Homepage » Metal Etching »
Nuclear Etching – Metal Etching for Nuclear Industry
Metal etching is a crucial process used in a wide range of industries, particularly in applications where precision, cleanliness, and material integrity are paramount. Among the various industries that benefit from metal etching, the nuclear industry stands out due to its rigorous standards and the demanding environments in which materials must perform. Metal etching for the nuclear industry involves techniques used to create precise patterns, remove unwanted material, or prepare surfaces for further treatments, all while maintaining the high standards required for safety, reliability, and performance. This process plays a key role in the fabrication of components used in nuclear reactors, nuclear fuel processing, waste management, and radiation shielding, among other applications.
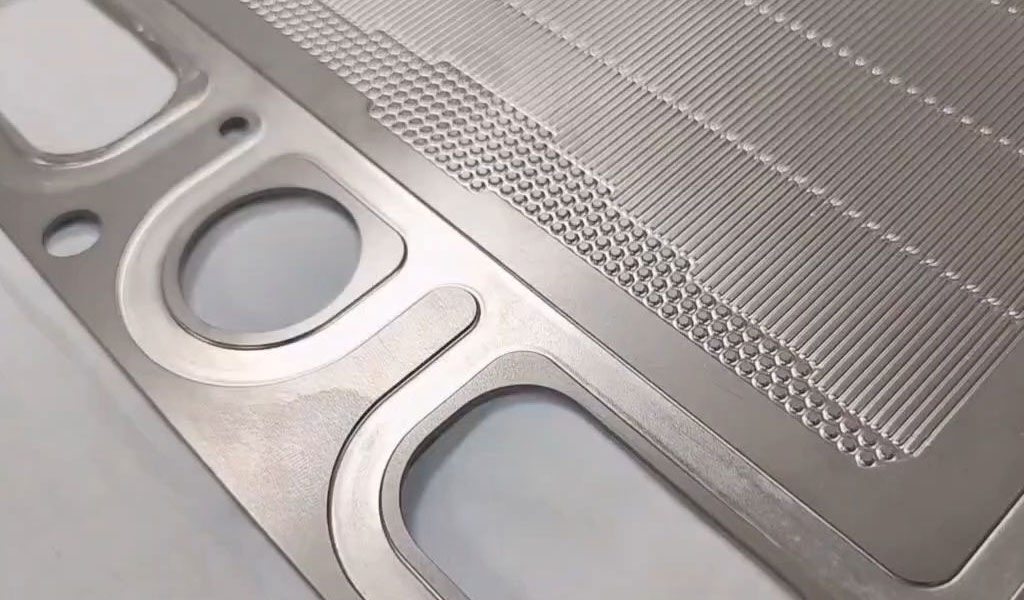
In the nuclear industry, metal etching serves a variety of purposes, each designed to meet stringent operational and safety requirements.
Metal etching is typically employed to prepare metal surfaces, create fine details, and achieve certain surface characteristics that are vital for nuclear applications.
This includes the removal of material from metal surfaces, the production of microstructures, and the creation of patterns for components used in reactors, fuel elements, and radiation shielding.
The materials used in the nuclear industry often need to withstand extreme temperatures, high radiation exposure, and corrosive environments. As such, the metals selected for use in nuclear components, including stainless steel, zirconium alloys, copper alloys, and nickel-based alloys, must be etched with great precision to maintain their mechanical properties, enhance corrosion resistance, and meet other functional demands.
Our Nuclear Etching Service
If you need Nuclear parts etched we are one of the most capable and affordable sources specializing in manufacturing custom etched parts on advanced photo etching machines with cnc precision. Through our Photo Chemical Etching process, the smallest and most complex designs are made possible such as electrical spring contacts, contact membranes, busbars, antennae and micro antennae, spring fingered contacts, heating elements and battery terminal as well as many other bespoke components to your own designs.
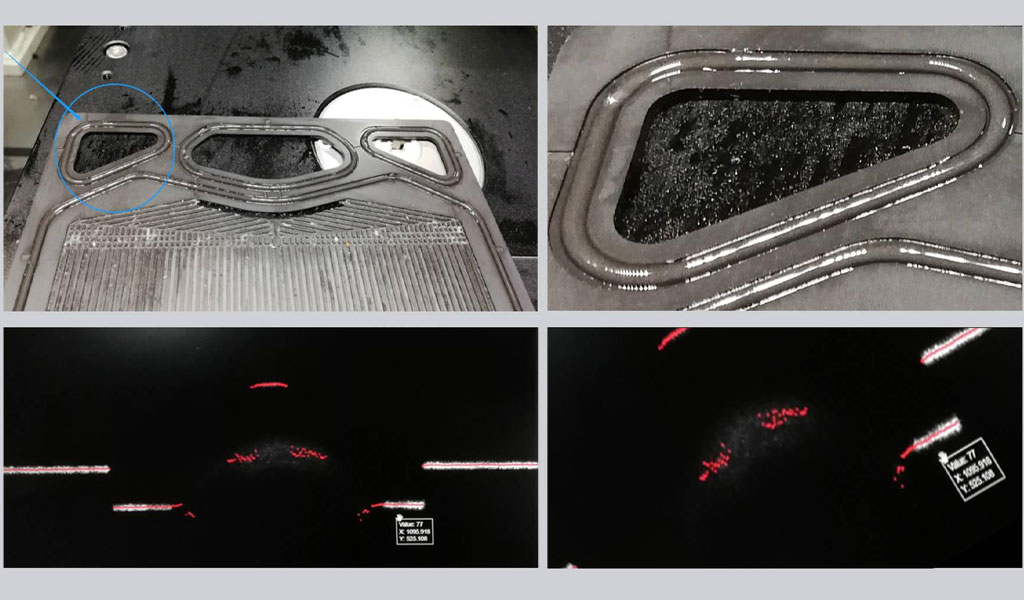
We can machine to print and accept the most common file formats including: .dwg .dxf .iges .step .sat as well as .pdf files. If you don’t see your file format here let us know. Please send us files to: [email protected] We can accept both small and large run jobs of custom Nuclear etching parts.
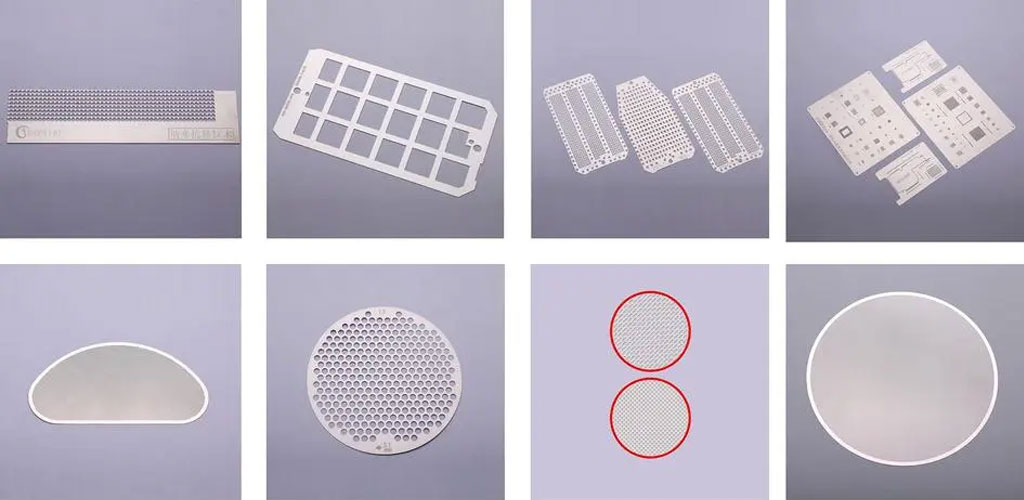
Our Etching Capabilities
- Etching of many grades of metal and more
- Combining Stamping, Laser Cutting,CNC machining and photochemical etching on sheets up to 2mm thick
- Etching of up to 0.025″ thick sheets as large as 22×12 inches
- Tolerances of ±.0005″ in many applications
How To Etch Nuclear Parts
Automated-Coating Automatic-Baking-Line Automatic-Shearing Coating-For-Etching-Parts Deinking Etching Exposure Inspection-For-Etching
Materials Used in Nuclear Industry Metal Etching
The selection of materials for use in the nuclear industry is critical, as these materials must meet stringent safety and performance criteria. Metals used in the nuclear industry must resist corrosion, withstand high radiation levels, and maintain their structural integrity under extreme temperatures and pressures. Commonly used materials in nuclear applications include:
Stainless Steel
Stainless steel, particularly grades 304 and 316, is one of the most commonly used materials in the nuclear industry due to its excellent corrosion resistance, strength, and ability to withstand high temperatures. Stainless steel is often used in reactor components, fuel rods, and other parts that are exposed to both radiation and harsh environmental conditions. Etching stainless steel for use in the nuclear industry typically involves the use of nitric acid-based solutions or electrochemical etching techniques.
Zirconium Alloys
Zirconium alloys, such as Zircaloy, are widely used in nuclear reactors due to their low neutron absorption cross-section and excellent corrosion resistance, especially in the high-temperature, high-radiation environment of nuclear reactors. Zirconium-based alloys are often etched using chemical etching methods, which are particularly effective for removing oxides and preparing the material for further processing or use in nuclear fuel elements.
Nickel Alloys
Nickel alloys, such as Inconel, are frequently used in nuclear reactors, particularly in heat exchangers, reactor cores, and other high-temperature components. These alloys are resistant to both high temperatures and corrosion, making them ideal for use in nuclear power plants and other nuclear applications. Etching nickel alloys involves specialized techniques, such as electrochemical etching or laser etching, to ensure that the material’s surface properties are maintained while precise patterns or textures are created.
Copper Alloys
Copper and its alloys are used in the nuclear industry primarily for their excellent electrical and thermal conductivity properties. Copper is often used in the manufacture of radiation shielding components, heat exchangers, and electrical connectors. Copper alloys are etched using both chemical and electrochemical methods to ensure that the material’s conductive properties are not compromised and that the components meet the necessary design specifications.
Applications of Metal Etching in the Nuclear Industry
Metal etching plays a crucial role in the nuclear industry, providing the precision, safety, and reliability required for the production of components used in nuclear reactors, fuel processing, waste management, and radiation shielding. The techniques of metal etching—whether chemical, laser, electrochemical, or mechanical—are employed to ensure that nuclear materials are fabricated with the utmost precision and integrity. By enabling the production of high-performance materials and components, metal etching contributes to the safe and efficient operation of nuclear power plants and other nuclear facilities.Some key applications include:
Nuclear Reactor Components
One of the primary applications of metal etching in the nuclear industry is in the production of nuclear reactor components. These components, such as fuel rods, control rods, and reactor pressure vessels, must be fabricated with extreme precision to ensure their proper functioning and to minimize the risk of failure under extreme conditions. Metal etching techniques are used to create fine details on these components, remove unwanted material, and prepare surfaces for further treatments that enhance their corrosion resistance and mechanical strength.
Nuclear Fuel Elements
Nuclear fuel elements, including fuel rods and assemblies, are another critical area where metal etching is employed. These components are often made from zirconium alloys or stainless steel and must be etched to precise specifications. Etching is used to remove oxides from the surface of these materials, to create microstructures that enhance the materials’ mechanical properties, and to ensure that the fuel elements fit together properly in the reactor.
Radiation Shielding
Radiation shielding is an essential part of any nuclear facility, and metal etching plays a role in the production of components used for this purpose. Materials such as lead, tungsten, and various alloys are often etched to create precise shapes or textures that enhance their ability to block or absorb radiation. Metal etching is particularly useful for creating intricate patterns or geometries on radiation shielding components, ensuring that they meet the safety standards required in nuclear facilities.
Instrumentation and Monitoring Equipment
Metal etching is also used in the production of instrumentation and monitoring equipment used in nuclear facilities. Components such as sensors, probes, and connectors often require precise etching to create fine patterns or microstructures. These components are used to monitor radiation levels, temperature, pressure, and other critical parameters in nuclear reactors, ensuring the safety and efficiency of nuclear operations.
Components That Are Produced By Etching Nuclear Parts
The popularity of Nuclear makes it a desirable metal for use in fabrication because it is easy to manufacture and has favorable properties for many industrial products.With the photo etching process, the metal is etched evenly without any structural deformations from the hard tooling used in stamping and punching.Since there isn’t a heat point of contact like laser cutting, the parts’ metal properties remain unchanged and free from thermal deformations.Get inspired by our custom etching part projects and contact us to Get Instant Quote for rapid prototype or Nuclear etching parts start from 1pcs.
-
Precision Etched Titanium Alloy Odor Eliminator Perforated Plates
-
High-End Etched TC4 Titanium Alloy Filters
-
Precision Etching Titanium Alloy Hanging Fixture for Anodizing
-
Metal Chemical Etching Reciprocating Razor Blades
-
Titanium Alloy Etched Coffee Filter
-
Etching Bipolar Plates for Hydrogen Fuel Production
-
0.3MM Laser Etched Titanium Mesh
-
Precision Etching Printer Single Drum Scraper
Metal Etching Certification,Equipment List and Quality
We are committed to enlisting the full support of all employees to continuously improve our processes and enhance quality, thereby fulfilling our customer's needs with defect free products and services, on time and every time
- ISO 9001:2015 certified
- Compliance in DFARS materials sourcing requirements
- Strict compliance with PPAP and Process FMEA
- Fully compliant with the exacting requirements of our customers
- ITAR registered
- NIST cybersecurity standard compliant
- Proprietary Patented quality systems
- Skilled in KanBan and other customer driven quality and inventory management systems
Metal Etching Material
BE-CU is experienced in precision etching various metals, allowing customers the freedom to specify components in hundreds of different materials.
The Surface Treatment Of Metal Etching Parts
Do you want your etching parts to be more corrosion-resistant or get a specific look? Metal finishing service is a essential choice to achieve your design perfectly. BE-CU – metal-etch.com is an accomplished finished parts manufacturer, our workers and craftsman are capable to provide precision metal etching services and a wide range of finishing services including aluminum anodizing, painting, passivation, electroplating, powder coating, polishing, black oxide, conversion coating, abrasive blasting, etc. We offers several common surface finishes to help improve functionality and aesthetics.
- Anodizing (Anodized)
- Passivation
- Plating (Electroplating)
- Painting
- Black Oxide (Hot Blackening)
- Polishing
- Powder Coating
- Heat Treatment
- Satin Finish
- Abrasive blasting (Sandblasting)
- Conversion coating
- Tungsten carbide coating
After browsing a list of metal finishing services, select a process based on essential considerations, like production time, cost-effectiveness, part tolerance, durability and applications. High-tolerance metal etching parts are not recommended to apply secondary metal surface finish, because the treatment may change the sizes of the finished part through removing or adding a small amount of materials.
Other requirements or custom designs, welcome to contact us for a free quote fast!