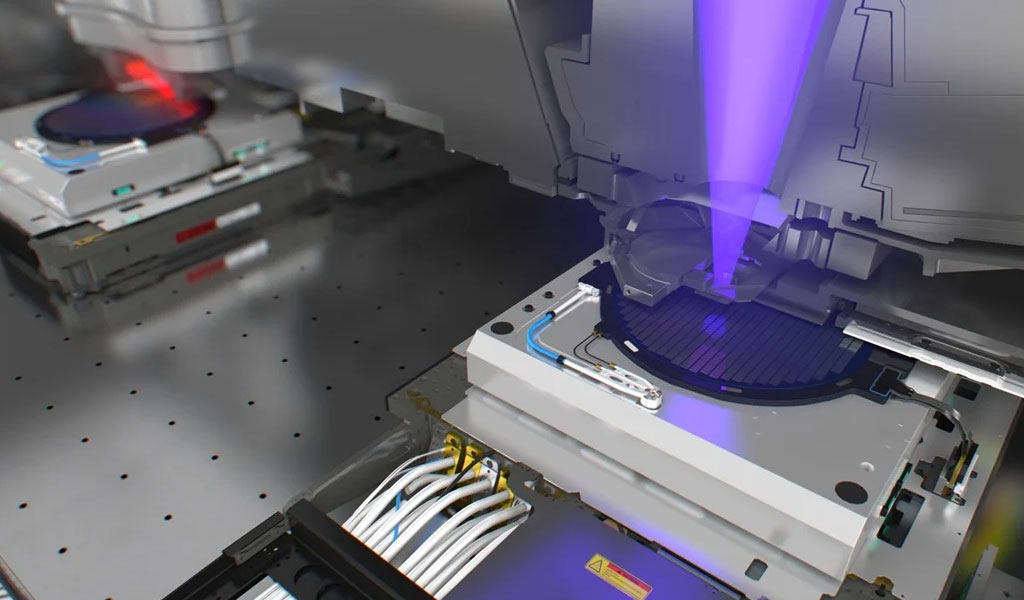
Etching electrical spring contacts is a specialized process in the field of precision manufacturing and micro-fabrication.
These components, crucial in a wide array of electronic devices, require precise tolerances, reliable conductivity, and mechanical resilience.
This article explores the methods, materials, tools, and applications of etching electrical spring contacts in detail, with insights into the underlying principles and best practices.
Materials for Electrical Spring Contacts
Electrical spring contacts are typically made from metals that offer a combination of high electrical conductivity, mechanical elasticity, and corrosion resistance. Common materials include:
- Copper and Copper Alloys: Copper is valued for its exceptional electrical conductivity, while alloys like beryllium copper add mechanical strength and resilience to withstand repeated deflections.
- Stainless Steel: Used for its corrosion resistance and moderate electrical conductivity, stainless steel is ideal for applications in harsh environments.
- Brass: An alloy of copper and zinc, brass is widely used for its good conductivity and ease of fabrication.
- Nickel Alloys: Alloys like Monel and Inconel offer excellent resistance to oxidation and wear, making them suitable for demanding applications.
- Silver and Gold-Plated Metals: Plated materials enhance conductivity and reduce contact resistance, particularly in low-voltage applications.
Overview of the Etching Process
Etching is a subtractive manufacturing process that removes material to create precise patterns or features on a metal surface. The process is commonly used for producing electrical spring contacts due to its ability to achieve tight tolerances and intricate designs. The etching process generally involves several key steps:
- Cleaning: The metal substrate is thoroughly cleaned to remove any surface contaminants, oils, or oxides that may interfere with the etching process.
- Masking: A protective resist is applied to the areas of the metal surface that should remain unetched. This resist can be a photoresist, stencil, or other types of masking material.
- Etching: The unprotected areas of the metal are exposed to an etching solution or plasma, which removes material to the desired depth.
- Stripping: The resist is removed, revealing the etched patterns or features.
- Post-Etching Treatment: The etched parts may undergo additional processing, such as cleaning, plating, or annealing, to enhance their properties.
Types of Etching Techniques
Chemical Etching
Chemical etching, also known as photochemical machining (PCM), is one of the most common methods for producing electrical spring contacts. This process involves the use of acid or alkaline solutions to dissolve unprotected metal. Key aspects include:
- Photoresist Application: The metal is coated with a photoresist material, which is then exposed to UV light through a photomask. The exposed areas are developed, leaving a pattern that protects the desired regions.
- Etching Solution: Common etchants include ferric chloride for copper alloys and nitric acid for stainless steel. The choice of etchant depends on the material and desired etching precision.
- Controlled Depth: The etching process is carefully monitored to ensure uniformity and precision.
Chemical etching is ideal for high-volume production due to its scalability and ability to produce complex geometries.
Electrochemical Etching
Electrochemical etching uses an electrical current to selectively remove metal ions from the substrate. This method offers greater control over the etching depth and is often used for intricate or high-precision applications. Key parameters include:
- Electrolyte Selection: The electrolyte solution facilitates ion transfer and must be compatible with the metal being etched.
- Current Density: The applied current density determines the rate of material removal and surface finish quality.
- Anodic vs. Cathodic Etching: The polarity of the workpiece affects the etching mechanism and resulting features.
Laser Etching
Laser etching employs focused laser beams to ablate material, offering unmatched precision and flexibility. Although less common for large-scale production, laser etching is invaluable for prototyping or applications requiring intricate patterns.
- Beam Control: Advanced systems allow precise control of laser intensity, spot size, and movement, enabling micro-etching on delicate components.
- Non-Contact Process: Laser etching is a non-contact technique, reducing the risk of mechanical deformation.
Plasma Etching
Plasma etching utilizes ionized gases to remove material at the atomic level. This method is particularly suitable for etching ultra-thin films or achieving extremely fine features.
- Reactive Gases: Gases like chlorine, fluorine, or oxygen react chemically with the metal surface, facilitating material removal.
- Vacuum Environment: Plasma etching is conducted in a vacuum chamber to maintain process consistency.
Design Considerations for Electrical Spring Contacts
When designing electrical spring contacts for etching, it is essential to consider the following factors:
- Material Thickness: The material thickness influences the choice of etching technique and achievable tolerances.
- Pattern Complexity: Etching is well-suited for complex geometries, but intricate designs may require more advanced masking and processing methods.
- Dimensional Tolerances: Tight tolerances are critical for ensuring the functionality and reliability of the contacts.
- Stress Relief: Post-etching treatments like annealing can help relieve residual stresses and improve mechanical performance.
Advantages of Etching for Electrical Spring Contacts
Etching offers several advantages over traditional machining methods, including:
- High Precision: Etching can achieve tolerances as tight as ±0.01 mm, making it suitable for micro-fabrication.
- Complex Geometries: The process allows the creation of intricate patterns and features that may be difficult or impossible with other techniques.
- Non-Mechanical Process: Etching does not involve physical cutting or deformation, reducing the risk of introducing mechanical stresses.
- Scalability: Chemical etching, in particular, is highly scalable, enabling cost-effective production of large quantities.
- Material Versatility: Etching is compatible with a wide range of metals and alloys, offering flexibility in material selection.
Applications of Etched Electrical Spring Contacts
Etched electrical spring contacts are widely used in various industries and applications, including:
- Consumer Electronics: Spring contacts are used in battery connectors, circuit boards, and mobile devices for reliable electrical connections.
- Automotive: Electrical spring contacts play a crucial role in sensors, switches, and control systems.
- Aerospace and Defense: High-precision spring contacts are employed in avionics, communication systems, and radar equipment.
- Medical Devices: Etched contacts are found in diagnostic equipment, implants, and monitoring devices, where precision and reliability are critical.
- Telecommunications: Spring contacts enable efficient signal transmission in networking equipment and communication devices.
Challenges and Solutions
Uniformity
Achieving uniform etching across large or complex parts can be challenging. Solutions include:
- Optimizing the etching solution composition and agitation.
- Ensuring consistent resist application and curing.
Undercutting
Undercutting occurs when the etchant removes material beneath the resist layer, affecting dimensional accuracy. To mitigate this:
- Use high-resolution photoresists and advanced masking techniques.
- Control etching time and solution concentration.
Environmental Considerations
Etching processes often involve hazardous chemicals. Proper waste management and the use of environmentally friendly etching solutions can address these concerns.