Titanium is a lustrous transition metal recognized for its high strength-to-weight ratio, low density, and exceptional resistance to corrosion, even in harsh environments such as seawater, aqua regia, and chlorine. These properties make titanium a preferred material in various industries, including aerospace, biomedical implants, chemical processing, and art.
Due to its inertness, titanium is often used in applications where biocompatibility and durability are critical. In art and industrial processes, titanium is employed for etching plates, which require a high degree of polish to produce detailed and precise designs.
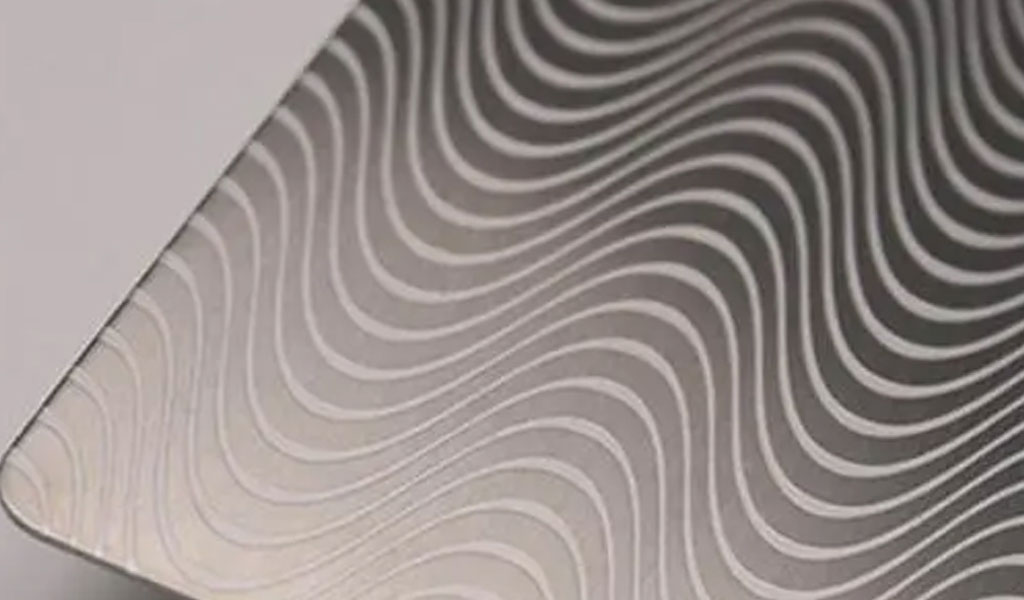
The Importance of Polishing in Etching
In the context of etching, polishing is a crucial step that affects the quality of the final product. A polished titanium plate ensures that the etching process yields sharp, clean lines with consistent depth, which is essential for achieving high-resolution and intricate designs.
Moreover, polishing removes surface imperfections, such as scratches, pits, and oxidation layers, which can interfere with the etching process.
Polishing Processes for Titanium Etching Plates
The polishing of titanium etching plates can be broadly categorized into mechanical, chemical, and electrochemical processes. Each method has its advantages, limitations, and specific applications depending on the desired outcome, plate size, and complexity of the design.
Mechanical Polishing
1. Surface Preparation
The initial step in polishing titanium involves surface preparation. This stage is critical for removing any existing oxide layers, dirt, and other contaminants that might hinder the polishing process. The preparation typically involves cleaning the titanium plate with solvents such as acetone or isopropyl alcohol, followed by rinsing with deionized water to remove any residual chemicals.
2. Grinding
Grinding is a mechanical process that utilizes abrasive particles to remove material from the surface of the titanium plate. The grinding process is usually carried out in several stages, beginning with coarse abrasives to remove large amounts of material and followed by progressively finer abrasives to achieve a smooth surface.
The most common abrasives used in titanium grinding include silicon carbide (SiC) and aluminum oxide (Al2O3). These materials are available in various grit sizes, ranging from coarse (e.g., 60-100 grit) for initial grinding to fine (e.g., 800-1200 grit) for finishing.
3. Lapping
Lapping is a refining process that follows grinding and involves the use of a flat, rotating surface (lapping plate) and a slurry containing fine abrasive particles. The titanium plate is placed on the lapping plate, and the slurry facilitates the removal of microscopic amounts of material, leading to a very flat and smooth surface.
Lapping compounds typically include abrasives like diamond, alumina, or cerium oxide suspended in a liquid carrier. The process may be performed under controlled pressure and speed to ensure uniform material removal across the plate’s surface.
4. Polishing
Polishing is the final mechanical step, which involves the use of even finer abrasives to achieve a mirror-like finish on the titanium plate. The polishing process can be done manually or using polishing machines, depending on the size and complexity of the plate.
Polishing compounds, such as diamond paste or colloidal silica, are often used in this stage. These compounds are applied to a soft cloth or polishing pad, which is then moved over the titanium surface in a controlled manner. The goal is to produce a surface free of scratches, pits, or any other imperfections that might affect the quality of the etching.
Challenges in Mechanical Polishing of Titanium
Titanium’s hardness and tendency to gall (adhesive wear) pose significant challenges during mechanical polishing. The metal’s reactivity with oxygen also leads to the formation of a passive oxide layer that can interfere with the polishing process. These challenges require the use of specialized techniques and materials, such as non-loading abrasives and lubricants, to achieve a high-quality finish.
Chemical Polishing
1. Chemical Milling
Chemical polishing, also known as chemical milling, involves the controlled removal of material from the titanium surface through chemical reactions. This process is particularly useful for removing surface irregularities that are difficult to eliminate through mechanical means.
Chemical milling typically involves the use of acid-based solutions, such as hydrofluoric acid (HF) or a mixture of nitric acid (HNO3) and HF, which selectively dissolve the titanium surface. The concentration, temperature, and immersion time must be carefully controlled to achieve the desired level of polish without excessive material removal.
2. Etchants for Titanium
The choice of etchant is critical in chemical polishing. Common etchants for titanium include:
- Hydrofluoric Acid (HF): HF is effective in dissolving titanium oxide layers and is often used in combination with other acids to achieve a smooth surface. However, HF is highly corrosive and toxic, requiring careful handling and safety precautions.
- Nitric Acid (HNO3): HNO3 is often used in combination with HF to control the etching rate and improve surface quality. The mixture of HNO3 and HF is commonly referred to as “titanium etch.”
- Sulfuric Acid (H2SO4): H2SO4 can be used as a pre-treatment to clean and activate the titanium surface before chemical polishing.
3. Passivation and Surface Protection
After chemical polishing, it is essential to passivate the titanium surface to protect it from further oxidation or corrosion. Passivation involves treating the titanium with a mild oxidizing solution, such as a dilute nitric acid solution, which forms a stable and inert oxide layer on the surface.
Electrochemical Polishing
1. Principles of Electrochemical Polishing
Electrochemical polishing, also known as electropolishing, is a process that involves the removal of material from a metal surface through anodic dissolution in an electrolytic cell. The titanium plate is connected as the anode, and a suitable cathode material is used in an electrolyte solution.
When an electric current is applied, metal ions from the titanium surface are dissolved into the electrolyte, leading to the smoothing and leveling of the surface. Electrochemical polishing is highly effective in producing a mirror-like finish and is often used for complex shapes and fine features that are difficult to polish mechanically.
2. Electrolytes for Titanium
The choice of electrolyte is crucial in electrochemical polishing. Common electrolytes used for titanium include:
- Perchloric Acid (HClO4): HClO4-based electrolytes are effective in polishing titanium, but they are highly reactive and require strict safety measures.
- Methanol and Perchloric Acid Mixtures: These mixtures are commonly used for polishing titanium, especially when a high degree of surface smoothness is required.
- Sulfuric Acid and Glycerin Mixtures: These mixtures are less aggressive than perchloric acid-based electrolytes and are often used for applications where safety is a concern.
3. Process Parameters
The key parameters in electrochemical polishing include voltage, current density, temperature, and polishing time. These parameters must be carefully optimized to achieve the desired surface finish without over-polishing or damaging the titanium plate.
- Voltage and Current Density: The applied voltage and current density control the rate of material removal. Higher values can lead to faster polishing but may also increase the risk of surface defects.
- Temperature: The electrolyte temperature affects the reaction kinetics and the quality of the polished surface. Elevated temperatures generally increase the polishing rate but may also lead to the formation of a rough surface.
- Polishing Time: The duration of the electrochemical polishing process must be carefully controlled to achieve the desired finish. Over-polishing can lead to excessive material removal and surface defects.
4. Post-Polishing Treatment
After electrochemical polishing, the titanium plate must be thoroughly rinsed with deionized water to remove any residual electrolyte. The plate is then dried and passivated to enhance its corrosion resistance and maintain the polished surface.
Quality Control and Inspection
1. Surface Roughness Measurement
Surface roughness is a critical parameter in evaluating the quality of a polished titanium plate. Roughness can be measured using techniques such as contact profilometry or atomic force microscopy (AFM). The goal is to achieve a surface with minimal roughness, typically in the nanometer range, depending on the application.
2. Visual Inspection
Visual inspection is performed to identify any surface defects, such as scratches, pits, or discoloration, that may affect the etching process. This inspection can be done using optical microscopes or, for more detailed analysis, scanning electron microscopy (SEM).
3. Thickness and Uniformity
The thickness of the titanium plate and the uniformity of material removal are also important quality control parameters. These can be measured using techniques such as X-ray fluorescence (XRF) or non-destructive testing methods like ultrasonic thickness measurement.
4. Testing for Surface Contamination
Surface contamination can negatively impact the etching process, leading to poor-quality designs. Testing for surface contamination involves techniques such as X-ray photoelectron spectroscopy (XPS) or Auger electron spectroscopy (AES) to detect any unwanted elements or compounds on the surface.
Conclusion
Polishing a titanium etching plate is a complex process that requires careful consideration of various techniques and parameters. From mechanical grinding and polishing to chemical and electrochemical methods, each step must be meticulously controlled to achieve the desired surface finish. The choice of materials, abrasives, electrolytes, and process parameters plays a significant role in determining the quality of the final product.
In industrial and artistic applications, the success of the etching process heavily depends on the quality of the polished titanium plate. As such, ongoing research and development in polishing techniques continue to enhance the efficiency and effectiveness of these processes, enabling the production of high-precision titanium etching plates that meet the stringent requirements of modern applications.