Etching is a widely utilized technique across various disciplines, including dentistry, materials science, and industrial applications, where a controlled chemical or physical process is employed to remove material from a surface to achieve specific functional or aesthetic outcomes. In dental practice, etching is commonly associated with the preparation of enamel or dentin surfaces for bonding restorative materials, while in materials science and engineering, it is used to prepare metal, semiconductor, or concrete surfaces for further processing or analysis. A phenomenon frequently observed post-etching, regardless of the material or context, is the appearance of white spots or residues on the treated surface. These white spots can have diverse origins, implications, and management strategies depending on the substrate and etching process involved. This article provides a comprehensive exploration of the nature, causes, mechanisms, and management of white spots observed after etching, with a focus on dental, metallurgical, and concrete applications, supported by detailed comparative analyses and scientific insights.
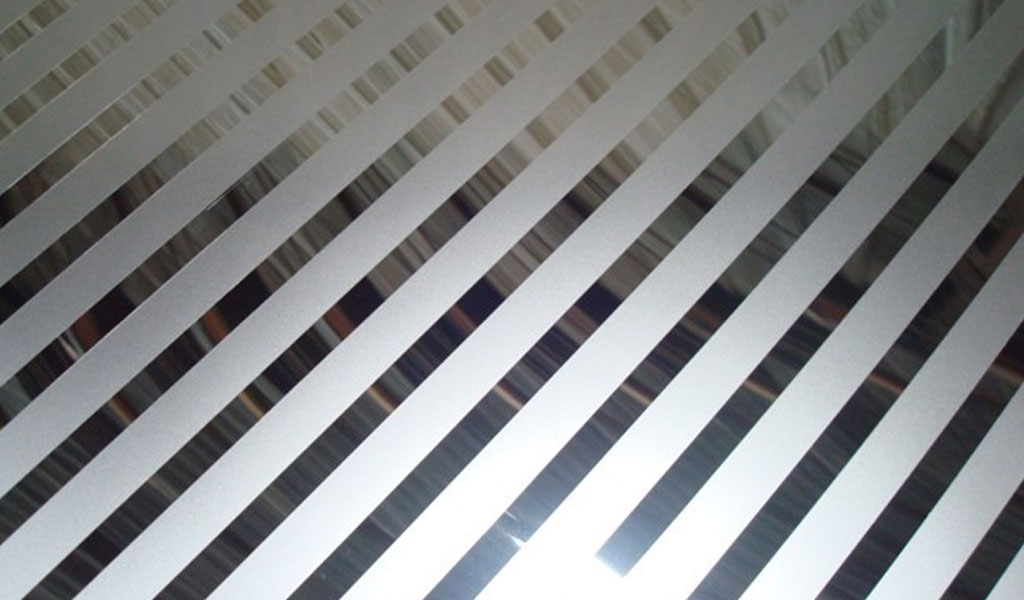
Etching and White Spots
Etching involves the selective removal of material from a surface using chemical agents (e.g., acids or alkalis), mechanical processes, or plasma-based techniques. The process alters the surface topography, chemical composition, or microstructure to facilitate subsequent treatments, such as bonding, coating, or microscopic examination. In dentistry, acid etching with phosphoric or hydrochloric acid is used to create a micro-porous enamel surface for adhesive bonding. In materials science, etching reveals microstructural features of metals or semiconductors, while in concrete applications, it prepares surfaces for coatings like epoxy. Despite its utility, etching often results in unintended surface changes, one of which is the formation of white spots.
White spots are visible alterations on the etched surface, appearing as opaque, chalky, or powdery areas that contrast with the surrounding material. These spots may arise from chemical residues, microstructural changes, demineralization, or surface contamination. Their presence can compromise the aesthetic, functional, or structural integrity of the treated surface, making their study critical across disciplines. This article examines the multifaceted nature of white spots, integrating findings from scientific literature and practical applications to elucidate their causes, characteristics, and management.
White Spots in Dental Etching
Mechanisms of White Spot Formation in Dentistry
In dental practice, white spots are most commonly associated with acid etching during orthodontic or restorative procedures. Acid etching, typically using 35–37% phosphoric acid or 15% hydrochloric acid, removes the smear layer and creates a micro-porous enamel surface to enhance bonding of adhesives or resin infiltrants. However, this process can lead to unintended consequences, particularly the formation of white spot lesions (WSLs).
WSLs are areas of enamel demineralization that appear as chalky white patches due to the loss of minerals, primarily calcium and phosphate, from the enamel matrix. These lesions are caused by the acidic dissolution of hydroxyapatite, the primary mineral component of enamel. During etching, the acid penetrates the enamel surface, dissolving mineral content and creating micro-porosities. If the etching process is excessive—either in duration or acid concentration—it can exacerbate demineralization, leading to visible white spots. Additionally, pre-existing conditions such as dental fluorosis or hypomineralization can become more pronounced after etching, as the acid highlights subsurface porosities.
Research indicates that WSLs are a significant concern in orthodontics, where fixed appliances (e.g., brackets) promote plaque accumulation, further exacerbating demineralization around the etched areas. A study by Abufarwa et al. (2018) found that 15 seconds of 37% phosphoric acid etching caused a significant increase in lesion area and a decrease in fluorescence intensity, indicating enamel demineralization, though it did not increase susceptibility to further demineralization during pH cycling. This suggests that while etching itself initiates WSLs, subsequent environmental factors, such as oral hygiene, play a critical role in their progression.
Clinical Implications of White Spots in Dentistry
The appearance of white spots after dental etching poses both aesthetic and functional challenges. Aesthetically, WSLs detract from the smile, particularly in anterior teeth, leading to patient dissatisfaction. Functionally, these lesions represent weakened enamel that is more susceptible to caries if not addressed. The progression of WSLs can lead to cavitation, requiring invasive restorative interventions.
Orthodontic patients are particularly vulnerable due to the prolonged presence of fixed appliances, which hinder oral hygiene and promote plaque retention. A randomized controlled trial by Horan et al. (2023) compared total etching (TE) and partial etching (PE) protocols, finding that TE resulted in higher WSL formation rates at six months, though no long-term differences were observed. This highlights the importance of minimizing etching extent to reduce iatrogenic damage.
Management Strategies for Dental White Spots
Managing white spots in dentistry involves preventive, remineralizing, and restorative approaches. Preventive strategies focus on optimizing oral hygiene and reducing plaque accumulation. Patients are advised to use fluoride toothpastes, mouthwashes, and varnishes to promote remineralization. Xylitol chewing gum and chlorhexidine varnishes have also been shown to reduce plaque acidity and cariogenic bacteria, respectively.
Remineralization therapies aim to restore mineral content to WSLs. Casein phosphopeptide-amorphous calcium phosphate (CPP-ACP) products, such as MI Paste, facilitate the delivery of bioavailable calcium and phosphate ions to the enamel subsurface, promoting remineralization. A clinical case reported by Limberakis (2011) demonstrated that repeated etching followed by MI Paste application over six months significantly reduced WSL visibility, even with suboptimal patient compliance.
For persistent WSLs, resin infiltration using low-viscosity resins (e.g., Icon) offers a minimally invasive solution. This technique involves etching with 15% hydrochloric acid to open enamel porosities, followed by resin infiltration to fill micropores and camouflage the lesion. Studies, such as one by Ziad and Alfares (2021), have shown that multiple etching cycles (up to two minutes) improve cosmetic outcomes by enhancing resin penetration. However, excessive etching cycles (beyond seven) can lead to significant enamel loss, as noted in a study by ScienceDirect (2023).
Restorative options, such as microabrasion, composite bonding, or veneers, are reserved for severe cases where remineralization or infiltration is insufficient. Microabrasion removes superficial enamel layers to eliminate stains, while bonding and veneers cover WSLs with tooth-colored materials. These approaches, while effective, are more invasive and costly.
Table 1: Comparison of Dental Etching Techniques and White Spot Outcomes
Etching Technique | Acid Used | Duration | White Spot Formation Risk | Management Strategies | References |
---|---|---|---|---|---|
Total Etching (TE) | 37% Phosphoric Acid | 15–30 s | Higher risk at 6 months; no long-term difference | Fluoride, CPP-ACP, resin infiltration | , |
Partial Etching (PE) | 37% Phosphoric Acid | 15 s | Lower risk at 6 months; similar long-term outcomes | Fluoride, CPP-ACP, oral hygiene | , |
Selective Etching | 30% Phosphoric Acid | 15 s | Reduced risk with customized guides | Oral hygiene, remineralization | |
Hydrochloric Acid Etching | 15% HCl | 20–120 s | Moderate risk; multiple cycles improve resin infiltration | Resin infiltration, fluoride | , |
No Etching (Control) | None | N/A | Minimal risk; baseline WSLs may persist | Fluoride, CPP-ACP, microabrasion |
White Spots in Metallurgical Etching
Mechanisms of White Spot Formation in Metals
In materials science, etching is employed to reveal the microstructure of metals and alloys for metallographic analysis or to prepare surfaces for coating or bonding. Chemical etching with acids (e.g., nital, picral) or electrochemical etching removes surface layers to expose grain boundaries, phases, or defects. White spots in this context often manifest as white etching areas (WEAs) or white etching cracks (WECs), particularly in high-strength steels used in bearings or gears.
WEAs are microstructural alterations that appear white under optical microscopy after etching with nital (nitric acid in ethanol). These areas result from severe plastic deformation, phase transformations, or chemical reactions induced by mechanical stress, electrical current, or hydrogen ingress during service. WECs are cracks associated with WEAs, often leading to premature failure in rolling contact fatigue (RCF) applications, such as wind turbine bearings. A study by ScienceDirect (2016) identified bearing seat form deviations as a root cause, where tensile stresses initiate subsurface cracks decorated with WEAs.
The formation of WEAs involves complex mechanisms, including carbide dissolution, carbon redistribution, and the formation of nanocrystalline structures. Electron backscatter diffraction (EBSD) analysis has shown that WEAs consist of nanostructured material with altered carbon and chromium contents, resulting from high-pressure torsion or RCF. Electrical current flow, slip, and polarity further amplify WEC formation by inducing localized plasticity and hydrogen embrittlement.
Implications of White Spots in Metallurgical Applications
WEAs and WECs are critical concerns in industries reliant on high-performance bearings, such as wind energy and automotive sectors. Their presence indicates material degradation, reducing component lifespan and reliability. For example, premature bearing failure in wind turbine gearboxes due to WECs can lead to significant economic losses. The white appearance of WEAs under microscopy is attributed to their higher hardness and altered microstructure, which resist etching compared to the surrounding matrix.
Management and Prevention in Metallurgical Etching
Preventing WECs requires addressing root causes, such as bearing seat form deviations, excessive tensile stresses, and environmental factors like hydrogen ingress. Finite element (FE) simulations have demonstrated that minimizing waviness in bearing seats reduces tensile stress, thereby mitigating WEC initiation. Lubricant selection also plays a role, with polyalkylene glycol-based oils showing reduced WEA formation compared to synthetic hydrocarbons in some steels.
Material modifications, such as using 8% Cr steel instead of 100Cr6, can reduce carbide deformation and WEA formation due to higher chromium content stabilizing the microstructure. Additionally, controlling electrical current flow and polarity in bearing applications minimizes hydrogen-induced WECs. For metallographic analysis, careful etching with dilute acids and thorough rinsing prevents residual white spots from chemical precipitates.
Table 2: Comparison of White Etching Areas in Metallurgical Applications
Material | Etching Agent | White Spot Type | Cause | Prevention Strategies | References |
---|---|---|---|---|---|
100Cr6 Steel | Nital (2–5%) | White Etching Area (WEA) | Carbide dissolution, RCF | Optimized bearing design, lubricant selection | |
8% Cr Steel | Nital (2–5%) | WEA/WEC | Reduced carbide deformation | High-Cr alloys, stress reduction | |
55SiMo8 Steel | Nital (2–5%) | WEA | High-frequency dynamic loading | Material selection, controlled etching | |
AISI 52100 | Nital (2–5%) | WEA/WEC | Plastic deformation, hydrogen ingress | Electrical insulation, lubricant optimization |
White Spots in Concrete Etching
Mechanisms of White Spot Formation in Concrete
In concrete applications, acid etching with muriatic acid (diluted hydrochloric acid) or citric acid is used to prepare surfaces for epoxy coatings or sealants. The process removes laitance (a weak surface layer) and opens pores to enhance coating adhesion. However, a common issue post-etching is the appearance of a white, powdery film or dust on the surface, often mistaken for etching residue.
This white film is primarily calcium carbonate or calcium dust leached from the concrete matrix during acid etching. Muriatic acid reacts with calcium hydroxide in the cement paste, forming soluble calcium chloride, which can precipitate as calcium carbonate upon drying if not thoroughly rinsed. A discussion on The Garage Journal (2011) noted that this residue adheres loosely to the surface and can be removed with pressure washing or additional rinsing, but if left, it compromises coating adhesion.
The formation of white spots in concrete is exacerbated by over-etching, where excessive acid or prolonged exposure dissolves more calcium than necessary, leaving a porous, weakened surface. Environmental factors, such as high humidity or inadequate drying, can also contribute by trapping residual acid or precipitates.
Implications for Concrete Applications
The white film on etched concrete surfaces poses significant challenges for coating applications. If not removed, it acts as a contaminant, reducing the bond strength between the concrete and epoxy or sealant. This can lead to coating delamination, peeling, or failure, particularly in high-traffic areas like garage floors. Aesthetically, the white spots are undesirable, especially on decorative concrete surfaces.
Management and Prevention in Concrete Etching
Effective management of white spots in concrete etching requires meticulous surface preparation and post-etching treatment. Key strategies include:
- Thorough Rinsing: Multiple rinse cycles with clean water neutralize residual acid and remove calcium precipitates. Pressure washing is highly effective for large surfaces.
- Neutralization: Applying a baking soda solution after etching neutralizes residual acid, preventing further calcium leaching.
- Controlled Etching: Limiting acid exposure to 5–10 minutes and working in small sections prevents over-etching, especially in hot weather.
- Drying: Allowing the surface to dry completely before coating application ensures no trapped moisture or precipitates interfere with adhesion.
For persistent white spots, re-etching with a milder acid solution or mechanical abrasion (e.g., sanding) may be necessary. Using chelating agents to remove metal stains absorbed by porous spots, as suggested in pool plaster applications, can also be adapted for concrete.
Table 3: Comparison of White Spot Formation in Concrete Etching
Etching Agent | White Spot Type | Cause | Management Strategies | References |
---|---|---|---|---|
Muriatic Acid (10–20% HCl) | Calcium Carbonate Dust | Calcium leaching, incomplete rinsing | Pressure washing, neutralization | |
Citric Acid (0.05 M) | Calcium Precipitates | Acid dissolution of cement paste | Multiple rinsing, controlled etching | |
Phosphoric Acid (30%) | Minimal Residue | Less aggressive etching | Rinsing, drying | |
No Etching (Mechanical) | None | No chemical reaction | Surface cleaning | N/A |
Comparative Analysis Across Disciplines
Commonalities in White Spot Formation
Despite the differences in materials and etching purposes, white spots across dental, metallurgical, and concrete applications share common themes:
- Chemical Residues: In dentistry, WSLs result from demineralization residues; in concrete, calcium carbonate precipitates form; in metals, WEAs involve altered microstructures resisting etching.
- Surface Alteration: All white spots reflect changes in surface composition or topography, whether through mineral loss, phase transformation, or precipitate deposition.
- Management Challenges: Effective management requires balancing etching extent with surface integrity, followed by thorough cleaning or remineralization.
Differences and Context-Specific Factors
The nature of white spots varies significantly by material and application:
- Dental Etching: Focuses on biological tissues (enamel, dentin), where white spots indicate health risks (caries) and aesthetic issues. Management prioritizes biocompatibility and minimally invasive techniques.
- Metallurgical Etching: Involves inorganic materials (steels, alloys), where white spots signal mechanical or chemical degradation. Prevention emphasizes material and environmental control.
- Concrete Etching: Deals with composite materials (cement, aggregates), where white spots are surface contaminants affecting coating performance. Management is primarily mechanical (rinsing, washing).
Table 4: Cross-Disciplinary Comparison of White Spots After Etching
Discipline | Material | White Spot Type | Primary Cause | Impact | Management | References |
---|---|---|---|---|---|---|
Dentistry | Enamel | White Spot Lesions | Demineralization | Aesthetic, caries risk | Fluoride, resin infiltration | , |
Metallurgy | Steel/Alloys | White Etching Areas | Microstructural change | Component failure | Material selection, stress control | , |
Concrete | Cement | Calcium Carbonate | Calcium leaching | Coating failure | Rinsing, neutralization | , |
Scientific Insights and Future Directions
Advanced Analytical Techniques
Understanding white spots requires advanced analytical tools. In dentistry, quantitative light-induced fluorescence (QLF) and transverse microradiography quantify WSL depth and mineral loss. In metallurgy, EBSD and energy-dispersive X-ray spectroscopy (EDS) reveal WEA composition and structure. For concrete, scanning electron microscopy (SEM) examines precipitate morphology. Integrating these techniques across disciplines could enhance cross-disciplinary insights.
Emerging Technologies
Innovations in etching and white spot management are emerging. Self-etching resin infiltrants in dentistry reduce the need for acid pre-treatment, minimizing WSL risk. In metallurgy, advanced coatings and lubricants mitigate WEC formation. In concrete, eco-friendly etching agents (e.g., organic acids) reduce environmental impact while maintaining efficacy. Future research should focus on optimizing these technologies for scalability and cost-effectiveness.
Interdisciplinary Collaboration
The similarities in white spot formation suggest opportunities for interdisciplinary collaboration. For example, dental remineralization strategies (e.g., CPP-ACP) could inspire surface stabilization techniques in concrete. Similarly, metallurgical stress management approaches could inform dental etching protocols to minimize iatrogenic damage. Collaborative research could yield universal principles for etching optimization.
Conclusion
White spots after etching are a complex phenomenon with diverse manifestations across dentistry, metallurgy, and concrete applications. In dentistry, they represent demineralized enamel lesions requiring preventive and restorative interventions. In metallurgy, they indicate microstructural changes threatening component reliability. In concrete, they are chemical residues compromising coating adhesion. Despite these differences, common mechanisms—chemical residues, surface alterations, and management challenges—underscore the need for precise etching control and post-treatment strategies. By integrating advanced analytics, emerging technologies, and interdisciplinary insights, researchers and practitioners can mitigate the adverse effects of white spots, enhancing the efficacy and safety of etching processes across fields.