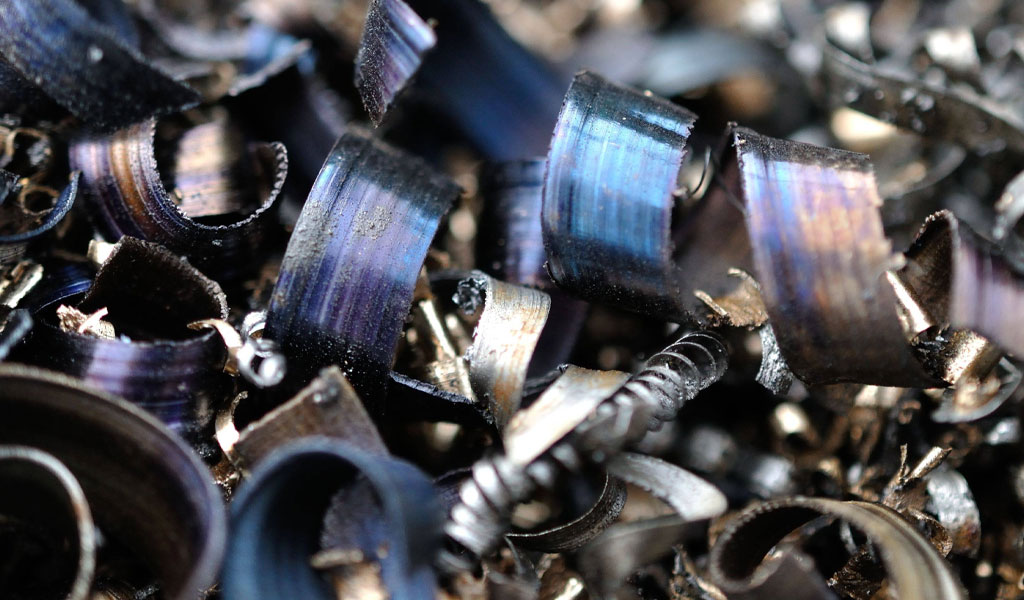
Metal etching, also known as chemical etching or photochemical machining, is a highly precise manufacturing process used to produce complex metal parts with intricate designs and tight tolerances. The chemical industry, which relies on a wide range of specialized equipment and components, often turns to metal etching to meet the demanding requirements of its operations. From filters and meshes to intricate flow-control components, the process enables the production of parts that would be difficult or impossible to create using conventional machining techniques. Below, we delve into the top 10 metal etching complex parts that are essential to the chemical industry, discussing their applications, materials, and advantages.
1. Precision Filters and Sieves
One of the most widely used etched components in the chemical industry is precision filters and sieves. These parts are essential for separating solid particles from liquids or gases, a process commonly found in chemical manufacturing, purification, and processing.
Applications:
- Separation of catalysts in chemical reactions.
- Filtration of fine particles in liquid processing.
- Gas purification in petrochemical and pharmaceutical applications.
Materials:
- Stainless steel, due to its corrosion resistance and durability.
- Monel and Hastelloy® for high-performance chemical resistance.
Advantages:
- Etched filters provide highly accurate aperture sizes, ensuring precise filtration levels.
- Unlike woven meshes, etched filters offer a uniform surface with no risk of wire displacement, which enhances reliability.
- The flexibility to create bespoke patterns enables optimization for specific chemical processes.
2. Custom Nozzles and Spray Discs
Nozzles and spray discs play a critical role in delivering liquids or gases in controlled patterns for various chemical processes. These components often feature intricate geometries to achieve optimal spray distribution, making etching the ideal manufacturing process.
Applications:
- Atomization of chemicals in reactors.
- Dispersion of cooling or cleaning agents in industrial equipment.
- Controlled spraying in agricultural and pharmaceutical chemical processes.
Materials:
- Stainless steel for general applications.
- Titanium for handling corrosive substances or high-temperature environments.
Advantages:
- Etching allows for the production of precise, uniform hole patterns that are essential for consistent spray performance.
- Smooth edges and burr-free features minimize turbulence and clogging.
- The ability to create highly complex designs at low tooling costs enables customization for unique chemical processes.
3. Heat Exchanger Plates
Chemical manufacturing processes often involve heat transfer, making heat exchanger plates a vital component. These plates require intricate patterns of channels and holes to maximize efficiency in transferring heat between fluids.
Applications:
- Cooling of chemical reactors.
- Heating or cooling in distillation columns.
- Temperature control in solvent recovery systems.
Materials:
- Stainless steel for general-purpose heat exchangers.
- Nickel alloys for applications requiring resistance to aggressive chemicals.
Advantages:
- Chemical etching allows for the production of thin, lightweight plates with precise channel geometries.
- The process supports complex designs that enhance heat transfer while reducing pressure drop.
- Etched plates can be manufactured with minimal lead times and setup costs compared to traditional machining.
4. Bipolar Plates for Electrochemical Cells
Bipolar plates are critical in electrochemical processes such as hydrogen production, fuel cells, and electrolysis. These plates feature intricate flow-field patterns that optimize the distribution of gases and liquids across the cell.
Applications:
- Proton exchange membrane (PEM) fuel cells.
- Electrolyzers for hydrogen production.
- Electrochemical synthesis of specialty chemicals.
Materials:
- Stainless steel for cost-effective solutions.
- Titanium for high-performance, corrosion-resistant applications.
Advantages:
- Etching enables the creation of precise flow-field designs, which are essential for maximizing efficiency.
- The process supports high-volume production of uniform plates with tight tolerances.
- Burr-free edges and smooth surfaces enhance performance and durability.
5. Catalyst Support Grids
Catalyst support grids are used to hold and support catalysts within reactors, facilitating efficient chemical reactions. These grids often require precise apertures to ensure optimal flow and contact between reactants and catalysts.
Applications:
- Petrochemical cracking.
- Ammonia synthesis.
- Polymerization reactions.
Materials:
- Stainless steel for standard chemical applications.
- Inconel for high-temperature and high-pressure environments.
Advantages:
- The chemical etching process enables the creation of intricate grid patterns with high precision.
- Uniform aperture sizes ensure consistent flow and distribution of reactants.
- The process is ideal for producing both prototypes and large-volume production runs.
6. Gas Diffusion Layers (GDLs)
Gas diffusion layers are an essential part of electrochemical cells, facilitating the even distribution of gases across a catalyst surface. These components require a fine balance between porosity, thickness, and electrical conductivity.
Applications:
- Fuel cells for chemical plants and energy storage.
- Electrolyzers for hydrogen generation.
- Battery systems in chemical manufacturing.
Materials:
- Stainless steel for durability and conductivity.
- Carbon-coated metal sheets for enhanced performance.
Advantages:
- Etched designs provide precise control over porosity and thickness.
- Burr-free surfaces ensure efficient gas flow and minimal resistance.
- The flexibility of etching allows for the rapid development of custom GDL designs.
7. Flow Restrictors
Flow restrictors regulate the flow rate of fluids or gases in chemical processes, ensuring consistent performance and safety. These components often feature highly complex geometries to achieve precise control.
Applications:
- Pressure regulation in chemical reactors.
- Controlled delivery of reactants in synthesis processes.
- Flow control in laboratory-scale chemical experiments.
Materials:
- Stainless steel for general applications.
- Hastelloy® for highly corrosive environments.
Advantages:
- Etched flow restrictors offer precise dimensions and tight tolerances.
- The chemical etching process ensures burr-free and uniform channels.
- Customization options enable the development of restrictors for specific flow rates and conditions.
8. Microfluidic Components
Microfluidic components are used in processes that involve the manipulation of small fluid volumes, such as in chemical analysis, synthesis, and mixing. These parts require intricate micro-scale patterns that are ideally suited for etching.
Applications:
- Lab-on-a-chip devices for chemical analysis.
- Microreactors for high-efficiency synthesis.
- Fluid mixing in precision chemical applications.
Materials:
- Stainless steel for durability and corrosion resistance.
- Titanium for biocompatibility and chemical inertness.
Advantages:
- Etching allows for the creation of highly complex microstructures with sub-micron precision.
- The process supports the production of thin, lightweight components with tight tolerances.
- Etched microfluidic components can be seamlessly integrated into larger systems.
9. Perforated Plates for Distillation Columns
Distillation is a core process in the chemical industry, requiring perforated plates to facilitate the efficient separation of components. These plates demand precise hole patterns to ensure optimal vapor-liquid contact.
Applications:
- Fractional distillation of hydrocarbons.
- Purification of solvents and chemicals.
- Separation of azeotropic mixtures.
Materials:
- Stainless steel for standard applications.
- Copper alloys for specialized chemical separations.
Advantages:
- Chemical etching produces uniform perforations with smooth edges, enhancing separation efficiency.
- The process supports complex patterns that optimize vapor and liquid flow.
- Customization options enable the development of plates for specific distillation requirements.
10. Etched Nameplates and Tags for Equipment Identification
While not a functional component, etched nameplates and tags are vital for identifying and labeling equipment in chemical plants. These items must withstand harsh environments and maintain legibility over time.
Applications:
- Equipment labeling in corrosive environments.
- Safety and warning signs for chemical processes.
- Identification of valves, pipes, and machinery.
Materials:
- Stainless steel for durability and readability.
- Brass and aluminum for aesthetic purposes.
Advantages:
- Etching provides permanent, legible markings that resist wear and corrosion.
- The process supports the creation of detailed logos, barcodes, and serial numbers.
- Etched nameplates can be customized to meet specific regulatory and operational requirements.
Conclusion
Metal etching is an indispensable process for producing complex parts in the chemical industry. From precision filters and nozzles to microfluidic components and heat exchanger plates, the ability to create intricate designs with exceptional accuracy and repeatability makes etching a preferred choice for manufacturers. By leveraging the versatility and precision of chemical etching, the chemical industry can meet the demands of modern production while ensuring reliability and efficiency in its operations.4o