In the realm of safety-critical applications, where precision is paramount, the manufacturing of parts takes on a whole new level of importance. One method that stands out for its ability to achieve intricate details and maintain dimensional accuracy is chemical etching. This sophisticated process plays a pivotal role in the production of precision parts that are integral to safety-critical systems across various industries.
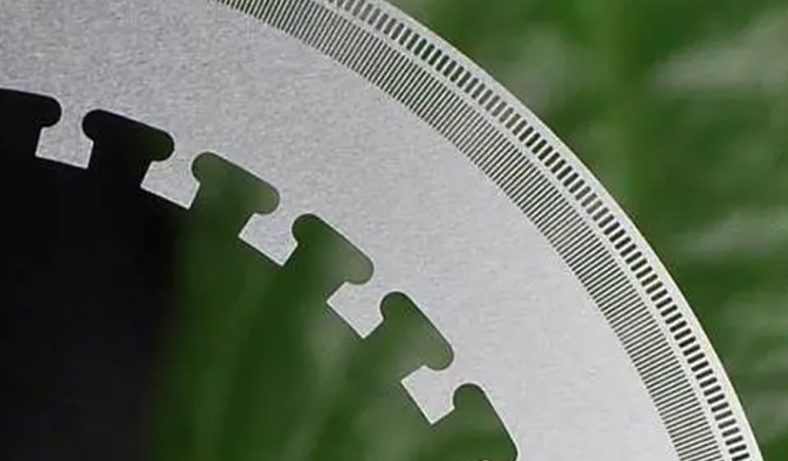
Understanding Chemical Etching
Chemical etching is a subtractive manufacturing process that involves selectively removing material from a substrate using chemical reactions.
This method allows for the creation of complex and intricate patterns with tight tolerances, making it particularly well-suited for safety-critical applications.
The process typically involves the use of a mask or resist to protect certain areas of the material while exposing others to a corrosive chemical solution.
Precision Beyond Conventional Methods
Compared to traditional machining techniques, chemical etching offers unparalleled precision. This is crucial in safety-critical applications where even the slightest deviation from design specifications can have catastrophic consequences. The ability to achieve fine details and maintain tight tolerances makes chemical etching an indispensable tool for producing components that meet the stringent requirements of safety-critical systems.
Material Versatility
Chemical etching is not limited by the type of material, allowing manufacturers to work with a wide range of substrates, including metals, alloys, and even exotic materials. This versatility is a significant advantage in safety-critical applications, where specific material properties are often required to withstand extreme conditions, corrosive environments, or high stress.
Consistency and Reproducibility
For safety-critical systems, consistency and reproducibility are non-negotiable. Chemical etching excels in providing batch-to-batch uniformity, ensuring that each precision part meets the same high standards. This level of reliability is vital in industries such as aerospace, medical devices, and automotive, where the performance and reliability of components directly impact human safety.
Design Freedom and Complexity
The design flexibility afforded by chemical etching is unparalleled. This process allows for the creation of intricate and complex geometries, intricate patterns, and micro-sized features that are challenging to achieve with other manufacturing methods. This design freedom is invaluable when crafting components for safety-critical applications, where optimal functionality often requires unconventional shapes and structures.
Cost-Effective Solutions
While precision is crucial in safety-critical applications, cost-effectiveness is also a key consideration. Chemical etching offers an efficient and economical solution for producing high-precision parts in large quantities. The ability to create complex designs without the need for extensive tooling or time-consuming setups makes chemical etching a cost-effective choice for safety-critical industries.
Conclusion:
In the pursuit of perfection in safety-critical applications, precision in manufacturing is non-negotiable. Chemical etching emerges as a champion in this arena, providing unmatched accuracy, versatility, and cost-effectiveness. As industries continue to push the boundaries of innovation, the role of chemical etching in crafting precision parts for safety-critical systems will only become more pronounced, ensuring the reliability and safety of critical components in various sectors.