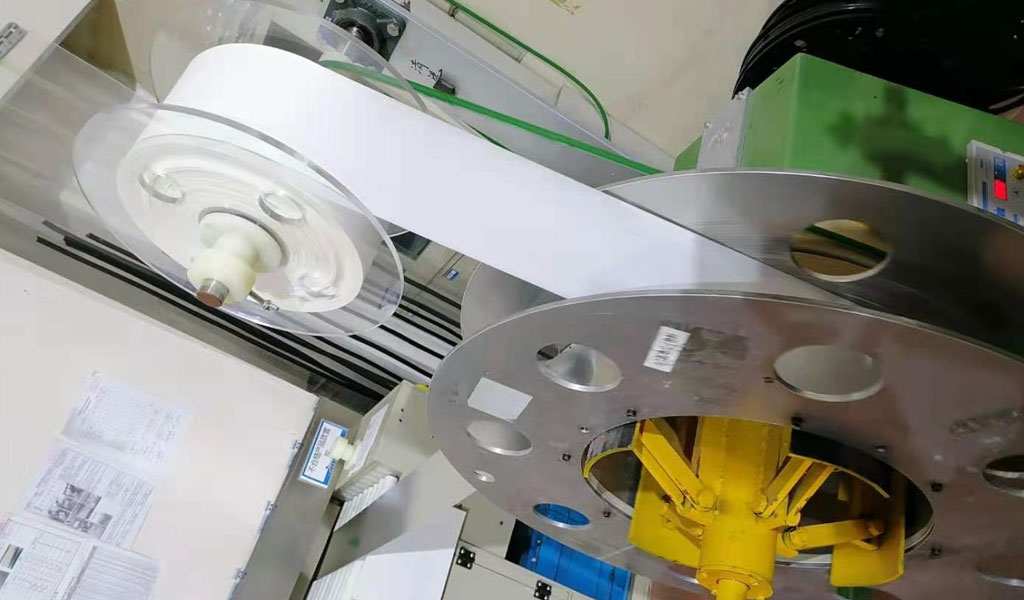
The development of fine chemical etching lies in the discovery of the chemical properties of photosensitive inks and photosensitive light sources. Using this property to carry out chemical reactions, complete raw materials can be processed into the required hollow shape according to appearance requirements or functional requirements. Since then, chemical etching has been widely used in the industrial field, processing a variety of different products to meet the needs of various industries.
The chip etching process flow is: surface cleaning – coating of photosensitive ink – drying – film exposure – development – drying – patching – etching – stripping – water washing – finished product
Traditional sheet etching processing is to first process the raw materials into individual parts (such as stainless steel sheets, copper sheets, etc.) by cutting or cutting. In the manufacturing process, due to the discontinuity of the sheets, the in-process and final processes Manual placement/closing of boards is required one by one, which is very labor intensive and cumbersome. During the operation, due to the operator’s strength or improper control of techniques, losses such as material collision or deformation are likely to occur. Therefore, this multi-process process of traditional wafer etching will greatly restrict production capacity and quality. Rate.
Let’s take a look at the roll-to-roll etching process?
Roll preparation – roll-to-roll cleaning – roll-to-roll lamination – roll-to-roll exposure – roll-to-roll development – roll-to-roll etching – roll-to-roll stripping – finished product
From the perspective of the process flow, the roll-to-roll etching process has several fewer steps than the chip etching process. The main reason is that there is no need to dry between processes, and roll-to-roll etching is automated, continuous and intact due to the roll-to-roll exposure and development. Due to these advantages, roll-to-roll etching can be performed directly after development without the need to make up the process.
Compared with the part-based production and relatively manual production of the traditional etching process, the roll-to-roll etching process realizes fully automated production provided by roll-to-roll equipment. Due to the setting of the equipment and the continuity of roll-to-roll, this etching mode The product quality is more stable and the accuracy is higher. At the same time, the fully automated production of roll-to-roll etching also greatly improves production efficiency and reduces labor intensity.
From an environmental protection point of view, the next step after chip etching is stripping, which requires the use of a release agent to remove the remaining photosensitive ink on the metal surface. The chemical reaction in this step will cause environmental pollution. In the roll-to-roll etching process, the dry film is peeled off in the stripping step. There is no need to use chemical solutions for chemical reactions, so no contamination will occur. Therefore, roll-to-roll etching is relatively environmentally friendly and will not cause environmental pollution problems.