In today’s rapidly evolving industrial landscape, manufacturing processes are constantly adapting to meet the growing demands for efficiency, flexibility, and cost-effectiveness. One of the key advancements in manufacturing technology that has gained significant attention is Hybrid Manufacturing. This innovative approach combines traditional subtractive manufacturing techniques, such as milling and turning, with additive manufacturing processes like 3D printing. The result is a powerful synergy that allows industries to maximize efficiency, reduce production costs, and push the boundaries of design and innovation.
In this comprehensive article, we will delve into the world of hybrid manufacturing, exploring its various aspects, benefits, applications, and challenges. We will examine how hybrid manufacturing is transforming industries and helping companies stay competitive in an ever-changing market. By the end of this article, you’ll have a deep understanding of what hybrid manufacturing is and how it can revolutionize your operations.
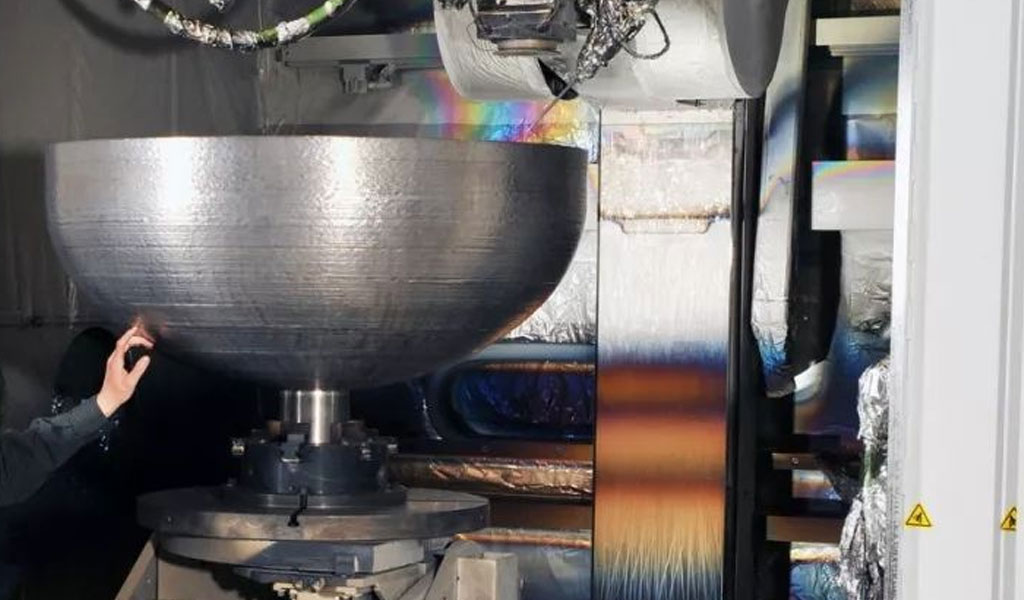
A Brief History of Manufacturing
To understand the significance of hybrid manufacturing, it’s essential to first examine the historical evolution of manufacturing processes and the driving forces behind their transformation.
Manufacturing has come a long way from its origins in the pre-industrial era, when skilled artisans crafted products by hand.
The first industrial revolution, marked by the advent of mechanization, steam power, and the textile industry, paved the way for mass production. Subsequent revolutions introduced new technologies, such as electricity, the assembly line, and automation, which significantly increased production capacity and efficiency.
The Second Industrial Revolution, in the late 19th and early 20th centuries, saw the widespread adoption of electricity, steel, and the combustion engine. Mass production techniques were developed, notably by companies like Ford, that enabled the efficient production of standardized goods. This period marked a significant shift from craft production to mass production and set the stage for further advancements in manufacturing.
The Third Industrial Revolution, often referred to as the digital revolution, occurred in the latter half of the 20th century. It was characterized by the widespread use of computers and automation. Computer Numerical Control (CNC) machines allowed for precise and automated control of machining tools, significantly increasing manufacturing precision and flexibility. Additionally, Computer-Aided Design (CAD) and Computer-Aided Manufacturing (CAM) systems revolutionized product design and production processes.
In recent decades, the digital revolution and the rise of computer-aided design and manufacturing (CAD/CAM) systems have further transformed the landscape. The introduction of Computer Numerical Control (CNC) machines and 3D printing marked a significant shift toward precision and customization in manufacturing processes.
The Need for Advanced Manufacturing Technologies
In today’s highly competitive global marketplace, businesses must continually innovate and adapt to changing customer demands and technological advancements. Efficiency, flexibility, and cost-effectiveness are paramount. Traditional manufacturing processes often struggle to meet these demands, leading to the need for more advanced manufacturing technologies.
Enterprises seek ways to optimize their operations, reduce waste, minimize lead times, and enhance product quality. The limitations of conventional manufacturing processes have driven the development of advanced technologies, such as hybrid manufacturing, to address these challenges.
Hybrid manufacturing represents the latest phase in this ongoing evolution, combining the strengths of subtractive and additive manufacturing to create a versatile and powerful solution. This approach enables manufacturers to achieve a level of efficiency, flexibility, and cost-effectiveness that was previously unattainable with traditional methods. In the following sections of this article, we will explore how hybrid manufacturing accomplishes these goals and examine its applications, benefits, challenges, and future potential.
What Is Hybrid Manufacturing?
Now that we have established the historical context and the need for advanced manufacturing technologies, it’s time to delve into the core concept of hybrid manufacturing.
Hybrid manufacturing is a cutting-edge approach that integrates subtractive and additive manufacturing techniques within a single, unified process. Subtractive manufacturing methods, such as milling and turning, involve removing material from a solid workpiece to create the desired shape. On the other hand, additive manufacturing, or 3D printing, builds parts layer by layer from digital design data.
The primary idea behind hybrid manufacturing is to harness the benefits of both approaches while mitigating their individual limitations. By fusing subtractive and additive techniques, manufacturers can achieve enhanced precision, design complexity, material versatility, and operational efficiency.
Key Components and Processes
To understand hybrid manufacturing fully, it’s crucial to explore its key components and the processes involved. These components work in synergy to create a powerful and flexible manufacturing system.
Additive Manufacturing Unit
The additive manufacturing unit is a critical component of hybrid manufacturing. This unit is responsible for the 3D printing or additive manufacturing part of the process. It includes various types of 3D printers, such as Fused Deposition Modeling (FDM), Stereolithography (SLA), Selective Laser Sintering (SLS), and more. These 3D printers are capable of building up structures layer by layer using a variety of materials, including plastics, metals, ceramics, and composites.
Subtractive Manufacturing Unit
The subtractive manufacturing unit is another essential element in the hybrid manufacturing process. This unit includes traditional CNC machines, such as milling and turning centers. These machines are responsible for removing excess material from the workpiece, creating the final shape with high precision. Subtractive manufacturing is known for its ability to produce parts with tight tolerances and smooth surface finishes.
Control and Integration
Advanced control software and hardware are crucial for ensuring seamless coordination between the additive and subtractive processes in hybrid manufacturing. This integration allows for precise toolpath planning and real-time adjustments. Modern manufacturing software often includes Computer-Aided Manufacturing (CAM) systems that generate toolpaths for both additive and subtractive operations. These systems facilitate efficient and accurate manufacturing processes.
Materials
Hybrid manufacturing can utilize a wide range of materials, which is one of its key strengths. The choice of material depends on the specific application and requirements. Materials commonly used in hybrid manufacturing include metals, plastics, ceramics, and composites. The ability to work with various materials makes hybrid manufacturing a versatile solution for a wide range of industries, from aerospace to healthcare and beyond.
The hybrid manufacturing process typically involves the following steps:
- Design: Engineers create a 3D model of the desired part or component using CAD software. This model serves as the blueprint for the hybrid manufacturing process.
- Additive Manufacturing: The 3D printing unit begins the additive manufacturing process by building the initial structure layer by layer. The 3D printer follows the digital design, adding material according to the model’s specifications.
- Subtractive Manufacturing: Once the additive stage is complete, the subtractive unit takes over. This unit uses CNC machinery to remove excess material and refine the part’s shape to meet precise specifications. The subtractive stage ensures that the part’s dimensions and surface finish are accurate.
- Quality Control: Various quality control measures are performed to ensure the final part meets the required standards. This can include dimensional checks, material inspections, and non-destructive testing.
- Post-Processing: Depending on the specific requirements, additional finishing steps may be necessary to enhance the part’s properties. This could involve surface treatment, coating, or other secondary processes to improve the part’s appearance or functionality.
- Final Product: The end result is a hybrid-manufactured part that combines the precision of subtractive machining with the design freedom of additive manufacturing. The part is ready for use in various applications, depending on the industry and the intended purpose.
Understanding these key components and processes is fundamental to grasping the capabilities and advantages of hybrid manufacturing. In the following sections of this article, we will delve deeper into the benefits and applications of hybrid manufacturing, as well as the challenges it may present and its potential future developments.
Benefits of Hybrid Manufacturing
Hybrid manufacturing offers a plethora of benefits that make it an attractive choice for various industries. In this section, we’ll explore five key advantages of adopting hybrid manufacturing techniques:
Increased Efficiency
Efficiency is a paramount concern in modern manufacturing, and hybrid manufacturing excels in this regard. By combining both additive and subtractive processes into a single, integrated workflow, manufacturers can streamline production and reduce the number of steps required to produce a component. This leads to increased operational efficiency, as well as significant time and cost savings.
Key factors contributing to increased efficiency include:
- Reduced Setup Times: Transitioning between additive and subtractive processes can be accomplished with minimal downtime, thanks to integrated software and hardware.
- Material Optimization: Hybrid manufacturing allows for precise control over the amount of material used. By adding material layer by layer, less waste is generated, which reduces material costs.
- Multi-Tasking Machines: Hybrid machines are often equipped with multi-tasking capabilities, which means that a single machine can perform various operations without the need for part transfer. This results in a smoother, more efficient production process.
Cost Reduction
Cost reduction is a driving force for many manufacturers, and hybrid manufacturing delivers on this front in several ways:
- Lower Material Costs: As mentioned earlier, the precise control over material usage in the additive stage reduces waste, leading to lower material costs. This is particularly significant when working with expensive materials, such as certain metals or high-performance polymers.
- Reduced Labor Costs: The integrated and automated nature of hybrid manufacturing reduces the need for manual intervention, which results in lower labor costs. Operators can oversee multiple machines simultaneously, further optimizing labor resources.
- Enhanced Resource Utilization: Hybrid manufacturing maximizes the utilization of equipment, reducing the need for multiple dedicated machines. This has the added benefit of decreasing capital expenditures.
Improved Design and Functionality
Hybrid manufacturing empowers designers to push the boundaries of what’s possible by combining subtractive precision with additive freedom. This results in components with enhanced design complexity and functionality:
- Complex Geometries: Additive manufacturing allows for the creation of highly complex geometries that would be challenging or impossible to achieve with traditional subtractive methods. These intricate designs can improve the performance and efficiency of parts.
- Lightweight Structures: Engineers can design lightweight components with optimized internal structures. These structures reduce overall weight while maintaining or even improving structural integrity. This is especially valuable in industries like aerospace and automotive.
- Customization: Hybrid manufacturing enables mass customization, where each part can be tailored to specific requirements. This is beneficial in applications such as medical implants and consumer goods.
Reduced Lead Times
Traditional manufacturing processes, particularly for complex or customized components, often involve lengthy lead times. Hybrid manufacturing accelerates the production cycle through integration:
- Faster Turnaround: By combining additive and subtractive processes, hybrid manufacturing eliminates the need to transfer parts between different machines or facilities, reducing lead times significantly.
- Real-Time Adjustments: Advanced control and monitoring systems allow for real-time adjustments, ensuring that production remains on track and errors can be corrected promptly.
- Just-in-Time Production: Hybrid manufacturing supports just-in-time (JIT) production, where parts are manufactured as needed, minimizing inventory costs and reducing lead times even further.
Sustainability
Sustainability is an increasingly important consideration for many industries, and hybrid manufacturing contributes to environmental goals in several ways:
- Reduced Material Waste: Additive manufacturing minimizes material waste by building parts layer by layer. This is particularly important when working with expensive or hard-to-source materials.
- Energy Efficiency: Hybrid manufacturing often uses energy-efficient equipment, and the integrated process reduces energy consumption compared to multiple standalone machines.
- Localized Production: By reducing lead times and supporting JIT production, hybrid manufacturing can enable more localized manufacturing, reducing the carbon footprint associated with long-distance transportation.
- Recyclability: Some hybrid manufacturing processes can use recyclable materials, further reducing their environmental impact.
By combining these benefits, hybrid manufacturing emerges as a transformative approach with the potential to revolutionize industries, from aerospace and automotive to healthcare and consumer goods. In the following sections of this article, we will explore the diverse applications of hybrid manufacturing and examine the challenges it may present in implementation.
Implementing Hybrid Manufacturing in Your Business
Implementing hybrid manufacturing in your business can be a transformative process, but it requires careful planning and consideration. In this section, we’ll outline the essential steps to get started, the importance of cost analysis, and the necessity of training and skill development for a successful integration.
Steps to Get Started
Transitioning to hybrid manufacturing involves a series of steps to ensure a smooth and effective implementation. Here are the key steps to get started:
- 1. Assess Your Needs and Objectives: Begin by identifying your specific needs, goals, and the areas of your business where hybrid manufacturing can make the most significant impact. Consider the types of components you produce and how hybrid manufacturing can enhance your processes.
- 2. Select the Right Equipment: Research and select the appropriate hybrid manufacturing equipment for your business. Consider factors like the size of the components you manufacture, the materials you work with, and your production volume. Choose a hybrid machine that aligns with your requirements.
- 3. Develop a Hybrid Manufacturing Strategy: Create a comprehensive strategy that outlines how hybrid manufacturing will integrate with your existing processes. Determine the sequence of additive and subtractive operations, tooling requirements, and quality control procedures.
- 4. Software Integration: Ensure that your existing CAD/CAM and other manufacturing software are compatible with your hybrid manufacturing equipment. You may need to invest in or update software to seamlessly integrate both additive and subtractive operations.
- 5. Training and Skill Development: As detailed in the next section, invest in training for your staff to build the necessary skills for operating and maintaining hybrid manufacturing equipment.
- 6. Quality Control and Process Validation: Develop quality control protocols to ensure that components meet the required standards. Validate your hybrid manufacturing process through testing and inspections.
- 7. Workforce Transition: Implementing hybrid manufacturing may involve changes in your workforce’s roles and responsibilities. Ensure that your team understands and adapts to these changes effectively.
- 8. Pilot Projects: Begin with small-scale pilot projects to gain experience and assess the performance of your hybrid manufacturing processes. This will help identify any issues or optimizations required.
- 9. Scaling Up: After successful pilot projects, gradually scale up your hybrid manufacturing operations. Monitor progress and make adjustments as necessary to optimize efficiency and quality.
- 10. Continuous Improvement: Implement a culture of continuous improvement within your organization. Encourage feedback from your team and gather data to make ongoing refinements to your hybrid manufacturing processes.
Cost Analysis
Before integrating hybrid manufacturing into your business, a thorough cost analysis is essential. It involves assessing the financial implications, benefits, and long-term returns on investment. Here are the key considerations for cost analysis:
- Initial Investment: Determine the capital required for purchasing hybrid manufacturing equipment, software, and any infrastructure modifications. Compare this to your available budget and financing options.
- Operating Costs: Consider ongoing operating costs, including material costs, energy consumption, labor, and maintenance. Evaluate how hybrid manufacturing will impact these expenses compared to your current manufacturing processes.
- Return on Investment (ROI): Calculate the expected ROI by comparing the costs of implementing hybrid manufacturing to the anticipated benefits, such as increased efficiency, reduced lead times, and improved product quality.
- Cost Savings: Identify areas where hybrid manufacturing can lead to cost savings. These may include reduced material waste, labor efficiency, and the ability to produce customized, higher-value components.
- Market Opportunities: Consider the potential for market growth and new business opportunities that hybrid manufacturing can create. This includes the ability to serve niche markets or offer specialized products.
- Competitive Advantage: Assess how hybrid manufacturing can provide a competitive edge in terms of innovation, flexibility, and the ability to meet customer demands more efficiently.
A comprehensive cost analysis will help you make informed decisions about integrating hybrid manufacturing into your business. It will also serve as a reference point for evaluating the actual financial impact of the implementation as you move forward.
Training and Skill Development
The successful adoption of hybrid manufacturing hinges on having a skilled and knowledgeable workforce. Your team will need the expertise to operate, program, and maintain hybrid manufacturing equipment. Here’s how you can address the training and skill development aspect:
- Training Programs: Invest in training programs for your existing staff or hire individuals with relevant skills. These programs should cover the operation of both additive and subtractive equipment, software utilization, and quality control.
- Cross-Training: Consider cross-training your employees in both additive and subtractive manufacturing techniques. This ensures that they can seamlessly switch between processes as needed, maximizing efficiency.
- Certification: Depending on your industry and region, certification programs for hybrid manufacturing may be available. Certifications can validate the skills of your team and demonstrate your commitment to quality.
- Ongoing Education: Encourage your team to stay up-to-date with the latest developments in hybrid manufacturing. Consider providing access to educational resources, conferences, and workshops.
- Specialized Roles: Identify team members who can specialize in hybrid manufacturing operations, programming, or maintenance. Having experts in these areas can be invaluable for troubleshooting and process optimization.
- Collaboration: Consider partnering with educational institutions or hybrid manufacturing experts to provide additional training and expertise to your team.
The skill development of your workforce is an ongoing process. It’s crucial to cultivate a culture of learning and continuous improvement to fully harness the potential of hybrid manufacturing. Your well-trained team will be better equipped to adapt to new challenges and take advantage of emerging opportunities.
In conclusion, implementing hybrid manufacturing in your business is a strategic decision that can significantly enhance your production processes, reduce costs, and improve product quality. By following the steps to get started, conducting a comprehensive cost analysis, and investing in training and skill development, you can ensure a smooth and successful integration of hybrid manufacturing into your operations.
Conclusion
Hybrid manufacturing represents a groundbreaking advancement in the world of manufacturing, offering a holistic approach that combines the strengths of both subtractive and additive manufacturing techniques. In this comprehensive article, we have explored the evolution of manufacturing, the need for advanced manufacturing technologies, and delved deeply into the concept and key components of hybrid manufacturing. We’ve also outlined the significant benefits that hybrid manufacturing brings to the table, including increased efficiency, cost reduction, improved design and functionality, reduced lead times, and sustainability.
The applications of hybrid manufacturing are vast and diverse, spanning industries like aerospace, automotive, medical and healthcare, consumer goods, defense and military, as well as customized and prototyping sectors. This versatile technology empowers businesses to achieve new levels of efficiency, precision, and customization while staying competitive in an ever-changing market.
When it comes to implementing hybrid manufacturing in your business, a well-thought-out strategy is essential. Starting with a clear assessment of your needs and objectives, selecting the right equipment, and developing a comprehensive plan are crucial steps. Cost analysis allows you to understand the financial implications and return on investment, while investing in training and skill development ensures that your workforce is well-equipped to operate and maintain hybrid manufacturing equipment.
The future of manufacturing is dynamic, and hybrid manufacturing is at the forefront of this evolution. As technology continues to advance, we can expect even more innovative solutions that further enhance the capabilities of hybrid manufacturing and its adoption across various industries.
Incorporating hybrid manufacturing into your business is not just an upgrade; it’s a transformation. It’s a commitment to efficiency, sustainability, and quality. By embracing this innovative approach, you can position your business at the forefront of modern manufacturing, ready to tackle the challenges and opportunities that lie ahead.