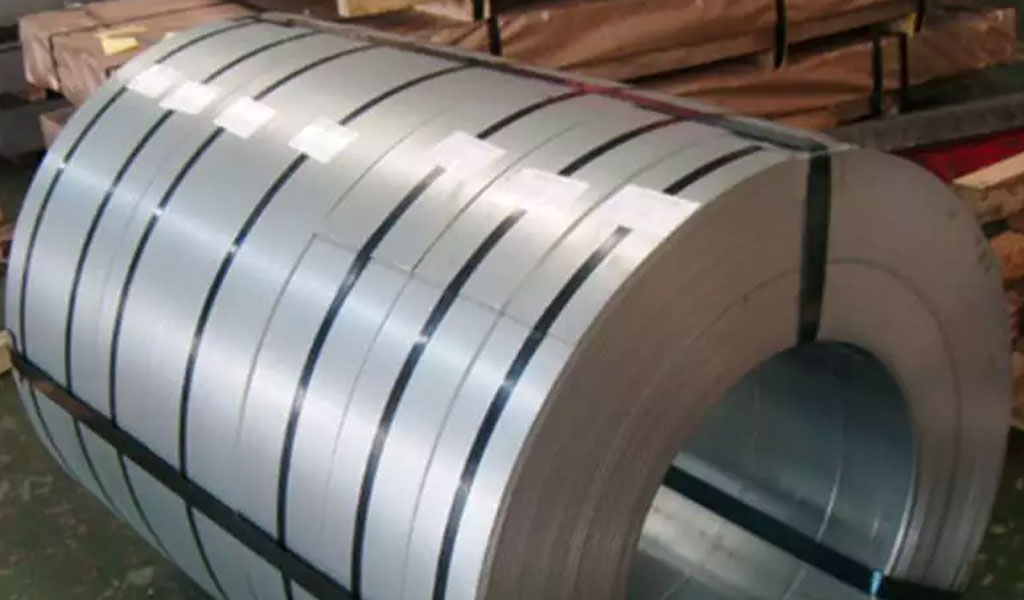
Metal etching is a sophisticated manufacturing process widely utilized across industries such as aerospace, electronics, automotive, and precision engineering to create intricate patterns, designs, or functional features on metal surfaces. This subtractive technique involves the selective removal of material from a metal substrate using chemical, electrochemical, or physical means. Commonly etched metals include stainless steel, copper, aluminum, titanium, and various alloys, each selected for their specific mechanical properties and applications. While the etching process itself is pivotal in achieving precision, the subsequent cleaning of etched metal parts is equally critical.
Residual etchants, contaminants, or byproducts left on the surface can compromise the integrity, functionality, and longevity of the components. Therefore, understanding and implementing effective cleaning methods is essential to ensure the quality of the final product.
The cleaning of etched metal parts is not a one-size-fits-all procedure. It varies depending on the type of metal, the etching technique employed (e.g., chemical etching, plasma etching, or laser etching), the nature of the etchant or residue, and the intended application of the part. This article provides an exhaustive exploration of the cleaning methods for metal etching parts, delving into the scientific principles, practical applications, and comparative analyses of various techniques. With an emphasis on clarity and detail, this discussion aims to serve as a comprehensive resource for engineers, researchers, and manufacturers seeking to optimize post-etching processes.
Fundamentals of Metal Etching and Residue Formation
Before delving into cleaning methods, it is imperative to understand the etching process and the types of residues it generates. Chemical etching, one of the most common methods, involves immersing a metal substrate in an acidic or alkaline solution—such as ferric chloride for copper or nitric acid for stainless steel—that selectively dissolves unprotected areas. This process leaves behind chemical residues, including metal salts, oxides, or unreacted etchant. Electrochemical etching, on the other hand, uses an electric current to drive material removal, often producing electrolytic byproducts or sludge. Physical etching techniques, such as plasma or laser etching, may introduce contaminants like carbon deposits or microscopic debris from vaporized material.
These residues can adhere to the surface through chemical bonding, physical entrapment in microcavities, or electrostatic forces. For instance, ferric chloride etching of copper may leave behind iron oxides or chloride salts, while plasma etching might deposit polymerized organic residues from the gas phase. The presence of such contaminants can lead to corrosion, poor adhesion in subsequent coating processes, or electrical malfunctions in microelectronic components. Thus, cleaning must address both the chemical composition and physical characteristics of these residues.
General Principles of Cleaning Etched Metal Parts
The cleaning of etched metal parts is governed by several overarching principles. First, the method must effectively remove all residues without damaging the etched features or altering the metal’s surface properties, such as its roughness, hardness, or passivation layer. Second, the process should be compatible with the metal’s chemistry—cleaning aluminum, for example, requires avoiding highly alkaline solutions that could cause pitting. Third, environmental and safety considerations play a role, as many traditional cleaning agents are hazardous or produce toxic waste. Finally, scalability and cost-effectiveness are critical for industrial applications, where large batches of parts must be processed efficiently.
Cleaning methods can be broadly categorized into wet processes (e.g., solvent-based, aqueous, or acid/base cleaning), dry processes (e.g., plasma cleaning or abrasive blasting), and hybrid approaches that combine elements of both. Each method has distinct advantages, limitations, and areas of applicability, which will be explored in detail in the following sections.
Wet Cleaning Methods
Solvent-Based Cleaning
Solvent-based cleaning involves the use of organic solvents to dissolve and remove residues from etched metal surfaces. Common solvents include acetone, isopropyl alcohol (IPA), trichloroethylene (TCE), and toluene, chosen based on their ability to solubilize specific contaminants. For example, acetone is effective at removing organic residues like photoresist left from photolithographic etching, while TCE excels at degreasing oily films.
The process typically involves immersion, spraying, or wiping the etched part with the solvent, often followed by rinsing with a secondary solvent or deionized water to prevent solvent residues. Ultrasonic agitation can enhance cleaning by dislodging trapped particles through cavitation—the formation and collapse of microscopic bubbles in the liquid. Solvent-based cleaning is particularly suited for precision components, such as microelectromechanical systems (MEMS), where water-based methods might cause oxidation.
However, solvents pose challenges. Many, like TCE, are volatile organic compounds (VOCs) with environmental and health risks, prompting stricter regulations. Additionally, they may not effectively remove inorganic residues like metal oxides, requiring a complementary method. Despite these drawbacks, solvent cleaning remains a staple in industries valuing speed and simplicity.
Aqueous Cleaning
Aqueous cleaning uses water-based solutions, often supplemented with detergents, surfactants, or chelating agents, to remove residues. This method is versatile, environmentally friendlier than solvents, and adaptable to a wide range of metals and contaminants. Neutral, acidic, or alkaline cleaners are selected based on the residue and metal type. For instance, a mild alkaline cleaner with sodium hydroxide might be used for stainless steel to remove organic residues, while a citric acid solution could clean copper without excessive corrosion.
The process often involves multiple steps: pre-rinsing to remove loose debris, immersion or spraying with the cleaning solution, ultrasonic agitation if needed, and final rinsing with deionized water to eliminate cleaner residues. Drying—via air jets, ovens, or vacuum—follows to prevent water spots or oxidation. Aqueous cleaning excels in batch processing and can be tailored with additives like corrosion inhibitors to protect sensitive metals like aluminum.
Limitations include the risk of water-induced corrosion for reactive metals (e.g., magnesium) and the need for wastewater treatment. Nonetheless, its adaptability and lower toxicity make it a preferred choice in many industrial settings.
Acid/Base Cleaning
For stubborn inorganic residues like oxides or salts, acid or base cleaning is employed. Acidic cleaners, such as dilute hydrochloric acid (HCl) or phosphoric acid, dissolve metal oxides and salts through protonation and complexation reactions. For example, HCl can remove iron oxide residues from stainless steel etched with ferric chloride. Alkaline cleaners, like potassium hydroxide solutions, are used for saponifying organic residues or neutralizing acidic etchants.
This method requires precise control of concentration, temperature, and exposure time to avoid over-etching or surface damage. Post-cleaning neutralization and rinsing are critical to remove residual acid or base. While highly effective, acid/base cleaning is less universal than aqueous methods due to its aggressive nature, making it ideal for specific applications like aerospace components requiring pristine surfaces.
Dry Cleaning Methods
Plasma Cleaning
Plasma cleaning uses a low-pressure gas (e.g., oxygen, argon, or a mixture) ionized into a plasma state to remove contaminants. The plasma generates reactive species—ions, electrons, and radicals—that break down organic residues into volatile compounds (e.g., CO₂ and H₂O) and dislodge inorganic particles via sputtering. Oxygen plasma is particularly effective for organic residues, while argon plasma excels at physical removal of debris.
This dry, solvent-free method is ideal for delicate etched parts, such as semiconductor wafers, where wet cleaning risks damage. It offers atomic-level precision and leaves no liquid residues, though it requires specialized equipment and is less effective for thick, bulk residues. Plasma cleaning’s high initial cost is offset by its repeatability and environmental benefits.
Abrasive Blasting
Abrasive blasting propels fine particles (e.g., glass beads, aluminum oxide, or walnut shells) at high velocity onto the etched surface to remove residues mechanically. This method is suited for robust metals like titanium or steel and excels at eliminating tenacious deposits like oxide scales. Parameters such as particle size, pressure, and angle of impact are adjusted to balance cleaning efficiency with surface integrity.
While fast and effective, abrasive blasting can alter surface roughness or embed particles, making it unsuitable for precision parts. It is commonly used in heavy industries like automotive manufacturing, where durability trumps finesse.
Hybrid Cleaning Approaches
Hybrid methods combine wet and dry techniques for enhanced results. For example, a part might undergo solvent cleaning to remove organic residues, followed by plasma cleaning for inorganic contaminants. Alternatively, aqueous cleaning with ultrasonic agitation might precede abrasive blasting for thorough residue removal. These approaches are tailored to complex etching processes or multi-material components, offering flexibility at the cost of increased process complexity.
Comparative Analysis of Cleaning Methods
To aid in method selection, the following tables compare key attributes of the discussed cleaning techniques.
Table 1: Cleaning Method Suitability by Metal Type
Method | Stainless Steel | Copper | Aluminum | Titanium | Notes |
---|---|---|---|---|---|
Solvent-Based | High | High | Moderate | High | Avoids water-induced corrosion |
Aqueous | High | Moderate | Low | High | Risk of pitting in aluminum |
Acid/Base | High | Low | Low | Moderate | Aggressive; metal-specific |
Plasma | High | High | High | High | Non-reactive, precise |
Abrasive Blasting | Moderate | Low | Low | High | Alters surface roughness |
Table 2: Effectiveness Against Residue Types
Method | Organic Residues | Inorganic Residues | Particulate Debris | Notes |
---|---|---|---|---|
Solvent-Based | High | Low | Moderate | Best for oils, photoresist |
Aqueous | High | Moderate | High | Versatile with additives |
Acid/Base | Moderate | High | Low | Targets oxides, salts |
Plasma | High | Moderate | High | Atomic-level cleaning |
Abrasive Blasting | Low | High | High | Mechanical removal |
Table 3: Practical Considerations
Method | Cost | Speed | Environmental Impact | Equipment Complexity |
---|---|---|---|---|
Solvent-Based | Moderate | High | High (VOCs) | Low |
Aqueous | Low | Moderate | Low | Moderate |
Acid/Base | Moderate | Low | Moderate | Low |
Plasma | High | Moderate | Low | High |
Abrasive Blasting | Moderate | High | Moderate (dust) | Moderate |
Case Studies in Cleaning Etched Metal Parts
Aerospace Industry: Titanium Turbine Blades
Titanium turbine blades, etched with hydrofluoric acid to enhance aerodynamics, require meticulous cleaning to remove fluoride residues. A hybrid approach—aqueous cleaning with chelating agents followed by plasma cleaning—ensures residue-free surfaces without compromising the metal’s fatigue resistance.
Electronics: Copper Circuit Boards
Copper circuit boards etched with ferric chloride undergo solvent-based cleaning with IPA to remove organic photoresist, followed by dilute HCl rinsing for chloride salts. This dual-step process preserves conductivity and solderability.
Environmental and Safety Considerations
Cleaning methods must balance efficacy with sustainability. Solvent-based cleaning’s VOC emissions necessitate ventilation and waste recovery systems. Aqueous and acid/base methods require wastewater neutralization, while dry methods like plasma cleaning minimize liquid waste but consume energy. Abrasive blasting generates dust, requiring filtration. Regulatory compliance (e.g., REACH, OSHA) shapes method selection, pushing industries toward greener alternatives.
Conclusion:Future Trends in Cleaning Technology
Advancements in cleaning etched parts include supercritical CO₂ cleaning, which uses pressurized carbon dioxide to dissolve residues without VOCs, and laser cleaning, which vaporizes contaminants with precision. These emerging technologies promise enhanced efficiency and reduced environmental footprints, though their adoption remains limited by cost and scalability.
Cleaning etched metal parts is a multifaceted process critical to ensuring component quality across industries. From solvent-based simplicity to plasma’s precision, each method offers unique strengths tailored to specific metals, residues, and applications. By understanding their scientific underpinnings and practical trade-offs—as illuminated by detailed comparisons—manufacturers can optimize post-etching workflows. As technology evolves, so too will cleaning methods, aligning performance with sustainability for future innovation.