Homepage » Metal Etching »
Energy Etching – Metal Etching for Energy Industries
Metal etching for energy industries is a crucial technique applied across various sectors, such as renewable energy, fossil fuels, nuclear power, and energy storage, to produce highly precise components used in complex systems. Metal etching offers advantages in terms of precision, cost-efficiency, and adaptability, making it indispensable for manufacturing high-performance parts with intricate geometries, essential for many energy applications.
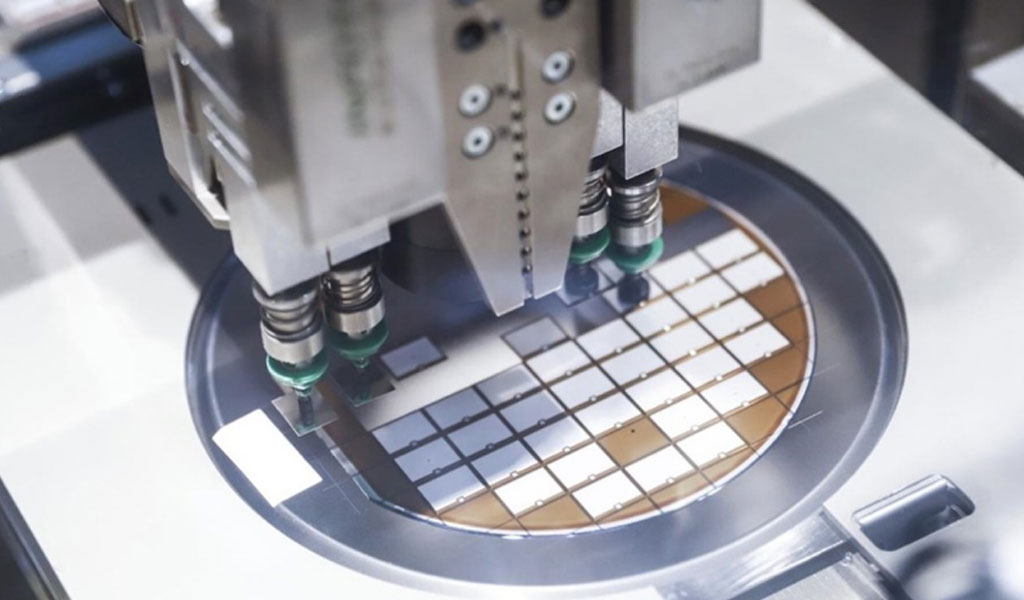
Photochemical etching is a multi-step process that involves coating the metal with a light-sensitive photoresist, exposing it to a UV light source through a photomask (a patterned stencil), and then developing the exposed photoresist.
The UV exposure causes the photoresist to harden on specific areas, while unexposed areas are subsequently washed away. The remaining unprotected metal is then subjected to the etchant solution, which removes the material in these exposed regions. The hardened photoresist protects the other regions, allowing the formation of precise, intricate patterns.
The energy industry often relies on photochemical etching for manufacturing components used in fuel cells, solar cells, batteries, and microelectronic mechanical systems (MEMS) that play roles in energy management, monitoring, and control. Photochemical etching is especially beneficial for creating microchannels, apertures, thin films, and surface patterns that improve heat dissipation, enhance electrical conductivity, or enable chemical interactions.
Our Energy Etching Service
If you need Energy etched we are one of the most capable and affordable sources specializing in manufacturing custom etched parts on advanced photo etching machines with cnc precision. Through our Photo Chemical Etching process, the smallest and most complex designs are made possible such as electrical spring contacts, contact membranes, busbars, antennae and micro antennae, spring fingered contacts, heating elements and battery terminal as well as many other bespoke components to your own designs.
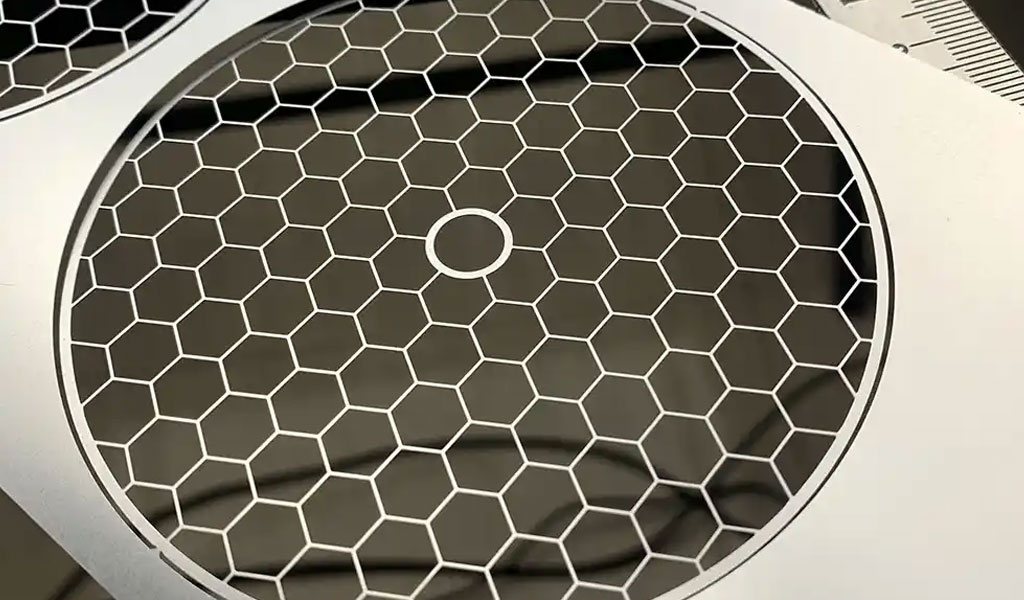
We can machine to print and accept the most common file formats including: .dwg .dxf .iges .step .sat as well as .pdf files. If you don’t see your file format here let us know. Please send us files to: [email protected] We can accept both small and large run jobs of custom energy parts.
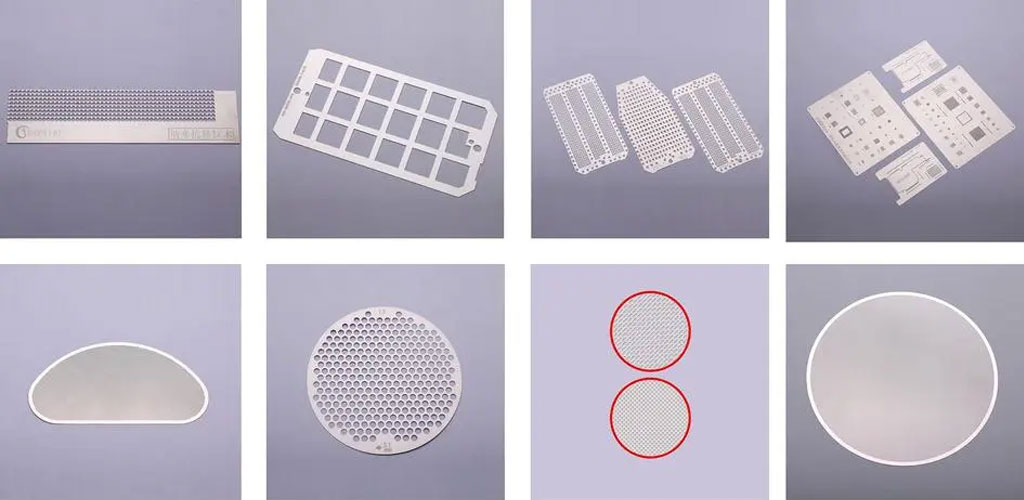
Our Etching Capabilities
- Etching of many grades of metal and more
- Combining Stamping, Laser Cutting,CNC machining and photochemical etching on sheets up to 2mm thick
- Etching of up to 0.025″ thick sheets as large as 22×12 inches
- Tolerances of ±.0005″ in many applications
How To Etch Energy Parts
Automated-Coating Automatic-Baking-Line Automatic-Shearing Coating-For-Etching-Parts Deinking Etching Exposure Inspection-For-Etching
Materials and Properties Relevant to Energy Industries
The energy sector demands materials that can withstand high temperatures, pressure variations, and corrosive environments. Metal etching supports a wide range of metals and alloys suited to these conditions, including:
- Titanium: Titanium’s strength, corrosion resistance, and biocompatibility make it an ideal choice for energy storage systems and offshore energy production. Etching titanium enables the production of components with high precision and robustness in applications like batteries and fuel cells.
- Stainless Steel: Known for its resistance to corrosion and durability, stainless steel is widely used in the construction of heat exchangers, fuel cells, and components exposed to harsh environments. Etching stainless steel provides a way to create corrosion-resistant patterns and components, essential for long-term reliability.
- Aluminum: Lightweight and corrosion-resistant, aluminum is used in applications requiring high strength-to-weight ratios, such as battery enclosures and cooling systems in renewable energy devices. Etching aluminum provides a means of creating lightweight but robust structures, essential for portable or compact energy devices.
- Nickel Alloys: High-performance alloys like Inconel and Hastelloy are known for their ability to withstand extreme conditions, such as high temperatures and corrosive environments in nuclear reactors and gas turbines. Etching nickel alloys allows for the fabrication of precise, resilient parts for these demanding applications.
- Copper: Due to its excellent electrical and thermal conductivity, copper is commonly etched for applications in energy storage and transmission, such as battery collectors and conductive pathways in photovoltaic cells.
Applications in Energy Industries
Energy etching is used in a variety of applications, each serving different functions within the toy manufacturing industry. Some of the most notable applications of Energy etching include:
Fuel cells are electrochemical devices that convert chemical energy from fuel into electricity. These systems rely on etched metal components to increase surface area for better reactions and enable fluid pathways to facilitate efficient fuel and air flow. Etching plays a role in creating microchannels and grooves for hydrogen and oxygen movement, vital for increasing the fuel cell’s overall efficiency. By etching high-strength materials like stainless steel or titanium, fuel cell manufacturers can achieve durability, corrosion resistance, and precise patterning, enhancing the longevity and reliability of these cells in applications such as electric vehicles and backup power systems.
Metal etching supports the creation of current collectors in lithium-ion batteries, commonly made from copper (anode side) and aluminum (cathode side). The etched metal provides a textured surface that enhances adhesion between active materials and current collectors, optimizing the charge/discharge efficiency of batteries. In advanced batteries, such as solid-state and lithium-sulfur batteries, etched components play a critical role in improving ion mobility and stability. Additionally, the etching process allows precise, customized designs for thermal management systems within battery packs, enabling better heat dissipation and extending battery life.
In photovoltaic (PV) cells, metal etching is used to create conductive pathways for electrical currents generated by sunlight. Copper and silver are typically etched to form electrode grids on the surface of silicon wafers in PV cells, where their conductive properties help capture and transfer solar energy into usable electricity. Micro-scale etching ensures minimal shadowing on the cell surface, allowing more sunlight to reach the silicon substrate, thus increasing efficiency. Additionally, etched textures on metal surfaces can reduce reflection, enhancing light absorption for improved energy conversion.
Heat exchangers are essential for managing temperatures in a variety of energy systems, from power plants to HVAC systems in buildings. Etched metals, particularly stainless steel and titanium, are commonly used to create fins, plates, and tubes with optimized surface patterns that enhance thermal transfer. The etching process allows manufacturers to create micro-fins or complex geometries that increase the surface area for heat exchange without adding bulk. This is particularly important in compact systems where space and weight are constraints, such as in mobile power units and renewable energy devices.
The nuclear power sector requires components capable of withstanding extreme conditions, such as high radiation levels, elevated temperatures, and corrosive environments. Etched nickel alloys and stainless steel are frequently used to manufacture components in nuclear reactors, such as cooling plates, control rods, and shielding elements. The high degree of accuracy offered by metal etching allows these components to meet stringent safety and performance standards. Furthermore, the non-invasive nature of photochemical etching ensures that there is no mechanical stress or heat distortion, making it ideal for nuclear applications where material integrity is critical.
Components That Are Produced By Etching Energy Parts
The popularity of Energy parts makes it a desirable metal for use in fabrication because it is easy to manufacture and has favorable properties for many industrial products.With the photo etching process, the metal is etched evenly without any structural deformations from the hard tooling used in stamping and punching.Since there isn’t a heat point of contact like laser cutting, the parts’ metal properties remain unchanged and free from thermal deformations.Get inspired by our custom etching part projects and contact us to Get Instant Quote for rapid prototype or Toy etching start from 1pcs.
Metal Etching Certification,Equipment List and Quality
We are committed to enlisting the full support of all employees to continuously improve our processes and enhance quality, thereby fulfilling our customer's needs with defect free products and services, on time and every time
- ISO 9001:2015 certified
- Compliance in DFARS materials sourcing requirements
- Strict compliance with PPAP and Process FMEA
- Fully compliant with the exacting requirements of our customers
- ITAR registered
- NIST cybersecurity standard compliant
- Proprietary Patented quality systems
- Skilled in KanBan and other customer driven quality and inventory management systems
Metal Etching Material
BE-CU is experienced in precision etching various metals, allowing customers the freedom to specify components in hundreds of different materials.
The Surface Treatment Of Metal Etching Parts
Do you want your etching parts to be more corrosion-resistant or get a specific look? Metal finishing service is a essential choice to achieve your design perfectly. BE-CU – metal-etch.com is an accomplished finished parts manufacturer, our workers and craftsman are capable to provide precision metal etching services and a wide range of finishing services including aluminum anodizing, painting, passivation, electroplating, powder coating, polishing, black oxide, conversion coating, abrasive blasting, etc. We offers several common surface finishes to help improve functionality and aesthetics.
- Anodizing (Anodized)
- Passivation
- Plating (Electroplating)
- Painting
- Black Oxide (Hot Blackening)
- Polishing
- Powder Coating
- Heat Treatment
- Satin Finish
- Abrasive blasting (Sandblasting)
- Conversion coating
- Tungsten carbide coating
After browsing a list of metal finishing services, select a process based on essential considerations, like production time, cost-effectiveness, part tolerance, durability and applications. High-tolerance metal etching parts are not recommended to apply secondary metal surface finish, because the treatment may change the sizes of the finished part through removing or adding a small amount of materials.
Other requirements or custom designs, welcome to contact us for a free quote fast!