In today’s fast-paced manufacturing world, precision and efficiency are paramount. Reducing assembly errors is not only a key factor in improving product quality but also in saving time and resources. One innovative solution that has been gaining prominence in various industries is precision etching. This advanced manufacturing technique is revolutionizing the way components are produced, significantly minimizing the risk of assembly errors. In this article, we will explore how precision etching parts can play a pivotal role in streamlining the assembly process and ensuring higher product reliability.
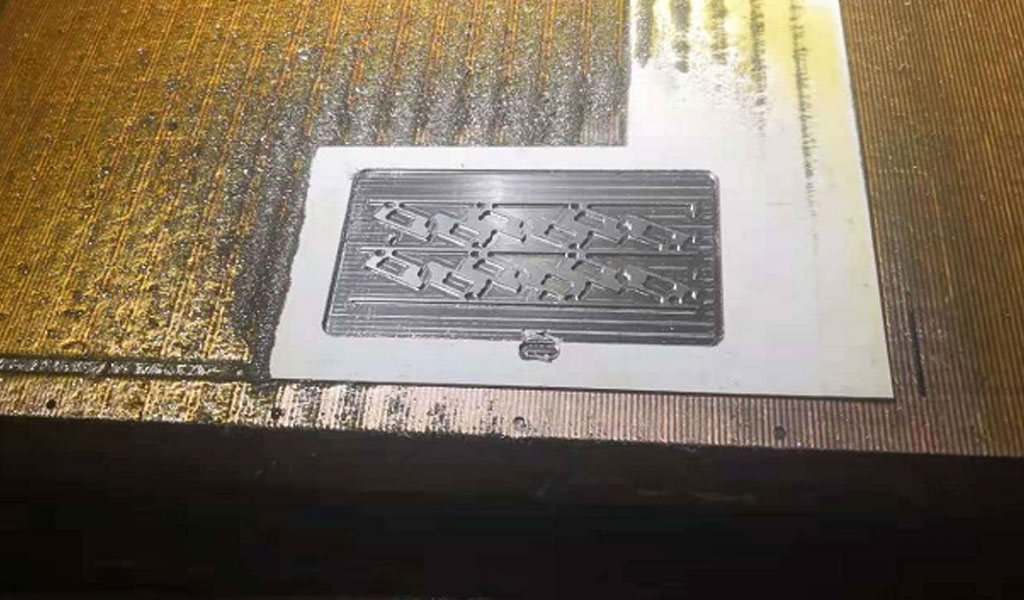
Common Assembly Errors
In manufacturing and assembly processes, achieving precision is of paramount importance.
Assembly errors can lead to a cascade of problems, ranging from decreased product quality to increased costs and potential safety risks. This section delves into some of the most prevalent assembly errors and the issues they can cause:
1.Misalignment
Misalignment is a common assembly error that occurs when parts do not fit together correctly, either due to human error, manufacturing discrepancies, or subpar component quality. The consequences of misalignment are wide-ranging:
- Reduced Product Functionality: When parts do not align as intended, the product may not function as expected or may even fail to function at all. Misalignment can hinder the movement of mechanical components, disrupt electrical connections, or interfere with fluid flow in systems.
- Increased Friction and Wear: Misalignment often leads to increased friction between parts, causing wear and tear. This can significantly reduce the lifespan of the product and increase the need for maintenance and replacement parts.
- Quality Issues: Misaligned parts can create visual imperfections and cosmetic defects in the final product, affecting its aesthetics and perceived quality.
- Safety Concerns: In certain applications, such as automotive or aerospace, misalignment can pose serious safety risks. Critical components must align correctly to ensure safe and reliable operation.
To address misalignment, precision manufacturing techniques like precision etching can be employed to produce parts with highly accurate dimensions and tolerances, minimizing the likelihood of misalignment issues.
2.Tolerances and Gaps
Tolerances and gaps refer to the permissible variations in part dimensions and the spaces between them. When these tolerances are not controlled or are too wide, it can result in gaps or interference in assemblies:
- Fit Issues: Parts with overly loose tolerances can lead to excessive gaps between components. Conversely, overly tight tolerances may cause interference, making it impossible to fit parts together, or leading to deformation during assembly.
- Reduced Functionality: Products may not work correctly if parts are too loose or too tight, resulting in unreliable performance and potential product failures.
- Quality Control Challenges: Wide tolerances can make quality control more difficult, as variations between parts may be mistaken for defects.
- Cost Implications: Wide tolerances can lead to increased material waste and higher assembly and maintenance costs, as compensatory measures become necessary to accommodate the variations.
Precision etching allows for precise control of tolerances, ensuring that parts fit together with minimal gaps and interference, leading to enhanced product functionality and reduced waste.
3.Material Compatibility
Material compatibility is crucial in ensuring that parts and components can work together harmoniously within an assembly. Incompatible materials can result in several assembly errors:
- Chemical Reactions: Certain materials may react with others, causing corrosion, weakening structural integrity, or leading to unexpected changes in material properties.
- Thermal Expansion and Contraction: Materials expand and contract at different rates when exposed to temperature fluctuations. Incompatible materials may lead to issues such as warping, cracking, or misalignment as temperatures change.
- Electrochemical Compatibility: In electronic assemblies, materials must be chosen carefully to ensure electrical conductivity, insulation, or other specific properties. Incompatible materials can disrupt electrical circuits and connections.
- Durability and Longevity: Incompatibility can reduce the overall durability and longevity of the product. Premature wear and deterioration may occur due to material mismatch.
To mitigate these issues, precision etching enables the selection and preparation of materials that are not only compatible but also optimized for the specific requirements of an assembly.
4.Fastener and Component Errors
Fasteners and components are integral parts of an assembly, and any errors related to their selection or installation can lead to significant problems:
- Inadequate Fastening: Incorrect or insufficiently tightened fasteners can result in parts coming loose, posing safety risks and potentially causing product malfunction.
- Incorrect Component Selection: Using the wrong components or substituting them with non-standard alternatives can lead to compatibility issues, reduced performance, and product failures.
- Mismatched Hardware: Mismatched fasteners and components can lead to misalignment, tolerances, and gaps issues, complicating assembly and increasing the likelihood of errors.
- Quality Control Challenges: Verifying the correctness of fasteners and components can be challenging, especially in complex assemblies with many parts.
Precision etching can play a role in producing customized fasteners and components that meet precise specifications, reducing the likelihood of errors associated with their use.
Common assembly errors, such as misalignment, tolerances and gaps, material compatibility, and fastener/component errors, can have far-reaching consequences for product quality, functionality, and safety. Precision etching offers a valuable solution to address these issues by providing parts with precise dimensions, tight tolerances, and material compatibility, ultimately reducing the likelihood of assembly errors and improving overall product performance.
Reducing Assembly Errors with Precision Etching
Precision etching is a manufacturing technique that offers a range of benefits, enabling manufacturers to produce components with extraordinary precision and consistency. In this section, we will explore how precision etching directly contributes to reducing assembly errors and improving overall product quality.
1.Improved Part Consistency
One of the key advantages of precision etching is its ability to produce parts with unmatched consistency in terms of dimensions and geometry. This level of consistency significantly reduces the occurrence of assembly errors, especially in cases of misalignment and tolerance issues:
- Dimensional Uniformity: Precision etching allows for the production of parts with extremely consistent dimensions. This minimizes the likelihood of parts not fitting together correctly due to slight variations in size.
- Repeatability: Unlike traditional manufacturing methods that may produce parts with varying dimensions, precision etching ensures that each component is nearly identical. This makes it easier to replace or interchange parts, reducing assembly errors due to inconsistencies.
- Predictable Performance: With precision etching, the performance of each part can be predicted with a high degree of confidence. Engineers and assemblers can rely on the uniformity of etched parts, making assembly processes more efficient and reducing the chances of errors.
2.Tolerance Control
Tolerance control is crucial in manufacturing, and precision etching excels in this regard. It allows for the tight control of tolerances, meaning that the permissible variations in part dimensions are exceptionally small. This tight control directly addresses issues related to gaps and interference in assemblies:
- Minimized Gaps: Precision etching ensures that the dimensions of parts are held within very tight tolerances, reducing the occurrence of gaps between components. Parts fit together precisely, promoting seamless assembly.
- Reduced Interference: Tight tolerance control means that parts do not interfere with each other during assembly. There’s no need for forceful adjustments or additional machining to make components fit correctly, which can introduce errors.
- Optimized Assemblies: Assemblies with parts produced through precision etching are optimized for ideal performance. The elimination of gaps and interference results in products that work smoothly and efficiently.
3.Material Selection
Another significant advantage of precision etching is the flexibility it offers in material selection. This has a direct impact on reducing assembly errors related to material compatibility:
- Materials Tailored to the Application: Precision etching allows manufacturers to select materials based on the specific requirements of the assembly. This means that the chosen materials can be optimized for factors like strength, durability, and chemical resistance, reducing the chances of incompatibility issues.
- Layered or Composite Parts: Precision etching enables the creation of layered or composite parts with different materials bonded together precisely. This is particularly useful in applications where one part requires electrical conductivity while another requires insulation.
- Material Compatibility Testing: Manufacturers can choose materials that have been tested and proven compatible for the intended use. This minimizes the risk of unexpected chemical reactions, corrosion, or other compatibility issues.
4.Customization and Complexity
Precision etching allows for the creation of intricate parts with customized designs. This level of customization is invaluable in ensuring that parts fit together perfectly within complex assemblies:
- Intricate Geometry: Precision etching can produce parts with intricate and complex geometries that would be difficult or impossible to achieve using traditional machining methods. These intricacies can be tailored to perfectly align with other components.
- Custom Fit: Customization options mean that each part can be uniquely designed to meet the precise requirements of the assembly. This eliminates the need for modification or adaptation during assembly, reducing errors.
- Assemblies with Reduced Components: Precision etching can consolidate multiple components into a single piece, reducing the number of parts required for assembly. Fewer parts mean fewer opportunities for errors during assembly.
Precision etching offers a comprehensive solution to reducing assembly errors by providing improved part consistency, precise tolerance control, material selection flexibility, and the ability to create customized and intricate components. These benefits collectively contribute to smoother assembly processes, lower error rates, and enhanced product quality.
In Conclusion
In the world of manufacturing and assembly, precision is the cornerstone of success. Assembly errors can lead to a myriad of problems, from compromised product quality to increased costs and safety concerns. Throughout this article, we have explored the profound impact of precision etching in mitigating assembly errors and enhancing overall product quality.
Precision etching, as a manufacturing technique, offers a multitude of advantages that directly address common assembly errors. By producing parts with consistent dimensions and tight tolerances, precision etching significantly reduces the chances of misalignment and issues related to gaps and interference during assembly. Moreover, it provides the flexibility to select materials optimized for compatibility, minimizing material-related errors. Additionally, precision etching allows for the creation of intricate, customized parts that seamlessly fit together, reducing complexity and the likelihood of component errors.
As industries across the spectrum continue to demand higher standards of quality and performance, the role of precision etching in reducing assembly errors becomes increasingly crucial. This technology not only ensures that products meet exacting specifications but also contributes to cost savings, increased reliability, and improved safety. Moreover, as precision etching continues to evolve, it promises to usher in new opportunities for innovation and sustainability, ensuring that the future of manufacturing remains bright.
In conclusion, precision etching is more than just a manufacturing method; it is a solution to the challenges posed by assembly errors. As we continue to harness the potential of precision etching, we can look forward to a world where product assembly is less prone to error, leading to greater efficiency, reliability, and the delivery of higher-quality products to consumers worldwide. The adoption of precision etching is not just a choice but a necessity for manufacturers who seek to excel in today’s competitive landscape and deliver products that exceed the expectations of a discerning market.