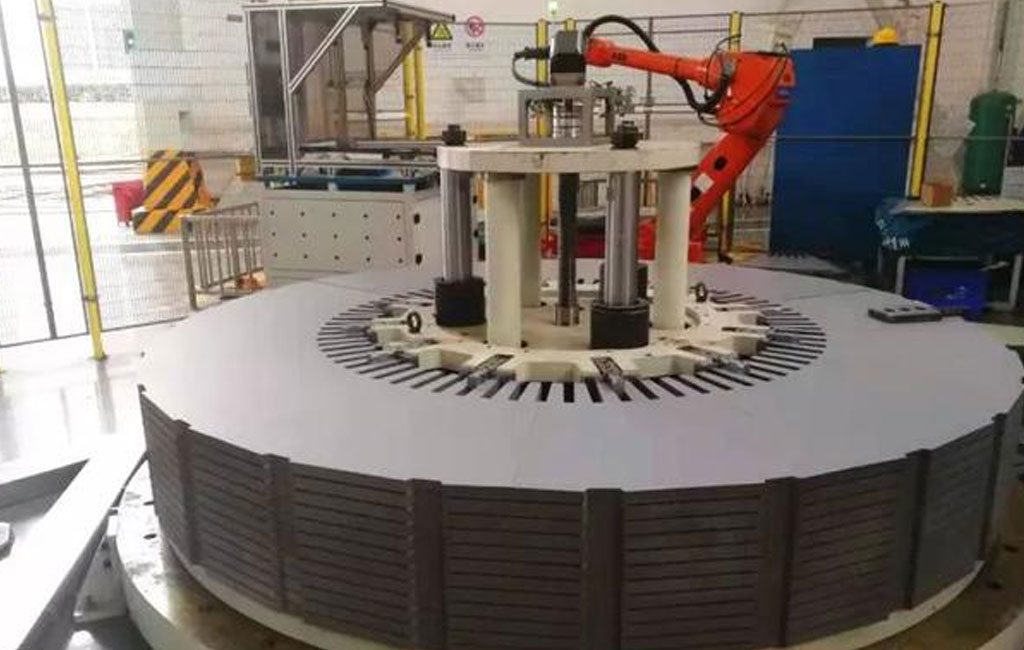
Motor lamination, a vital component in electric motors, lies at the heart of efficient energy conversion. The manufacturing of motor laminations is a critical process influencing motor performance, efficiency, and cost-effectiveness. Among the array of techniques available, stamping, laser cutting, and chemical etching stand out as primary methods, each offering distinct advantages and limitations. This article aims to delve into these manufacturing processes, offering a comprehensive comparison to elucidate their strengths and limitations.
Stamping
Stamping, a traditional method, involves feeding a sheet of electrical steel through a die to cut out individual laminations. This process, efficient for high-volume production, boasts relatively low tooling costs, making it economically viable. However, it presents challenges in intricate designs and tool maintenance due to wear and tear.
Laser Cutting
Laser cutting, an evolving technique, employs a high-powered laser to precisely cut laminations from a sheet. Its non-contact nature allows for intricate designs and rapid prototyping, making it suitable for low to medium volume production. Despite its flexibility and accuracy, laser cutting may encounter limitations in processing thicker materials and can generate heat-affected zones, potentially altering the material properties.
Chemical Etching
Chemical etching, a method gaining traction, utilizes chemical solutions to selectively dissolve metal and create intricate lamination shapes. It offers exceptional precision, enabling complex geometries and thin laminations, thus enhancing motor efficiency. Nevertheless, chemical etching necessitates meticulous control of parameters and involves environmental considerations due to chemical usage and disposal.
In terms of cost-effectiveness, stamping often prevails in high-volume production due to its low per-unit cost and established tooling. Conversely, laser cutting and chemical etching offer flexibility and precision, making them favorable for smaller batch productions and intricate designs, albeit with relatively higher per-unit costs.
Moreover, these methods differ in material utilization and waste generation. Stamping, despite its efficiency in high-volume runs, can produce considerable scrap material, impacting resource utilization. Conversely, laser cutting and chemical etching exhibit higher material efficiency by reducing waste, aligning with sustainable manufacturing practices.
When considering lead times, stamping typically offers shorter production cycles for established tooling, while laser cutting and chemical etching provide quicker turnaround times for design alterations and prototyping.
The choice of manufacturing process for motor laminations depends on various factors such as production volume, design complexity, cost considerations, and environmental concerns. Integrating a combination of these techniques may also offer a hybrid approach, optimizing benefits from each method based on specific requirements.
In conclusion, the selection of a suitable manufacturing process for motor laminations involves a careful evaluation of factors ranging from production volume and design intricacy to cost, waste generation, and environmental impact. While stamping, laser cutting, and chemical etching each possess unique advantages and limitations, their comparative analysis aids manufacturers in making informed decisions to meet the diverse demands of the electric motor industry.