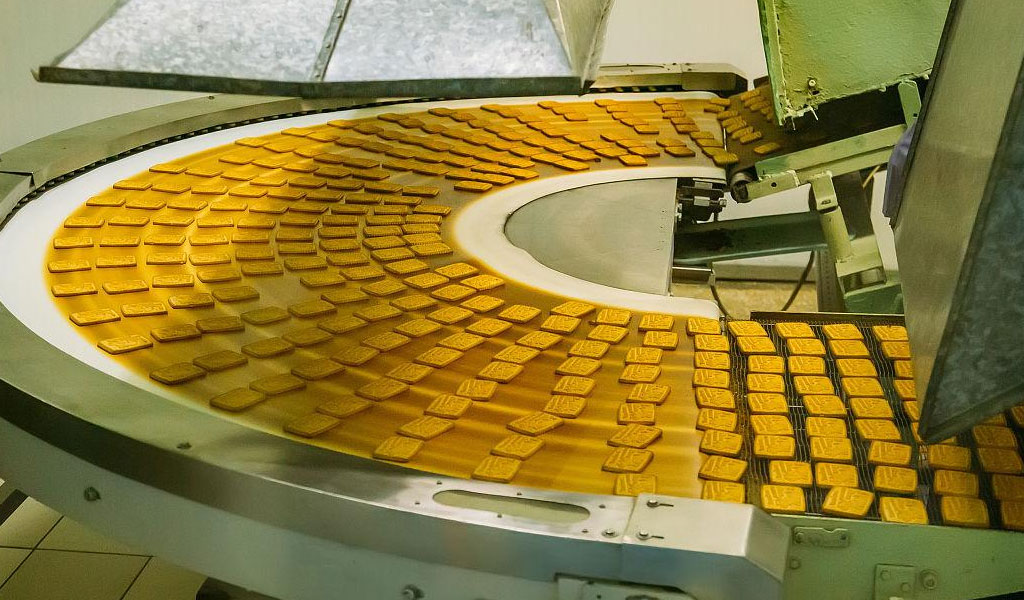
Etching on a conveyor system represents a fascinating intersection of industrial engineering, materials science, and precision manufacturing. This process involves the controlled removal of material from a substrate—typically metal, glass, or semiconductor wafers—while the workpiece is transported via a conveyor mechanism. Commonly employed in industries such as electronics, automotive manufacturing, and decorative arts, conveyor-based etching offers advantages in scalability, uniformity, and efficiency over traditional stationary etching methods. This article explores the principles, techniques, equipment, and applications of etching on a conveyor, delving into its scientific underpinnings, practical considerations.
Introduction to Conveyor-Based Etching
Etching, in its broadest sense, is a subtractive process used to selectively remove material from a surface to create patterns, designs, or functional features. Historically, etching has been performed manually or with stationary equipment, requiring individual handling of each workpiece. The advent of conveyor systems, however, revolutionized this practice by introducing continuous, automated material transport through the etching environment. Conveyor-based etching integrates mechanical motion with chemical or physical material removal, enabling high-throughput production suitable for modern industrial demands.
The conveyor itself is a motorized or gravity-driven system designed to move workpieces through various stages of the etching process—cleaning, masking, etching, rinsing, and drying—without interruption. This continuous flow reduces labor costs, minimizes human error, and ensures consistent exposure of the substrate to etching agents. The technique is particularly valuable in applications requiring precision, such as microelectronics, where uniformity across large batches of components is critical.
Conveyor etching can employ wet chemical methods, dry plasma techniques, or even laser-based approaches, depending on the material and desired outcome. Each method brings distinct advantages and challenges, which this article will explore in depth. By examining the scientific principles, equipment design, process parameters, and comparative analyses, readers will gain a comprehensive understanding of how to etch on a conveyor and its role in contemporary manufacturing.
Historical Context of Etching and Conveyor Integration
The origins of etching date back centuries, with early examples found in decorative metalwork during the Middle Ages. Artisans used acid solutions to engrave intricate designs into armor and jewelry, laying the groundwork for modern chemical etching. The Industrial Revolution in the 18th and 19th centuries brought mechanization to manufacturing, but etching remained a largely manual process until the 20th century.
Conveyor systems emerged during this period as a means to streamline production lines, most famously in Henry Ford’s automobile assembly plants in the early 1900s. The adaptation of conveyors to etching processes, however, gained traction later, particularly with the rise of the electronics industry in the mid-20th century. The need to produce printed circuit boards (PCBs) in large quantities spurred innovations in automated etching, where conveyors facilitated the movement of boards through chemical baths.
By the 1980s, conveyor etching had become a standard in semiconductor fabrication, with advancements in plasma etching and conveyor design further enhancing precision and scalability. Today, the technique is a cornerstone of industrial processes, supported by sophisticated control systems and materials science research that optimize its performance.
Scientific Principles of Etching on a Conveyor
Etching on a conveyor relies on a combination of chemical, physical, and mechanical principles. At its core, the process involves the selective removal of material from a substrate, guided by a mask or pattern that protects certain areas while exposing others to the etching agent. The conveyor introduces a dynamic element, ensuring that the substrate interacts uniformly with the etching medium over time.
Chemical Etching Mechanisms
In wet chemical etching, the most common conveyor-based method, an acidic or basic solution reacts with the substrate to dissolve unprotected material. For example, ferric chloride is widely used to etch copper in PCB manufacturing, following the reaction:
\ceCu+2FeCl3−>CuCl2+2FeCl2
The conveyor moves the substrate through a bath or spray of etchant, maintaining consistent exposure. The rate of material removal depends on factors such as etchant concentration, temperature, and substrate composition. Fick’s laws of diffusion govern the transport of etchant to the surface, while reaction kinetics determine the etching speed.
Physical Etching Mechanisms
Dry etching, such as plasma or ion beam etching, uses energetic particles to bombard the substrate, physically dislodging material. In a conveyor system, the workpiece passes through a plasma chamber where reactive gases (e.g., CF₄ or SF₆) are ionized to form a plasma. The conveyor ensures uniform exposure to the plasma, critical for achieving consistent etch depths in semiconductor wafers.
Mechanical Considerations
The conveyor’s motion introduces additional variables, such as speed and vibration, which must be controlled to prevent uneven etching. Laminar flow of etchant over the substrate, facilitated by the conveyor’s steady movement, minimizes turbulence that could lead to over-etching or under-etching. Mechanical engineering principles, including belt tension and roller alignment, ensure smooth transport without damaging delicate substrates.
Equipment for Conveyor-Based Etching
The equipment used in conveyor etching varies by method and application but generally includes several key components: the conveyor system, etching chamber, masking apparatus, and post-processing stations. Below is a detailed examination of each.
Conveyor System Design
The conveyor is the backbone of the process, typically consisting of a belt, rollers, or chain-driven mechanism. Materials such as stainless steel or chemical-resistant polymers (e.g., PTFE) are chosen for their durability against etchants. Conveyor speed is adjustable, ranging from a few centimeters per minute for precision etching to several meters per minute for high-volume production.
Modern conveyors incorporate sensors and programmable logic controllers (PLCs) to monitor and adjust speed, ensuring synchronization with etching conditions. For example, in PCB etching, a conveyor might operate at 1–2 m/min to balance throughput and etch uniformity.
Etching Chamber
The etching chamber houses the etching agent—liquid, gas, or laser—and is designed to contain and direct it onto the substrate. In wet etching, spray nozzles or immersion baths deliver the etchant, while plasma etching chambers use vacuum systems and electrodes to generate the plasma. Laser etching setups feature focused beams guided by mirrors or optics, with the conveyor positioning the workpiece precisely under the beam.
Masking Apparatus
Masking protects areas of the substrate that should not be etched. In conveyor systems, masks are applied before the workpiece enters the etching zone, often using photoresist in microelectronics or stencils in decorative applications. Automated mask application stations, integrated into the conveyor line, enhance efficiency by coating and curing the resist as the substrate moves.
Post-Processing Stations
After etching, the conveyor transports the substrate through rinsing, neutralization, and drying stages. Water jets remove residual etchant, while air knives or heaters dry the surface. These steps prevent contamination and prepare the workpiece for further processing or inspection.
Process Parameters in Conveyor Etching
Successful conveyor etching requires careful control of multiple parameters, each influencing the outcome. These include etchant properties, conveyor speed, temperature, and exposure time.
Etchant Properties
The choice of etchant depends on the substrate material. For instance, hydrofluoric acid etches glass, while nitric acid is used for stainless steel. Concentration and pH affect the etch rate; a 10% increase in ferric chloride concentration might double the etch rate for copper, necessitating precise dosing systems on the conveyor line.
Conveyor Speed
Speed determines the duration of exposure to the etchant. Too fast a speed may result in under-etching, while too slow a speed risks over-etching. For a typical PCB process, a speed of 1.5 m/min with a 2-meter-long etching chamber yields a 60-second exposure, optimized for a 50 µm copper layer.
Temperature
Temperature accelerates chemical reactions in wet etching, following the Arrhenius equation:
k=Ae−Ea/RT
where k k k is the rate constant, A A A is a pre-exponential factor, Ea E_a Ea is the activation energy, R R R is the gas constant, and T T T is the absolute temperature. A 10°C increase might halve the etching time, but excessive heat can degrade the mask or conveyor materials.
Exposure Time
Exposure time is a function of conveyor speed and chamber length. For plasma etching, a 30-second exposure at 0.5 m/min in a 0.25-meter chamber might suffice for a 100 nm silicon etch, adjustable based on real-time monitoring.
Techniques of Conveyor Etching
Conveyor etching encompasses several techniques, each suited to specific materials and applications. The three primary methods—wet chemical, dry plasma, and laser etching—are detailed below.
Wet Chemical Etching
Wet etching involves immersing or spraying the substrate with a liquid etchant as it moves along the conveyor. This method is cost-effective and widely used for metals and glass. The conveyor typically passes through a series of tanks or spray zones, with adjustable nozzles controlling etchant flow. For example, in PCB production, copper-clad boards are etched with ferric chloride, removing 35–70 µm of copper in 1–2 minutes.
Advantages include simplicity and scalability, but challenges include waste disposal and isotropic etching, which limits feature resolution.
Dry Plasma Etching
Plasma etching uses ionized gases to remove material anisotropically, ideal for microelectronics. The conveyor moves wafers through a vacuum chamber where radiofrequency (RF) energy ionizes gases like SF₆, etching silicon with sub-micron precision. This method excels in uniformity and control, though equipment costs are higher than wet etching.
Laser Etching
Laser etching employs focused light to ablate material, offering unmatched precision for small-scale features. The conveyor positions the substrate under a laser head, which scans or pulses to create patterns. Used in jewelry and microfluidics, laser etching is non-contact and produces minimal waste, but its throughput is lower than chemical methods.
Applications of Conveyor Etching
Conveyor etching finds applications across diverse industries, leveraging its automation and precision.
Electronics Manufacturing
In electronics, conveyor etching produces PCBs, integrated circuits, and MEMS devices. Wet etching dominates PCB fabrication, while plasma etching is critical for semiconductor wafers, enabling features as small as 2 nm in advanced nodes (as of 2025).
Automotive Industry
Automotive parts, such as gears and sensors, are etched on conveyors to enhance durability or add microtextures. Stainless steel components might undergo nitric acid etching to improve corrosion resistance.
Decorative and Artistic Uses
In decorative arts, conveyor etching creates intricate designs on metal or glass panels. Continuous processing allows mass production of etched jewelry or architectural elements.
Comparative Analysis of Etching Techniques
To elucidate the differences between wet, plasma, and laser etching on conveyors, the following table provides a detailed comparison based on key metrics.
Parameter | Wet Chemical Etching | Dry Plasma Etching | Laser Etching |
---|---|---|---|
Material Compatibility | Metals, glass, some polymers | Semiconductors, metals | Metals, glass, ceramics |
Feature Resolution | 10–100 µm (isotropic) | <1 µm (anisotropic) | 1–10 µm |
Throughput | High (100s of parts/min) | Moderate (10s of parts/min) | Low (1–10 parts/min) |
Cost | Low (chemicals, simple setup) | High (vacuum, RF systems) | Moderate (laser equipment) |
Uniformity | Moderate (flow-dependent) | High (plasma control) | High (beam precision) |
Waste Generation | High (liquid waste) | Low (gas byproducts) | Minimal (vaporized material) |
Conveyor Speed Range | 0.5–5 m/min | 0.1–1 m/min | 0.01–0.5 m/min |
This table highlights trade-offs: wet etching excels in cost and throughput, plasma etching in precision, and laser etching in flexibility.
Recent Advancements in Conveyor Etching
Recent developments have enhanced conveyor etching’s capabilities, driven by industry demands for efficiency and miniaturization.
Automation and AI Integration
Artificial intelligence now optimizes conveyor speed and etchant delivery in real time. Machine learning algorithms analyze etch depth via inline sensors, adjusting parameters to reduce defects by up to 15% compared to manual control.
Eco-Friendly Etchants
Research into biodegradable etchants, such as citric acid-based solutions, has reduced environmental impact in wet etching, with pilot conveyor systems achieving 90% waste recyclability.
Hybrid Systems
Hybrid conveyor setups combining wet and plasma etching in a single line have emerged, allowing sequential processing for complex substrates. A 2024 study demonstrated a 20% increase in throughput for PCB-silicon hybrid components.
Practical Considerations for Implementing Conveyor Etching
Implementing conveyor etching requires addressing safety, maintenance, and scalability.
Safety Protocols
Chemical etchants pose risks of burns or inhalation; conveyor systems must include fume hoods and emergency stops. Plasma and laser systems require shielding to protect operators from radiation.
Maintenance
Regular cleaning of conveyor belts and etching chambers prevents contamination. For wet systems, etchant replenishment every 500–1000 parts maintains consistency.
Scalability
Scaling from prototype to production involves adjusting conveyor length and speed. A small-scale system (5 m long) might handle 50 parts/hour, while a 20 m system could process 500 parts/hour.
Conclusion
Conveyor etching faces challenges such as mask durability, etchant disposal, and equipment cost. Masks degrade under prolonged exposure, requiring frequent replacement. Wet etching generates hazardous waste, necessitating treatment facilities. High initial costs for plasma or laser systems may deter small-scale adopters.
The future of conveyor etching lies in nanotechnology and sustainability. Advances in nanoscale etching could enable 1 nm features by 2030, while green chemistry initiatives aim to eliminate toxic etchants entirely.
Etching on a conveyor combines the precision of material removal with the efficiency of automated transport, making it indispensable in modern manufacturing. From its chemical and physical foundations to its diverse applications, this process exemplifies the synergy of science and engineering. As technology evolves, conveyor etching will continue to adapt, meeting the demands of an increasingly complex industrial landscape.