In recent years, the automotive industry has witnessed a paradigm shift with the growing demand for electric vehicles (EVs). Alongside the advancements in battery technology and electric drivetrains, the design and manufacturing processes for EV components have undergone significant transformations. Among these innovations, chemical etching has emerged as a revolutionary technique, redefining the way electric vehicles are designed and manufactured.
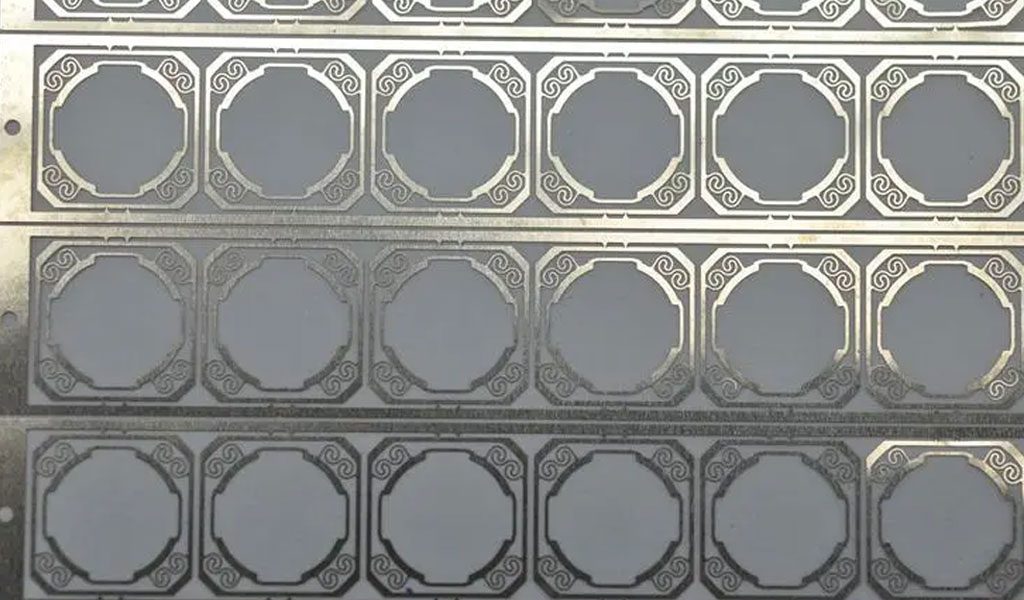
Chemical Etching: An Overview
Chemical etching, also known as chemical milling or photochemical machining, is a subtractive manufacturing process that utilizes chemical solutions to selectively remove material from a substrate.
This precise and controlled technique allows intricate patterns, shapes, and designs to be etched onto various materials, including metals such as aluminum, copper, and stainless steel, among others.
The process involves several key steps:
- Preparation of the substrate: The material to be etched is thoroughly cleaned and coated with a light-sensitive photoresist.
- Exposure to light: A photomask or stencil with the desired design is placed over the coated substrate, and the assembly is exposed to UV light. The areas not covered by the mask remain sensitive to the subsequent chemical treatment.
- Chemical etching: The substrate is submerged in an etchant solution that selectively dissolves the exposed areas, leaving behind the desired pattern or design.
- Post-processing: The remaining photoresist is removed, and the etched part undergoes any necessary finishing processes.
Transforming EV Design
The integration of chemical etching in the electric vehicle manufacturing process has revolutionized the design and production of various components. Let’s delve into how this technology is reshaping the world of EVs:
Lightweight and High-Strength Components
Weight reduction is a crucial factor in enhancing the efficiency and range of electric vehicles. Chemical etching enables the creation of lightweight yet durable components by selectively removing material from metal substrates. This technique allows engineers to design intricate patterns that reduce weight without compromising structural integrity. Components such as battery enclosures, heat sinks, and structural panels benefit from this approach, contributing to improved performance and energy efficiency of EVs.
Enhanced Thermal Management
Efficient thermal management is essential for optimizing the performance and lifespan of EV components, especially batteries and powertrain systems. Chemical etching facilitates the creation of complex heat dissipation structures with precise geometries on metal surfaces. These structures promote better heat transfer and dissipation, ensuring optimal operating temperatures within critical components. Improved thermal management not only enhances performance but also extends the longevity of electric vehicle systems.
Customization and Design Flexibility
EV manufacturers strive to differentiate their vehicles through unique designs and features. Chemical etching offers unparalleled design flexibility, allowing for the creation of intricate and customized patterns on metal surfaces. From decorative elements on exterior panels to functional components within the vehicle, this technology enables designers to bring their innovative concepts to life. As a result, EVs can exhibit distinct aesthetics while maintaining high standards of functionality and performance.
Precision and Cost Efficiency
The precise nature of chemical etching ensures high accuracy and repeatability in manufacturing, leading to minimal material waste. Compared to traditional machining methods, this technique requires fewer tooling changes and reduces the need for secondary operations, thus streamlining the manufacturing process. Additionally, the scalability of chemical etching makes it a cost-effective solution for mass production of complex and intricate components used in electric vehicles.
Applications in EV Components
The application of chemical etching in electric vehicle components spans across various critical areas:
Battery Enclosures and Thermal Management Plates
The battery pack is a vital component in electric vehicles, and its efficiency depends on proper thermal management. Chemical etching allows the creation of intricate cooling channels and heat dissipation patterns on aluminum or copper plates used in battery enclosures. These custom-designed thermal management plates optimize heat transfer, thereby improving the performance and safety of the battery system.
Electric Motor Components
Electric motors are at the heart of EV propulsion systems, and their efficiency is crucial for overall vehicle performance. Chemical etching enables the production of precision-cut laminations for motor cores, reducing eddy currents and enhancing motor efficiency. Additionally, this technique facilitates the creation of complex shapes in motor components, contributing to improved power density and reduced noise levels.
Structural Panels and Aesthetic Features
Beyond functional components, chemical etching is employed in creating aesthetically pleasing designs on exterior panels and interior trim components. Manufacturers can incorporate intricate patterns, logos, and texturing on metal surfaces, allowing for customization while maintaining structural integrity. This versatility in design adds to the visual appeal of electric vehicles and enhances brand identity.
Future Perspectives and Challenges
Despite the numerous advantages of chemical etching in electric vehicle design, challenges persist, primarily concerning material selection, process optimization, and environmental sustainability. Researchers and manufacturers continue to explore advanced materials and refining processes to further improve the efficiency and applicability of chemical etching in the automotive industry.
Moreover, as the demand for EVs continues to rise, there is a growing need for sustainable manufacturing practices. Efforts are underway to develop eco-friendly etchants and enhance recycling methods for etching solutions, reducing the environmental impact of the process.
Conclusion
Chemical etching has emerged as a game-changing technology in the realm of electric vehicle design and manufacturing. Its ability to create intricate patterns, lightweight structures, and efficient thermal management solutions has revolutionized the production of critical components in EVs. As the automotive industry undergoes a rapid transformation towards electrification, chemical etching stands out as a versatile and indispensable tool, shaping the future of electric mobility.
The integration of this innovative manufacturing process not only enhances the performance, efficiency, and aesthetics of electric vehicles but also signifies a shift towards more sustainable and advanced manufacturing practices. With continuous advancements and refinement, chemical etching is set to play an increasingly pivotal role in driving the evolution of electric vehicle design and engineering.
As the automotive landscape evolves, the impact of chemical etching on electric vehicle technology continues to grow, fostering innovation and pushing the boundaries of what’s possible in the quest for cleaner, more efficient transportation solutions.