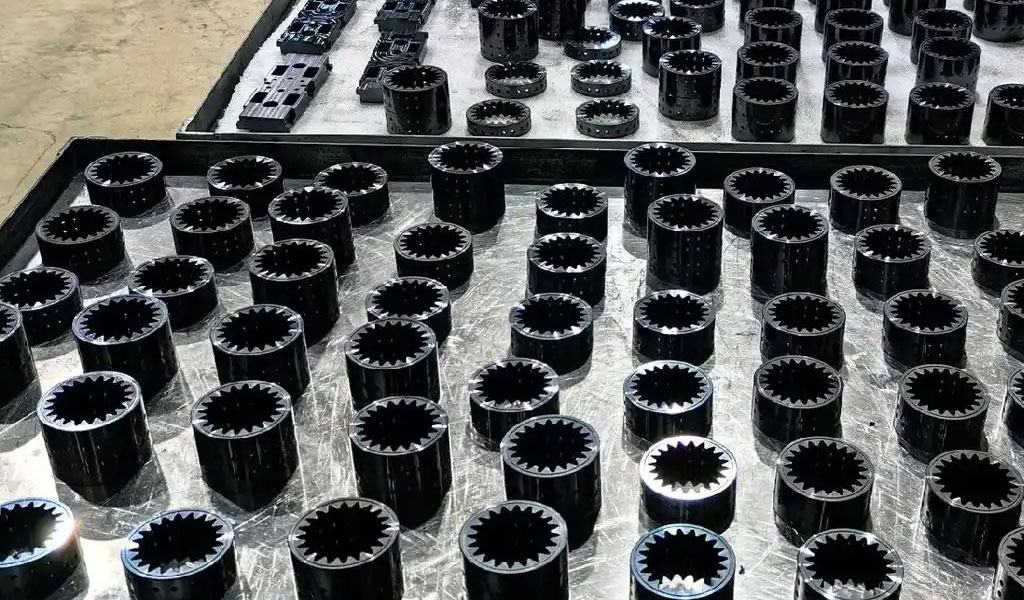
Diamond-like carbon (DLC) coatings have emerged as a revolutionary technology in the field of materials science, offering a versatile solution to the diverse needs of various industries. DLC coatings are characterized by their exceptional hardness, low friction, high wear resistance, and excellent biocompatibility. These properties make DLC an ideal choice for applications ranging from automotive and aerospace to medical devices and consumer electronics. This article delves into the scientific principles behind DLC technology, its manufacturing processes, and its cross-domain applications, providing a comprehensive overview of how DLC meets the needs of multiple industries.
Scientific Principles of DLC Technology
DLC coatings are composed of amorphous carbon with a significant fraction of sp³ hybridized bonds, similar to those found in diamond. The unique combination of sp³ and sp² hybridized bonds in DLC provides a balance between hardness and flexibility, making it suitable for a wide range of applications. The properties of DLC coatings can be fine-tuned by adjusting the deposition parameters, such as the type of precursor gas, substrate temperature, and deposition technique.
Types of DLC Coatings
DLC coatings can be categorized into several types based on their composition and properties:
- Hydrogenated DLC (a-C:H): Contains hydrogen and is deposited using hydrocarbon precursors. It offers good wear resistance and low friction.
- Tetrahedral Amorphous Carbon (ta-C): Contains a high fraction of sp³ bonds and is deposited using filtered cathodic vacuum arc (FCVA) or pulsed laser deposition (PLD) techniques. It exhibits extreme hardness and wear resistance.
- Metal-Containing DLC (Me-DLC): Incorporates metals such as titanium, chromium, or tungsten to enhance adhesion and tribological properties.
- Doped DLC: Incorporates elements such as silicon, nitrogen, or fluorine to modify the coating’s properties for specific applications.
Manufacturing Processes of DLC Coatings
The deposition of DLC coatings involves various techniques, each with its advantages and limitations. The choice of deposition method depends on the desired coating properties, substrate material, and application requirements.
Plasma-Enhanced Chemical Vapor Deposition (PECVD)
PECVD is a widely used technique for depositing a-C:H coatings. It involves the decomposition of hydrocarbon precursors in a plasma environment, allowing for the formation of a uniform and adherent coating. The process parameters, such as plasma power, gas flow rate, and substrate temperature, can be optimized to achieve the desired coating properties.
Filtered Cathodic Vacuum Arc (FCVA)
FCVA is a technique used for depositing ta-C coatings. It involves the evaporation of a graphite cathode in a vacuum arc, followed by the filtration of the plasma to remove macroparticles. The filtered plasma is then deposited onto the substrate, resulting in a coating with a high fraction of sp³ bonds. FCVA offers the advantage of producing coatings with extreme hardness and wear resistance.
Pulsed Laser Deposition (PLD)
PLD is another technique used for depositing ta-C coatings. It involves the ablation of a graphite target using a high-power laser, followed by the deposition of the ablated material onto the substrate. PLD offers the advantage of producing coatings with a high degree of control over the coating properties, but it is typically limited to small-scale applications.
Sputtering
Sputtering is a technique used for depositing Me-DLC coatings. It involves the bombardment of a metal target with energetic ions, resulting in the ejection of metal atoms that are then deposited onto the substrate along with carbon. Sputtering offers the advantage of producing coatings with enhanced adhesion and tribological properties.
Cross-Domain Applications of DLC Coatings
DLC coatings have found applications in various industries due to their unique combination of properties. The following sections provide an overview of the cross-domain applications of DLC coatings, highlighting their benefits and specific use cases.
Automotive Industry
In the automotive industry, DLC coatings are used to enhance the performance and durability of various components. The low friction and high wear resistance of DLC coatings make them ideal for applications such as engine pistons, camshafts, and fuel injectors. DLC coatings can reduce friction and wear, leading to improved fuel efficiency and extended component lifespan.
Table 1: Applications of DLC Coatings in the Automotive Industry
Component | Benefits of DLC Coating |
---|---|
Engine Pistons | Reduced friction, improved fuel efficiency |
Camshafts | Enhanced wear resistance, extended lifespan |
Fuel Injectors | Improved durability, reduced maintenance |
Gear Components | Reduced wear, improved performance |
Bearings | Enhanced lubrication, reduced friction |
Aerospace Industry
In the aerospace industry, DLC coatings are used to improve the performance and reliability of critical components. The high hardness and wear resistance of DLC coatings make them suitable for applications such as aircraft bearings, landing gear, and turbine blades. DLC coatings can withstand the harsh operating conditions of aerospace applications, providing long-term protection against wear and corrosion.
Table 2: Applications of DLC Coatings in the Aerospace Industry
Component | Benefits of DLC Coating |
---|---|
Aircraft Bearings | Enhanced wear resistance, reduced friction |
Landing Gear | Improved durability, reduced maintenance |
Turbine Blades | Enhanced corrosion resistance, extended lifespan |
Actuators | Improved performance, reduced wear |
Fasteners | Enhanced corrosion resistance, improved durability |
Medical Industry
In the medical industry, DLC coatings are used to enhance the biocompatibility and durability of medical devices. The excellent biocompatibility and low friction of DLC coatings make them ideal for applications such as orthopedic implants, surgical instruments, and dental tools. DLC coatings can reduce the risk of infection, improve tissue integration, and extend the lifespan of medical devices.
Table 3: Applications of DLC Coatings in the Medical Industry
Component | Benefits of DLC Coating |
---|---|
Orthopedic Implants | Improved biocompatibility, reduced infection risk |
Surgical Instruments | Enhanced durability, reduced wear |
Dental Tools | Improved performance, reduced friction |
Catheters | Enhanced biocompatibility, reduced thrombosis |
Stents | Improved durability, reduced restenosis |
Consumer Electronics Industry
In the consumer electronics industry, DLC coatings are used to enhance the durability and performance of various devices. The high hardness and wear resistance of DLC coatings make them suitable for applications such as smartphone screens, laptop keyboards, and wearable devices. DLC coatings can protect against scratches, improve touch sensitivity, and extend the lifespan of electronic components.
Table 4: Applications of DLC Coatings in the Consumer Electronics Industry
Component | Benefits of DLC Coating |
---|---|
Smartphone Screens | Improved scratch resistance, enhanced durability |
Laptop Keyboards | Reduced wear, improved performance |
Wearable Devices | Enhanced durability, reduced friction |
Touchscreens | Improved touch sensitivity, reduced wear |
Camera Lenses | Enhanced scratch resistance, improved clarity |
Industrial Machinery
In the industrial machinery sector, DLC coatings are used to enhance the performance and longevity of various components. The low friction and high wear resistance of DLC coatings make them ideal for applications such as cutting tools, molds, and dies. DLC coatings can reduce tool wear, improve machining efficiency, and extend the lifespan of industrial machinery.
Table 5: Applications of DLC Coatings in Industrial Machinery
Component | Benefits of DLC Coating |
---|---|
Cutting Tools | Reduced wear, improved machining efficiency |
Molds | Enhanced durability, reduced maintenance |
Dies | Improved performance, reduced wear |
Bearings | Enhanced lubrication, reduced friction |
Gears | Improved wear resistance, extended lifespan |
Comparative Analysis of DLC Coatings
To provide a comprehensive understanding of the advantages and limitations of DLC coatings, a comparative analysis with other coating technologies is essential. The following table compares DLC coatings with other commonly used coating materials in terms of their properties and applications.
Table 6: Comparative Analysis of DLC Coatings with Other Coating Technologies
Property/Application | DLC Coatings | TiN Coatings | CrN Coatings | WC/C Coatings |
---|---|---|---|---|
Hardness | Very High | High | High | High |
Wear Resistance | Excellent | Good | Good | Good |
Friction Coefficient | Very Low | Low | Low | Low |
Biocompatibility | Excellent | Poor | Poor | Poor |
Corrosion Resistance | Good | Good | Excellent | Good |
Thermal Stability | Good | Good | Good | Good |
Adhesion | Good | Good | Good | Good |
Cost | Moderate | Low | Low | High |
Applications | Automotive, Aerospace, Medical, Electronics, Industrial Machinery | Cutting Tools, Decorative Coatings, Industrial Machinery | Cutting Tools, Decorative Coatings, Industrial Machinery | Cutting Tools, Industrial Machinery |
Future Directions and Innovations
The field of DLC technology is continually evolving, with ongoing research and development aimed at enhancing the properties and expanding the applications of DLC coatings. Some of the future directions and innovations in DLC technology include:
- Nanocomposite DLC Coatings: Incorporating nanoparticles into DLC coatings to enhance their mechanical and tribological properties.
- Multilayer DLC Coatings: Developing multilayer DLC coatings with graded compositions to improve adhesion and performance.
- Environmentally Friendly Deposition Techniques: Exploring alternative deposition techniques that reduce the environmental impact of DLC coating processes.
- Advanced Characterization Techniques: Utilizing advanced characterization techniques such as atomic force microscopy (AFM) and X-ray photoelectron spectroscopy (XPS) to gain deeper insights into the structure and properties of DLC coatings.
- Industry-Specific Customization: Tailoring DLC coatings to meet the specific needs of different industries, such as developing biocompatible DLC coatings for medical applications or high-temperature-resistant DLC coatings for aerospace applications.
Conclusion
DLC technology represents a significant advancement in the field of materials science, offering a versatile and high-performance coating solution for multiple industries. The unique combination of hardness, wear resistance, low friction, and biocompatibility makes DLC coatings suitable for a wide range of applications, from automotive and aerospace to medical devices and consumer electronics. As research and development continue to push the boundaries of DLC technology, the potential for even more innovative and industry-specific applications is vast. The cross-domain coating revolution driven by DLC technology is poised to transform manufacturing processes and enhance the performance and durability of products across various sectors.