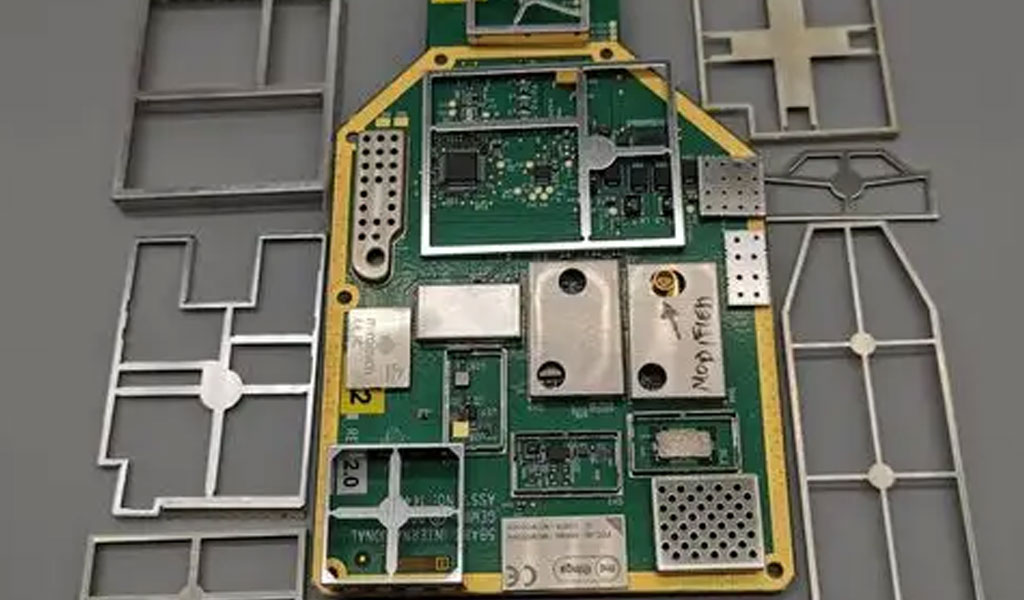
Electromagnetic interference (EMI) poses significant challenges in modern electronic systems, particularly in densely populated circuit boards and highly integrated devices. Board-level electromagnetic interference (EMI) shielding is a critical technology designed to mitigate these challenges by reducing or eliminating the adverse effects of EMI on the functionality of electronic components. This shielding plays a vital role in ensuring compliance with electromagnetic compatibility (EMC) standards and maintaining the reliability of electronic systems in diverse applications, ranging from consumer electronics to aerospace and medical devices.
Understanding Electromagnetic Interference (EMI)
Electromagnetic interference occurs when an electromagnetic field from one electronic device disrupts the operation of another. This interference can manifest in various forms, including radiated and conducted emissions. Radiated EMI involves the transmission of electromagnetic waves through the air, while conducted EMI refers to interference carried through electrical connections, such as power lines or signal traces.
The sources of EMI are diverse and can include natural phenomena, such as lightning and solar activity, as well as man-made sources like power lines, radio frequency (RF) transmitters, and other electronic devices. In circuit boards, EMI can originate from high-speed switching components, power supplies, and unintentional emissions from poorly shielded devices.
The Necessity of Board-Level EMI Shielding
Board-level EMI shielding addresses interference at the printed circuit board (PCB) level, where components are densely arranged, and signal integrity is paramount. The necessity for EMI shielding arises from several key factors:
- Miniaturization of Electronics
As electronic devices become smaller and more compact, components are positioned closer together on PCBs. This proximity increases the likelihood of electromagnetic coupling between components, leading to crosstalk and signal degradation. - Higher Operating Frequencies
Modern electronic devices operate at increasingly high frequencies, resulting in stronger electromagnetic emissions. These emissions can interfere with adjacent components or devices, necessitating effective shielding. - Stringent Regulatory Standards
Many countries enforce stringent EMC standards to limit EMI emissions and susceptibility in electronic devices. Failure to comply with these standards can lead to product recalls, financial penalties, and reputational damage. - Critical Applications
In applications such as medical devices, automotive electronics, and aerospace systems, EMI can have life-threatening consequences. Ensuring robust EMI shielding is essential for maintaining system reliability and safety.
Materials Used in Board-Level EMI Shielding
The selection of materials for board-level EMI shielding is crucial to achieving effective mitigation of electromagnetic interference. These materials are chosen based on their electromagnetic properties, manufacturability, and compatibility with electronic components. Common materials include:
- Metals
Metals such as copper, aluminum, and stainless steel are widely used due to their excellent electrical conductivity and ability to reflect electromagnetic waves. These materials are often used in the form of shielding cans, enclosures, or foil layers. - Metalized Plastics
Metalized plastics are lightweight and cost-effective alternatives to solid metal shields. These materials are created by coating plastic substrates with a thin layer of conductive metal, providing adequate shielding while reducing weight. - Conductive Elastomers
Conductive elastomers combine the flexibility of rubber with the conductivity of metal particles. These materials are used in gaskets and seals to create an EMI-tight enclosure around sensitive components. - Composite Materials
Composite materials, such as carbon-filled polymers and fiber-reinforced plastics, offer a balance of strength, weight, and electromagnetic shielding effectiveness. These materials are particularly useful in applications where weight reduction is critical. - Thin Film Coatings
Thin film coatings, such as vacuum-deposited metals or conductive paints, provide a lightweight and space-efficient shielding solution. These coatings are commonly applied to plastic housings or directly onto PCBs.
Board-Level Shielding Techniques
The implementation of EMI shielding at the board level involves a combination of design strategies, material selection, and manufacturing processes. Key techniques include:
Shielding Cans
Shielding cans are metal enclosures placed over sensitive components or areas of a PCB to block electromagnetic emissions. These cans are typically made from stamped or machined metal and are secured to the board using soldering or mechanical clips. Shielding cans are effective for high-frequency EMI and are widely used in RF and microwave applications.
Ground Planes
A ground plane is a conductive layer integrated into the PCB stack-up, providing a reference potential for signals and acting as a shield against EMI. Ground planes reduce radiated emissions and improve signal integrity by minimizing return path inductance. Proper grounding techniques, such as the use of vias and low-impedance connections, are essential for maximizing the effectiveness of ground planes.
Shielded Traces
Shielded traces involve surrounding signal-carrying traces with grounded conductors to minimize crosstalk and external interference. This technique is particularly important for high-speed digital and analog signals, where maintaining signal integrity is critical.
Enclosures and Covers
Metal enclosures and covers provide comprehensive shielding for entire PCBs or devices. These structures block external EMI while containing emissions generated within the enclosure. Design considerations include ventilation for heat dissipation and accessibility for maintenance.
Conformal Coatings
Conformal coatings are thin, protective layers applied to PCBs to shield against EMI, moisture, and contaminants. Conductive conformal coatings enhance shielding effectiveness by incorporating metal particles or conductive polymers.
Challenges in Board-Level EMI Shielding
Despite its effectiveness, board-level EMI shielding presents several challenges:
- Cost
High-performance shielding materials and techniques can increase manufacturing costs, particularly in high-volume production. - Design Complexity
Integrating shielding into PCB layouts requires careful planning to balance performance, manufacturability, and space constraints. - Thermal Management
Shielding materials can impede heat dissipation, necessitating the use of thermal vias, heat sinks, or advanced materials with high thermal conductivity. - Assembly and Testing
Shielding structures must be securely attached to the PCB without interfering with automated assembly processes or test points. - Evolving Standards
As regulatory requirements and operating frequencies evolve, shielding solutions must adapt to meet new challenges.
Applications of Board-Level EMI Shielding
Board-level EMI shielding is employed across a wide range of industries and applications, including:
- Consumer Electronics
Smartphones, tablets, and laptops rely on EMI shielding to ensure reliable operation in environments with numerous electronic devices. - Automotive Electronics
Advanced driver-assistance systems (ADAS), infotainment systems, and electric vehicle (EV) powertrains require robust EMI shielding to maintain performance and safety. - Medical Devices
EMI shielding is critical in medical devices, such as pacemakers and diagnostic equipment, to prevent interference that could compromise patient health. - Aerospace and Defense
In aerospace and defense applications, EMI shielding ensures the reliability of communication systems, navigation equipment, and radar systems. - Industrial Automation
Factory automation and robotics rely on EMI shielding to maintain precision and prevent downtime caused by interference.
Future Trends in Board-Level EMI Shielding
As electronic devices continue to evolve, so do the requirements for EMI shielding. Emerging trends include:
- Advanced Materials
Research into nanomaterials, such as graphene and carbon nanotubes, aims to develop lighter, more effective shielding solutions. - Integration with 5G and IoT
The proliferation of 5G networks and the Internet of Things (IoT) demands innovative shielding techniques to address higher frequencies and increased device density. - Sustainability
Eco-friendly shielding materials and manufacturing processes are gaining traction to reduce environmental impact. - Custom Solutions
Tailored shielding designs optimized for specific applications are becoming more common, driven by advancements in simulation and prototyping technologies.
Conclusion
Board-level electromagnetic interference shielding is a cornerstone of modern electronics, enabling devices to function reliably in increasingly complex electromagnetic environments. By combining advanced materials, innovative design strategies, and rigorous testing, engineers can ensure that electronic systems meet the demands of performance, compliance, and safety. As technology continues to advance, board-level EMI shielding will remain a critical area of research and development, shaping the future of electronics.