The metal etching process for encoder discs is a specialized manufacturing method that plays a critical role in the production of high-precision components used in motion control systems. Encoder discs are integral to rotary and linear encoders, providing positional feedback necessary for applications in robotics, aerospace, automotive systems, and industrial automation. The production of these discs demands exacting tolerances and intricate detailing, making metal etching an ideal technique for their fabrication. This article delves into the nuances of the metal etching process for encoder discs, including its principles, materials, equipment, and quality assurance.
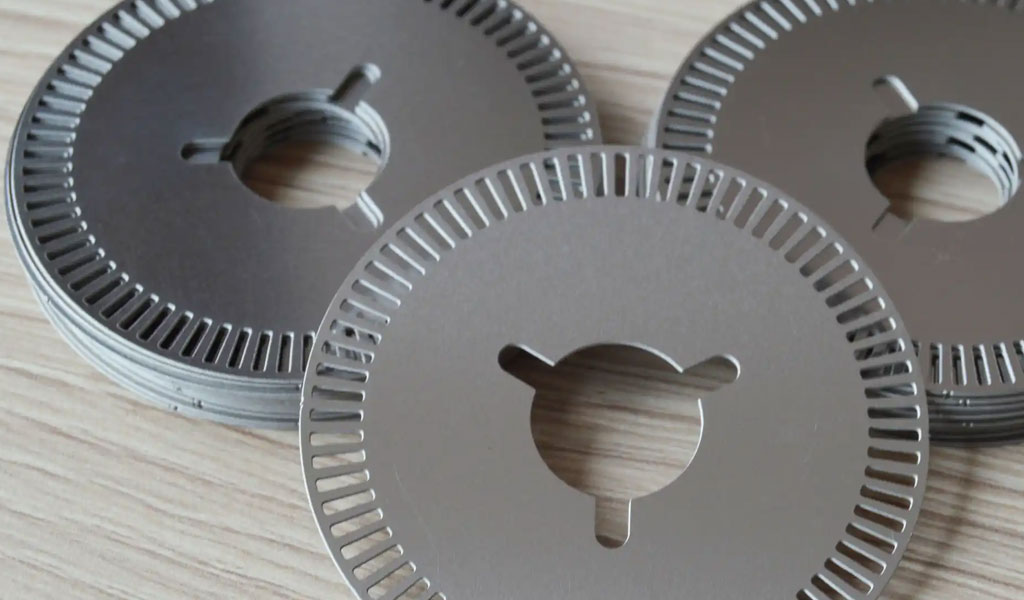
Principles of Metal Etching
Metal etching, also known as photochemical machining (PCM) or photochemical milling, is a subtractive manufacturing process. It involves the removal of material from a metal substrate using chemical agents, typically acids or alkalis. Unlike mechanical machining or laser cutting, metal etching does not exert physical force or heat stress on the material. This ensures that the inherent properties of the metal, such as hardness, elasticity, and thermal resistance, remain unaltered.
The process typically begins with the application of a photoresist—a light-sensitive polymer—onto the surface of the metal sheet. A photomask, which contains the precise design of the encoder disc, is then aligned with the metal substrate. When exposed to ultraviolet (UV) light, the photoresist undergoes a chemical reaction, solidifying in areas not covered by the photomask. Subsequent development removes the unexposed photoresist, leaving behind a pattern that corresponds to the photomask design. This exposed metal is then subjected to an etchant, which dissolves the unprotected areas to create the desired geometry.
Materials for Encoder Discs
Encoder discs are typically fabricated from high-grade metals and alloys selected for their durability, precision, and compatibility with the etching process. Common materials include:
- Stainless Steel: Known for its corrosion resistance and strength, stainless steel is the most commonly used material for encoder discs. Grades such as 301 and 304 are favored for their balance of machinability and performance.
- Nickel and Nickel Alloys: These materials are used for their excellent wear resistance and magnetic properties, making them suitable for specialized encoder applications.
- Brass and Copper: Although less common, these materials are sometimes chosen for their electrical conductivity in certain sensor-related encoder discs.
- Aluminum: Lightweight and corrosion-resistant, aluminum is occasionally used for low-load applications.
- Titanium: High-performance encoders may utilize titanium for its superior strength-to-weight ratio and exceptional resistance to harsh environments.
The choice of material depends on the intended application of the encoder disc, environmental conditions, and mechanical requirements.
Photomask Design and Preparation
The photomask serves as the blueprint for the encoder disc’s intricate patterns. It is typically created using advanced computer-aided design (CAD) software to ensure precise detailing. High-resolution printing techniques or laser imaging are employed to transfer the design onto a transparent film or glass substrate. The photomask must meet strict dimensional accuracy and resolution standards to ensure the fidelity of the final etched product.
The design of encoder discs often involves complex geometries, including concentric rings, radial lines, and precision slots. These features are crucial for the disc’s functionality in measuring angular displacement or speed. Any deviation from the design can compromise the accuracy of the encoder system.
Etching Equipment and Chemicals
The metal etching process requires specialized equipment and carefully controlled chemical solutions. Key components include:
- Etching Tanks: These are used to contain the etching solution and support the chemical reaction. Tanks are often made of materials resistant to corrosive agents, such as polypropylene or stainless steel.
- Spray Etching Systems: For enhanced precision, spray etching systems are employed. These systems use high-pressure nozzles to spray the etchant uniformly across the metal surface.
- Etchants: The choice of etchant depends on the material being processed. Ferric chloride is commonly used for stainless steel, while ammonium persulfate or sodium hydroxide may be used for other metals.
- Rinse Systems: After etching, thorough rinsing is necessary to remove residual chemicals and halt the etching reaction.
- Drying Systems: Specialized dryers ensure that the etched components are free from moisture, which could cause oxidation or other surface defects.
Process Parameters and Control
The success of the metal etching process hinges on meticulous control of several parameters, including:
- Etchant Concentration: The chemical composition of the etching solution must be optimized for the material being processed.
- Temperature: Elevated temperatures can accelerate the etching reaction but must be controlled to prevent over-etching.
- Etching Time: Precise timing ensures that the desired depth and sharpness are achieved without compromising dimensional accuracy.
- Agitation: Gentle agitation or spray techniques enhance etchant uniformity, reducing the likelihood of undercutting or irregular patterns.
Modern etching facilities often utilize automated systems and sensors to monitor these parameters in real time, ensuring consistency and quality.
Advantages of Metal Etching for Encoder Discs
Metal etching offers several advantages over other manufacturing techniques, including:
- High Precision: The process allows for extremely fine detail and tight tolerances, essential for encoder disc applications.
- Scalability: Metal etching is well-suited for both prototype development and high-volume production.
- Material Integrity: The absence of mechanical stress or thermal distortion preserves the original properties of the metal.
- Complex Geometries: Intricate patterns and features can be achieved without the limitations of traditional machining.
- Cost-Effectiveness: For intricate designs, etching can be more economical than CNC machining or EDM (electrical discharge machining).
Applications and Use Cases
Encoder discs produced through metal etching are used in a variety of industries, including:
- Robotics: High-precision encoders are essential for robotic arms and autonomous systems, enabling accurate motion control.
- Aerospace: Flight control systems and navigation equipment rely on encoder discs for reliable feedback.
- Automotive: Encoder discs are used in anti-lock braking systems (ABS), throttle position sensors, and other critical components.
- Medical Devices: Surgical robots and imaging systems employ encoders for precise positioning.
- Industrial Automation: Factory machinery and conveyor systems use encoders for monitoring and control.
Quality Assurance and Testing
To ensure the reliability of encoder discs, rigorous quality assurance protocols are implemented. These include:
- Dimensional Inspection: Advanced metrology tools, such as coordinate measuring machines (CMM) and optical comparators, verify the accuracy of etched features.
- Material Testing: Properties such as hardness, corrosion resistance, and surface finish are assessed to confirm material integrity.
- Functional Testing: Encoder discs are evaluated under simulated operating conditions to ensure they meet performance specifications.
Environmental Considerations
The metal etching process involves the use of chemicals that require careful handling and disposal. Adhering to environmental regulations, such as the Restriction of Hazardous Substances (RoHS) directive, is crucial. Modern etching facilities often incorporate waste treatment systems to neutralize and recycle etchant solutions, minimizing environmental impact.
Conclusion
Metal etching is an indispensable technique in the manufacturing of encoder discs, offering unmatched precision and versatility. By leveraging advanced technologies and stringent quality control measures, manufacturers can produce encoder discs that meet the demanding requirements of today’s industries. As technology evolves, the metal etching process is likely to see further enhancements, solidifying its role as a cornerstone of precision manufacturing.