In the modern era of advanced technology, the demand for smaller, more intricate satellite components has grown exponentially. To meet this demand, engineers and manufacturers have turned to innovative techniques such as chemical etching. Chemical etching, also known as chemical milling, is a precise and effective method used in the manufacturing of intricate parts, including those crucial for satellite systems. This article delves into the intricate process of chemical etching, its applications in satellite component fabrication, and the advancements in this technology that have enabled the creation of some of the most sophisticated satellite components to date.
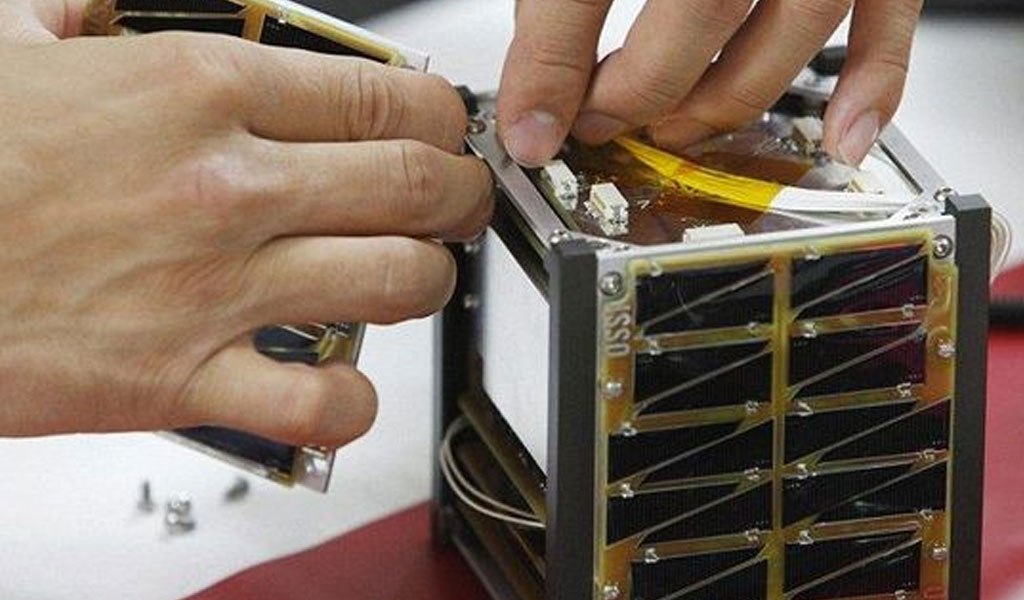
Understanding Chemical Etching
Chemical etching is a subtractive manufacturing process that involves using chemicals to selectively remove material from a metal sheet or plate to create intricate and precise patterns. This process is highly accurate and can achieve intricate designs that may be challenging or even impossible to achieve with traditional machining techniques. The process involves several key steps, including surface preparation, applying a photoresist mask, exposing the desired pattern, etching, and finally removing the mask to reveal the finished part.
Applications in Satellite Component Fabrication
The fabrication of satellite components demands high precision, reliability, and durability. Chemical etching has become an integral part of the satellite manufacturing process due to its ability to produce intricate, lightweight, and high-performance components. Some of the key satellite components that can be fabricated using chemical etching include:
1. Microstrip Antennas
Microstrip antennas are critical components of satellite communication systems. These antennas require precise dimensions and intricate patterns to ensure optimal performance. Chemical etching allows for the creation of these antennas with high accuracy and repeatability, enabling consistent and reliable communication between satellites and ground stations.
2. Flexible Printed Circuits
Satellite systems often require flexible printed circuits to accommodate complex geometries and tight spaces within the satellite structure. Chemical etching enables the production of flexible circuits with intricate pathways and connections, ensuring seamless data transmission and electrical connectivity within the satellite.
3. Radiation Shields
Satellites are exposed to various forms of radiation in space, which can potentially damage sensitive electronic components. Chemical etching facilitates the fabrication of radiation shields with intricate patterns and specific thicknesses to provide effective protection against harmful radiation, thereby ensuring the longevity and reliability of satellite systems.
4. Solar Array Panels
Solar array panels are crucial for providing power to satellites in space. Chemical etching is used to create precise patterns on solar array panels, optimizing their efficiency and power generation capabilities. By fine-tuning the surface properties of these panels, chemical etching plays a significant role in enhancing the overall performance and lifespan of satellite power systems.
5. Heat Sinks and Thermal Management Components
Managing heat dissipation is a critical aspect of satellite design, as excess heat can degrade the performance of sensitive components. Chemical etching enables the fabrication of intricate heat sinks and thermal management components that efficiently dissipate heat and maintain optimal operating temperatures within the satellite, thereby ensuring the overall functionality and longevity of the satellite system.
Advancements in Chemical Etching Technology
Over the years, significant advancements have been made in chemical etching technology, further enhancing its capabilities and applications in satellite component fabrication. Some notable advancements include:
1. Improved Chemical Formulations
The development of advanced chemical formulations has significantly enhanced the precision and efficiency of the etching process. These improved chemicals enable more precise control over material removal rates, resulting in the production of highly intricate and complex designs with minimal material waste.
2. Enhanced Etching Equipment
The integration of advanced automation and computer-controlled systems in etching equipment has streamlined the fabrication process and improved overall production efficiency. Automated systems enable the precise control of etching parameters, ensuring consistent and accurate results, even for large-scale production of intricate satellite components.
3. Digital Design Integration
The integration of digital design tools and software has revolutionized the way intricate patterns and designs are created for chemical etching. Advanced computer-aided design (CAD) software allows engineers to generate complex designs with high precision and intricacy, which can be directly translated into the etching process, further improving the accuracy and reliability of the final satellite components.
4. Material Innovation
The development of new materials and alloys that are compatible with chemical etching processes has expanded the range of applications for satellite component fabrication. These innovative materials offer improved strength, durability, and resistance to harsh environmental conditions, making them ideal for use in satellite systems operating in challenging space environments.
Future Prospects and Challenges
While chemical etching has proven to be an indispensable technique in satellite component fabrication, several challenges and opportunities lie ahead. Some of the key prospects and challenges include:
1. Miniaturization and Integration
The ongoing trend toward miniaturization and integration in satellite design poses a challenge for chemical etching techniques to achieve even higher precision and intricacy in the fabrication of miniature components. The development of new methodologies and technologies to address these challenges will be crucial for meeting the evolving demands of the satellite industry.
2. Sustainability and Environmental Impact
The chemicals used in the etching process can have an environmental impact if not handled properly. As the focus on sustainability grows, there is a need for the development of eco-friendly etching solutions that minimize environmental harm without compromising the precision and efficiency of the process.
3. Integration of Additive Manufacturing Techniques
Combining chemical etching with additive manufacturing techniques offers the potential to create hybrid manufacturing processes that leverage the strengths of both technologies. This integration could lead to the development of novel satellite components with complex geometries and multifunctional capabilities, further advancing the capabilities of satellite systems in space.
4. Standardization and Quality Control
Ensuring consistent quality and performance of satellite components is crucial for the reliability and longevity of satellite systems. The establishment of standardized processes and stringent quality control measures will be essential in maintaining the high standards required for satellite components fabricated using chemical etching.
Conclusion
Chemical etching has emerged as a fundamental manufacturing process for producing intricate and high-precision satellite components. Its ability to create complex designs with exceptional accuracy has revolutionized the satellite industry, enabling the development of smaller, more efficient, and reliable satellite systems. With ongoing advancements in technology and materials, the future of chemical etching holds the promise of further enhancing the capabilities and applications of satellite component fabrication, paving the way for the continued exploration and utilization of space for the benefit of humanity.