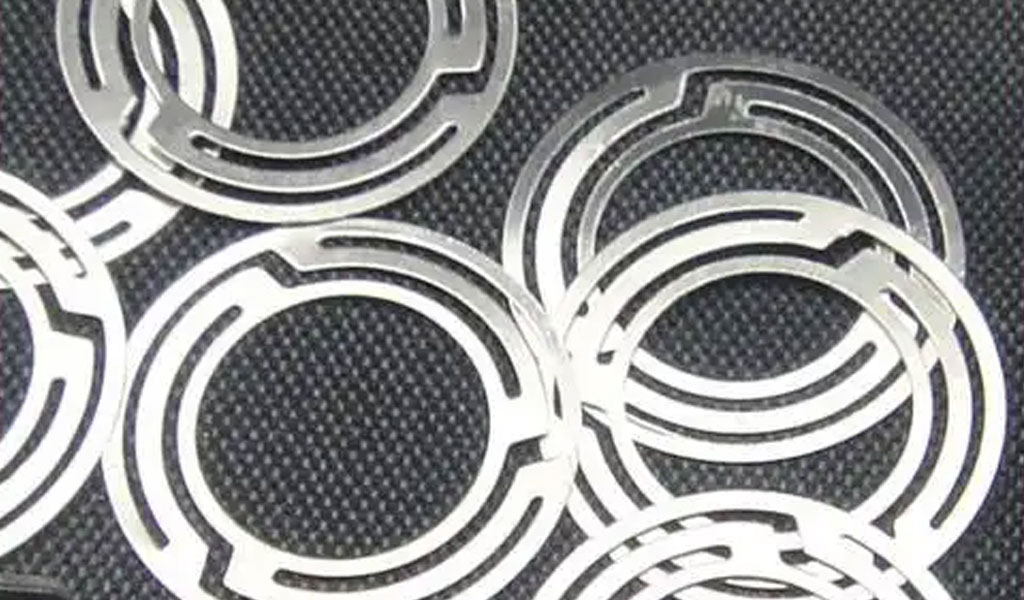
Metal etching, a subtractive manufacturing process, has emerged as a pivotal technique in the production of micro springs—tiny, precision-engineered components critical to industries such as aerospace, medical devices, electronics, and automotive engineering. Micro springs, typically ranging from micrometers to millimeters in scale, serve as essential elements in mechanisms requiring elasticity, force transmission, or energy storage at a miniature level. Unlike traditional mechanical methods like coiling or stamping, metal etching leverages chemical or electrochemical processes to selectively remove material from a metal substrate, offering unparalleled precision and the ability to craft intricate geometries unachievable through conventional means.
This article delves into the science, methodologies, applications, and comparative analyses of metal etching as applied to micro spring fabrication, providing a comprehensive exploration of this advanced manufacturing paradigm.
metal-etch.com
The process of metal etching, often referred to as chemical milling or photochemical machining (PCM), traces its roots to early industrial practices but has evolved significantly with advancements in materials science and microfabrication technologies. For micro springs, etching provides a non-contact method that minimizes mechanical stress, preserves material properties, and enables the production of high-aspect-ratio structures. These attributes are particularly advantageous when working with metals such as stainless steel, titanium, copper alloys, and nickel-based alloys, which are commonly employed in micro spring applications due to their mechanical strength, corrosion resistance, and elasticity.
This article aims to elucidate the principles of metal etching, the specific adaptations for micro spring production, and the broader implications for precision engineering. Through detailed sections and comparative tables, readers will gain a thorough understanding of how this technique shapes modern manufacturing landscapes.
Historical Context of Metal Etching
The origins of metal etching can be traced back to the decorative arts of the Middle Ages, where artisans used acidic solutions to engrave intricate designs onto armor and jewelry. However, its transition into an industrial process began in the 19th century with the advent of chemical milling for aerospace components. By the mid-20th century, the development of photolithography—a process borrowed from the semiconductor industry—revolutionized metal etching, enabling the precise patterning required for microscale components like micro springs.
In the context of micro springs, the need for miniaturization in the late 20th and early 21st centuries drove innovations in etching technologies. Traditional spring manufacturing, reliant on mechanical winding or stamping, struggled to meet the demands of microelectromechanical systems (MEMS) and other high-precision applications. Metal etching emerged as a solution, offering a scalable, repeatable method to produce springs with dimensions as small as a few micrometers. Today, it stands as a cornerstone of microfabrication, supported by advancements in photoresist materials, etching chemistries, and process control.
Fundamentals of Metal Etching
Metal etching involves the controlled removal of material from a metal substrate using a chemical etchant, typically an acid, base, or salt solution. The process begins with the preparation of a metal sheet, often a thin foil of uniform thickness, which is cleaned to remove contaminants. A protective layer, known as a photoresist, is then applied to the surface. This photoresist is patterned using photolithography, where ultraviolet (UV) light is projected through a mask onto the resist, selectively hardening or softening it based on the design. The unexposed areas are washed away, exposing the underlying metal to the etchant, which dissolves the unprotected regions.
For micro springs, the etching process must account for factors such as isotropy (uniform etching in all directions) versus anisotropy (directional etching), etch rate, and undercutting—the lateral erosion beneath the photoresist edges. These parameters influence the final geometry, tolerances, and mechanical properties of the springs. Common etchants include ferric chloride for stainless steel, nitric acid for copper alloys, and hydrofluoric acid for titanium, each tailored to the metal’s chemical reactivity.
Types of Metal Etching Techniques
Several etching techniques are employed in micro spring production, each with distinct advantages and limitations. Below, we explore the primary methods:
Wet Chemical Etching
Wet chemical etching, the most widely used approach, involves immersing the metal substrate in a liquid etchant. The process is cost-effective, scalable, and suitable for a variety of metals. For micro springs, wet etching excels in producing planar structures, such as flat spiral springs or cantilever designs, where the spring is etched from a single sheet. However, its isotropic nature can lead to undercutting, which may compromise dimensional accuracy in high-precision applications.
Dry Etching
Dry etching, encompassing techniques like plasma etching and reactive ion etching (RIE), uses gaseous etchants rather than liquids. This method offers greater control over anisotropy, enabling the creation of vertical sidewalls and complex 3D geometries. For micro springs requiring high aspect ratios—such as helical springs etched from thicker substrates—dry etching provides superior precision. Its drawbacks include higher equipment costs and slower etch rates, making it less common for large-scale production.
Electrochemical Etching
Electrochemical etching combines chemical reactions with an electric current to enhance material removal. By applying a voltage between the metal (anode) and a cathode in an electrolyte solution, the process achieves localized etching with minimal undercutting. This technique is particularly useful for micro springs made from conductive alloys, offering a balance between precision and throughput. However, it requires careful control of electrical parameters to avoid uneven etching.
Materials Selection for Micro Springs
The choice of material is a critical determinant of micro spring performance, influencing elasticity, fatigue resistance, and environmental durability. Metal etching accommodates a wide range of metals, each suited to specific applications:
- Stainless Steel: Known for its corrosion resistance and strength, stainless steel (e.g., 304 or 316 grades) is a popular choice for medical and industrial micro springs. Its compatibility with ferric chloride etching ensures efficient processing.
- Titanium: Lightweight and biocompatible, titanium is ideal for aerospace and biomedical springs. Its resistance to hydrofluoric acid etching poses challenges but yields high-quality results.
- Copper Alloys: Beryllium copper and phosphor bronze offer excellent electrical conductivity and elasticity, making them suitable for electronic micro springs. Nitric acid-based etching is commonly employed.
- Nickel Alloys: Inconel and Hastelloy provide exceptional heat and corrosion resistance, favored in harsh environments. Specialized etchants like hydrochloric acid mixtures are used.
Process Optimization for Micro Spring Fabrication
Fabricating micro springs via metal etching requires meticulous process optimization to achieve desired outcomes. Key parameters include:
Photoresist Selection
The photoresist must withstand the etchant while maintaining pattern fidelity. Dry film photoresists are preferred for their uniformity, while liquid resists offer higher resolution for intricate designs.
Mask Design
The photomask defines the spring’s geometry, including coil width, spacing, and thickness. Computer-aided design (CAD) software ensures precision, with tolerances as tight as ±5 micrometers achievable in advanced setups.
Etch Rate Control
Etch rate, influenced by temperature, etchant concentration, and agitation, determines production speed and accuracy. For micro springs, rates typically range from 0.1 to 1 micrometer per minute, adjusted to minimize defects.
Post-Etching Finishing
After etching, micro springs undergo cleaning, stripping of residual photoresist, and surface treatment (e.g., passivation or coating) to enhance durability and performance.
Applications of Micro Springs
Micro springs produced via metal etching find applications across diverse fields:
- Medical Devices: In implants like pacemakers or stents, titanium micro springs provide elasticity and biocompatibility.
- Electronics: Copper alloy springs in connectors and switches ensure reliable electrical contact.
- Aerospace: Stainless steel or nickel alloy springs in sensors withstand extreme conditions.
- MEMS: Etched planar springs in accelerometers and gyroscopes enable precise motion detection.
Comparative Analysis of Etching Techniques
To illustrate the trade-offs between etching methods, the following table compares wet chemical etching, dry etching, and electrochemical etching for micro spring production:
Parameter | Wet Chemical Etching | Dry Etching | Electrochemical Etching |
---|---|---|---|
Precision | Moderate (±10 µm) | High (±2 µm) | High (±5 µm) |
Cost | Low | High | Moderate |
Speed | Fast (1-5 µm/min) | Slow (0.1-0.5 µm/min) | Moderate (0.5-2 µm/min) |
Anisotropy | Isotropic | Anisotropic | Semi-anisotropic |
Material Versatility | High | Moderate | High |
Equipment Complexity | Simple | Complex | Moderate |
Undercutting | Significant | Minimal | Low |
Applications | Planar springs, mass production | 3D springs, MEMS | Conductive alloys, precision |
Advantages and Limitations
Metal etching offers distinct advantages for micro spring production:
- Precision: Sub-micrometer accuracy supports intricate designs.
- Scalability: Batch processing reduces costs for high volumes.
- Material Integrity: Non-contact process avoids mechanical damage.
However, limitations include:
- Undercutting: Isotropic etching can distort fine features.
- Material Constraints: Not all metals etch uniformly.
- Environmental Impact: Chemical waste requires careful disposal.
Conclusion
Advancements in etching technologies promise to further enhance micro spring fabrication. Laser-assisted etching, which combines photochemical and thermal effects, offers hybrid precision. Nanotechnology integration may enable springs with nanoscale features, expanding their use in quantum devices. Additionally, sustainable etchants and recycling systems aim to mitigate environmental concerns, aligning with global manufacturing trends.
Consider a stainless steel micro spring for a medical sensor, etched using wet chemical etching. The spring, a flat spiral with a 100 µm coil width and 10 µm thickness, is fabricated from a 304-grade foil. A ferric chloride etchant at 40°C achieves an etch rate of 0.8 µm/min, completing the process in 12.5 minutes. Post-etching, the spring exhibits a spring constant of 0.5 N/m, suitable for detecting subtle pressure changes. This example underscores the practical efficacy of etching in real-world applications.
Metal etching represents a transformative approach to micro spring manufacturing, blending precision, versatility, and scalability. From its historical roots to its modern applications, the technique has evolved to meet the demands of cutting-edge industries. Through careful material selection, process optimization, and technique comparison, manufacturers can harness its full potential. As technology progresses, metal etching will likely remain a linchpin of microfabrication, driving innovation in miniature engineering.