Metal shims, though seemingly inconspicuous, play a crucial role in various industries by providing support, alignment, and tolerance adjustments within machinery and equipment. Traditionally, producing metal shims involved conventional methods such as stamping, laser cutting, or water jet cutting. However, these methods often pose limitations in terms of precision, cost-effectiveness, and material versatility. Chemical etching has emerged as a revolutionary technique that overcomes these constraints, revolutionizing the way metal shims are manufactured.
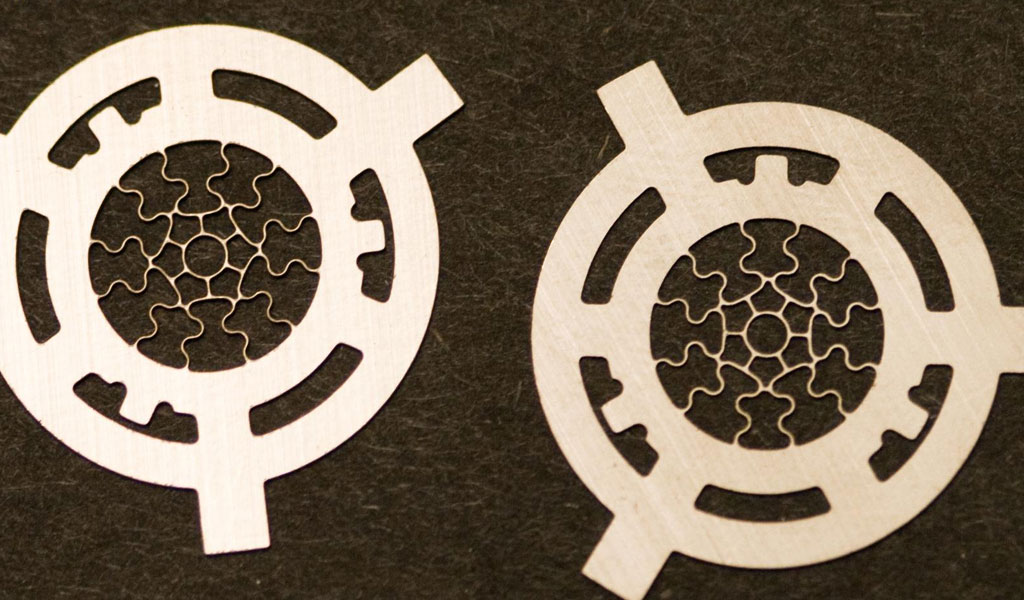
Exploring Conventional Metal Shim Production Methods
Conventional methods like stamping, laser cutting, and water jet cutting have been the go-to techniques for manufacturing metal shims. Stamping involves the use of dies to cut out shapes from metal sheets, but it’s limited by tool wear, high setup costs, and challenges in achieving intricate designs. Laser cutting offers more precision, but its thermal effects can cause material distortion and alter the properties of the metal. Water jet cutting, using high-pressure water mixed with abrasives, is versatile but can be slower and less cost-effective for high-volume production.
Limitations of Conventional Methods
- Precision Constraints: Achieving intricate designs and fine tolerances is often challenging with stamping and laser cutting due to tool wear and heat-affected zones.
- Material Alteration: Thermal methods like laser cutting can alter the material properties, leading to changes in hardness or metallurgical structure.
- Cost Inefficiency: Conventional methods often involve high setup costs, especially for tooling and equipment, making them less cost-effective, especially for small batch productions.
The Emergence of Chemical Etching
Chemical etching, also known as chemical milling, has emerged as a superior alternative for producing metal shims. This subtractive manufacturing process involves selectively removing material using chemical reactions, creating precise and complex designs with high repeatability.
Advantages of Chemical Etching Over Conventional Methods
- Superior Precision: Chemical etching offers exceptional precision and accuracy, allowing the creation of intricate designs and tight tolerances down to a fraction of a millimeter.
- Material Integrity: Unlike thermal methods, chemical etching does not subject the metal to heat, preserving its inherent properties, such as hardness and ductility.
- Cost-effectiveness: With minimal setup costs and the ability to produce small to large batches with ease, chemical etching proves to be highly cost-effective, especially for intricate designs and prototypes.
- Versatility in Materials: Chemical etching is compatible with various metals like stainless steel, aluminum, copper, and alloys, providing flexibility in material selection.
Process of Chemical Etching for Metal Shim Production
The chemical etching process involves several steps:
- Design: The design of the metal shim is created using CAD software, allowing for precise specifications and adjustments.
- Material Selection: Different metals and alloys can be chosen based on the application’s requirements.
- Photoresist Application: A photoresist material is applied to both sides of the metal sheet, protecting areas not meant for etching.
- Exposure and Development: The metal sheet is exposed to UV light through a mask, hardening the photoresist in specific areas. The unexposed photoresist is then washed away, revealing the metal areas for etching.
- Etching: The metal sheet is submerged in a chemical solution that selectively removes the unprotected metal, etching the desired pattern.
- Post-Etching Processes: The remaining photoresist is stripped, and the metal undergoes cleaning and finishing processes to achieve the desired surface characteristics.
Applications and Impact
The versatility and precision of chemical etching have led to its widespread adoption across various industries. From aerospace to medical devices, automotive to electronics, metal shims produced through chemical etching find applications in critical areas where precision and reliability are paramount. These shims ensure proper alignment, spacing, and support within machinery, leading to enhanced performance, reduced downtime, and improved overall efficiency.
Conclusion
In conclusion, the evolution of metal shim production from conventional methods to chemical etching signifies a significant leap in manufacturing technology. The unparalleled precision, material integrity, cost-effectiveness, and versatility offered by chemical etching have revolutionized the production of metal shims. As industries continue to demand higher precision and efficiency, chemical etching stands as a testament to technological innovation, providing a superior solution that surpasses the limitations of traditional manufacturing methods in the production of metal shims.