In the realm of filtration and separation processes, precision is paramount. From industrial applications to everyday consumer products, the efficacy of filters, screens, and sieves plays a pivotal role in ensuring the quality and purity of substances. Chemical etching has emerged as a game-changer in the production of these critical components, offering unparalleled precision, versatility, and efficiency.
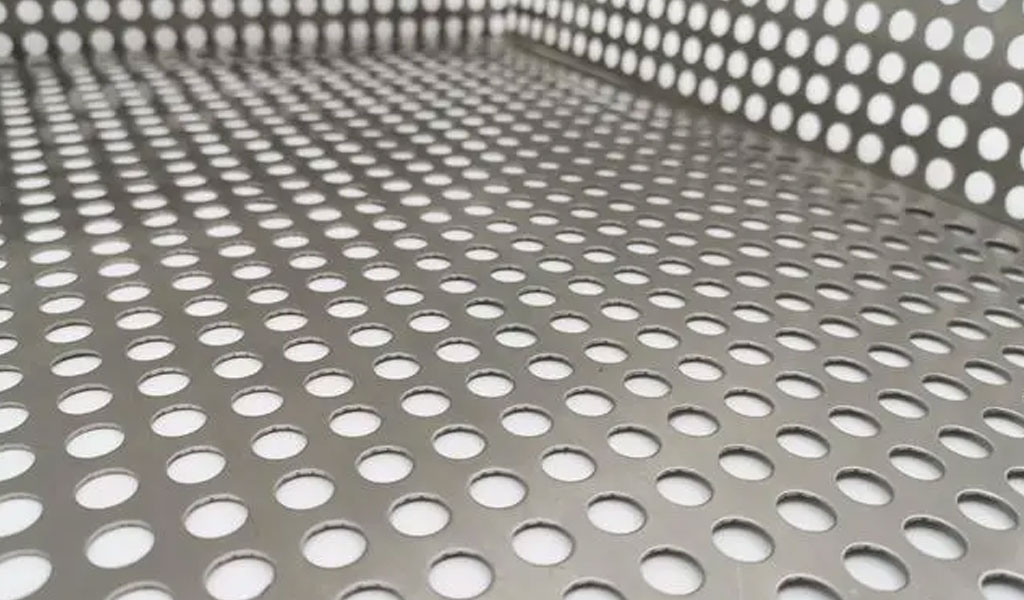
Traditionally, manufacturing filters, screens, and sieves involved various methods such as stamping, punching, or laser cutting. While effective to some extent, these methods often presented limitations in terms of precision, intricate design capabilities, and material options. Chemical etching, on the other hand, has evolved into a sophisticated and highly sought-after technique, addressing these limitations with finesse.
The process of chemical etching involves the selective removal of material from a metal sheet through a combination of chemical reactions. It starts by protecting specific areas of a metal sheet with a resistant material, leaving the desired pattern exposed.
Submerging the sheet into a corrosive solution then dissolves the unprotected metal, precisely etching away the exposed areas. This process allows for the creation of intricate patterns, precise apertures, and varying mesh sizes with unparalleled accuracy.
One of the most significant advantages of chemical etching in filter, screen, and sieve production lies in its ability to craft complex designs with micron-level precision. This precision facilitates the creation of filters and screens with uniform pore sizes, enabling more effective filtration of particles, gases, or liquids. Whether it’s for medical devices, aerospace components, or electronic applications, the customization possibilities offered by chemical etching are virtually limitless.
Furthermore, the versatility of chemical etching extends beyond mere precision. It supports the production of filters, screens, and sieves from a wide range of metals and alloys, including stainless steel, copper, aluminum, and titanium. This versatility in material selection enables manufacturers to tailor components according to specific application requirements, enhancing durability, corrosion resistance, and overall performance.
Another compelling aspect of chemical etching is its cost-effectiveness and scalability. Despite its high precision and intricate capabilities, chemical etching remains a remarkably cost-efficient process, especially for producing prototypes or small to medium batch sizes. Additionally, its scalability allows for seamless transition from prototyping to mass production without compromising on quality or precision.
In various industries, the demand for enhanced filtration systems continues to rise. Chemical etching has emerged as a driving force behind the evolution of filters, screens, and sieves, enabling advancements in sectors such as healthcare, environmental protection, automotive engineering, and more. Its role in improving filtration efficiency, reducing material waste, and enabling the production of bespoke components cannot be overstated.
Moreover, the continuous advancements in technology have further refined the chemical etching process, making it more environmentally friendly by reducing chemical waste and energy consumption. As sustainability becomes an increasingly integral aspect of manufacturing processes, the eco-friendliness of chemical etching stands as a testament to its future viability.
In conclusion, the integration of chemical etching in the production of filters, screens, and sieves signifies a paradigm shift in precision manufacturing. Its ability to offer unparalleled precision, versatility in design, material options, cost-effectiveness, and scalability makes it a cornerstone of modern filtration technology. As industries continue to push the boundaries of innovation, chemical etching remains poised to lead the charge toward more efficient, precise, and tailored filtration solutions across diverse applications.