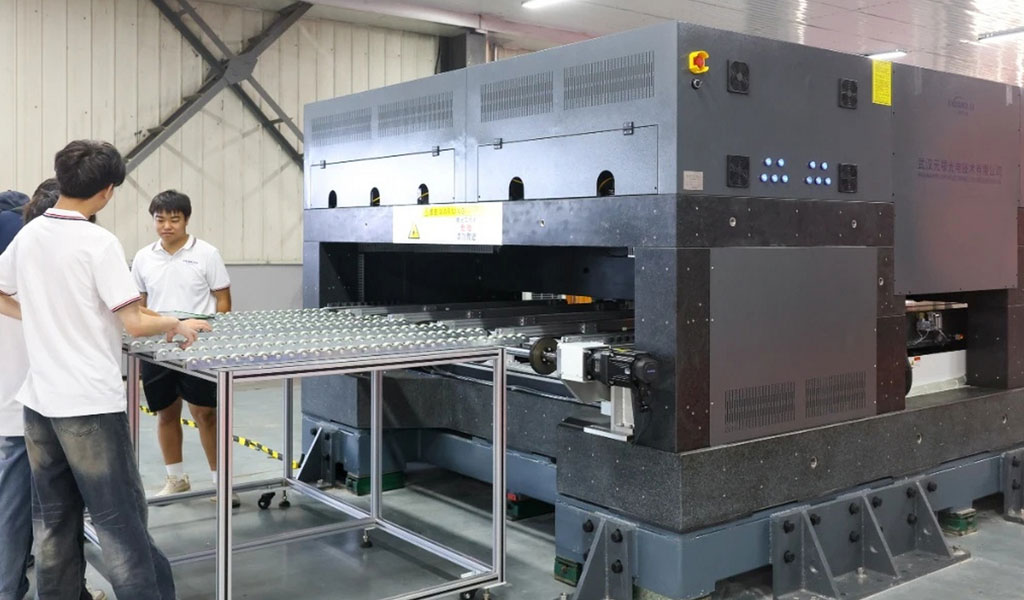
Galvo laser etching is a precision manufacturing process that utilizes galvanometer-driven laser systems to create permanent marks, patterns, or designs on a variety of materials. This technology, rooted in the principles of optics and electromechanical control, has become a cornerstone in industries ranging from electronics and aerospace to jewelry and medical device manufacturing. By directing a focused laser beam with high-speed mirrors, galvo laser etching achieves exceptional accuracy and efficiency, distinguishing it from traditional laser systems and other etching methods. This article explores the scientific foundations, technological mechanisms, applications, and comparative advantages of galvo laser etching, providing a detailed examination suitable for both technical and general audiences.
Historical Context and Development
The concept of laser etching emerged shortly after the invention of the laser in 1960 by Theodore H. Maiman, who demonstrated the first functional ruby laser. Early laser applications were limited by the inability to precisely control beam direction, restricting their use to static or manually adjusted processes. The introduction of galvanometer technology—originally developed in the 19th century to measure electric current—marked a pivotal advancement in laser beam steering. By the late 20th century, galvanometer scanners (commonly abbreviated as “galvo”) were integrated with laser systems, enabling rapid and accurate beam positioning.
The galvo laser etching process gained prominence in the 1980s as industries sought faster and more reliable methods for marking and engraving. Companies like Epilog Laser and Trotec pioneered commercial galvo systems, leveraging advancements in fiber optics, CO2 laser sources, and computer-aided design (CAD) software. Today, galvo laser etching represents a mature technology, continuously refined through innovations in mirror design, servo control, and laser power modulation.
Principles of Galvo Laser Etching
Galvo laser etching operates on the interaction between a coherent light source (the laser) and a material substrate, facilitated by a galvanometer scanning system. The galvanometer consists of two small, high-precision mirrors mounted on rotary motors, each responsible for deflecting the laser beam along the X and Y axes. These mirrors, driven by servo motors, adjust their angles rapidly in response to electrical signals, allowing the laser beam to trace complex patterns across a marking field.
Laser-Material Interaction
The etching process begins with the laser beam, which is typically generated by a fiber, CO2, or ultraviolet (UV) source, depending on the material and desired outcome. When the beam strikes the material surface, it delivers concentrated energy, causing localized heating, vaporization, or chemical alteration. The specific interaction depends on the material’s properties and the laser’s wavelength:
- Metals: Fiber lasers (typically 1064 nm) are commonly used, causing surface ablation or annealing to create high-contrast marks without significant material removal.
- Non-Metals: CO2 lasers (10.6 μm) excel at vaporizing organic materials like wood, plastic, and glass, producing deep engravings or clean cuts.
- Specialized Materials: UV lasers (e.g., 355 nm) are employed for delicate substrates like ceramics or polymers, minimizing thermal damage due to their shorter wavelength and higher absorption rates.
The energy density, or fluence, of the laser beam—measured in joules per square centimeter (J/cm²)—determines the depth and quality of the etch. This is modulated by parameters such as power output, pulse duration, and scanning speed.
Galvanometer Mechanism
The galvanometer system is the heart of galvo laser etching, enabling speeds far exceeding those of traditional gantry-based lasers. Each mirror is controlled by a closed-loop servo system, which uses feedback from position detectors (e.g., capacitive or optical sensors) to ensure precise angular adjustments. The mirrors reflect the laser beam through an F-theta lens, which focuses it onto the material surface while maintaining a flat field of focus across the marking area. This eliminates the need for mechanical movement of the laser head, reducing wear and increasing throughput.
The step response time of the galvanometer—typically in the range of 100 microseconds to 1 millisecond—defines its ability to reposition the beam quickly. This is complemented by a resonant frequency (often 1-2 kHz), which indicates the system’s stability under rapid oscillations. These characteristics make galvo systems ideal for high-speed applications.
Technical Specifications and Components
Galvo laser etching systems vary widely in design, tailored to specific industrial needs. Key components and specifications include:
Laser Sources
- Fiber Lasers: Output power ranges from 20 W to 100 W, with a wavelength of 1064 nm. Known for durability and efficiency (20-30% electro-optical conversion).
- CO2 Lasers: Power ranges from 30 W to 150 W, with a wavelength of 10.6 μm. Suited for non-metals, though less efficient (6-7%) due to chiller requirements.
- UV Lasers: Lower power (2-5 W), with wavelengths like 355 nm or 532 nm. Offer high precision for heat-sensitive materials.
Galvanometer Scanners
- Mirror Size: Typically 10-20 mm in diameter, affecting beam deflection range and speed.
- Scan Angle: Up to ±20° per axis, defining the marking field size (e.g., 100×100 mm to 310×310 mm).
- Speed: Up to 10,000 mm/s, far surpassing gantry systems (100-500 mm/s).
Optics
- F-theta Lens: Focal lengths of 163 mm or 254 mm are common, balancing field size and spot resolution. Spot sizes range from 10-50 μm, depending on lens and wavelength.
- Beam Quality (M²): Near 1.1 for fiber lasers, ensuring tight focus and minimal divergence.
Control Systems
Modern galvo systems are paired with software like Epilog’s Laser Dashboard or Trotec’s SpeedMark, allowing users to import designs from CAD programs (e.g., AutoCAD, CorelDRAW) and adjust parameters like power, speed, and pulse frequency. Advanced models feature 1 GB of onboard memory for job queuing and Ethernet connectivity for networked operation.
Applications of Galvo Laser Etching
Galvo laser etching’s versatility stems from its speed, precision, and adaptability to diverse materials. Key applications include:
Industrial Marking
- Traceability: Serial numbers, barcodes, and QR codes are etched onto metal components (e.g., automotive parts) or plastic housings (e.g., electronics) for inventory and quality control.
- Branding: Logos and text are marked on tools, medical instruments, and consumer goods, ensuring durability and resistance to wear.
Microfabrication
- Electronics: Etching conductive pathways or insulating layers on printed circuit boards (PCBs) with sub-micron precision.
- Medical Devices: Marking titanium implants or engraving polymer catheters with biocompatible patterns.
Artistic and Decorative Uses
- Jewelry: Intricate designs on gold, silver, or stainless steel, often with depths of 0.1-0.5 mm.
- Custom Gifts: Personalized engravings on wood, glass, or leather, leveraging CO2 or UV lasers for varied textures.
Emerging Fields
- Agriculture: Blue galvo lasers (405-450 nm) label fruits or process crops with minimal damage, integrating with robotic systems for automated farming.
- 3D Printing: Post-processing of additively manufactured parts, refining surfaces or adding functional markings.
Advantages and Limitations
Advantages
- Speed: Galvo systems can mark at rates of 4,000-10,000 mm/s, completing intricate patterns in seconds compared to minutes for gantry lasers.
- Precision: Sub-micron accuracy supports detailed designs and small-scale features.
- Durability: Mirror-based scanning eliminates mechanical wear on belts or pulleys, reducing maintenance needs.
- Flexibility: Adjustable marking fields and compatibility with multiple laser types suit diverse applications.
Limitations
- Field Size: Limited to 100×100 mm to 535×535 mm without additional axis systems, smaller than flatbed lasers (up to 87×126 inches).
- Material Thickness: Best suited for thin or flat surfaces; cutting thick materials (e.g., >10 mm) is less efficient than gantry CO2 systems.
- Cost: Initial investment is higher due to precision optics and servo systems, with prices ranging from $5,000 to $50,000 depending on power and features.
Comparison with Other Laser Technologies
To elucidate galvo laser etching’s position within the broader laser processing landscape, the following tables compare it with flatbed (gantry) lasers and diode lasers across key metrics.
Parameter | Galvo Laser | Flatbed Laser | Diode Laser |
---|---|---|---|
Beam Steering | Galvanometer mirrors | Gantry (X-Y axes) | Fixed or gantry |
Max Speed (mm/s) | 4,000-10,000 | 100-500 | 50-300 |
Marking Area | 100×100 mm to 535×535 mm | Up to 87×126 inches | 100×100 mm to 400×400 mm |
Precision (μm) | 10-50 | 50-100 | 20-100 |
Power Range (W) | 2-150 (varies by type) | 10-400 | 5-20 |
Wavelength (nm) | 355, 532, 1064, 10,600 | 10,600 (CO2), 1064 (fiber) | 405-980 |
Efficiency (%) | 20-30 (fiber), 6-7 (CO2) | 6-10 (CO2), 20-30 (fiber) | 10-20 |
Maintenance | Low (lens cleaning only) | Moderate (belts, pulleys) | Low to moderate |
Cost (USD) | $5,000-$50,000 | $2,000-$100,000 | $200-$5,000 |
Material | Galvo Laser (Fiber) | Galvo Laser (CO2) | Flatbed Laser (CO2) | Diode Laser |
---|---|---|---|---|
Metals | Excellent | Poor | Poor | Moderate |
Plastics | Good | Excellent | Excellent | Good |
Wood | Poor | Excellent | Excellent | Excellent |
Glass | Moderate (UV) | Good | Good | Poor |
Ceramics | Excellent (UV) | Moderate | Moderate | Poor |
Leather | Poor | Excellent | Excellent | Excellent |
Analysis
- Galvo vs. Flatbed: Galvo lasers excel in speed and precision for small-to-medium areas, while flatbed systems dominate in large-scale cutting and engraving due to their expansive work areas.
- Galvo vs. Diode: Galvo systems outperform diode lasers in speed and versatility, though diode lasers are more affordable for hobbyists and small-scale projects.
Recent Advances and Research
Recent developments in galvo laser etching focus on enhancing speed, expanding material compatibility, and integrating with smart systems. Studies published in 2024 (e.g., Journal of Laser Applications) highlight:
- 3D Scanning: Incorporation of 3D cameras (e.g., Intel RealSense) for automatic focus adjustment on uneven surfaces, improving accuracy on complex geometries.
- Blue Lasers: Opt Lasers’ 405-450 nm systems offer higher absorption in ceramics and organic materials, reducing energy consumption by 15-20% compared to CO2 lasers.
- Automation: Integration with AI and robotics, as seen in agricultural applications, increases throughput by 30-50% in high-volume settings.
These advancements underscore galvo laser etching’s evolving role in precision manufacturing and emerging fields.
Conclusion
Operating galvo laser systems requires adherence to safety standards (e.g., ANSI Z136.1) due to risks of eye damage and fume generation. Protective eyewear matched to the laser wavelength is mandatory, and enclosed systems with fume extractors mitigate inhalation hazards. Environmentally, fiber-based galvo lasers are more energy-efficient than CO2 counterparts, though disposal of ablated material (e.g., metal dust) necessitates proper waste management.
The future of galvo laser etching lies in its convergence with Industry 4.0 technologies. Predictive maintenance using IoT sensors, real-time process optimization via machine learning, and expanded use in additive manufacturing post-processing are anticipated trends. As costs decrease and accessibility improves, galvo systems may penetrate smaller enterprises and educational settings, democratizing advanced manufacturing.
Galvo laser etching stands as a pinnacle of precision and efficiency in laser processing, leveraging galvanometer technology to meet diverse industrial and artistic demands. Its ability to rapidly mark intricate designs on metals, plastics, and organic materials positions it as a vital tool in modern manufacturing. While limitations in field size and cost persist, ongoing innovations promise to broaden its applicability, ensuring its relevance in an increasingly automated and precise world.