Metal etching, a precise and versatile manufacturing process, plays a pivotal role in the production of components used for Radio Frequency Interference (RFI) protection. The ability to create intricate patterns and maintain tight tolerances makes etching an ideal technique for crafting shields, meshes, and other elements critical to safeguarding electronic devices and systems from electromagnetic interference. This article delves into the details of the metal etching process, its significance in RFI protection, and the materials and methods employed to achieve optimal performance.
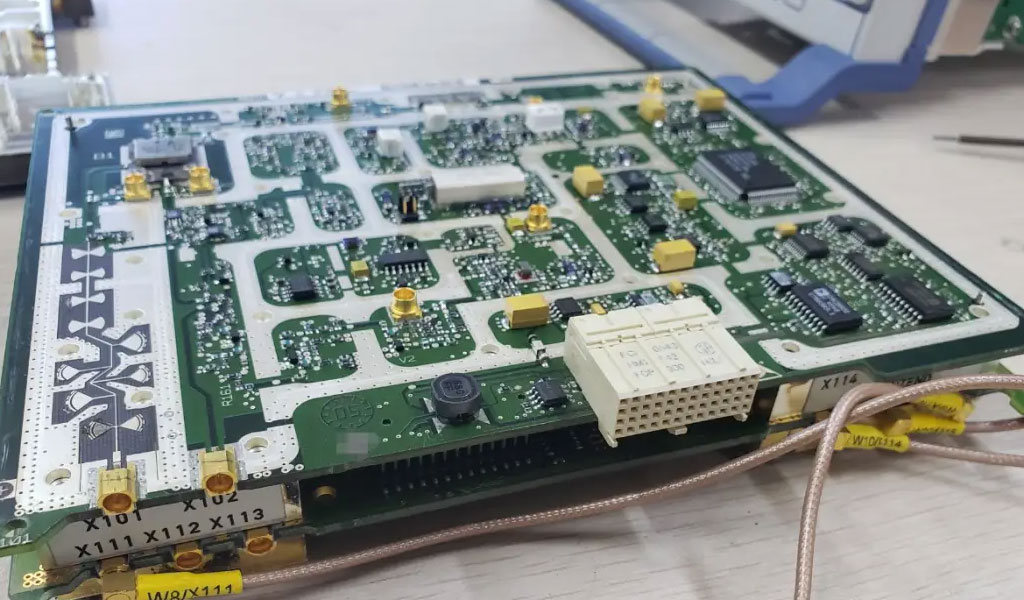
Understanding RFI and Its Challenges
Radio Frequency Interference refers to the disruption in the operation of electronic devices caused by unwanted electromagnetic waves.
These interferences can originate from natural phenomena such as lightning or artificial sources such as electronic circuits, power lines, and wireless communication devices. RFI can result in degraded device performance, data corruption, or even complete operational failure, making effective shielding indispensable.
RFI shielding involves creating barriers that prevent electromagnetic waves from entering or exiting a specific area. This is often achieved using materials with high conductivity and magnetic permeability. Metal etching is employed to fabricate these barriers due to its ability to produce components with precise geometries and features, which are crucial for effective shielding.
The Metal Etching Process for RFI Protection and Shielding
Metal etching, also known as chemical milling or photochemical machining, involves the controlled removal of material from a metal surface to create desired patterns or features. The process typically follows these steps:
Material Selection and Preparation
The choice of material is crucial for RFI protection. Common materials include copper, brass, stainless steel, and nickel alloys due to their high conductivity and shielding properties. The selected metal sheet is cleaned thoroughly to remove contaminants, oils, and oxides, ensuring optimal adhesion of the resist material applied in subsequent steps.
Photoresist Application
A photoresist material is applied to the metal sheet’s surface. This resist, sensitive to ultraviolet (UV) light, acts as a protective layer during the etching process. Depending on the application and desired features, either liquid or dry film photoresists are used.
Exposure and Development
The metal sheet, coated with the photoresist, is exposed to UV light through a photomask containing the desired pattern. The photomask acts as a stencil, allowing light to pass through specific areas while blocking others. Upon exposure, the resist undergoes a chemical change, making it either more resistant or more soluble, depending on whether a positive or negative resist is used. The unexposed or exposed areas are then removed during development, leaving behind a protective pattern that corresponds to the photomask.
Etching
The sheet is immersed in a chemical etchant, typically ferric chloride, cupric chloride, or nitric acid, depending on the material being processed. The etchant dissolves the exposed metal areas while leaving the resist-covered regions intact. The duration of this step is carefully controlled to achieve the desired depth and precision.
Resist Removal and Finishing
After etching, the remaining resist is stripped from the metal surface, revealing the final pattern. Additional finishing processes, such as cleaning, deburring, or passivation, may be performed to enhance the component’s performance and longevity.
Application in RFI Protection
The etched metal components used for RFI shielding often take the form of enclosures, gaskets, meshes, or frames. These components serve to block, reflect, or absorb electromagnetic waves, thereby mitigating interference. The metal etching process enables the production of these elements with exceptional precision, ensuring compatibility with electronic devices and adherence to strict performance standards.
Enclosures
Etched metal enclosures are used to encapsulate sensitive electronic circuits, providing a robust shield against RFI. The ability to etch complex geometries allows manufacturers to create enclosures with vented areas or integrated mounting features without compromising shielding effectiveness.
Gaskets and Seals
Metal gaskets and seals are etched to ensure precise dimensions and consistent performance. These components are typically placed between mating surfaces, creating a conductive path that prevents electromagnetic leakage.
Meshes and Screens
Meshes and screens are vital in applications where airflow or visibility is required alongside RFI shielding. The etching process can produce intricate patterns with high accuracy, ensuring consistent aperture sizes and optimal shielding performance.
Filters and Layers
Etched metal layers are incorporated into multilayer shielding assemblies, such as printed circuit boards (PCBs) and EMI filters. These layers enhance the overall shielding performance by reflecting or absorbing specific frequencies of electromagnetic waves.
Advantages of Metal Etching for RFI Applications
The metal etching process offers several advantages over other manufacturing methods, such as stamping or laser cutting, when it comes to RFI protection components:
- Precision and Complexity: Etching enables the creation of intricate patterns and microfeatures, which are often challenging or impossible to achieve with mechanical methods.
- Material Integrity: Unlike processes that involve mechanical force, etching does not introduce stress or deformation to the material, preserving its structural and electromagnetic properties.
- Scalability: The same photomask can be used to produce multiple components, making etching highly scalable for both low- and high-volume production.
- Versatility: Etching is compatible with a wide range of metals and alloys, allowing manufacturers to tailor the material properties to specific RFI shielding requirements.
Material Considerations for RFI Shielding
The choice of material significantly impacts the performance of RFI shielding components. Key factors to consider include conductivity, permeability, corrosion resistance, and manufacturability. Common materials include:
- Copper: Known for its excellent electrical conductivity and shielding effectiveness, copper is widely used in RFI applications. Its malleability makes it suitable for intricate designs.
- Brass: An alloy of copper and zinc, brass offers good conductivity and corrosion resistance, making it a popular choice for outdoor or industrial environments.
- Stainless Steel: With high strength and corrosion resistance, stainless steel is ideal for demanding environments where durability is essential.
- Nickel Alloys: Alloys such as Inconel and Monel provide excellent shielding performance and resistance to oxidation and chemical attack.
Recent developments in etching technologies have further enhanced the process’s capabilities and efficiency. Innovations such as laser-assisted chemical etching, precision chemical formulations, and automated production systems have improved the accuracy, speed, and environmental sustainability of the etching process. These advancements have expanded the applicability of metal etching to more complex and demanding RFI shielding requirements.
Conclusion
Metal etching is a cornerstone technology for the production of components used in RFI protection. Its ability to create precise and intricate patterns with minimal material waste makes it an indispensable tool for safeguarding electronic devices from electromagnetic interference. By leveraging advanced materials, innovative techniques, and rigorous quality control, manufacturers continue to push the boundaries of what is possible with metal etching, ensuring reliable performance in an increasingly interconnected world.