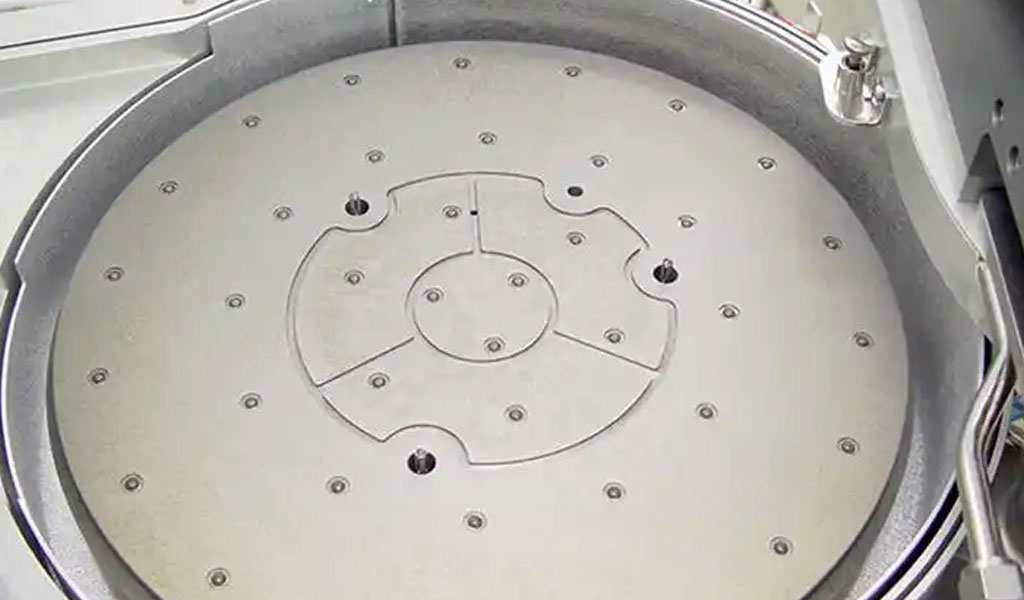
Etching a flow control disc is a precise and intricate process that requires expertise in chemical etching, material science, and manufacturing techniques.
Flow control discs are critical components used in various industries, including aerospace, automotive, medical, and industrial fluid systems, where precision control of fluid or gas flow is essential.
This article delves into the comprehensive steps, techniques, materials, and considerations involved in etching a flow control disc.
Material Selection for Flow Control Discs
The choice of material is foundational to the etching process. Common materials used for flow control discs include stainless steel, brass, copper, nickel alloys, and titanium. Each material presents unique properties that affect the etching process:
- Stainless Steel: Known for its corrosion resistance and strength, stainless steel is a popular choice for flow control discs, especially in harsh environments. Grades like 304 and 316 are commonly used.
- Brass and Copper: These materials are preferred for their excellent machinability and thermal conductivity, which are ideal for certain fluid control applications.
- Nickel Alloys: High resistance to corrosion and heat makes nickel alloys suitable for demanding environments.
- Titanium: Lightweight and highly resistant to corrosion, titanium is often used in medical and aerospace applications.
The choice of material impacts the etching method, chemical composition of the etching solution, and the overall manufacturing process.
Designing the Flow Control Disc
Designing the disc involves precise engineering to ensure optimal flow control. Factors to consider include:
- Disc Dimensions: Thickness, diameter, and the size of flow channels must be accurately specified.
- Flow Holes and Patterns: The arrangement and size of flow holes determine the disc’s performance. Advanced software is often used to design intricate patterns to achieve desired flow rates.
- Tolerance Levels: High precision is essential, with tolerances often specified in microns to ensure consistent performance.
The design is typically rendered in CAD (Computer-Aided Design) software. Once finalized, the design is transferred to a photomask for the etching process.
Photolithography: Preparing the Design Template
Photolithography is a critical step in transferring the disc design onto the material. The process involves:
- Coating with Photoresist:
- A light-sensitive photoresist layer is applied to the material’s surface. This can be achieved through spin coating or lamination, ensuring an even and consistent layer.
- Exposing the Design:
- The photomask, containing the disc design, is placed over the coated material. Ultraviolet (UV) light is used to expose the photoresist. The areas exposed to light become soluble (positive photoresist) or insoluble (negative photoresist), depending on the type used.
- Developing the Photoresist:
- A developer solution removes the soluble portions of the photoresist, leaving behind the design on the material.
Chemical Etching Process
Chemical etching, also known as photochemical machining (PCM), removes material to create the desired flow patterns and features. The process involves:
- Preparing the Etching Solution:
- The choice of etchant depends on the material. For stainless steel, ferric chloride is commonly used, while copper alloys often require ammonium persulfate or a similar solution.
- The concentration, temperature, and agitation of the etchant are critical parameters.
- Etching the Material:
- The material is submerged in the etching solution.
- The exposed areas, unprotected by the photoresist, react with the etchant, dissolving and creating the flow holes and patterns.
- Etching time is carefully controlled to achieve precise depth and dimensions.
- Monitoring the Process:
- Continuous monitoring ensures uniform etching. Advanced systems use optical or laser measurement tools to check progress.
- Rinsing and Drying:
- After etching, the disc is thoroughly rinsed to remove residual chemicals. High-pressure water or ultrasonic cleaning may be used.
Stripping and Finishing
After etching, the remaining photoresist is removed using a stripping solution. The disc is then subjected to finishing processes, including:
- Deburring: Removing sharp edges or burrs formed during etching.
- Polishing: Achieving a smooth surface finish for optimal performance.
- Passivation: For stainless steel discs, passivation enhances corrosion resistance by removing free iron and forming a protective oxide layer.
Quality Control
Ensuring the flow control disc meets specifications is crucial. Quality control steps include:
- Dimensional Inspection: Measuring dimensions and hole sizes using tools like coordinate measuring machines (CMMs) or optical profilers.
- Flow Testing: Simulating operational conditions to verify flow rates and pressure drops.
- Surface Analysis: Checking for defects, scratches, or inconsistencies that could affect performance.
Applications and Customization
Flow control discs are used in various applications, including fuel injectors, medical devices, and industrial machinery. Customization options include:
- Material Coatings: Adding coatings like Teflon for enhanced performance.
- Engraving or Marking: Laser marking for identification or branding.
- Special Features: Incorporating filters, multiple flow zones, or specific geometries.
Environmental and Safety Considerations
The etching process involves hazardous chemicals, requiring strict adherence to safety and environmental protocols:
- Personal Protective Equipment (PPE): Workers must wear gloves, goggles, and protective clothing.
- Waste Management: Etching solutions must be neutralized and disposed of in compliance with environmental regulations.
- Ventilation Systems: Proper ventilation minimizes exposure to harmful fumes.
Advancements in Etching Technology
Recent advancements have enhanced the efficiency and precision of etching flow control discs:
- Laser-Assisted Etching: Combining lasers with chemical etching for greater precision.
- Automated Systems: Using robotics and AI for consistent quality and reduced production time.
- Eco-Friendly Etching: Developing biodegradable etching solutions to reduce environmental impact.
Conclusion
Etching flow control discs is a highly specialized process requiring meticulous attention to detail, advanced technology, and a deep understanding of materials and chemistry. By following the outlined steps, manufacturers can produce high-quality discs tailored to specific applications, ensuring optimal performance and reliability in critical systems.