In the realm of heat exchange technology, plate heat exchangers stand out as a versatile and efficient solution for transferring heat between two fluids. These exchangers consist of a series of thin metal plates arranged in a manner that facilitates the exchange of thermal energy between the fluids without allowing them to mix. To optimize the performance and durability of plate heat exchangers, engineers must consider various manufacturing techniques. Among these techniques, chemical etching emerges as a pivotal method for enhancing the functionality and efficiency of these devices.
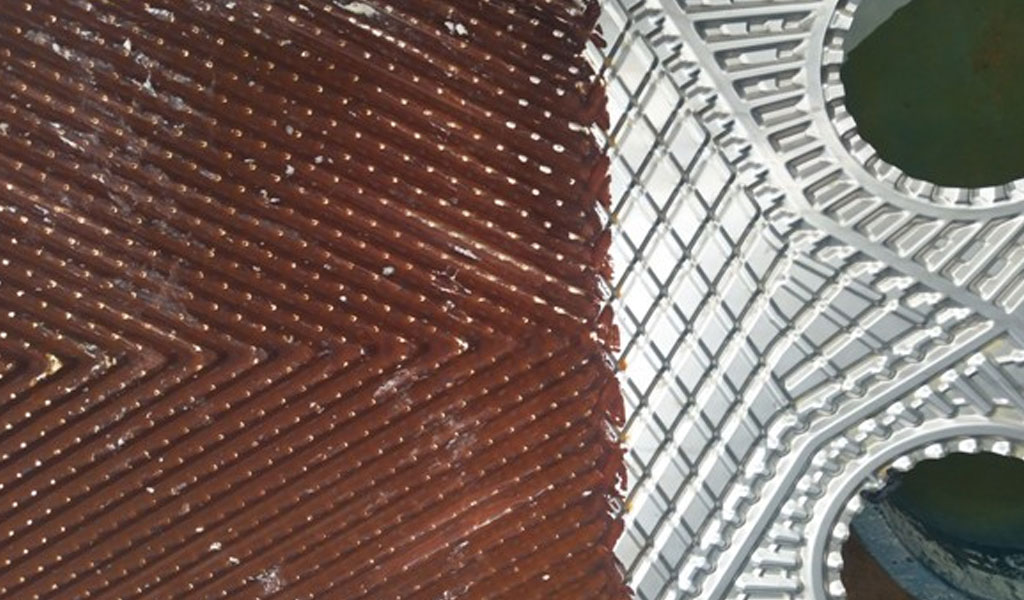
Understanding Plate Heat Exchangers
Before delving into the significance of chemical etching, it’s imperative to grasp the fundamental principles of plate heat exchangers.
These devices operate on the principle of heat transfer through metal plates. Fluids flow through alternating channels formed by these plates, enabling the transfer of heat from one fluid to another.
The design of plate heat exchangers allows for high rates of heat transfer due to their large surface area relative to volume. This results in improved efficiency and reduced energy consumption compared to traditional heat exchange methods. However, the efficiency and performance of these devices can be further optimized through precise manufacturing techniques.
The Role of Chemical Etching in Plate Heat Exchangers
Chemical etching is a process that involves selectively removing material from the surface of metal plates using chemical solutions. This technique allows for intricate and precise patterns to be etched onto the plates, creating customized designs that enhance the performance of plate heat exchangers in several ways.
1. Improved Heat Transfer Efficiency
By employing chemical etching, engineers can create intricate patterns and structures on the surface of the plates. These patterns, such as microchannels or turbulators, significantly increase turbulence and disrupt laminar flow within the fluid channels. This disruption enhances heat transfer rates by promoting better mixing and reducing boundary layers, thereby improving overall efficiency.
2. Enhanced Fluid Flow Control
The etching process enables engineers to control the flow characteristics of fluids within the heat exchanger. By adjusting the shape, size, and arrangement of channels, it becomes possible to optimize fluid flow patterns. This control over flow dynamics minimizes pressure drops, improves flow distribution, and mitigates fouling, thereby extending the operational lifespan of the heat exchanger.
3. Customization for Specific Applications
Chemical etching offers engineers the flexibility to tailor plate designs according to specific application requirements. Different industries demand unique heat exchange parameters, and through etching, engineers can create specialized plates that cater to these diverse needs. Whether it’s for pharmaceuticals, food processing, HVAC systems, or chemical manufacturing, customized plate designs optimize performance for specific conditions.
4. Corrosion Resistance and Material Integrity
Etching can also be utilized to improve the corrosion resistance of plate materials. Engineers can selectively remove vulnerable areas or apply protective coatings through the etching process, enhancing the durability and longevity of the heat exchanger. Moreover, this process can be performed without compromising the structural integrity of the material.
Advancements in Chemical Etching Techniques
The evolution of technology has led to advancements in chemical etching processes, offering engineers more sophisticated methods to achieve precise plate designs. Laser-assisted chemical etching, for instance, combines the accuracy of laser technology with the chemical etching process to create intricate and highly customized plate patterns. This innovative technique allows for greater control over the etching process, resulting in enhanced heat transfer and fluid dynamics within the plate heat exchangers.
Challenges and Considerations
While chemical etching presents numerous advantages, engineers must also consider certain challenges associated with this process. The selection of suitable materials, environmental considerations related to chemical disposal, and ensuring consistent quality in large-scale production are some of the challenges that require careful attention.
Additionally, the cost-effectiveness of chemical etching compared to other manufacturing methods needs to be evaluated. Despite initial investment considerations, the long-term benefits of improved efficiency and performance may outweigh the upfront costs.
Conclusion
In conclusion, plate heat exchangers play a vital role in various industries where efficient heat transfer is crucial. Chemical etching stands out as a pivotal technique that empowers engineers to optimize the performance, efficiency, and durability of these devices. Through precise customization and control over plate designs, chemical etching enhances heat transfer efficiency, fluid flow dynamics, and corrosion resistance. Advancements in etching technologies continue to expand the possibilities, allowing engineers to tailor plate heat exchangers to meet specific application requirements. As the pursuit of energy efficiency and sustainability intensifies, the role of chemical etching in advancing heat exchange technology remains indispensable for engineers seeking optimal solutions in the field.