Metallic bipolar plates are critical components in fuel cells and electrochemical devices, serving as conductive, structural, and protective elements. These plates are essential for the operation and efficiency of proton exchange membrane fuel cells (PEMFCs) and solid oxide fuel cells (SOFCs). They function by distributing gases over the electrodes, conducting electrons between cells, and removing heat from the active area. This article delves into the materials, design considerations, manufacturing processes, and applications of metallic bipolar plates, providing a comprehensive overview of their role in modern energy technologies.
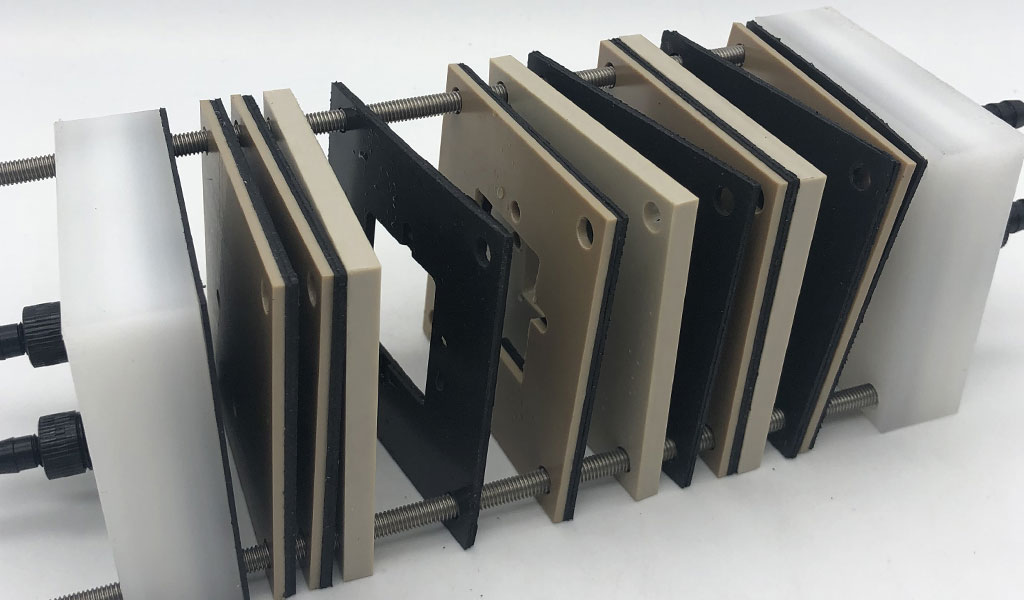
What Is Metallic Bipolar Plates
Metallic bipolar plate is an electronic device that is commonly used in power transmission, semiconductor devices, and experimental research. It consists of two parallel metal plates with positive and negative polarities, and can generate an electric field effect by applying voltage. Bipolar plates play an important role in the field of electronic engineering, and can control the flow of current and the distribution of electric fields, providing additional functions for various applications.
Metallic bipolar plate is an electronic device consisting of two parallel metal plates. These two metal plates are usually called positive plates and negative plates, which are kept at a certain distance and isolated by insulating materials. When voltage is applied, an electric field is formed between the bipolar plates, which affects the charge and current in the surrounding environment.
The development of fuel cell technology dates back to the 19th century, but significant progress occurred in the mid-20th century with the advent of space exploration and the subsequent energy crises. Early fuel cells predominantly used graphite-based materials for bipolar plates. However, the demand for more durable, efficient, and cost-effective solutions led to the exploration of metallic materials. The shift towards metallic bipolar plates was driven by their superior electrical conductivity, mechanical strength, and potential for mass production.
The Role of Metallic Bipolar Plates
Metallic Bipolar plates are usually used to control the distribution of electric fields and currents, and can affect the performance and working mode of electronic devices by changing the voltage and electric field strength.Metallic bipolar plates play a crucial role in the operation and efficiency of fuel cells and various electrochemical devices. These components serve several vital functions that are essential for the performance, longevity, and overall effectiveness of the systems in which they are employed.
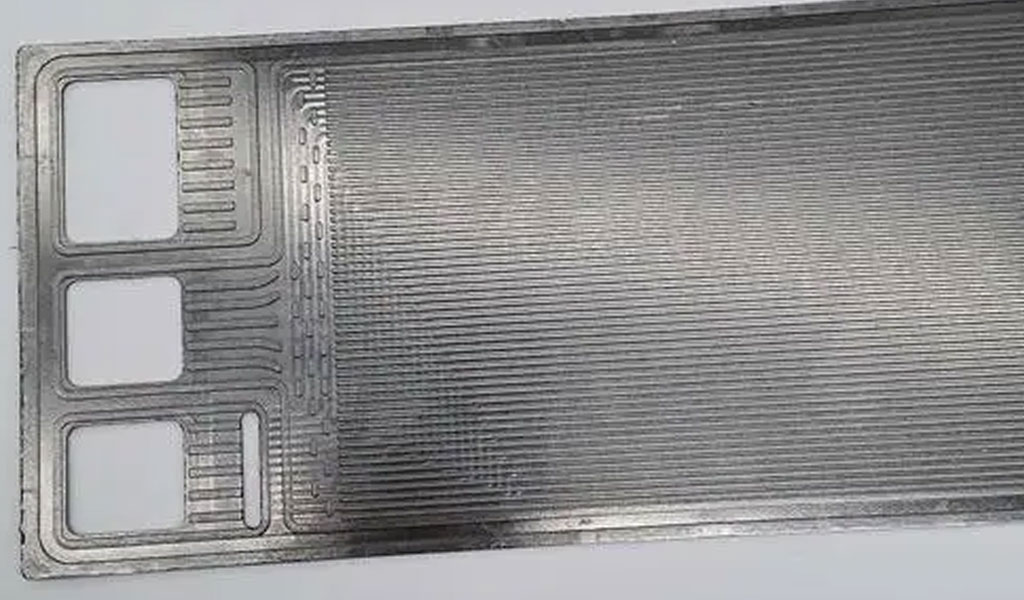
Conductive Role
- Electrical Conductivity:One of the primary roles of metallic bipolar plates is to conduct electrons between the anode and cathode of a fuel cell. High electrical conductivity is essential to minimize energy losses and ensure efficient operation. Metals such as stainless steel, titanium, and nickel alloys are chosen for their superior conductivity compared to non-metallic alternatives like graphite. Additionally, conductive coatings such as gold or platinum can be applied to enhance this property further.
- Contact Resistance : Minimizing contact resistance between the bipolar plate and other components, such as the gas diffusion layer (GDL), is critical for maintaining overall efficiency. Surface treatments and coatings are often employed to reduce contact resistance, ensuring a stable and efficient electron flow across the fuel cell stack.
Structural Role
- Mechanical Strength : Metallic bipolar plates provide the necessary mechanical strength to support the fuel cell stack. This is particularly important in applications subjected to high pressures and varying thermal conditions, such as automotive and stationary power systems. Metals offer superior strength and durability compared to graphite, making them ideal for long-term use in demanding environments.
- Thickness and Weight : The thickness of metallic bipolar plates must be optimized to balance mechanical integrity and weight. Thinner plates contribute to a more compact and lightweight fuel cell design, which is crucial for automotive applications where space and weight are at a premium. However, they must still be thick enough to provide adequate structural support and resist deformation under operational stresses.
- Rib Design and Flow Field Patterns : The design of the ribs and flow field patterns on the bipolar plates is crucial for the distribution of reactant gases and the removal of byproducts. These features must be precisely engineered to ensure uniform distribution, minimize pressure drops, and facilitate efficient water management. Common flow field designs include parallel, serpentine, and interdigitated patterns, each with its advantages and trade-offs.
Protective Role
- Corrosion Resistance : Fuel cells operate in harsh chemical environments, with exposure to acidic or alkaline electrolytes, humid conditions, and fluctuating temperatures. Metallic bipolar plates must resist corrosion to maintain their integrity and performance over time. Materials like stainless steel and titanium are chosen for their inherent corrosion resistance, and additional coatings such as titanium nitride (TiN) or chromium nitride (CrN) can be applied to enhance this property further.
- Surface Treatments and Coatings : To protect against corrosion and mechanical wear, various surface treatments and coatings are applied to metallic bipolar plates. These treatments can also improve electrical conductivity and reduce contact resistance. Techniques such as passivation, nitriding, and plasma spraying are commonly used to modify the surface properties and extend the lifespan of the plates.
- Thermal Management : Efficient thermal management is critical for maintaining optimal operating temperatures and preventing thermal degradation of fuel cell components. Metallic bipolar plates play a role in heat removal due to their high thermal conductivity. Proper thermal management ensures that the fuel cell operates within the desired temperature range, enhancing performance and durability.
Additional Roles
- Water Management : In PEMFCs, effective water management is vital to prevent flooding or drying out of the membrane. The design of the flow fields on metallic bipolar plates influences water distribution and removal. Serpentine and interdigitated flow fields, for example, are designed to promote efficient water management, ensuring that excess water is removed while maintaining adequate hydration of the membrane.
- Gas Distribution : Metallic bipolar plates are responsible for distributing reactant gases (hydrogen and oxygen) evenly across the electrode surfaces. Uniform gas distribution is crucial for maximizing the active area of the electrodes and ensuring consistent electrochemical reactions. The flow field patterns and channel dimensions are carefully designed to achieve this goal.
- Cost Considerations : While metallic bipolar plates offer numerous advantages, cost is a significant consideration. The choice of materials, coatings, and manufacturing processes all impact the overall cost of the fuel cell. Researchers and manufacturers continually seek to balance performance with cost-effectiveness, exploring new materials, and innovative manufacturing techniques to reduce expenses without compromising quality.
The roles of metallic bipolar plates in fuel cells and electrochemical devices are multifaceted and essential for the overall performance, efficiency, and durability of these systems. Their conductive, structural, and protective functions are critical to the operation of fuel cells, influencing everything from electron flow and mechanical stability to corrosion resistance and thermal management. As the demand for clean energy solutions grows, the development of advanced metallic bipolar plates will continue to be a key area of focus, driving improvements in fuel cell technology and contributing to the advancement of sustainable energy systems.
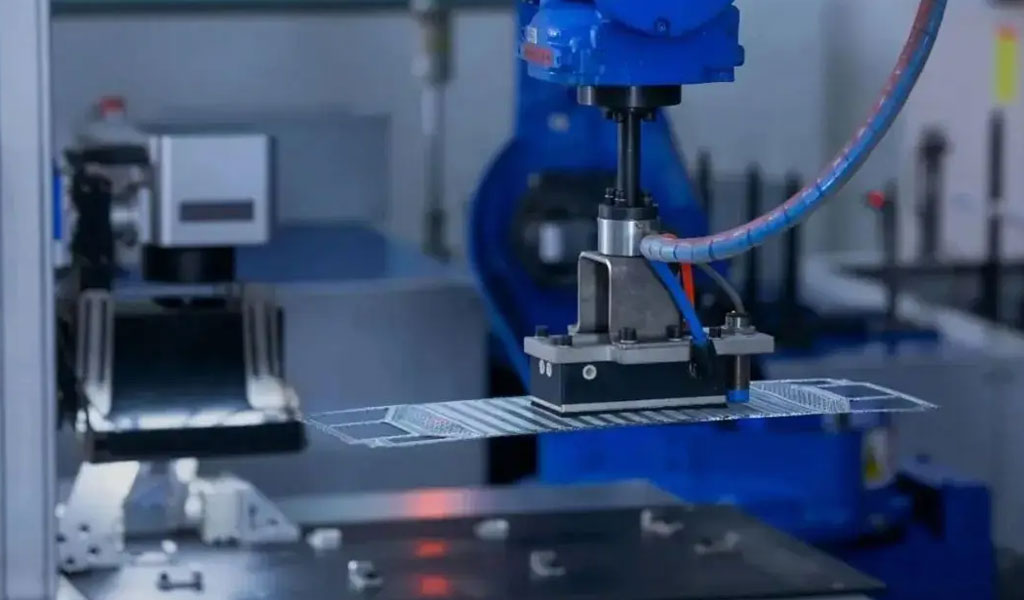
Types of Metallic Bipolar Plates
Metallic bipolar plates are categorized based on the types of metals and alloys used in their construction, as well as the specific applications they are designed for.
The choice of material significantly impacts the plate’s performance, durability, and suitability for different operational environments. This section explores the various types of metallic bipolar plates, detailing their characteristics, advantages, and typical applications.
1. Stainless Steel Bipolar Plates
Stainless steel is a popular choice for bipolar plates due to its excellent corrosion resistance, mechanical strength, and cost-effectiveness. Common grades used include:
- SS316L: Known for its superior corrosion resistance and good mechanical properties, making it suitable for harsh environments.
- SS304: Offers a balance between cost and performance, with adequate corrosion resistance and strength for many applications.
Advantages
Mechanical Strength: High tensile strength and durability, ensuring long-term reliability and structural integrity.
Cost-Effectiveness: Relatively low cost compared to other high-performance metals like titanium.
Applications
Electrolyzers: Suitable for hydrogen production systems.
2. Titanium Bipolar Plates
Titanium and its alloys are used in applications requiring high corrosion resistance and strength. Common alloys include:
- Pure Titanium (Grade 2): Offers excellent corrosion resistance and is relatively easy to form and weld.
- Titanium Alloys (e.g., Ti-6Al-4V): Provide enhanced strength and resistance to high temperatures.
Advantages
Strength-to-Weight Ratio: High strength combined with low density, making titanium plates lightweight yet robust.
Biocompatibility: Suitable for medical and biomedical applications due to its non-toxic nature.
Applications
Solid Oxide Fuel Cells (SOFCs): Suitable for high-temperature operations.
3. Aluminum Bipolar Plates
Aluminum is used for its lightweight properties and high conductivity. Common alloys include:
- 6061 Aluminum: Offers a good balance of strength, corrosion resistance, and formability.
- 7075 Aluminum: Known for its high strength, comparable to many steels, and good fatigue resistance.
Advantages
High Conductivity: Excellent electrical and thermal conductivity, enhancing the efficiency of the fuel cell.
Ease of Manufacturing: Easy to form, machine, and weld, which can reduce manufacturing costs.
Applications
Automotive Fuel Cells: Used in lightweight vehicle designs to improve fuel efficiency.
4. Nickel-Based Alloy Bipolar Plates
Nickel-based alloys are chosen for their high-temperature stability and corrosion resistance. Common alloys include:
- Inconel: Known for its excellent resistance to oxidation and corrosion, particularly at high temperatures.
- Monel: Offers good resistance to acids and alkalis, as well as high mechanical strength.
Advantages
Corrosion Resistance: Resistant to a wide range of corrosive environments, including oxidizing and reducing conditions.
Mechanical Strength: High tensile and yield strength, providing durability and reliability.
Applications
Industrial Electrolyzers: Used in systems where robust performance and longevity are required.
5. Copper Bipolar Plates
Copper and its alloys are valued for their superior electrical conductivity. Common alloys include:
- Pure Copper (C11000): Offers the highest electrical conductivity among commercial metals.
- Copper-Nickel Alloys: Provide enhanced corrosion resistance compared to pure copper.
Advantages
Thermal Conductivity: Excellent heat dissipation, aiding in thermal management of the fuel cell stack.
Malleability: Easy to form and fabricate, allowing for complex flow field designs.
Applications
Heat Exchangers: Suitable for use in systems requiring efficient heat dissipation.
6. Coated Metallic Bipolar Plates
To enhance the performance of metallic bipolar plates, various coatings are applied:
- Gold and Platinum Coatings: Applied to improve electrical conductivity and reduce contact resistance.
- Titanium Nitride (TiN) and Chromium Nitride (CrN) Coatings: Used to enhance corrosion resistance and mechanical durability.
- Carbon-Based Coatings: Applied to reduce contact resistance and improve surface conductivity.
Advantages
Customization: Different coatings can be tailored to specific applications and operational conditions.
Applications
Electrolyzers: Coated plates enhance efficiency and durability in hydrogen production systems.
The choice of metallic bipolar plate depends on the specific requirements of the fuel cell or electrochemical device, including factors such as operational environment, performance needs, and cost considerations. Stainless steel, titanium, aluminum, nickel-based alloys, copper, and coated metals each offer unique advantages that make them suitable for different applications. As technology advances and new materials and coatings are developed, the performance and cost-effectiveness of metallic bipolar plates will continue to improve, driving the adoption of fuel cells and electrochemical systems across various industries.
The Use and Application Of Metallic Bipolar Plates
Bipolar plates can be divided into many types according to different applications and construction methods. Here are some common types of bipolar plates:
- Parallel plate capacitor: Parallel plate capacitor is the simplest and most basic bipolar plate structure. It consists of two parallel metal plates separated by insulating materials and forms a capacitor with adjustable electric field strength.
- Micro-nano scale bipolar plates: With the development of micro-nano technology, micro-nano scale bipolar plates have been widely studied and applied. These bipolar plates are usually composed of microscopic or nanoscale metal wires or graphite sheets, with smaller size and higher integration. Micro-nano scale bipolar plates have important application potential in the fields of electronic devices, sensors and optical devices.
- Multi-level bipolar plate: A multi-level bipolar plate is a structure composed of multiple bipolar plates cascaded. Different voltages can be applied between each bipolar plate, forming a complex electric field distribution and potential gradient. Multi-level bipolar plates are widely used in high-precision experimental equipment such as particle accelerators, electron microscopes and ion traps.
- Adjustable bipolar plate: Adjustable bipolar plate has the characteristic of changing the spacing or tilt angle. By adjusting the distance or angle between the bipolar plates, the strength and distribution of the electric field can be changed, thereby achieving precise control of the current and electric field.
- In addition to the above common types of bipolar plates, there are other bipolar plates with special designs and applications. These different types of bipolar plates play an important role in fields such as power transmission, semiconductor devices, and experimental research, and provide flexible and controllable electric field control capabilities for various applications.
A bipolar plate is an electronic device consisting of two parallel metal plates that forms an electric field effect by applying voltage. It plays an important role in fields such as power transmission, semiconductor devices, and experimental research, and can control the current and electric field distribution by changing the voltage and electric field strength. Different types of bipolar plates include parallel plate capacitors, micro-nanoscale bipolar plates, multi-level bipolar plates, and adjustable bipolar plates, which provide additional functions and flexibility for various applications.
The Application Of Metal Etching Process in Fuel Cell Bipolar Plates
Previously, we introduced the production process and a summary of manufacturers for metal bipolar plates in hydrogen fuel cell technology. There are several different processing methods for these plates, including CNC machining, stamping, laser cutting, and etching, all of which can achieve the desired results.
- Stamping Bipolar Plates: Metal materials are stamped to form channels, followed by welding, coating, adhesive application, and airtightness testing. Stamping requires costly tooling, and changes in design drawings incur significant retooling costs. Stamping is prone to deformation, making it challenging to control channel formation. Therefore, sometimes etching processes are used to create channels.
- Etching Bipolar Plates: No tooling is required, allowing unlimited design flexibility and easy modification. Development costs are low, and etching ensures high precision, accommodating full or partial etching and logo addition.
- CNC Machining Bipolar Plates: This method is costly, and achieving precise grooves can be challenging.
- Laser Cutting Bipolar Plates: Laser engraving cannot achieve partial etching of bipolar plates, limiting its range of applications.
Etching was initially used for making printing plates such as copper or zinc plates, and it is widely adopted for lightweighting, instrument panels, nameplates, and processing thin parts that are difficult to manufacture using traditional methods. Through continuous improvement and technological advancements, etching is also used in the precise processing of electronic thin film components in industries like aerospace, mechanical engineering, and chemistry, particularly in semiconductor processes where it is indispensable.
Etching is not a new manufacturing technique but has evolved with improvements in equipment and processes, making it essential for high-precision devices. It is widely used in applications such as circuit board production through etching and manufacturing thin parts like nameplates that are difficult to process using traditional methods. Therefore, etching technology is a suitable path for manufacturing thin metal bipolar plates.
Etching Supports Hydrogen Fuel Cell Bipolar Plates
With over 20 years rooted in the automotive industry, BE-CU is committed to manufacturing bipolar plates for fuel cells using patented etching processes. From the establishment of manufacturing infrastructure for etching tools to their application in FCEVs, we have implemented a vertically integrated innovation process.Metal bipolar plate primarily consists of five parts: anode-side sealing ring, anode metal plate, cathode metal plate, weld seam, and cathode-side sealing ring. By combining and welding the anode and cathode metal plates, and utilizing sealing rings on both sides, we prevent cross-mixing of reaction gases and coolant, as well as leakage.
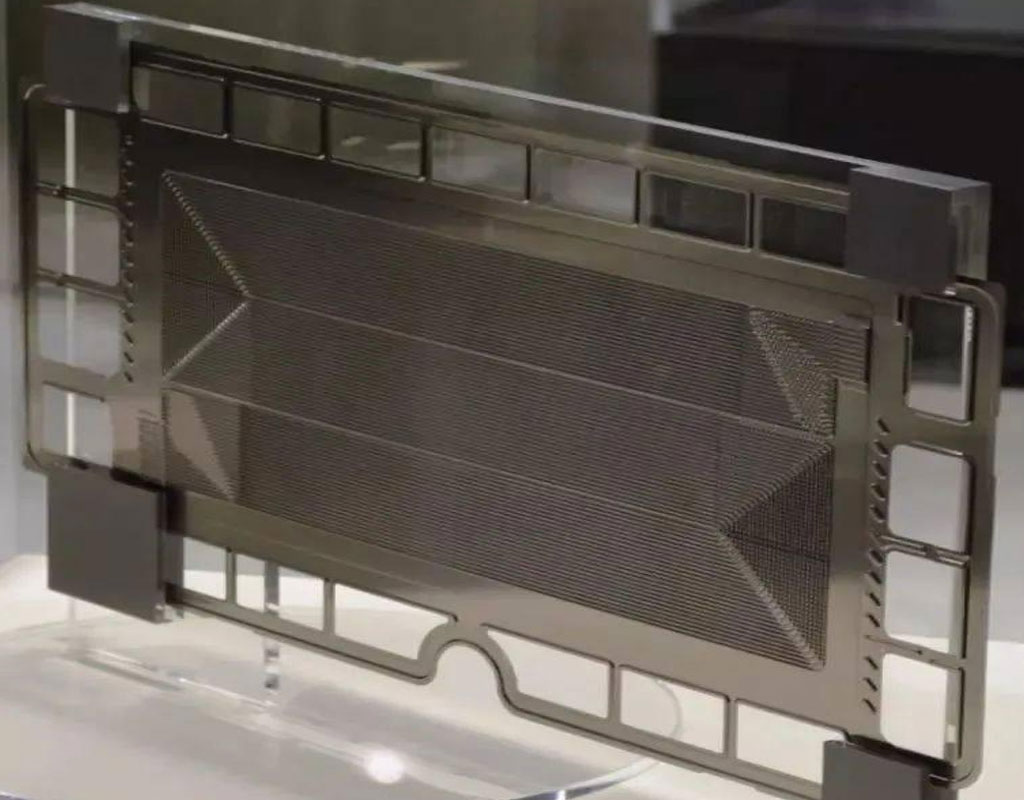
The design of the metal bipolar plate includes three main sections: inlet and outlet areas, reaction gas transition zone (gas distribution area), and effective reaction area. Through Computational Fluid Dynamics (CFD) simulations, the transition zone and reaction area are optimized for fluid flow, ensuring uniform distribution of reactants within the reaction area to promote even electrochemical reaction.
Metal bipolar plates are manufactured using etching processes primarily because etching ensures smooth surfaces without burrs and can accommodate materials with thicknesses ranging from 0.01 to 2 mm. Using metal foil for changes in design incurs no additional costs, and batch production meets required specifications efficiently.