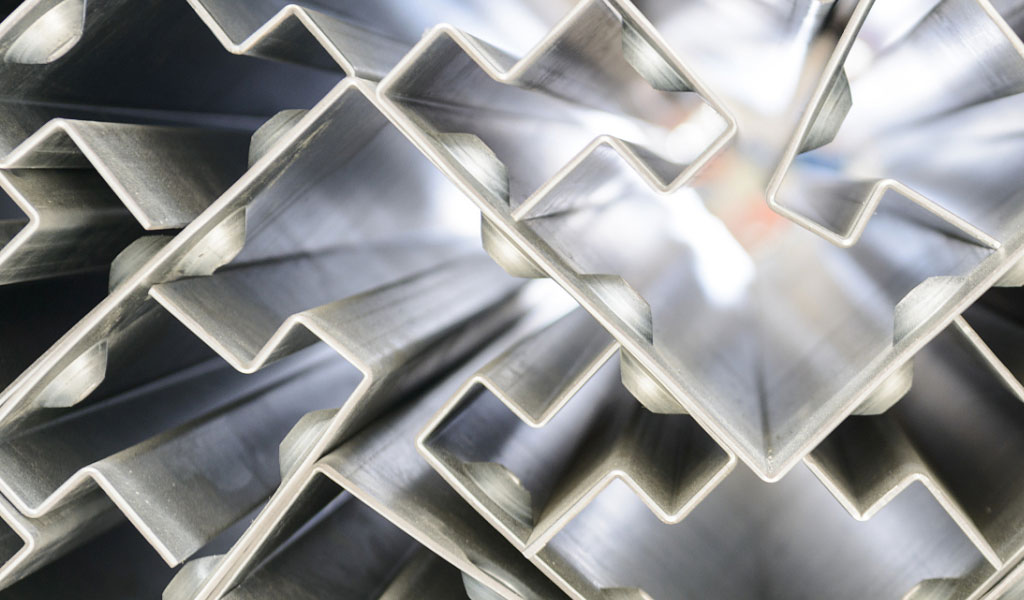
The evolution of control systems and methods in CNC machining has led to significant advancements in manufacturing precision and efficiency.
The rotating five-axis machining center represents a state-of-the-art technology in the realm of automated machining, offering increased flexibility, precision, and the ability to handle complex geometries.
This article explores the principles of online control systems, the methods of controlling rotating five-axis systems, and the integration of such systems into CNC machining centers.
CNC Machining and Control Systems
Computer Numerical Control (CNC) machining refers to a manufacturing process in which pre-programmed computer software controls the movement of machine tools. CNC machining centers encompass a variety of tools such as lathes, mills, and grinders, and are typically employed in industries requiring high precision and complex parts, including aerospace, automotive, medical, and electronics.
Control systems in CNC machining are critical to the successful operation of these machines. They are responsible for interpreting design data, generating the necessary motion commands, and executing the machining processes with high precision. Traditional CNC machines were limited to linear movements (X, Y, Z axes), but with the advent of advanced technologies, five-axis systems were introduced to allow for simultaneous movement along five axes, enhancing machining capabilities.
Five-Axis Machining
Five-axis machining involves the use of a CNC machine tool that moves a workpiece or tool along five different axes. This setup enables complex geometries, such as those found in aerospace components or medical devices, to be machined with a high degree of accuracy. Unlike three-axis machines, which are confined to movements in three perpendicular directions, five-axis systems introduce additional rotational movements, enabling the tool to approach the workpiece from virtually any angle.
The five axes typically include the three primary linear axes (X, Y, Z) and two rotational axes, often referred to as the A and B axes. These rotational movements allow the tool to rotate around the X, Y, or Z axis, which provides additional flexibility in the positioning of the tool relative to the workpiece. This configuration reduces the need for repositioning the workpiece, thus increasing efficiency and precision.
Rotating Five-Axis Systems
In a rotating five-axis system, the workpiece is mounted on a rotating table, which is controlled by two additional rotational axes (usually A and B). The rotating table allows the workpiece to be positioned and oriented in different directions, allowing the cutting tool to reach multiple sides of the workpiece without the need to move it physically. The rotating mechanism can be either rotary tables or tilting head systems, with both offering specific advantages depending on the machining requirements.
Rotating five-axis CNC machines are particularly advantageous in applications where multiple surfaces need to be machined simultaneously, such as in turbine blades, complex molds, and intricate medical implants. The ability to position the workpiece in multiple orientations with precision makes rotating five-axis systems ideal for high-precision industries.
Control Methods in CNC Machining
Control methods in CNC machining encompass the software and hardware systems used to manage machine operations. These systems can be broadly classified into open-loop and closed-loop control systems.
Open-Loop Control
An open-loop control system operates by sending predefined commands to the machine without receiving feedback. In the context of CNC machining, this means that the machine follows a series of programmed instructions but does not have the ability to correct any deviations from the expected operation. Open-loop control systems are often simpler and less expensive but are less accurate and suitable for less complex tasks.
Closed-Loop Control
Closed-loop control systems, in contrast, are more advanced and involve feedback mechanisms that allow the machine to self-correct deviations. These systems utilize sensors, encoders, and other feedback devices to monitor the position and movement of machine components. If any discrepancies are detected between the desired and actual positions of the tool or workpiece, the system automatically adjusts the operation to maintain precision.
Closed-loop systems are integral to modern CNC machining, especially in applications involving rotating five-axis systems, where the complexity and precision requirements demand real-time monitoring and adjustments.
Online Control Systems
An online control system refers to a system where the machine communicates with an external control interface or network during operation. This connection enables real-time monitoring, adjustment, and troubleshooting of the CNC machine, providing operators and engineers with the ability to intervene promptly if an issue arises. In contrast to traditional offline systems, where all instructions are pre-programmed and executed independently, online systems allow for continuous interaction between the machine and the controlling software.
Real-Time Data Collection and Analysis
In rotating five-axis CNC machining, online control systems are essential for ensuring optimal performance. They collect data in real time about various parameters such as feed rates, tool positions, temperatures, and vibrations. This data is transmitted to a central control unit, which can make instant adjustments to improve machining accuracy, prevent errors, and optimize production speed.
Advanced online systems also integrate artificial intelligence (AI) and machine learning algorithms to predict potential failures or inefficiencies based on historical data and current machine conditions. This capability allows for predictive maintenance, reducing machine downtime and increasing overall productivity.
Communication Protocols
Communication between the CNC machine and external systems is typically managed through various industrial communication protocols. These protocols, such as Modbus, Ethernet/IP, and OPC UA, ensure seamless data exchange between the machine’s controllers and other systems, including enterprise resource planning (ERP) software, production management systems, and remote monitoring tools.
The integration of online control systems with other manufacturing systems can lead to a fully automated and highly efficient production line. For example, when coupled with advanced scheduling software, online control systems can prioritize tasks, allocate resources, and adjust parameters to ensure optimal throughput and minimal delays.
Control Methodologies for Rotating Five-Axis CNC Machines
Controlling a rotating five-axis CNC machine requires specialized algorithms and methods to ensure that the tool follows the intended path with high precision. The unique challenges of five-axis machining, such as dealing with complex tool paths and maintaining accuracy during multi-axis movements, require advanced control techniques.
Kinematic Control
Kinematic control focuses on the movement of the tool relative to the workpiece. In five-axis machining, the tool needs to be positioned and oriented precisely to achieve the desired cut without colliding with the workpiece or any other part of the machine. Kinematic models of the machine are used to simulate the movements of the tool and optimize the motion trajectory.
In the case of rotating systems, the workpiece’s orientation can change dynamically, requiring continuous adjustments in the toolpath. Advanced kinematic control algorithms take into account the rotation of the workpiece and the interactions between the tool and the surface being machined.
Tool Path Planning
Tool path planning is a critical component of CNC machining, particularly in five-axis systems. The complexity of the tool path increases exponentially with each additional axis, and rotating five-axis systems require highly sophisticated algorithms to ensure that the tool maintains the correct orientation and trajectory at all times.
Modern tool path planning methods for rotating five-axis systems use optimization techniques such as genetic algorithms, simulated annealing, and particle swarm optimization. These methods evaluate a wide range of possible tool paths and select the one that minimizes machining time, reduces tool wear, and ensures the highest quality finish.
Simulation and Compensation
Before actual machining, simulations are often used to validate tool paths and check for potential issues. This allows operators to preview the machining process, visualize the cutting operation, and detect any potential errors in the tool’s movement or collision risks.
In addition to simulation, real-time compensation algorithms are used to adjust the machine’s movements based on actual conditions. For instance, if the machine detects slight deviations in tool positioning due to thermal expansion or mechanical wear, compensation methods adjust the tool path accordingly to maintain precision.
Challenges and Future Directions
Despite the significant advancements in CNC machining and control systems, several challenges remain, particularly when dealing with rotating five-axis systems. These challenges include the complexity of programming, the need for real-time feedback and compensation, and the demand for high-speed processing of large amounts of data.
The future of CNC machining will likely see the further integration of AI and machine learning, enabling systems to adapt more autonomously to changes in machining conditions. Additionally, advances in sensor technologies, such as high-precision encoders and force sensors, will enhance the ability of CNC machines to detect and correct errors in real time, further improving their precision and reliability.
Furthermore, the growing need for mass customization in manufacturing may drive the development of more flexible and adaptive CNC machining systems that can easily switch between different types of parts or materials. These systems will likely rely on advanced online control methods and dynamic reprogramming techniques to achieve high efficiency while maintaining high quality.
Conclusion
The integration of rotating five-axis systems with advanced online control methodologies represents a leap forward in the field of CNC machining. These systems offer unprecedented capabilities in terms of precision, flexibility, and efficiency, making them essential tools in modern manufacturing. As control methods continue to evolve, the potential for fully autonomous, highly adaptive CNC machining centers will revolutionize industries, pushing the boundaries of what is possible in high-precision manufacturing.4o mini